Searching for metal fab parts means you need information on how these parts are made, the materials used, and the different types available. This article covers the essential processes in metal fabrication, the most common types of metal fab parts, material options, and finishing techniques. Understanding these aspects will help you choose the right parts for your project.
Key Takeaways
Metal fabrication involves processes like cutting, bending, and welding to create durable and customized metal parts for various industries.
Understanding the properties of materials like steel, aluminum, and specialty metals is crucial for selecting the right components to ensure optimal performance in specific applications.
Finishing techniques such as plating, powder coating, and anodizing enhance the aesthetics and durability of metal parts, making them suitable for harsh environments.
Understanding Metal Fab Parts
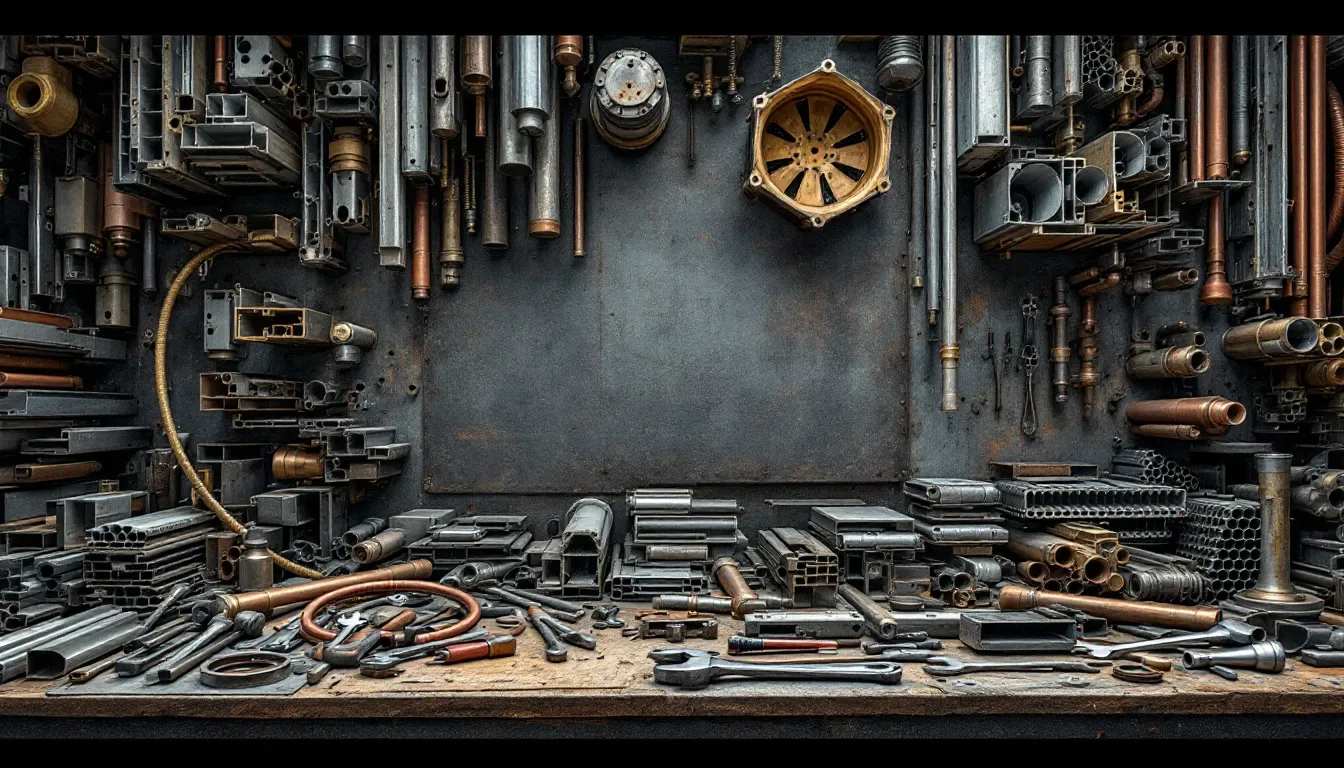
Metal fabrication encompasses a range of processes including the cutting and bending of metal, along with assembling these components. This method is critical for producing an array of items such as irrigation pivots, jet engine components, and metal stanchions. The adaptability inherent in metal fabrication permits manufacturers to craft parts that meet exact specifications, guaranteeing peak performance in their designated roles.
A thorough comprehension of the different procedures and materials used in crafting metal parts can significantly benefit manufacturers. By recognizing the distinct attributes each material offers during fabrication, they can streamline production while ensuring high-quality outcomes. The enduring nature and superior quality of these fabricated parts are pivotal to any project’s triumphant completion.
Specialty metals like titanium and stainless steel are frequently chosen for certain tasks because they offer unique benefits like excellent strength-to-weight ratios and resistance to deterioration over time. Titanium stands out due to its impressive strength-to-weight ratio, which suits it perfectly for use within the aerospace industry. Meanwhile, aluminum is favored not only for being light but also highly resistant to corrosion, which makes it advantageous for automotive and aerospace industries alike.
Key Processes in Metal Fabrication
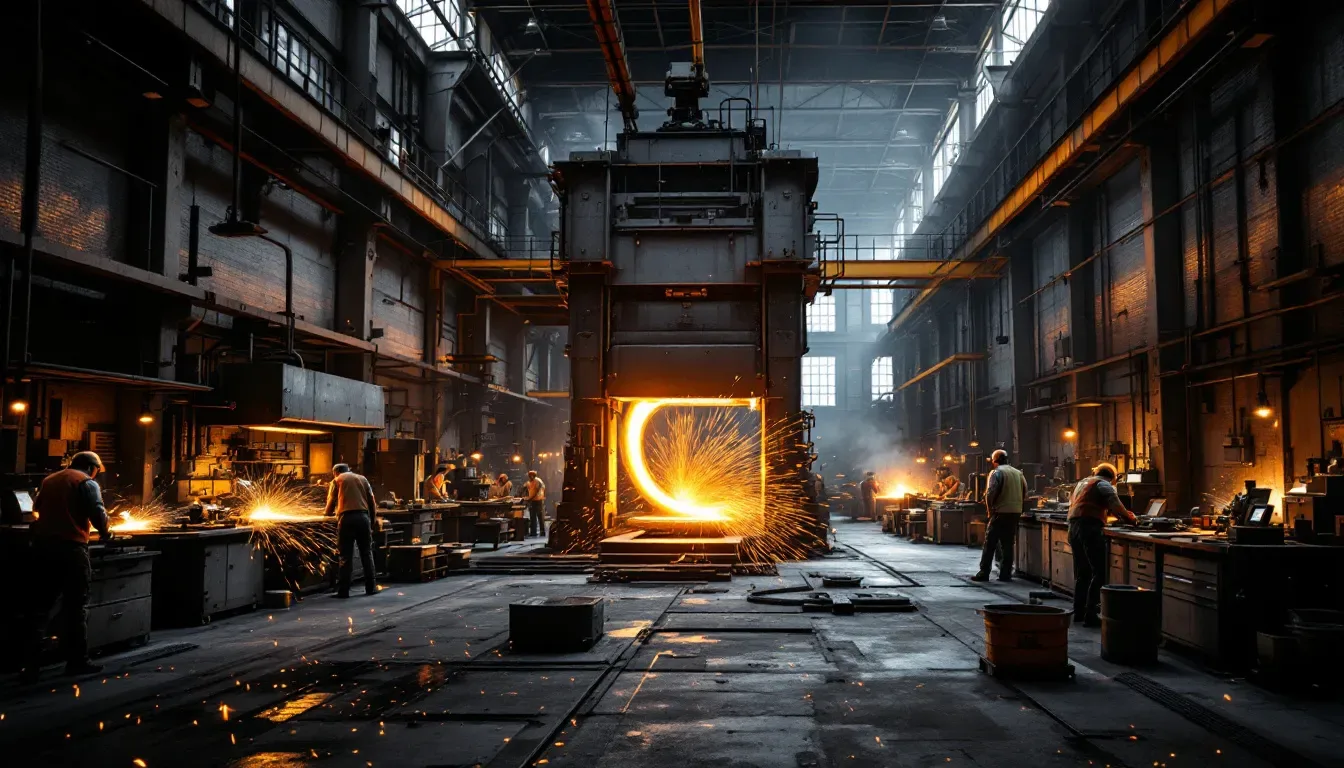
Metal fabrication involves a series of essential methods such as cutting, bending, welding, and machining, which are instrumental in creating custom-made fabrication parts that meet particular requirements. These central techniques are crucial for converting raw metal into high-quality bespoke components ready for use.
We should delve into the three fundamental procedures within metal fabrication: cutting, bending, and welding. Each process employs distinct tools and methodologies. Grasping these can assist you in making knowledgeable choices regarding your project.
Cutting
Shaping metal into smaller components is achieved through the adaptable process of cutting, which employs various techniques such as laser cutters, power shears, waterjets, and plasma torches. CNC laser cutting stands out for its precision in creating detailed cuts via lasers—perfect for complex patterns. Meanwhile, waterjet cutting leverages a high-pressure stream to effortlessly carve through different thicknesses of metal while delivering clean and accurate results.
For materials like steel that oxidize readily, torch cutting serves as an efficient option due to its use of high-temperature flames capable of piercing these metals. The selection among these methods depends on the unique demands of each project. Hence choosing the right tools and approaches is crucial in influencing the final product’s overall quality and exactitude.
Bending
In metal fabrication, a brake press or hammer accompanied by clamp bars is utilized to accomplish the task of bending. This technique is employed with the intention of crafting specific angles and forms, which facilitates the production of various components designed for particular uses.
The method is crucial in shaping parts that necessitate exacting angles and curvatures.
Welding
Metal fabrication frequently utilizes welding due to its ability to fuse metal parts of varying dimensions and forms together. The process achieves this by applying heat and pressure, which establishes a durable connection among the pieces involved. Techniques widely employed in welding include stick welding, MIG (Metal Inert Gas) welding, TIG (Tungsten Inert Gas) welding, and flux-cored arc welding.
The role of welding is crucial when it comes to assembling intricate structures while ensuring that the fabricated components possess longevity. Through the application of suitable methods for blending different elements seamlessly into one another, a strong and unified end product emerges. To tailor your choice of welding methodology precisely according to your requirements can be informed by gaining an insight into each available technique’s distinct advantages.
Types of Metal Fab Parts
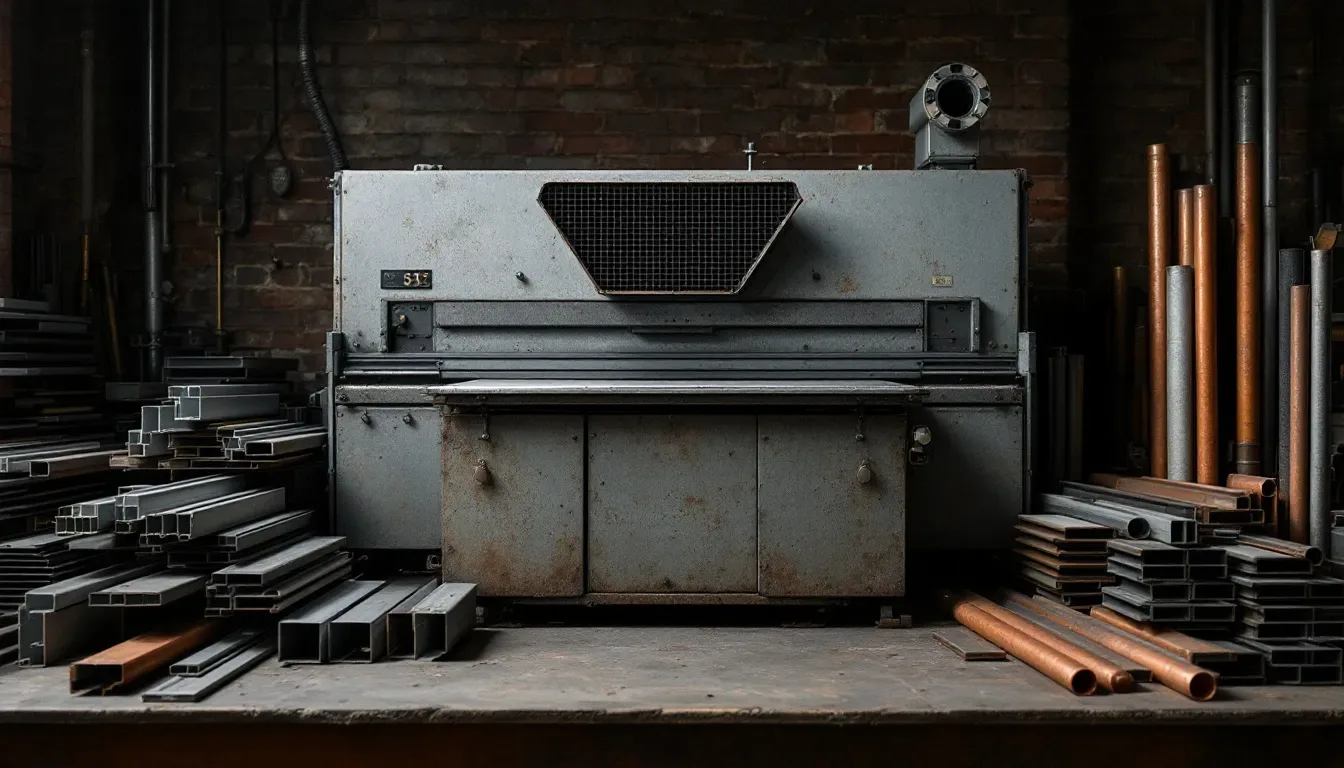
Metal fabrication plays a pivotal role in numerous sectors, including construction and automotive industries. It is indispensable for crafting vital parts that are fundamental to our current technological landscape and infrastructure. This process transforms raw metal into practical products, frequently employing materials such as steel and aluminum due to their versatile attributes.
Exploring typical varieties of fabricated metal components reveals the importance of brackets and mounts, gussets and tabs, along with custom plates. These distinct elements each serve specific purposes across various applications. Gaining insights into their functions is beneficial when selecting appropriate parts for your particular project needs.
Brackets and Mounts
Customizable brackets for 3 or 4-link suspensions can be adapted to suit various angles, which significantly increases the adaptability of off-road vehicles. Tailoring these brackets enhances their performance in particular uses like the suspension systems of off-road transportation.
Such elements play a crucial role in offering support and ensuring stability across diverse structures by serving as a firm stand.
Gussets and Tabs
Gussets play an essential role in bolstering joints and structures, significantly improving their overall robustness. By spreading stress over a wider surface, they help avoid structural breakdowns and extend the life expectancy of different elements. Tabs function as critical anchoring spots for numerous parts, offering vital links within frameworks.
In unison, gussets and tabs are instrumental in fortifying the comprehensive design and guaranteeing the endurance of manufactured components. These features are frequently employed in both construction and automotive sectors to fabricate strong and reliable constructs.
Custom Plates
Custom plates are pivotal in numerous sectors, serving as the backbone that imparts vital robustness and steadiness within construction domains and heavy-duty machinery. Carbon steel is often selected for these purposes because of its distinguished strength and durability. Meanwhile, alloy steel, enriched with components such as nickel and chromium, is preferred in both automotive and aerospace industries on account of its superior mechanical characteristics.
The material’s extensive use in manufacturing stems from its impressive tensile strength, which renders it perfect for structural roles and arduous fabrication tasks. The adaptability inherent to custom plates enables their precise customization to meet specific mounting requirements necessary for off-road uses, assuring a seamless integration into unconventional setups.
Material Options for Metal Fab Parts
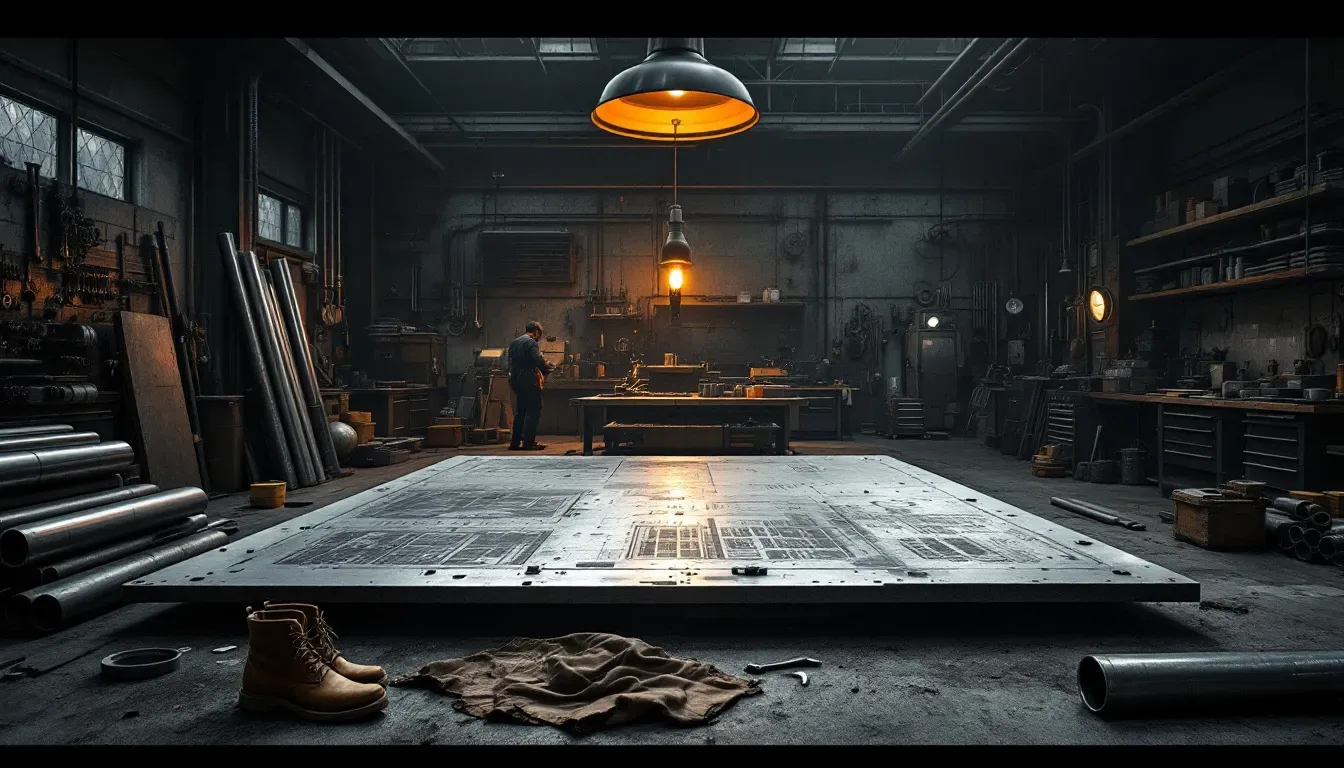
Selecting an appropriate material for the fabrication of metal parts is vital since it influences both their longevity and effectiveness in certain uses. Typical components produced through metal fabrication encompass a variety of structural elements such as beams, plates, sheets, and tubes. Among the available materials for these parts are steel, aluminum, and various specialty metals. Each provides distinct qualities and benefits.
To ensure you choose the optimal material for your specific project requirements, it’s beneficial to explore different options. A detailed examination of the properties associated with steel, aluminum, and specialty metals can serve as a valuable guide during this selection process.
Steel
Renowned for its outstanding strength, steel is often the material of choice in metal fabrication. It can be tailored into custom plates that come in an array of shapes and sizes to accommodate unique structural designs, providing adaptable options for both mounting and strengthening across a variety of projects. This blend of robustness and adaptability renders steel custom plates perfectly suited to meet various project requirements.
The formidable tensile strength possessed by steel enables it to bear substantial weight, rendering it ideal for use in structural purposes as well as heavy-duty manufacturing processes. Incorporating steel into parts during the fabrication process guarantees not only longevity but also their reliable performance within their designated operational settings.
Aluminum
Aluminum is prized for its low weight, which makes it perfect for uses where keeping weight down is essential. It also has superior corrosion resistance that helps extend the life of metallic parts exposed to severe conditions. Structural applications often rely on 6000 series aluminum alloys due to their optimal combination of strength and flexibility.
The lightness of aluminum aids in achieving better energy efficiency, which is why it’s a favored material for components and frames in the automotive industry. Its impressive ability to resist corrosion lends itself well to various uses across both the automotive and aerospace sectors.
Specialty Metals
Titanium and stainless steel are specialty metals known for their superior strength and ability to resist corrosion, which makes them perfect for the rigorous demands of off-road use. Titanium is particularly valued for its combination of lightness and robustness, often chosen for parts that need to be durable yet not overly heavy. Stainless steel, on the other hand, is a popular choice in off-road fabrication because it can withstand rust and extreme weather conditions effectively.
Incorporating these specialty metals into the manufacturing process of off-road components greatly enhances their longevity, decreasing the frequency at which parts need to be replaced. Alloy steels are customizable according to particular needs. They provide an optimal mix of toughness and hardness needed in off-roading equipment.
Finishing Techniques for Metal Fab Parts
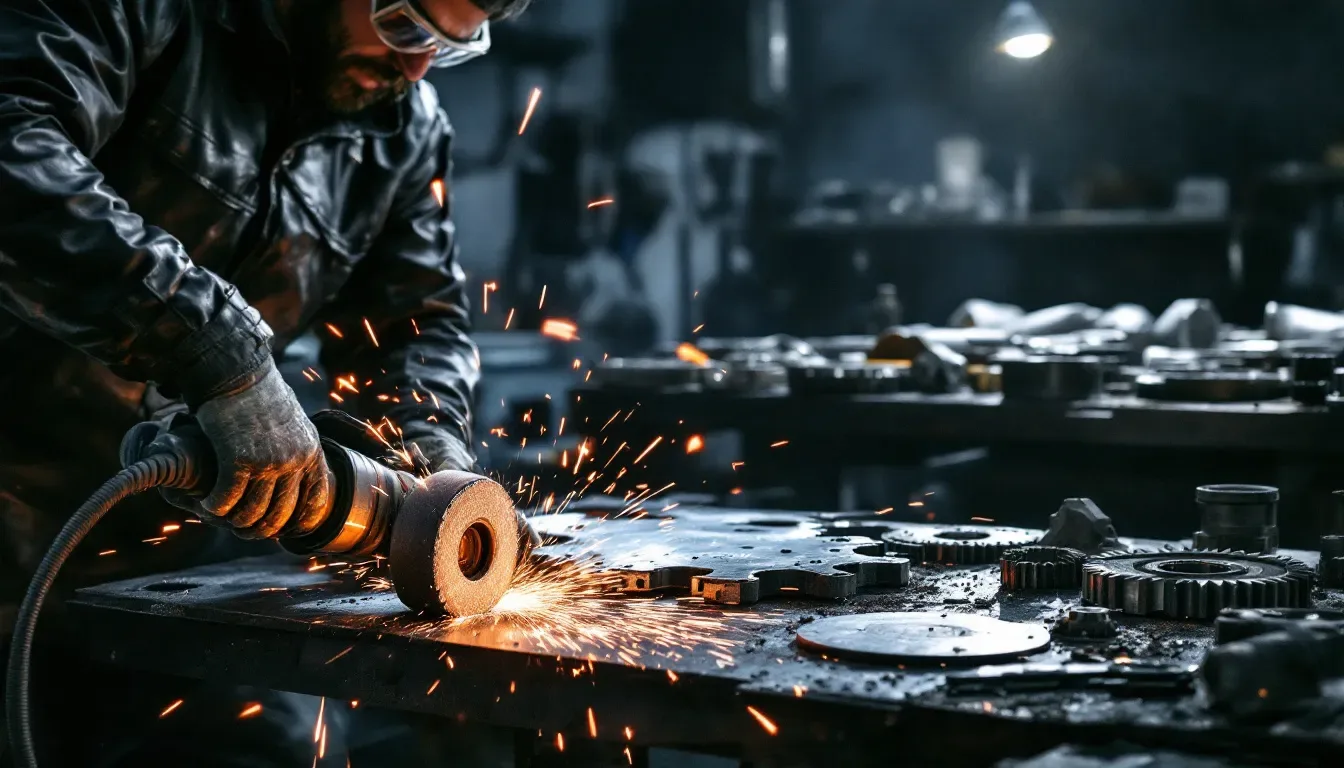
Techniques for finishing, such as anodizing, powder coating, and plating, are essential in enhancing the durability and aesthetic quality of components made from metal fabrication. These methods serve a dual purpose: they improve the parts’ appearance while also applying protective coatings that help prevent corrosion and reduce wear.
We should delve into each of these finishing techniques more thoroughly to understand their distinct advantages. Depending on what a particular project demands, one can select between anodizing, powder coating, or plating based on which method aligns best with those specific needs.
Plating
In metal fabrication, plating serves as a finishing method that improves the protection and longevity of metal components. A protective layer is formed during electroplating by immersing a metal part into a solution filled with metal ions. Conversely, electroless plating eschews the use of electricity and instead relies on chemical processes to apply metals such as nickel to surfaces.
The provision of these vital coatings through both electroplating and electroless plating methods significantly augments the utility and aesthetic appeal of fabricated metallic parts. Implementing these techniques is crucial for safeguarding both their durability and operational effectiveness.
Powder Coating
The process of powder coating applies a dry polymer powder onto metal surfaces, resulting in a finish that is thicker and more robust than standard paint. By promoting uniform coverage on metallic structures, it not only improves their appearance but also provides protection against rust. Powder coating utilizes an electrostatic method that minimizes excess material use and expedites the time needed for production.
Crafting a resilient coat through powder finishing offers superior durability over conventional painting methods, which makes it particularly well-suited for conditions that are extreme or demanding. For undertakings where enduring strength is just as important as visual quality, this technique of finishing stands out as ideal.
Anodizing
Anodizing is an electrochemical technique that amplifies the inherent oxide layer on aluminum to boost its resistance to corrosion. The procedure fosters an electrochemical response, which not only augments the surface hardness of the metal but also offers a range of coloring options, lending an aesthetic appeal to the aluminum parts.
During the process of anodizing, there’s a crucial sealing phase designed to occlude pores within the oxidized coating. This enhances functional attributes and prolongs the longevity of metallic elements. Such finishing strategies are exceptionally beneficial in contexts where both resilience and visual aspects play critical roles.
Start Your Next Project with LKprototype
LKprototype simplifies procurement for custom manufacturing, Suitable for making your products or prototypes with a variety of materials, such as metal or plastic, silicone rubber, from 3D Printing to CNC Machined Parts and Vacuum Casting , with a focus on speed and efficiency. Our platform provides instant quotes. With LKprototype, You can connect with the team to communicate your project to ensure quality and on-time delivery.
Start with an instant quote and experience how our technology and expertise can make custom part procurement faster and easier.
Customization and Ordering Process
Starting with the appropriate design and precise specifications is essential for customizing metal fabrication parts. To achieve optimal outcomes for your project, it’s crucial to manage the ordering process efficiently. This entails uploading Computer-Aided Design (CAD) files, choosing suitable materials and finishes, and completing your order.
We will guide you through every stage of customization and placing an order to guarantee that you receive the superior-quality metal fab parts required for your undertaking.
Uploading CAD Files
Submitting CAD files through the dedicated upload portal on our website facilitates the meticulous creation and personalization of metal components, ensuring they align perfectly with your unique project specifications. Navigate to the upload section, choose a compatible file type, and adhere to the guidelines presented there to guarantee that your design details are effectively conveyed to those crafting your product.
After successfully uploading your CAD files, you will gain immediate access to price evaluations and can investigate an array of tailor-made choices for fabricating your metal parts. This process streamlines the journey from concept to completion, confirming that what is produced matches precisely with what’s needed for your endeavor.
Selecting Materials and Finishes
Selecting appropriate materials for off-road fabrication is crucial to bolster the robustness and functionality of components, allowing them to endure rigorous conditions. Steel and aluminum are typical choices in this field due to their distinct benefits regarding weight and structural integrity.
Applying finishes such as powder coating enhances not only the visual appeal, but also provides a defensive barrier against corrosion and deterioration. It’s important to take into account the environment where the parts will be used when determining which finishes are suitable. Outdoor use demands coatings that can withstand factors like UV rays and moisture.
Our proficiency is demonstrated through custom fabrication processes, which often include simulations designed to verify that selected materials and finishing techniques will hold up under anticipated circumstances.
Finalizing Your Order
Prior to initiating production, it’s imperative that you meticulously examine the specifics of your order to confirm they align with your stipulations. This examination should encompass a thorough verification of the materials chosen, applied finishes, and precise measurements in an effort to prevent any inaccuracies during manufacturing.
Ensuring that every detail on the order adheres strictly to specifications is crucial before commencing production. Customers are encouraged to scrutinize their choices and validate that all details correspond perfectly with their project needs prior to solidifying their request. Undertaking this precautionary step is instrumental in providing finished parts of superior quality which precisely cater to the requirements of your project.
Summary
To ensure top-notch outcomes in your metal fabrication projects, it’s imperative to have a deep understanding of the essential processes involved, including cutting, bending, and welding. These steps are critical for transforming raw metal into practical parts. Selecting appropriate materials and finishing methods is key to enhancing both the longevity and visual appeal of these components.
Adhering closely to the customization and ordering procedures can help guarantee that each piece conforms precisely to your specific needs. Regardless of whether you’re engaged in crafting an off-road vehicle, erecting a structure or assembling complex machinery, applying what this guide has taught will aid you in making well-informed choices and attaining optimal results for any future project endeavors.
Frequently Asked Questions
What are the key processes involved in metal fabrication?
The key processes in metal fabrication are cutting, bending, and welding, which each utilize various techniques and tools to transform raw metal into functional parts.
Mastering these processes ensures precision and quality in your projects.
Why is it important to choose the right material for metal fab parts?
It’s essential to choose the right material for metal fab parts because it directly influences durability and performance in their intended use. Different materials like steel, aluminum, and specialty metals bring unique benefits to the table, so selecting wisely is key.
What are the benefits of plating as a finishing technique?
Plating offers great benefits by boosting the durability and protection of metal parts while also enhancing their look and functionality.
It’s a simple way to improve the quality of your products!
How do I upload CAD files for custom metal fabrication?
You can easily upload your CAD files by visiting the website’s designated upload area, selecting the right file format, and following the instructions provided.
This will ensure your metal parts are fabricated accurately to suit your needs.
What should I consider when selecting finishes for metal fab parts?
When choosing finishes for metal fab parts, think about where they’ll be used—outdoor parts need finishes that withstand UV rays and moisture.
Techniques like powder coating and anodizing not only enhance appearance but also protect against corrosion and wear.