CNC machining prototypes utilize advanced computer-controlled machines to create precise prototypes rapidly, showcasing their versatility and precision across various industries, including military, medical, automotive, aerospace, oil, and energy. This process is crucial in product development, offering advantages like speed, accuracy, and material versatility. Read on to explore the benefits and applications of CNC prototyping in various industries.
Key Takeaways
CNC prototype machining accelerates product development by enabling rapid iterations and precise prototypes that closely match final product specifications.
The versatility of CNC machining allows for the use of various materials like metals, plastics, and composites, making it adaptable to diverse industry needs.
Collaborating with experienced manufacturers can streamline the CNC prototyping process, enhancing efficiency and ensuring high-quality outcomes.
Mastering CNC Prototype Machining: A Practical Guide
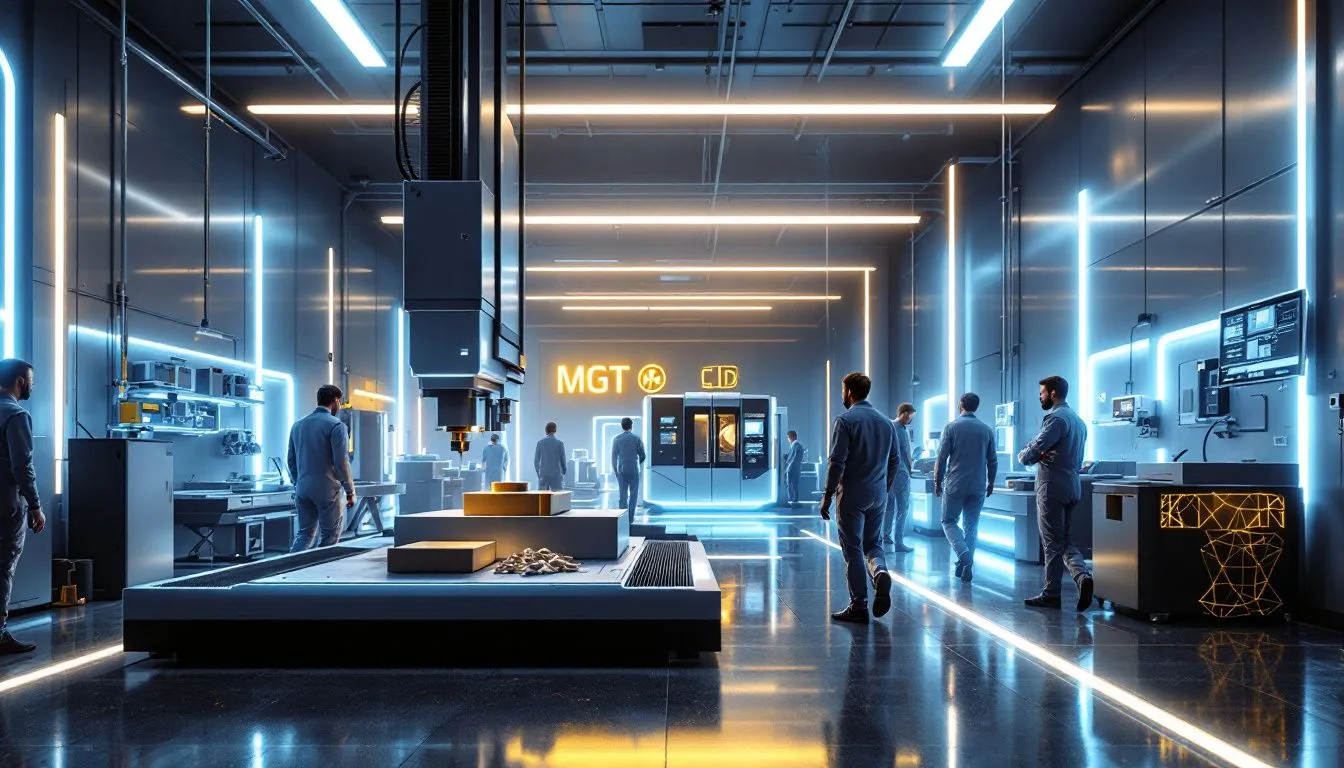
The introduction of CNC prototype machining has revolutionized the field of manufacturing. This technological advancement permits engineers to efficiently refine and examine their groundbreaking designs with high-speed accuracy, expediting product evolution and hastening market entry. The essence of prototype CNC machining is its ability to generate and evaluate prototypes in a cost-effective manner prior to mass production, thus reducing potential risks while ensuring compliance with all quality standards and specifications.
CNC machined prototypes offer a plethora of benefits within the sphere of rapid prototyping. Renowned for its precision and efficiency, it remains a top choice among engineers and designers alike. In contrast to older methods used for creating prototypes, the process involved in CNC prototyping yields quicker results—a critical advantage in today’s fast-paced industrial climate. Such expedited processes not only catalyze the development phase, but also guarantee that these early models are functionally and aesthetically akin to their intended final form.
An impressive attribute about using CNC machined components is their adaptability across various materials such as metals, alloys, wood, or plastics—meeting an array of sector-specific requirements effortlessly. Whether one requires durable metal parts or lighter plastic elements for testing purposes. This technique delivers without complication due both material versatility ensures authentic performance during real-world scenarios providing invaluable insight into future enhancements.
In essence, cnc prototyping transcends mere physical model creation—it strives towards achieving design excellence through continuous optimization trials integral throughout every stage within product innovation cycles. It allows companies to quickly identify correct potential flaws design stages thereby streamlining subsequent production operations in a more economically viable manner.
This document endeavours to shed light on the entirety involved when embarking upon journeys concerning cnc machined types, offering insights respective procedures usages along advising best approaches maximise efficacies outcomes concerning endeavors.
Introduction
The article delves into the detailed realm of CNC prototype machining, underscoring its benefits, uses, and revolutionary effect on the manufacturing sector. Emphasizing heavy automation and high precision, CNC machining reduces the need for manual labor significantly, which facilitates swift and precise creation of prototypes.
Upon concluding this guide, individuals will possess a comprehensive grasp of how utilizing CNC technology can refine their prototyping processes and bolster efficiency in product development.
Understanding CNC Prototype Machining
The CNC prototype machining process has transformed the approach to product development within various industries, employing CNC machine prototypes, cnc machining prototype services, and machines tailored for cnc prototyping.
Through the use of computer numerical control (CNC) technology in these machines, engineers are empowered to fabricate prototypes with exceptional precision that accurately replicate every aspect of the intended design.
This technological advancement is crucial across numerous sectors including aerospace, automotive, consumer electronics, and medical devices—areas where exactitude and dependability are essential.
The importance of CNC prototyping lies in its multiple benefits. It facilitates a faster production pace through reduced cycle times while allowing for the creation of prototypes closely resembling mass-produced items. CNC machining services are versatile and efficient for both rapid prototyping and production of custom parts, benefiting from a wide range of materials and stringent quality certifications. This efficiency boost not only accelerates product evolution, but also aids in early detection and resolution of possible defects before transitioning into large-scale manufacturing processes.
Employing cutting-edge CNC machinery enables manufacturers to refine their operations significantly by utilizing consistent tooling methods for both creating initial samples via prototype machining as well as subsequent component fabrication during full production runs.
What is CNC Prototyping?
CNC prototyping utilizes computer numerical control to craft precise and detailed prototypes, a crucial component in the manufacturing process. CNC prototyping machines are known for their superior tolerance, toughness, and repeatability compared to other manufacturing processes like 3D printing. This subtractive method relies on automated controls that direct cutting tools along with the material being shaped, ensuring meticulous replication of every aspect of the intended design. In the product development stages, CNC prototyping’s role is pivotal for generating tangible models that can be exhaustively evaluated for both aesthetic appeal and practical function before initiating mass production.
An advantage of this technique is its capacity for early detection and correction of design flaws during the development phase. By fabricating prototypes reflective of the end product, manufacturers have an opportunity to identify discrepancies or issues ahead and amend them accordingly. This step significantly enhances cost efficiency while streamlining overall production operations. It holds particular significance when dealing with intricate designs or parts necessitating exacting tolerances where precision takes precedence.
Benefits of CNC Prototyping
CNC prototyping brings a wealth of advantages to the table, particularly in the realm of product development. Its remarkable precision stands out as one of its key benefits, enabling the creation of components that adhere strictly to design specifications with tight tolerances. Such exactitude is vital in sectors where minor discrepancies could greatly affect both safety and functionality. The implementation of CNC machining techniques not only augments product quality but also expedites production processes, delivering prototypes swiftly. Utilizing a CNC machining service ensures the speed and efficiency of obtaining prototypes and production parts, along with quality assurance provided through certifications and a network of qualified suppliers.
The adaptability offered by CNC machining extends into material choices. It supports an extensive assortment of metals, plastics, and composites. This allows producers to select optimal materials for their unique needs, which broadens the spectrum for prototype experimentation and simultaneously positions CNC machining as a financially prudent alternative—particularly valuable when producing small quantities that would otherwise require costly molds or tooling setups.
Typical CNC Prototyping Methods
The practice of CNC prototyping machining comprises a variety of techniques, each tailored to fabricate distinct kinds of parts and shapes, offering precision and efficiency in product development and rapid prototyping. The method known as milling utilizes rotating cutting tools that carve away material from the blank, facilitating the production of complex forms with precision. Such a process is particularly useful for crafting parts demanding intricate design elements and precise detailing.
CNC turning presents another prevalent technique where the workpiece is spun on its axis while a fixed cutting tool trims it into shape. This approach excels in manufacturing tubular or round components like rods and fasteners, delivering exceptional precision for features such as grooves, threads, and conical shapes.
By leveraging multi-axis machining within CNC prototyping operations, there’s an expansion in capability allowing movements across several planes simultaneously. This technology makes it possible to construct highly detailed prototypes that adhere closely to specified tolerances and showcase elaborate designs effectively.
Key Applications of CNC Machined Prototypes
CNC prototype machining makes it feasible to produce functional prototypes quickly and accurately, ensuring cost-effectiveness and efficiency across numerous industries. This process is crucial for validating designs and ensuring functionality before mass production.
Rapid fabrication of reliable, high-quality prototypes via CNC machining is essential in multiple sectors such as:
automotive
aerospace
medical devices
consumer electronics
industrial machinery
This process substantially lowers both the duration and expense associated with conventional prototype creation methods, expediting product development timelines and boosting efficiency.
The adaptability of CNC prototyping demonstrates its value within various industry segments. It plays a critical role ranging from crafting precise parts for automobiles to fabricating detailed elements for medical apparatuses and constructing robust components for aerospace applications. Illustrating how central precision and consistency are in current manufacturing practices.
Automotive Industry
CNC prototype machining plays a vital role in the automotive sector, verifying that components adhere to rigorous performance and safety criteria. By utilizing CNC prototyping, manufacturers can expedite development while minimizing expenses by evaluating parts for operability and compatibility before initiating mass production.
Such swift refinement and examination processes are critical in crafting key automobile elements such as engine parts and transmission mechanisms, enabling a streamlined transition into efficient mass production.
Medical Devices
CNC machining is essential in the medical sector for crafting components with exceptional precision and accuracy, critical for the functionality of devices like surgical tools and implants. The CNC prototyping method yields high-quality functional prototypes that expedite the advancement of sophisticated medical equipment, facilitating swifter examination and implementation.
The ability to rapidly prototype through this machining process is crucial in hastening the introduction of groundbreaking medical innovations into the market with greater speed and efficiency.
Aerospace Components
The aerospace industry relies heavily on CNC machining due to its capacity to produce components with the high precision necessary for ensuring safety and enhancing performance. This technology is crucial in adhering to the rigorous tolerances that aerospace parts must satisfy, which have significant implications for both safety and operational efficacy.
Complex parts such as turbine blades and engine components are commonly fabricated using CNC machining techniques, guaranteeing conformity with exacting safety regulations. This extensive utilization underscores CNC machining’s pivotal role in crafting intricate components within the sector.
CNC Machining Processes for Prototyping
The process of CNC machining for creating prototypes largely utilizes a subtractive method where the excess material is carved out from a solid block to form the intended design. This procedure begins with the generation of an elaborate 3D CAD model, which furnishes essential details on part geometry necessary for the effective operation of CNC machines. The meticulous nature of this practice guarantees that prototypes endure extensive testing before progressing into mass production.
Inherently flexible, CNC machines have the capability to execute various operations such as milling, turning, and drilling on one single workpiece. Such flexibility facilitates the fabrication of parts that are not only complex but also detailed in their construction. Factors like selection of machining processes, complexity inherent in designs, and choice of materials play pivotal roles in affecting both cost-efficiency and quality benchmarks related to CNC prototypes. To ensure optimal results are obtained. Skilled machinists along with engineers make vital decisions concerning these elements.
CNC Milling Process
Utilizing a milling machine, the CNC milling process swiftly removes material to form complex geometries with notable accuracy. This method is exceptionally useful for crafting parts that require intricate designs and precise details, which is crucial in fields such as aerospace and medical where adherence to tight tolerances is of utmost importance.
CNC milling significantly improves the speed at which prototypes can be produced, thus accelerating the prototyping process and increasing its efficiency.
CNC Turning Process
The machining process known as CNC turning involves the use of a cutting tool on a lathe to shape cylindrical parts. It does so by spinning the workpiece while a non-moving cutter trims away material. This technique excels in fabricating elements such as shafts and pins, delivering precise results for features like straight lines, grooves, threads, and conical shapes.
Turning stands apart from milling primarily due to the rotational movement of the piece being worked on rather than the cutting tool itself. This distinction provides particular benefits when it comes to crafting certain geometric configurations within parts.
Multi-Axis Machining
Utilizing multi-axis machining for CNC prototyping affords the flexibility to achieve complex specifications through the use of various axes, ranging from 4 to 9. This advanced process grants high tolerances and facilitates the creation of parts that are otherwise challenging to machine. The precision cutting of elaborate shapes and complex geometries is significantly enhanced by these capabilities, underlining the sophistication offered in CNC prototyping operations.
Material Selection for CNC Prototypes
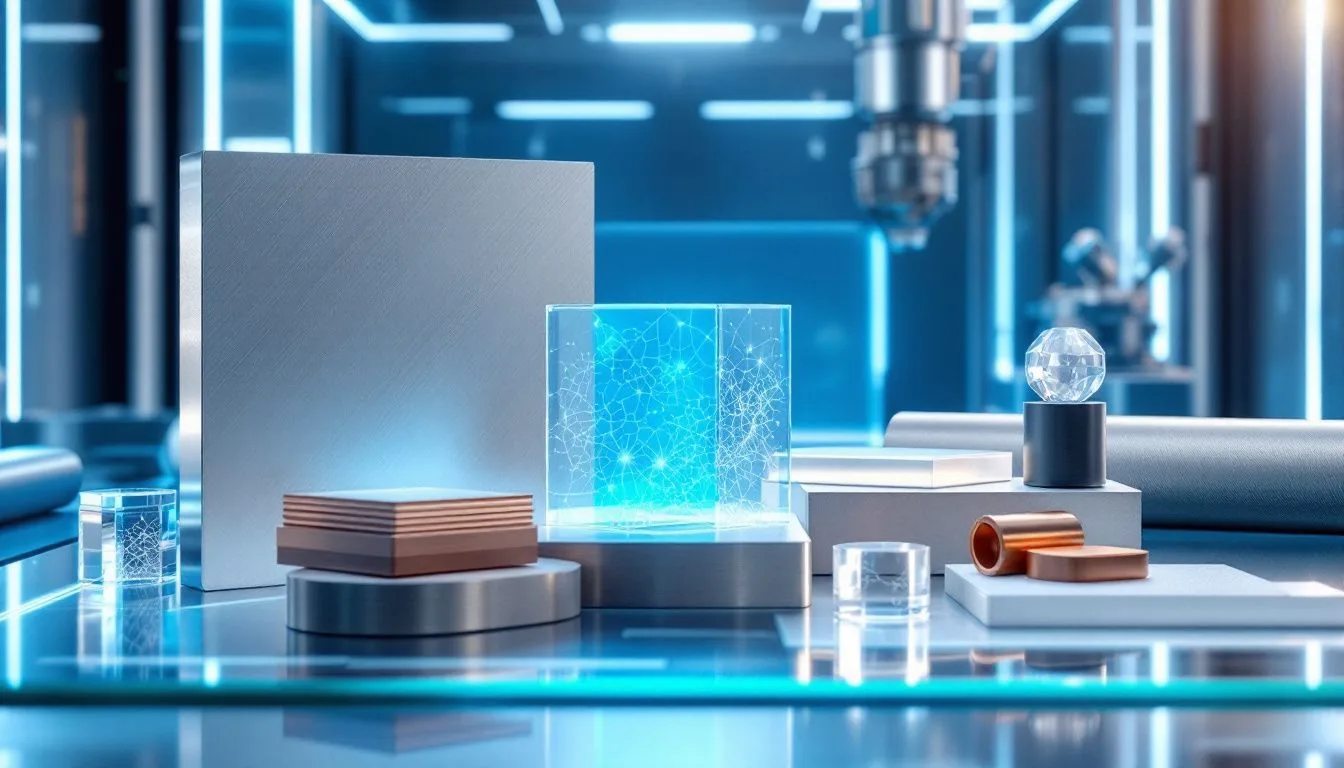
It’s essential to select the appropriate material for obtaining the necessary attributes such as robustness, longevity, and accuracy in CNC prototypes. With a variety of materials accessible including metals like stainless steel, plastics, and composites (each with its distinct advantages suited to different uses), CNC machining offers extensive options. Expertise from seasoned CNC manufacturers can assist in choosing the right material that aligns with particular project needs, thus leading to superior results.
CNC machining is remarkably adaptable due to its capability of working with an array of materials ranging from industrial metals such as aluminum to advanced plastics like ABS and nylon. This adaptability guarantees that prototypes are meticulously tailored according to precise requirements across diverse sectors including automotive, aerospace, medical devices and consumer electronics ensuring they meet industry-specific standards.
Metals
Aluminum alloys like 6061 and 7075 are commonly selected for CNC prototyping due to their optimal mix of weight and strength characteristics. Stainless steel is also a favored material because it provides exceptional corrosion resistance, particularly after undergoing processes such as passivation or electropolishing.
By undergoing these treatments, the materials not only gain increased durability, but their visual qualities are enhanced too. This makes them appropriate for applications that require high precision in the finished components.
Plastics
Numerous plastics such as ABS, nylon, and polycarbonate are commonly employed in CNC prototyping owing to their superior mechanical properties along with their resistance to chemicals. ABS is celebrated for its significant strength, while nylon provides stiffness and maintains stability at elevated temperatures. Polycarbonate is chosen due to its remarkable ability to withstand impacts. These characteristics render these materials ideal for various challenging uses.
Additional plastics like polypropylene and PTFE offer outstanding electrical characteristics as well as resistance against corrosion, thereby expanding the versatility of applications possible with CNC prototyping.
Composites
In CNC prototyping, composite materials such as carbon fiber, fiberglass, and aramid fibers are highly prized due to their superior strength-to-weight ratios along with their resilience against fatigue and corrosion. This makes composites perfectly suited for crafting prototypes that demand durability while minimizing weight, thereby boosting performance and fostering innovation across a multitude of sectors.
Surface Finishes for CNC Machined Parts
Enhancing both the appearance and practicality of CNC machined parts is significantly influenced by their surface finishes. The ‘As-Milled’ finish, characterized by visible tool marks and sharp edges, is typically what one can expect as a standard on these components. To satisfy particular aesthetic or operational demands, there are numerous surface treatments such as sandblasting, anodizing, electroplating and polishing that could be employed to augment the quality of surfaces. For smoother results free from sharp edges and burrs, tumbling stands out as another widely adopted method.
When it comes to producing prototypes via CNC machining processes, they yield superior surface finishes than alternative techniques like injection molding – often achieving smoothness levels akin to 125 uin Ra finish standards. To Bolster metal part durability while simultaneously improving corrosion resistance for robust performance in diverse conditions, additional measures such as zinc plating and electropolishing may be taken into consideration.
Anodizing
The electrochemical procedure known as anodizing is applied to enhance the oxide layer that naturally exists on metal surfaces, especially those of aluminum. This technique encompasses multiple forms such as Type I, II, and III. Each form provides a unique degree of strength and corrosion resistance capabilities. The Type II version of anodizing stands out for its ability to produce a finish with excellent resistance to corrosion, making it appropriate for numerous uses.
Not only does this method increase the durability of parts by offering protection against wear, but also improves their visual appeal by allowing different color choices through anodization.
Powder Coating
The powder coating process entails the application of powdered paint by spraying it onto a component, followed by heat treatment to form a durable layer that is resistant to wear and corrosion. It presents an array of color options for personalization, which is advantageous for parts that demand resilience in conjunction with visual attractiveness.
Especially beneficial for components exposed to severe environments, powder coating delivers a sturdy and enduring surface finish, ensuring prolonged protection and maintenance of appearance.
Electropolishing
The electrochemical procedure known as electropolishing is employed to enhance the surface finish of metal parts by leveling out minute imperfections. By significantly improving the surface condition, this technique diminishes the likelihood of corrosion and is particularly well-suited for applications that require high precision.
By providing a smoother and purer surface, electropolishing ensures enhanced functionality and extends the durability of metal components.
Challenges and Considerations in CNC Prototyping
CNC prototyping brings with it a host of benefits. There are certain hurdles that must be overcome to ensure its success. Geometric intricacies in design can lead to elevated CNC machining costs and extend the duration required for machine preparation and development processes. When compared with alternative methods such as 3D printing, CNC machining tends to produce more material waste which could affect the total cost of materials used. Engaging experienced manufacturers is beneficial as they offer expert advice on best practices that help adeptly tackle these challenges.
In considering the expenses associated with CNC prototyping, several elements play a critical role in determining cost-effectiveness. Factors like design complexity, precision specifications demanded by the project, along with material selection all contribute to shaping overall expenditures related to CNC machining endeavors.
Geometrical Limitations
During the prototyping process, CNC machining encounters obstacles with complex internal geometries because cutting tools might struggle to access and shape small, intricate spaces. This constraint can affect design agility and prolong the time it takes for development. Hence, it is critical for engineers to take these limitations into account while designing in order to enhance the efficiency of prototype creation.
Material Waste
CNC machining inherently generates significant material waste, as it involves cutting away excess material from a solid block to create the desired shape. While some of this waste can be recycled, the increased material usage leads to higher material costs.
This is a notable drawback compared to additive manufacturing methods like 3D printing, which produce less waste.
Cost Factors
Several variables, such as the intricacy of the design, the level of precision needed, and material selection, can impact the expenses related to CNC prototyping. It tends to be pricier than alternatives like 3D printing due to its need for costly workpieces and raw materials as well as highly skilled labor.
Nevertheless, CNC prototyping offers a significant advantage in its capacity to detect and correct design errors early on. This ability can lead to reduced costs in mass production and heightened efficiency throughout the manufacturing process.
Comparing CNC Prototyping with Other Methods
CNC prototyping is often juxtaposed with alternative techniques like 3D printing and injection molding, given their unique methods for crafting prototypes. The CNC machining process involves the subtractive removal of material to achieve the targeted shape. On the other hand, 3D printing builds a prototype by adding layers upon layers in an additive manner. Both strategies offer their own set of strengths and weaknesses, necessitating manufacturers to judiciously select which path best aligns with their particular project demands.
The distinction between CNC machining and 3D printing can notably be seen in aspects such as precision level and material efficiency. CNC machines are capable of churning out parts that meet strict tolerances swiftly, hence they’re more suitable for projects where heightened accuracy and robustness are mandatory. Conversely, while 3D printing stands out when it comes to fabricating components with intricate geometries unfettered by constraints typical of CNC machinery. Its technique may falter when dealing with detailed internal features, leading to potentially less dense creations compared to those produced via conventional means.
CNC vs. 3D Printing
In evaluating the project’s particular needs, a comparison between CNC machining and 3D printing must be made. The high precision and robust material integrity provided by CNC machining make it ideal for components that require resilience to intense stress and usage. This subtractive process leads to considerable material wastage.
Conversely, 3D printing is proficient in fabricating intricate shapes while preserving materials due to its additive manufacturing approach. Parts produced through this method tend to exhibit higher porosity and reduced strength compared to their machined counterparts.
CNC vs. Injection Molding
CNC machining is better suited for creating distinctive components or prototypes in small quantities because it avoids the need for costly molds and tooling that are necessary for injection molding. Injection molding, on the other hand, becomes more economical on a per-unit basis when used for large-scale production runs, making it ideal for mass manufacturing.
When choosing between CNC machining and injection molding, one must consider various elements like the volume of production required, the complexity of the parts to be manufactured, and budget constraints.
Tips for Effective CNC Prototyping
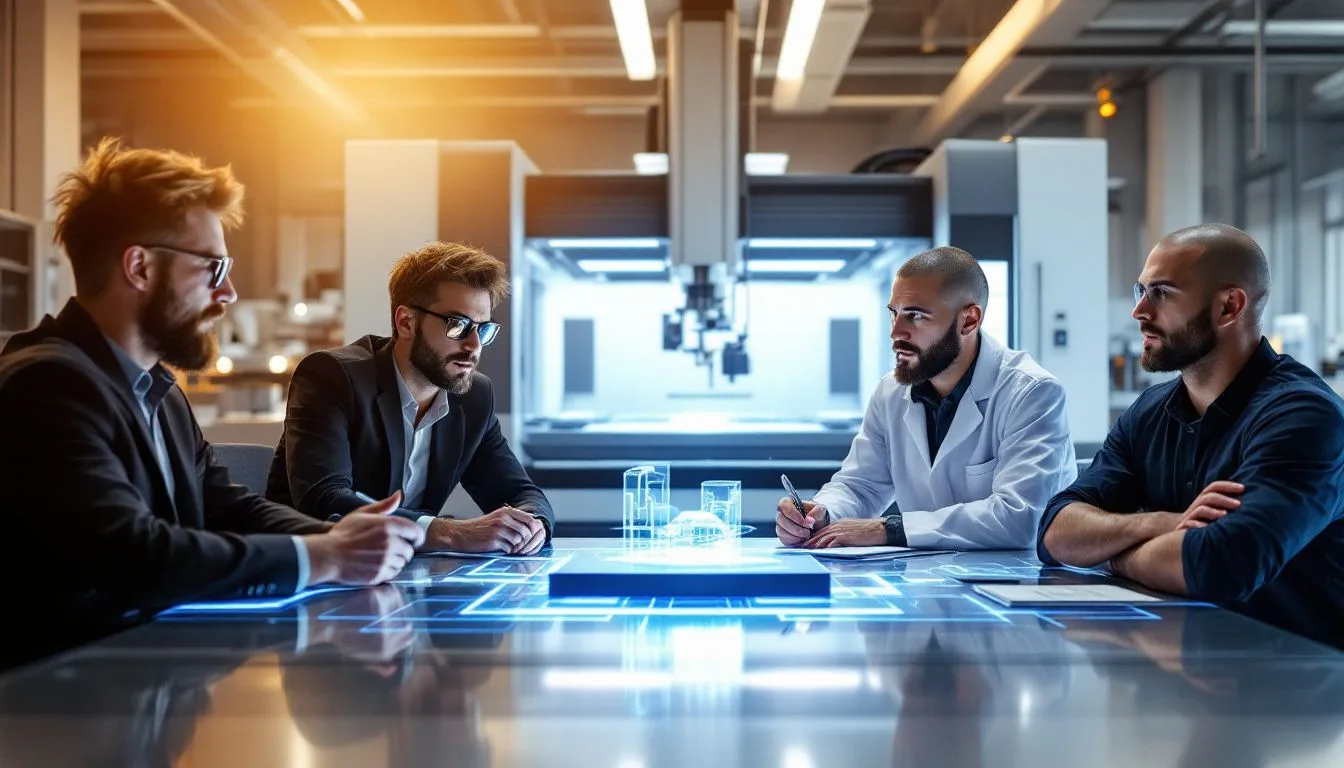
In order to achieve superior results and efficiency in the CNC prototyping process, it is essential to adopt a deliberate approach. Consider these vital strategies.
Minimize design complexity for quicker machine setups and reduced production timeframes.
Limit intricate elements within designs to diminish expenses while increasing machining precision, thereby facilitating the attainment of anticipated outcomes with greater ease.
Apply standard tolerances as they contribute towards maintaining budget-friendly production costs without compromising on quality.
Adhering to these guidelines can significantly boost both the efficacy and efficiency of your CNC prototyping procedures.
Forging partnerships with manufacturers who possess extensive experience is also pivotal for triumphant CNC prototyping endeavors. Such experts can optimize prototyping processes resulting in more streamlined production operations that lead not only to heightened quality but also faster outcomes.They are adept at navigating geometric limitations and ensuring prototype fidelity in terms of meeting designed specifications as well as functional requirements.Collaboration with these adept practitioners substantially increases the likelihood of successful completion within the sphere of CNC prototyping ventures.
Simplify Design Complexity
For improved efficiency in CNC prototyping, it’s crucial to steer clear of elaborate designs and concentrate on creating simpler parts. Simplifying the designs can result not only in reduced expenses but also heightened precision during machining.
By breaking down complex designs into more basic elements, production can be greatly optimized leading to cost savings. By limiting the number of small features within a design, one can enhance machining effectiveness and diminish the amount of time required for processing.
Utilize Standard Tolerances
Using established tolerances ensures that production expenses are kept in check while still maintaining high-quality outcomes. By adopting commonly recognized tolerance thresholds, the manufacturing process becomes more streamlined and achieving specified goals is simplified.
Implementing standard sizes for holes allows for swift machining using readily accessible drill bits, thereby boosting efficiency even further.
Partner with Experienced Manufacturers
Working alongside skilled CNC prototyping manufacturers is crucial for attaining the best outcomes in prototyping endeavors. These expert manufacturers enhance the efficiency of prototyping processes, resulting in improved production speed and superior quality results. They consider geometric limitations to guarantee that prototypes conform to design expectations and fulfill functional demands.
Engaging with veteran experts significantly increases the chances of success in CNC prototyping ventures.
Case Studies of Successful CNC Prototyping Projects
Examples from the real world where CNC prototyping has been successfully employed showcase the significant influence this technology wields. When companies work in tandem with expert CNC manufacturers, they can produce prototypes that are of superior quality and accuracy, thus guaranteeing that these designs adhere to required specifications and perform up to set standards.
The case studies reflect how critical it is for successful CNC prototyping projects to maintain precise tolerances and implement processes that are streamlined and efficient.
Automotive Component Development
During a robotic assembly project in the automotive sector, over 70 components were swiftly produced within a fortnight using CNC machining as part of rapid prototyping efforts. This method of small-scale production effectively reduced potential financial risks associated with defective parts, demonstrating how CNC rapid prototyping can be employed to create critical automotive parts accurately and expediently.
Medical Device Innovation
The prototyping process for advanced medical devices is significantly expedited by the critical role of CNC machining. Utilizing common methods like milling, turning, and multi-axis machining allows for the creation of exact prototypes with high accuracy and a wide variety of materials.
Such efficiency and precision in CNC machining contribute immensely to enhancing the prototyping stage, resulting in accelerated development timelines for medical devices.
Aerospace Part Precision
The production of an aerospace turbine blade showcases the effectiveness of CNC machining in attaining the required precision and improving overall performance. The criticality of CNC machining in this sector stems from its ability to produce intricate components that adhere to stringent tolerances, which are imperative for maintaining aerodynamic properties and safety standards.
Incorporating multi-axis machining within this process is vital due to its capability for exacting cuts on complex contours and precise geometries. Such high-level precision is indispensable for applications within the aerospace industry where accuracy is paramount.
Summary
To sum up, the revolutionary CNC prototype machining has significantly redefined product development by delivering outstanding precision, efficiency, and adaptability. Mastery of different operations, materials choices, and optimal procedures allows manufacturers to enhance their prototype machining initiatives resulting in superior quality products. The adoption of CNC technology facilitates a faster development process while guaranteeing adherence to rigorous performance and safety criteria. As various sectors persist in innovating and progressing forward, it is clear that CNC prototyping will continue to play an indispensable role in materializing concepts into tangible forms.
Frequently Asked Questions
What are the typical lead times for CNC prototypes?
CNC prototypes can typically be completed in 1-3 days for simple designs and 5-7 days or longer for more complex ones.
Stay focused and plan accordingly to make the most of your project timeline!
What surface treatment options are available for CNC prototypes?
For your CNC prototypes, consider surface treatments like sandblasting, anodizing, electroplating, and polishing to enhance their appearance and durability.
Choosing the right finish can not only elevate your prototype’s aesthetic but also improve its performance!
What industries are suitable for CNC prototypes?
CNC prototypes are perfect for automotive, aerospace, medical devices, consumer electronics, and industrial equipment industries.
Embrace the opportunity to innovate and streamline production in these evolving fields!
How does CNC prototyping help in minimizing production costs?
CNC prototyping significantly reduces production costs by identifying design flaws early, which leads to efficient testing and optimized materials.
Embrace this method to enhance your production efficiency and save money!
How does LKprototype ensure the dimensional accuracy of CNC prototypes?
LKprototype ensures the dimensional accuracy of CNC prototypes through the use of precise CNC equipment, strict control of processing parameters, and thorough post-testing.
Trust in their methods to deliver the accuracy you need!
Design Considerations for CNC Prototype Machining
When embarking on a CNC prototype machining project, thoughtful design considerations are paramount to ensure efficient and effective manufacturing. Here are some key factors to keep in mind:
Material Selection: Choosing the right material is crucial for the success of your CNC prototype machining project. Consider the material’s strength, durability, and cost. Metals like aluminum and stainless steel, as well as plastics such as ABS and polycarbonate, are popular choices due to their machinability and performance characteristics.
Part Geometry: Design your part with CNC machining in mind. Avoid overly complex geometries and features that may be challenging or impossible to machine. Simplifying the design can lead to faster production times and lower CNC machining costs.
Tolerances: Specify tolerances that are achievable with CNC machining. While tight tolerances can be met, they may require additional machining operations or specialized equipment, which can increase costs. Balancing precision with practicality is key.
Surface Finish: Consider the required surface finish for your part. CNC machining can produce high-quality finishes, but additional finishing operations like polishing or anodizing may be necessary to meet specific aesthetic or functional requirements.
Tool Access: Ensure that your part design allows for easy tool access. This consideration helps reduce machining time and improves accuracy. Features that are difficult to reach can complicate the CNC machining process and increase production time.
Fixture Design: A well-designed fixture is essential for holding the part securely during machining. Proper fixture design can enhance accuracy and reduce machining time, leading to better overall results.
By addressing these design considerations, you can optimize your CNC prototype machining process, resulting in high-quality, cost-effective prototypes.
Choosing a CNC Machine for Prototyping
Selecting the right CNC machine for your prototyping needs is a critical step in ensuring successful outcomes. Here are some key factors to consider:
Machine Type: The type of CNC machine you choose should align with your project requirements. Common options include milling machines, turning machines, and grinding machines. Each type has its strengths and is suited for different tasks within the CNC machining process.
Machine Size: Ensure that the CNC machine can accommodate the size of your part. Consider the maximum part size and the machine’s working envelope. A machine that is too small may limit your ability to produce larger prototypes, while an oversized machine may be unnecessary for smaller parts.
Axis Configuration: The axis configuration of the CNC machine is another important consideration. Options include 3-axis, 4-axis, and 5-axis machines. More axes allow for greater flexibility and the ability to machine complex geometries with precision.
Spindle Speed: The spindle speed of the CNC machine should match your project requirements. Higher spindle speeds are often necessary for machining certain materials, such as metals, to achieve the desired finish and accuracy.
Tooling: Consider the tooling required for your project. Choose a CNC machine that can accommodate the necessary tooling and has a suitable tool changer. The right tooling setup can significantly impact the efficiency and quality of the machining process.
By carefully evaluating these factors, you can select a CNC machine that meets your prototyping needs and ensures high-quality results.
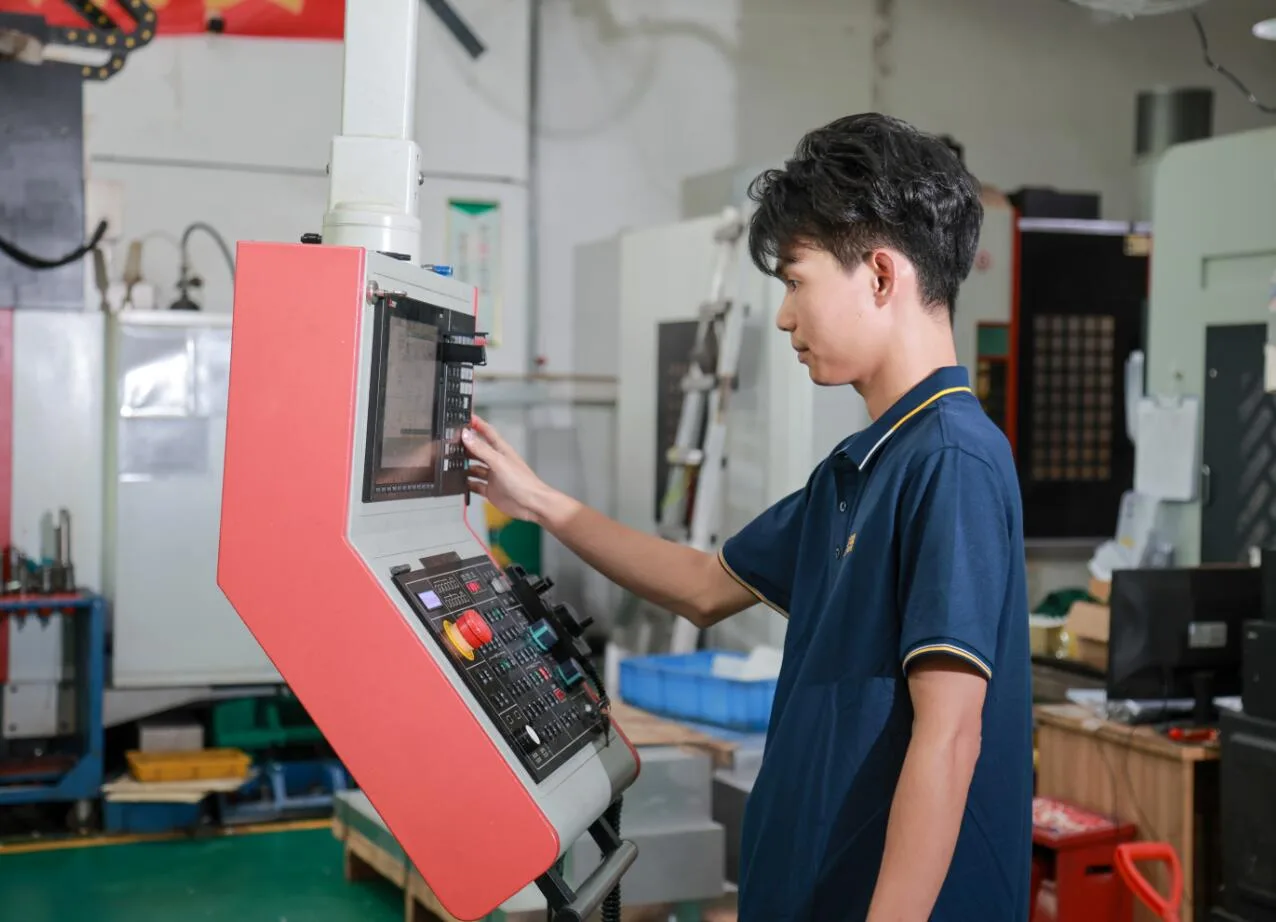
CNC Prototype Machining Services and Capabilities
CNC prototype machining services offer a wide range of capabilities to support diverse project requirements. Here are some key services and capabilities to consider:
Rapid Prototyping: CNC prototype machining services excel in rapid prototyping, allowing for quick turnaround times. This capability is essential for meeting tight project deadlines and accelerating the product development cycle.
Precision Machining: CNC machines are renowned for their ability to produce parts with high precision and accuracy. This level of detail is crucial for prototypes that need to closely match final product specifications.
Material Versatility: CNC machines can work with a wide variety of materials, including metals, plastics, and composites. This versatility allows for the creation of prototypes that meet specific material requirements and performance standards.
Complex Geometries: CNC machines are capable of producing complex geometries and intricate features that may be challenging or impossible to achieve with other manufacturing processes. This capability is particularly valuable for industries that require detailed and precise components.
Low-Volume Production: CNC prototype machining services can accommodate low-volume production runs, making them ideal for projects that do not require large quantities of parts. This flexibility helps manage costs and reduces waste.
Design for Manufacturability (DFM): Many CNC prototype machining services offer design for manufacturability (DFM) feedback. This service helps optimize part designs for CNC machining, ensuring that prototypes are both functional and cost-effective.
By leveraging these services and capabilities, you can enhance your CNC prototyping process, resulting in high-quality prototypes that meet your project requirements and accelerate your path to market.
-----------------------------------------------------------------------------------------------------------
Still, need help? Contact Us: lk@lkprototype.com
Need a Engineering structure prototype, product appearance prototype, and whole machine function model quote? Quote now