Cast metal parts are essential components created by pouring molten metal into a mold, allowing it to solidify into a desired shape. This versatile manufacturing process is vital for producing complex and durable parts used in industries ranging from automotive to aerospace. In this article, we will explore the techniques and applications of cast metal parts, offering insights into their advantages and the various methods involved in their production.
Key Takeaways
Metal casting involves pouring molten metal into a mold to create durable, intricate parts and is widely used across various industries, including automotive, aerospace, and medical.
The metal casting process includes stages such as pattern creation, mold making, pouring, cooling, and cleaning, with diverse methods like sand casting and die casting catering to different production needs.
Modern technologies like 3D printing and advanced simulation software are enhancing the efficiency and precision of metal casting, while sustainable practices focus on recycling and energy-efficient techniques to minimize environmental impact.
Understanding Cast Metal Parts
The manufacturing process known as metal casting is a venerable technique that encompasses the pouring of liquid metal into a mold, resulting in the formation of a solid metal part. This approach has proven to be crucial for fabricating complex shapes with dependable qualities, which are utilized throughout numerous industries such as manufacturing, technology, and transportation.
Metal casting boasts remarkable versatility in its capacity to produce items whose weights span from mere grams to several thousand pounds.
What are cast metal parts?
The manufacturing of cast metal parts involves the process where molten metal is filled into a pre-shaped mold, which then cools and takes on a solid state conforming to the intricate contours designed within the mold. This technique allows for complex designs that might be challenging or unfeasible with other production methods. As it transitions from liquid to solid, the molten metal assumes the detailed geometry of its container. It’s crucial during this phase for engineers to account for any contraction in size as a result of cooling so that finished components align precisely with their intended dimensions.
When it comes to casting, non-ferrous materials like aluminum, zinc, and magnesium are frequently chosen due to their advantageous attributes such as being lightweight and having superior resistance against rust. These metals facilitate the creation of durable yet light components across various industries — from automotive sectors producing vehicle elements to healthcare fields manufacturing medical apparatuses.
Key benefits of cast metal parts
Metal casting stands out for its economic efficiency compared to the process of machining solid metal, especially when fabricating complex shapes. The cost and effectiveness of achieving intricate designs are greatly enhanced through casting as opposed to CNC machining methods. Sand casting, in particular, is widely utilized due to its low initial costs and ability to quickly manufacture elaborate components, offering a significant advantage for manufacturers.
In terms of design versatility and judicious use of materials, metal casting excels. Aluminum is often chosen for creating robust yet lightweight parts that play a critical role in sectors like aerospace and automotive industries. Metal casting’s proficiency in crafting detailed and accurate parts with little material waste makes it the method of choice for producing items on a large scale.
The Metal Casting Process Explained
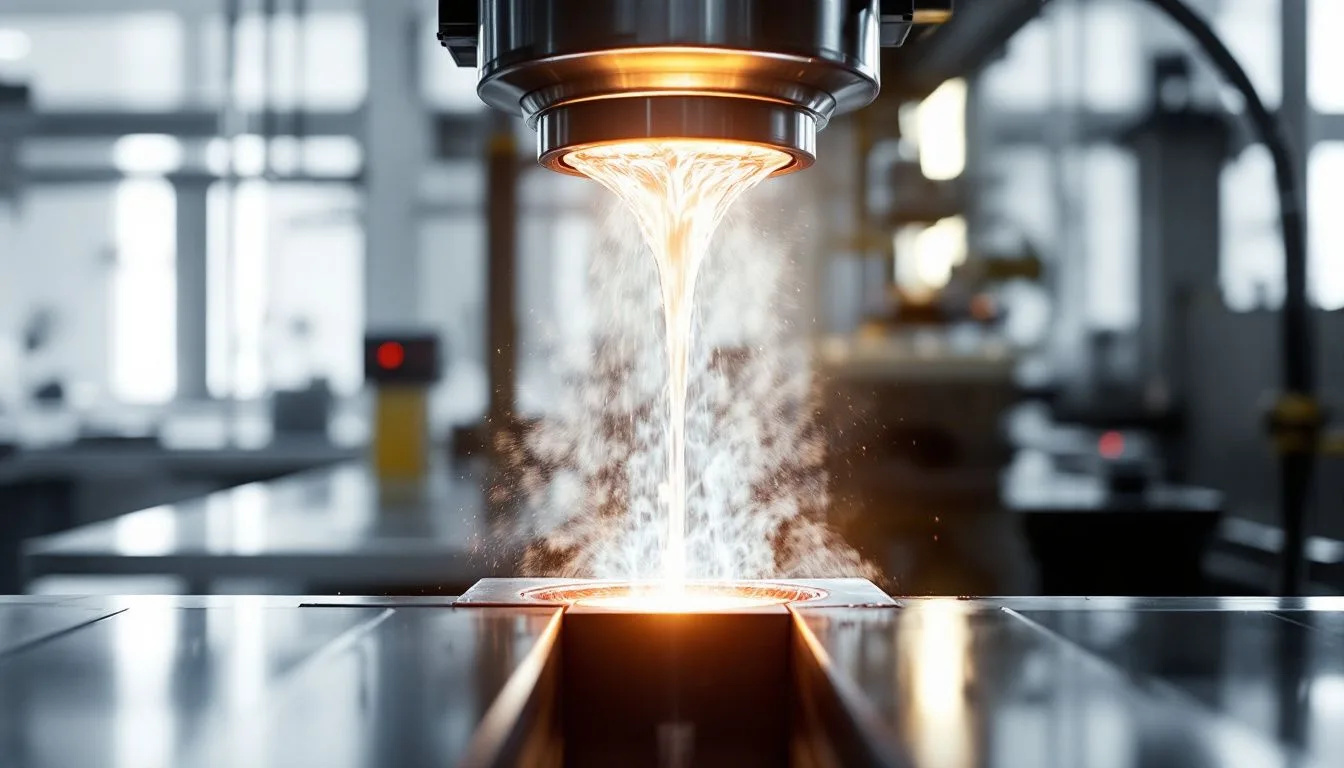
The metal casting process is a detailed and exceptionally effective method of manufacturing that has been perfected over thousands of years. It involves critical phases which include the creation of a pattern, mold construction, the pouring of molten metal into the mold, followed by cooling and solidification. The final steps involve extraction and purification of the cast using established metal casting techniques.
Each phase is integral to guaranteeing that the end product meets high standards for quality and precision.
Creating the pattern
Metal casting commences with the fabrication of a pattern, which sets the outline for both the mold and the eventual component. This crucial first phase entails fashioning a prototype mirroring the intended part out of materials like wood, metal, plastic, or plaster to guarantee precise dimensions.
Serving as a blueprint, this pattern is critical in shaping the mold that envelops it — establishing essential groundwork for all subsequent steps within the casting process.
Making the mold
In the process of casting metal, once the pattern is finalized, crafting the mold becomes the subsequent task. The selection of mold material plays a critical role and varies from options like sand to plaster, refractory slurry, or even liquid ceramics depending on what metal is being cast as well as specific requirements for the final product’s characteristics.
Owing to its affordability, abundance, and resistance to high temperatures, sand proves optimal for expendable molds intended for single use. This attribute underpins why sand casting remains a widely adopted technique. Conversely, permanent molds are fabricated using metals that possess melting points surpassing those of the metals meant to be cast within them. These durable molds can withstand numerous cycles of usage.
The intricacies involved in creating a mold may also entail employing cores which serve in establishing internal spaces and designing pathways such as sprues and gates that facilitate an uninterrupted flow into every region within the mold cavity. To generate complicated shapes in moulds requires impressing a design onto one half of a split mould before fastening it securely with its counterpart.
Pouring molten metal
Once the mold has been prepared, metal is heated until it liquefies and then the molten metal is transferred into the cavity of the mold.
The sand casting process stands out for its affordability in terms of setup expenses and its adaptability to complex shapes when introducing the molten material during casting.
Cooling and solidification
Once the molten metal is poured into the mold, it commences the process of cooling and solidification, conforming to the contours of the mold. The outcome regarding both shape and integrity of the cast metal part hinges on this crucial phase.
Allowing ample time for cooling and solidification is imperative to ensure that the metal part attains its intended characteristics and measurements.
Removing and cleaning the casting
Upon the metal becoming solid, it is extracted from its mold. This extraction can be accomplished through a variety of methods including shaking with vibrations, cleansing with high-pressure water jets, or utilizing ejector pins to push out the casting. When dealing with expendable molds such as those used in sand casting, the common practice involves breaking apart the mold to access and retrieve the cast item. Conversely, for operations involving molds that are designed for multiple uses, ejector pins tend to be favored in order not to compromise the integrity of these reusable forms.
The subsequent phase entails purifying the cast object by eliminating any superfluous materials so as to attain an appropriate surface quality. To remove remnants of molding material and enhance their appearance, refinement steps like vibrational motions may use manual tools or pressure washing might come into play depending on requirements. Specifically within investment casting procedures, destruction and agitation techniques often employ vibrating platforms shake off encasing shell layers guaranteeing a cleaned result fitting onward finishing touches if required.
Types of Metal Casting Processes
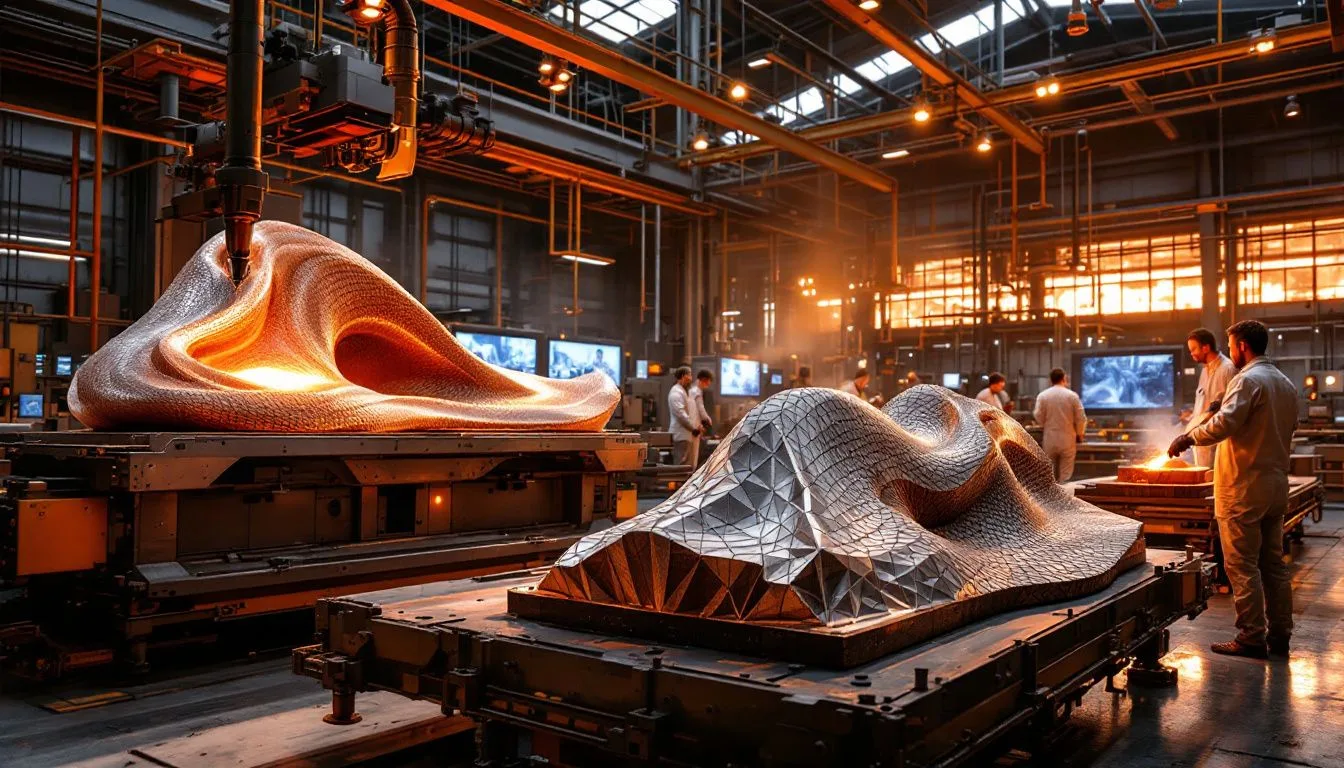
Metal casting encompasses a variety of processes, each distinct in its methods and benefits. Broadly, these can be classified into two categories: those that use expendable molds—including sand casting and investment casting—and those employing non-expendable or permanent molds, such as die casting and permanent mold casting.
Sand casting
Metal casting frequently employs sand casting due to its efficiency in using sand as the mold material. This technique is adept at creating substantial and sturdy items such as ornate fences, cast iron cookware, and automobile engine components. The patterns used for forming these molds are intentionally made larger to compensate for any shrinkage that occurs when the metal cools down. Sand casting is particularly appreciated for its economic advantages and capacity to facilitate intricate shapes without requiring a high initial investment.
Compared with alternative methods, this process does not yield the finest surface finish. It involves one-time use of molds. Various types of sands can be employed depending on specific needs: while green sand contains wet clay which hardens upon drying, air set sand incorporates dry particles combined with an adhesive agent.
Die casting
Die casting is a manufacturing process that involves forcing molten metal into a steel mold cavity using high pressure. This technique is highly favored for mass production since the robustness of the metal molds allows them to be employed repeatedly. The equipment utilized in die castings comprises a reservoir for holding melted metal, a metallic mold, and an apparatus for injection. The application of significant pressure during injection contributes to both precision and expedited processing times, rendering die casting particularly suitable for the swift fabrication of complex parts.
Materials often chosen for this process include lightweight yet strong elements like aluminum and magnesium. Die casting’s utility spans across various sectors with critical demands such as aerospace and automotive industries, which necessitate intricate components manufactured with exacting tolerances.
Investment casting
Investment casting, often referred to as lost wax casting, is celebrated for its capacity to fabricate parts with high complexity and precision. The technique initiates with the formation of a wax pattern through metal dies. Subsequently, this pattern is enveloped in a ceramic substance to generate the mold. This approach is frequently employed when manufacturing detailed structures essential for medical equipment and aerospace parts.
Despite its accuracy benefits, investment casting typically incurs higher costs compared to sand casting. It also possesses restrictions on the dimensions and depth of holes it can produce effectively, potentially limiting its use across various applications.
Other casting methods
Centrifugal casting employs a rotational force that directs molten metal into molds, which is perfect for creating cylindrical shapes such as pipes. This technique improves the density of the finished product and minimizes imperfections, making it exceptionally suitable for parts with a circular cross-section.
In contrast, continuous casting involves an uninterrupted stream of molten metal to form materials like tubes and slabs in a consistent shape. It boasts high production speeds, improved precision in final products, and diminished material waste.
Both centrifugal and continuous casting methods offer distinct benefits tailored to meet the specific needs of different components being manufactured. These processes serve as complementary options to conventional casting techniques, providing specialized solutions across various industry sectors.
Choosing the Right Metal for Casting
It is essential to select an appropriate metal for casting to ensure that the final components exhibit the necessary properties and performance. This choice involves evaluating aspects like mechanical characteristics, resistance to corrosion, and the particular demands of its intended application.
Common casting metals
Casting frequently involves a variety of metals, such as:
Aluminum, which stands out for creating components that are both strong and lightweight. This quality makes aluminum particularly attractive for use in the industrial and automotive sectors.
Magnesium, which is prized for its outstanding stiffness-to-weight ratio, thereby becoming a common choice in manufacturing automotive parts.
Zinc alloys like ZAMAK earn preference due to their excellent properties suitable for casting. This attribute renders them perfect choices for components in vehicles and electronic devices.
For medical applications where robust mechanical attributes and corrosion resistance are essential criteria, stainless steel castings are the go-to option. These materials bring forth an array of characteristics tailored to meet various casting needs. Consequently, they facilitate the crafting of top-tier parts spanning multiple sectors.
Factors to consider
In the selection process for a metal suitable for casting, numerous variables must be taken into account. Critical to this decision are the mechanical properties needed — these encompass resistance to temperature extremes, robustness, and the capacity to withstand tensile stress. If the final product is destined for environments that are aggressive or corrosive in nature, its ability to resist corrosion becomes crucial.
The determination of which metal to use influences more than just how well the end component functions. It also affects both efficiency and cost within the scope of the casting process itself. Manufacturers who meticulously assess these considerations will enhance their chances of choosing an optimal metal tailored to meet their unique requirements effectively.
Applications of Cast Metal Parts
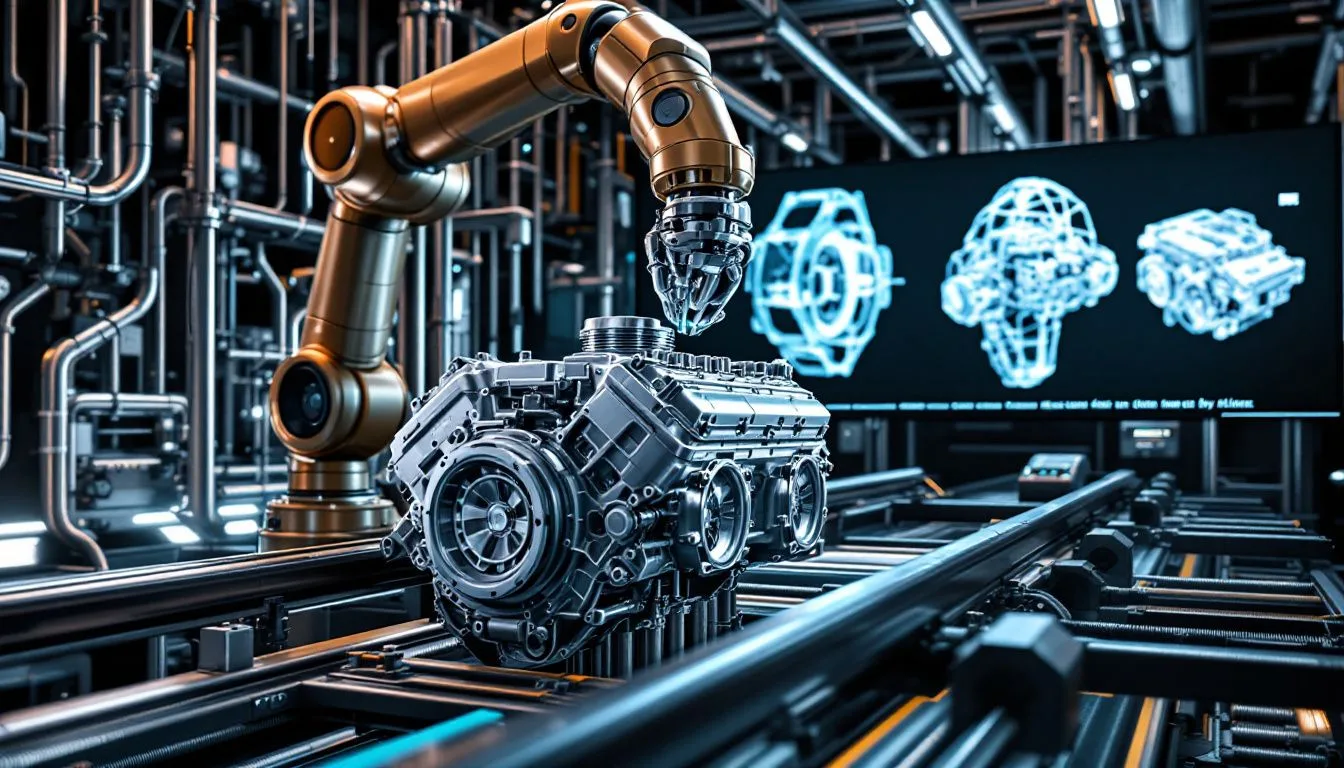
Components made from cast metal are essential in various sectors such as automotive, aerospace, medical, and energy due to their robustness, adaptability, and ability to be formed into complex shapes. This makes them irreplaceable in contemporary production processes.
Automotive industry
The metal casting process plays a crucial role in the automotive industry by enabling the manufacture of strong and intricate parts. The selection of zinc for its superior strength, stability, and outstanding conductivity attributes renders it perfect for numerous automotive uses. Notably used to cast engine blocks and transmission cases, these parts demand exactitude as well as durability to guarantee both performance excellence and dependability within vehicles.
Employing various casting methods during manufacturing allows for the creation of metal components that are capable of enduring the rigorous conditions typical in automobile settings, such as extreme temperatures and significant mechanical forces. This aspect of producing cast metal items ensures adherence to high-quality standards while also achieving cost efficiency – essential factors considered by manufacturers when creating parts designed for vehicular use.
Aerospace industry
In the aerospace sector, parts crafted from cast metal are valued for their combination of low weight and robust strength. These attributes play a significant role in enhancing fuel economy and boosting performance levels. Aluminum stands out as an especially adaptable material that can withstand high temperatures during operations, marking its importance for use in aerospace contexts.
The manufacturing of turbine engines and the structural elements of airplanes often relies on components made from cast metal due to the necessity for exactness and resilience. The casting process permits the creation of intricate parts with precise specifications, guaranteeing that these components satisfy the stringent requirements essential for safe and effective air travel.
Medical devices
Medical devices, including prosthetics and imaging machinery, depend greatly on the use of cast metal components. It is critical for these metal parts to be both accurate and biocompatible to maintain safety and functionality in healthcare settings. The inclusion of cast metal parts improves not only the performance but also the dependability of medical equipment, thereby supporting improved patient results and propelling advancements in medical technology.
Enhancing Metal Casting with Modern Technologies
Advanced technologies are transforming the casting process for metal, improving its accuracy and efficiency. The implementation of 3D printing along with sophisticated simulation software is crucial in elevating the standard while diminishing the production time required for metal parts created through metal casting.
3D printing in casting
The incorporation of 3D printing technology into the metal casting process substantially reduces the amount of material waste and facilitates swift pattern production. Patterns or molds can be created in a matter of hours using a 3D printer, slashing the traditional lead times from several weeks to just a few days. This technological leap not only expedites the manufacturing cycle, but also reduces expenses by cutting back on dependencies on various machinery or external service providers.
Enhancements like High Temp Resin, which is resistant to high temperatures, have pushed forward the boundaries of what’s possible with 3D printing for metal casting applications. These innovations allow for crafting patterns that are intricate and superior in quality, leading to castings with better surface finishes and greater dimensional precision.
Advanced simulation software
In contemporary metal casting, sophisticated simulation software plays a crucial role by enabling manufacturers to anticipate possible imperfections prior to the commencement of production. These simulations assist in refining the pour method and guarantee appropriate ventilation within the mold, thus mitigating porosity along with various typical flaws associated with metal casting.
Utilizing this technology significantly bolsters quality assurance measures, diminishes material waste, and boosts efficiency across all aspects of the metal casting process.
Finishing Techniques for Cast Metal Parts
Refineing the aesthetics and precision of components made from cast metal is significantly dependent on finishing techniques. Such processes are essential to guarantee that the end product adheres to the expected quality standards and specifications.
Sandblasting
Abrasive blasting, commonly referred to as sandblasting, employs a stream of abrasive particles propelled by high-pressure air to clean the surface of castings. This technique is efficient for eradicating impurities from the cast surface and ensuring a more refined finish.
The process of sandblasting plays an essential role in readying cast parts for additional finishing procedures or their ultimate application.
Anodizing
The process of anodizing employs an electrolytic passivation technique to augment the natural oxide layer’s thickness on aluminum components. It bolsters their resistance to corrosion and permits a range of color finishes, thereby improving both the durability and visual appeal of these parts.
Especially advantageous for aluminum parts that are subjected to severe conditions, anodizing plays a crucial role in maintaining their integrity and function.
Polishing
Abrasive materials and polishing compounds are utilized in various polishing methods to produce a reflective, mirror-like surface on components made from cast metal. By decreasing the roughness of the surface, these processes improve light reflectivity and yield a smooth, glossy finish.
Depending on the type of material used for casting and the level of sheen required, diverse techniques can be employed to polish cast parts. These techniques significantly influence how glossy or lustrous the final product appears.
Quality Control in Metal Casting
Ensuring that cast parts adhere to performance and reliability criteria is crucial within the metal casting process, which necessitates stringent quality control measures. By adopting thorough inspection methodologies, potential problems can be identified and rectified promptly, preserving the final product’s integrity.
Inspection methods
Various methods are employed to inspect cast parts, including mechanical tests, assessments of chemical makeup, and non-destructive approaches like ultrasonic or radiographic examinations. To spot defects such as surface cracks or cavities prior to the final quality assessment phase, visual inspections are conducted on the metal parts. The use of precise instruments for dimensional inspection is crucial for verifying that the specifications provided by customers are met accurately.
To confirm that alloy compositions align with required standards, chemical analysis procedures such as X-ray fluorescence testing play a key role in inspections. Techniques like magnetic particle inspection and liquid penetrant examination serve to detect any imperfections on the surfaces without causing harm to the castings.
These aforementioned practices form an essential framework for guaranteeing both high-grade performance and robustness within metal parts created through casting processes.
Common defects and solutions
When metal is in the process of solidifying during metal casting, shrinkage defects can arise due to contraction as the metal cools. This may result in cavities within the cast piece. To combat this issue, incorporating risers and creating molds that promote a regulated cooling process for the cast metal are effective strategies.
By proactively tackling these imperfections at an early stage, one can enhance the caliber of the end product considerably.
Environmental Impact and Sustainability in Metal Casting
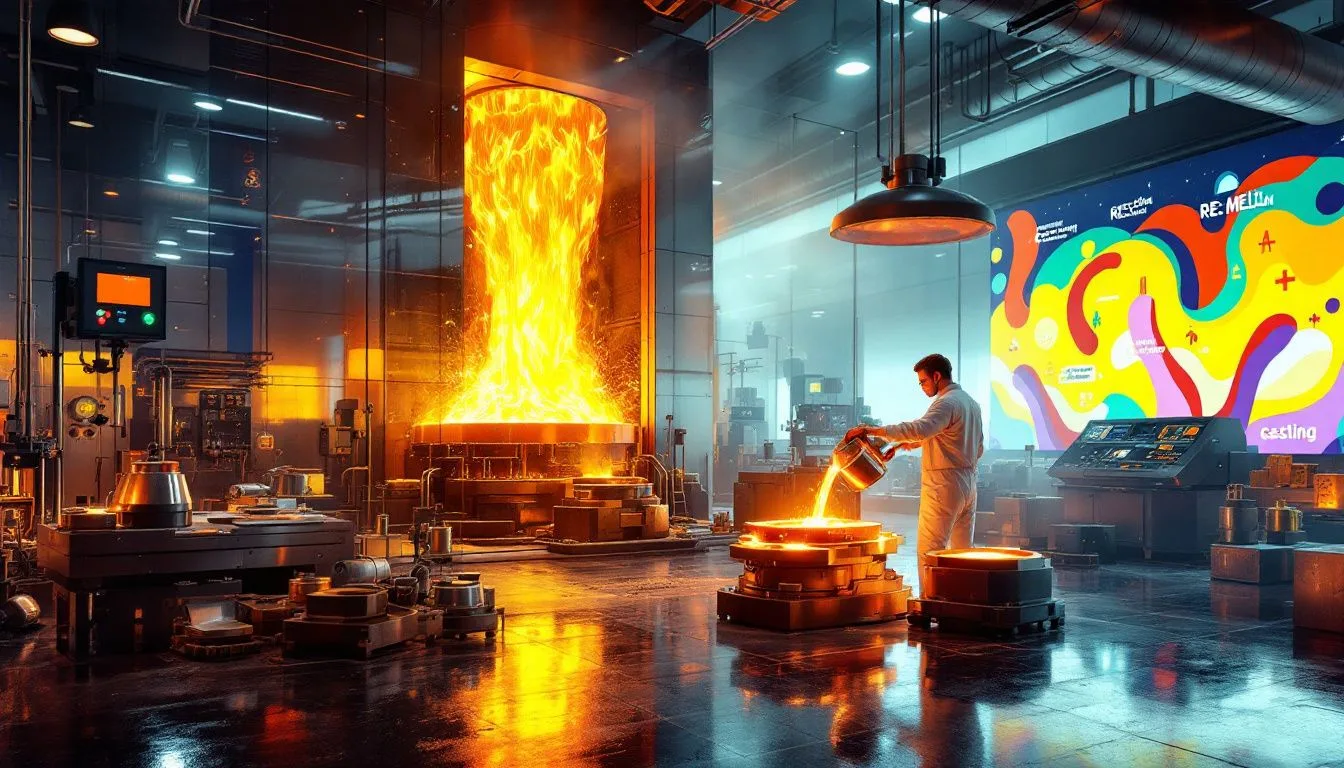
In an effort to shrink its ecological footprint and adhere to environmental regulations, the metal casting sector is intensifying its commitment to sustainable practices and diminishing its detrimental environmental effects.
Recycling in metal casting
In the metal casting industry, repurposing scrap metal plays a vital role in reducing waste and preserving natural resources. Foundries that recycle scrap are able to cut down on their use of new, or virgin, metal, which leads to decreased manufacturing expenses and lessens the ecological footprint of production.
Energy-efficient practices
In the realm of metal casting, introducing energy-efficient strategies such as improved furnace efficiency and better insulation can minimize thermal dissipation. The incorporation of sophisticated systems for monitoring energy usage is instrumental in pinpointing areas where the casting process may be falling short on efficiency.
The integration of these eco-friendly methods not only leads to a reduction in expenses, but also bolsters initiatives aimed at sustainability within the industry dedicated to metal casting.
Summary
Grasping the complexities of metal casting requires an in-depth knowledge that extends from making the initial pattern to applying sophisticated finishing techniques to refine the end product. The widespread utilization of cast metal parts throughout various sectors, including automotive, aerospace, and medical technology, illustrates their critical role within contemporary production methods. To fabricate high-quality components with precision that adhere to exacting requirements, manufacturers must select appropriate metals and implement cutting-edge technological processes.
As progress marches on within this field, it becomes increasingly important for industry practices to pivot towards sustainability while embracing advanced technologies aimed at heightening productivity and minimizing ecological footprints. Whether you’re a well-versed expert or simply keenly interested in the subject matter, acquiring proficiency in metal casting unlocks vast opportunities for producing robust and complex metallic elements which are fundamental catalysts for innovation and advancement.
Frequently Asked Questions
What are the key benefits of metal casting compared to other manufacturing methods?
The process of metal casting offers notable benefits like being economical, allowing for a flexible design approach, and making efficient use of materials. This enables the creation of intricate shapes which are frequently impossible to achieve through other manufacturing techniques.
Such attributes render metal casting exceptionally apt for producing components that are both robust and light in weight, catering to a wide range of uses.
What are the common metals used in casting and their applications?
Common metals used in casting include aluminum, zinc, magnesium, and stainless steel, each serving specific applications. Aluminum is ideal for automotive and aerospace due to its strength-to-weight ratio. Zinc is utilized in automotive components, magnesium is chosen for lightweight, detailed castings, and stainless steel is favored in medical applications for its corrosion resistance.
How does 3D printing enhance the metal casting process?
The metal casting process is substantially improved by 3D printing, which not only cuts down the time required from several weeks to mere hours and reduces material wastage, but also elevates the quality and precision of the final castings while simultaneously decreasing expenses.
What are the environmental benefits of recycling in metal casting?
Recycling in metal casting significantly minimizes waste and conserves natural resources by reducing the need for virgin metal. This not only lowers production costs, but also supports sustainability and compliance with environmental regulations.
What inspection methods are used to ensure the quality of cast metal parts?
Comprehensive inspection techniques are employed to maintain the quality of metal parts made by casting. These methods include mechanical testing, analysis of chemical composition, as well as nondestructive evaluations like ultrasonic and radiographic tests.
By leveraging these strategies, it’s possible to detect any imperfections on the surface and confirm that essential criteria are met, thereby guaranteeing both the durability and functionality of the cast metal components.