Machining Kovar involves dealing with its unique properties, such as low thermal expansion and high toughness. This guide covers the challenges and techniques needed for effective Kovar machining, including tool selection, heat management, and optimal CNC settings.
Key Takeaways
Kovar alloy features a low coefficient of thermal expansion, making it suitable for high-performance applications in electronics, aerospace, and medical devices.
Machining Kovar presents challenges due to its toughness and low thermal conductivity, necessitating specific techniques and specialized cutting tools to ensure precision.
Design considerations and post-machining treatments, such as pre-annealing and passivation, are critical for enhancing the machinability and performance of Kovar components.
Understanding Kovar Alloy
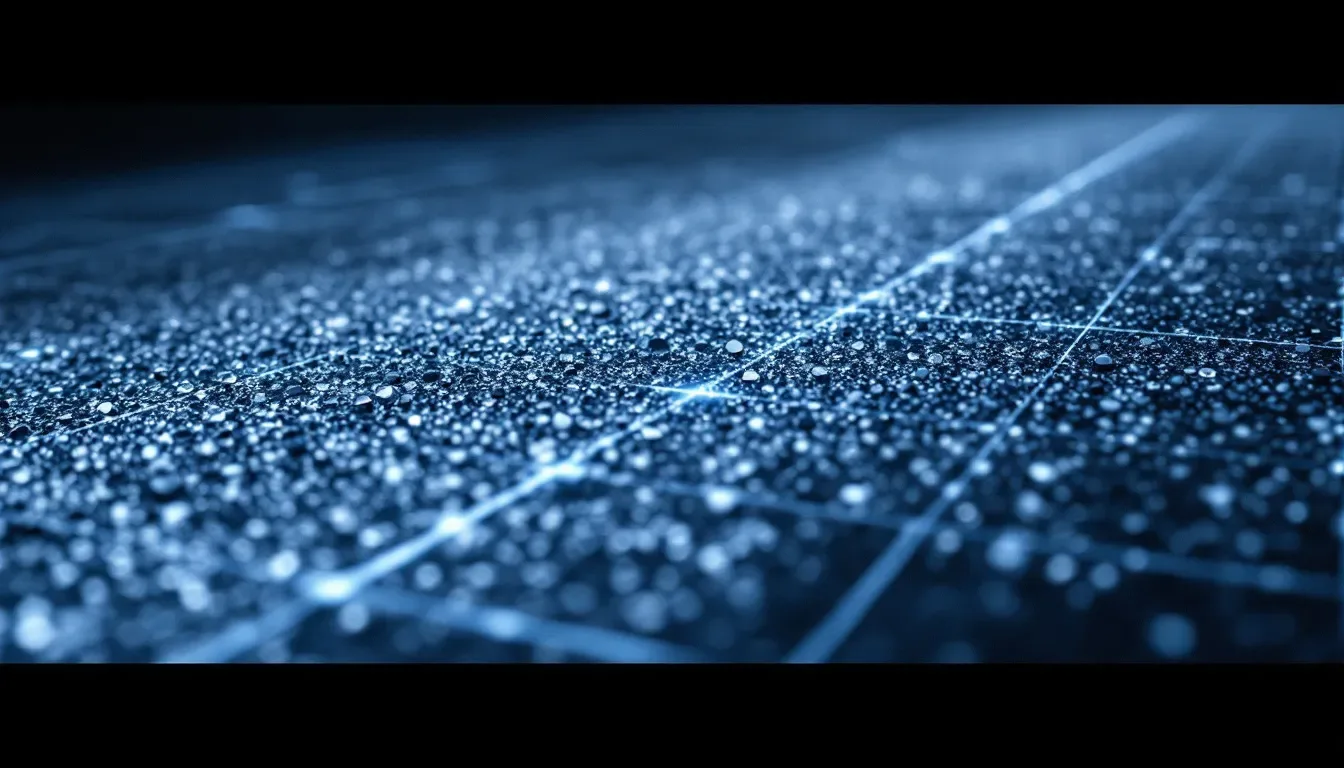
This distinct quality sets it apart from other nickel alloys by allowing Kovar to retain its shape and size even when subjected to varying temperatures, which makes it indispensable in contexts where precision tolerances are mandatory.
With its minimal thermal expansion coefficient mirroring that of borosilicate glass or ceramics, Kovar becomes the material of choice for sealing electronic packages as well as applications within aerospace and medical technology industries. The significance lies in ensuring materials expand or contract at uniform rates during temperature changes thus preventing stress and potential breakdowns—attributes heightening Kovar’s profile compared with various other nickel-based alloys.
Vacuum melting purifies the kovar alloy enhancing strength while offering versatility - key aspects necessary for crafting reliable connections within electronic gadgets, assuring robustness in aerospace parts, and verifying biocompatibility for medical implants. Understanding these core characteristics holds substantial value for those engaged in manufacturing kovar alloy or precisely machining components made from this unique substance.
Machining Challenges with Kovar Alloy
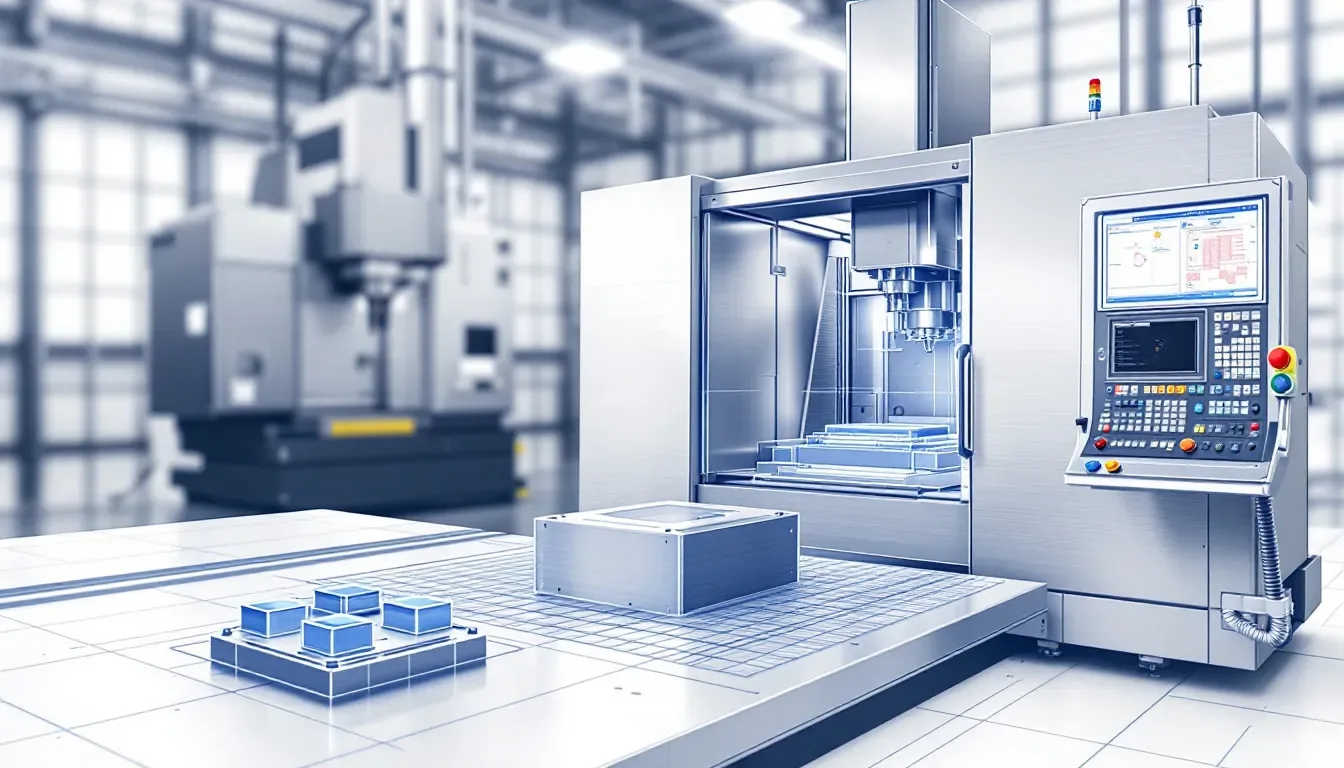
Working with Kovar alloy during the machining process can be particularly challenging due to its high toughness, tendency to work harden, and limited thermal conductivity. These characteristics make it difficult not only to shape with precision for demanding applications, but also contribute substantially to the wear of cutting tools.
Dealing with heat accumulation is a crucial aspect while machining Kovar since its inadequate thermal conductivity prevents efficient dispersion of heat created throughout the process. Strategies like designing effective fixtures or pre-annealing parts made from Kovar before commencing the actual machine work may enhance dimensional stability as well as dampen vibrations encountered during operations.
To meet precise standards necessary for components made from kovar alloy, machinists need to modify their methods leveraging sophisticated CNC technology tailored specifically for such materials. Adjustments encompassing optimized feed rates, adjustments in speed when cutting, along with improved cooling techniques help regulate excess temperature buildup and counteract the effects of work hardening on both material properties and tool integrity – ensuring that outcomes from kovar machining processes stand up as reliable and superior quality products.
Essential Cutting Tools for Kovar
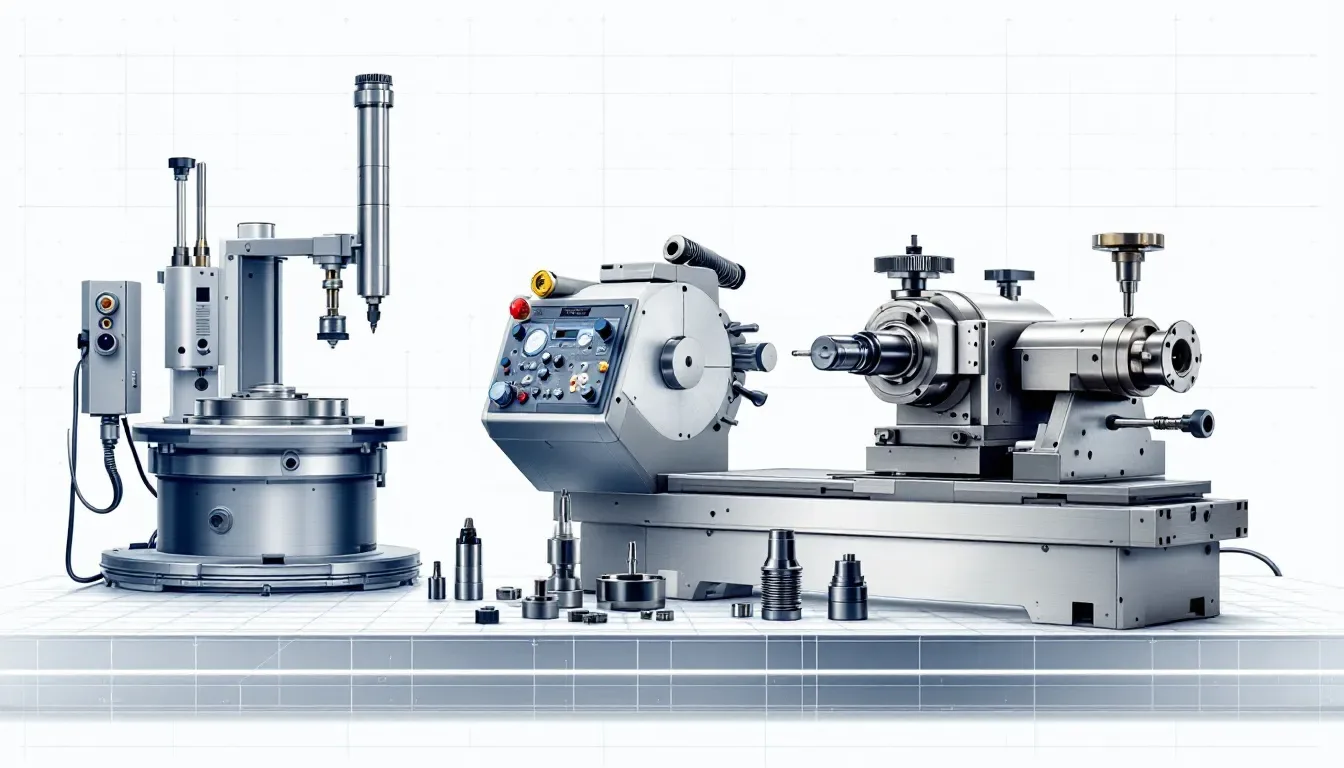
Ensuring the use of appropriate cutting tools is critical when machining Kovar alloy. . Such properties facilitate a more efficient machining process by prolonging tool life and ensuring consistent performance. High-speed steel tools play an important role in the precise execution of various operations like cutting, drilling, reaming and tapping on Kovar material.
Incorporating diamond-coated options with standard carbide or high-speed steel instruments can also markedly improve the effectiveness of working with Kovar alloys. These advanced cutting materials provide exceptional resistance against wear which assists in keeping precision intact during production runs and contributes positively towards extending longevity for all utilized tools.
The utilization of acutely sharpened implements coupled with adequate edge preparations is crucial to optimizing cut quality — this meets the demanding specifications associated with manufacturing components from kovar alloy successfully.
Optimizing CNC Machining for Kovar
CNC machining stands as a potent technique for fabricating high-precision, consistent Kovar components with outstanding surface quality. In CNC turning, the process revolves around spinning the Kovar workpiece while a non-moving tool carves away material to form cylindrical parts. This method achieves exacting specifications required in Kovar pieces, ensuring each component adheres to strict quality criteria via CNC machining.
Successfully milling of Kovar through CNC is pivotal when crafting complex geometries, involving subtractive techniques that are especially vital for detailed constructs. Through refined methods, machinists can realize precise tolerances and superior finishes critical for high performance nickel alloys.
Leveraging sophisticated CNC technology alongside bespoke tooling markedly improves CNC practices when working with Kovar. Strategies include modulating cut rates and feed ratios, employing appropriate cooling agents, maintaining sharpness and proper condition of tools are among these tactics that enable precision craftsmanship in creating highly accurate components which meet peak standards of precision and excellence.
Managing Heat Generation and Tool Wear
Managing heat generation and tool wear is critical when machining Kovar. Heat buildup can cause warpage and affect the dimensional stability of the machined component, necessitating careful heat control. Slower speeds and higher feed rates can help alleviate work hardening and reduce heat generation, ensuring a more stable machining environment. Proper use of coolants is also essential for managing Kovar’s thermal properties, reducing friction, and preventing chip-related issues.
High-quality tool coatings, such as TiAlN, can significantly reduce wear rates, extending the life of cutting tools. Selecting sharp tools and utilizing proper edge treatments further enhances the machining process, ensuring that tools remain effective and efficient.
Controlling heat buildup and managing tool wear ensures the precision required for high-performance Kovar components.
Specific Machining Processes for Kovar
Handling Kovar’s challenging material properties necessitates dedicated machining processes. The main techniques employed for machining Kovar include CNC turning, milling, drilling, and grinding. Each process employs distinct methods and factors to consider ensuring efficiency. Laser cutting is a viable option that yields precise edges while minimizing heat-affected zones – this approach serves to decrease both tool wear and the amount of material wasted.
This process alleviates internal stresses and contributes to better dimensional stability throughout subsequent operations.
Drilling Techniques
This treatment enhances the tool’s stability and aids in preventing breakage. The optimal angle for the drill point when working with Kovar lies within 118° to 120° for superior cutting efficacy. It is advisable for cutting tools designed to cut through Kovar’s distinctive properties to possess a minimum tip angle of 25°.
To ensure successful drilling operations on Kovar materials, choosing appropriate drill types along with precise angles is essential. These guidelines are key to maintaining stable and efficient drilling procedures which result in accurately drilled holes while also minimizing wear on the tools used. Adhering to these practices allows those machining kovar components to expect ideal outcomes from their work efforts.
Tapping Methods
When working with Kovar, employing a fluted tapping tool is essential to maintain the integrity of the threads and avoid any binding. For operations involving automatic machines, using two or three fluted tools for tapping can enhance both stability and productivity. Tapping at an approximate speed of 20 feet per minute (FPM) is recommended in order to produce precise and reliable threading.
To ensure thread quality while tapping Kovar, it’s beneficial to use a tap drill that’s slightly larger than standard size. Should binding be encountered during this process, reducing the heel width by grinding may offer a solution. Following these techniques enables machinists to craft high-caliber threads inkovar components which are crucial for their reliability and functionality.
Reaming Guidelines
Before reaming Kovar, adjust the speeds to half that of drilling speeds. Set the feed rate at a value triple that of the drill speed for an efficient and accurate process while minimizing tool wear and safeguarding dimensional stability. Reaming tools specific to Kovar should be as compact in length as possible with a slight face rake angle between 5° and 8°.
After:
Reduce reaming speeds to one-half those used during drilling.
Set up feed rates at three times higher than your drill speed for seamless precision in the reaming operation.
Utilize short-length reaming tools tailored for Kovar workpieces.
Incorporate a modest face rake within roughly 5° to 8° range. This is crucial for attaining reduced drill-speed effectiveness.
It’s advisable to have about a ten-foot margin on land when you’re tasked with reaming Kovar if you want optimal performance from your efforts. By following these instructions meticulously, one can guarantee successful execution of the ream process along with meeting stringent hole specifications required by various applications or designs.
Key Applications of Machined Kovar Components
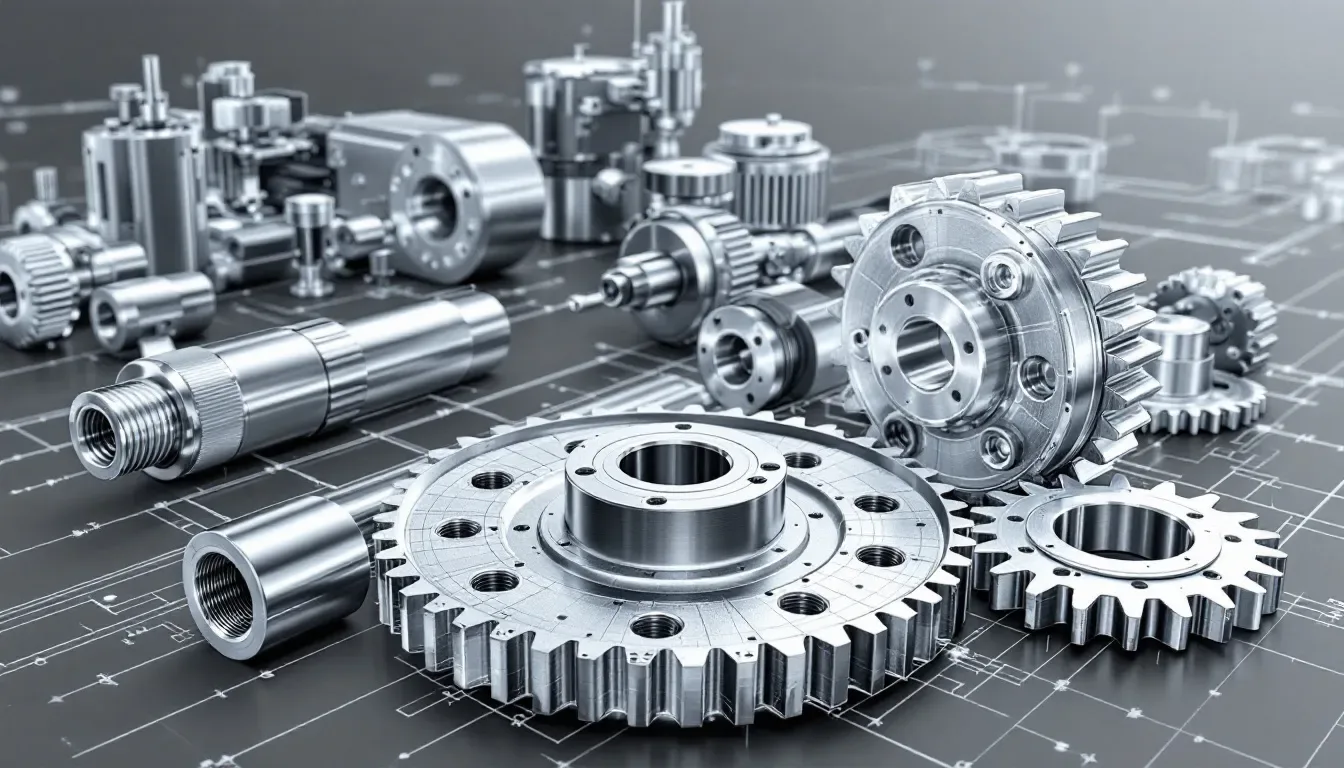
The distinctive qualities of Kovar are invaluable in industries that demand precision. In the electronics sector, it is utilized for components such as diodes and transistors due to its ability to form dependable connections between dissimilar materials. Kovar’s minimal thermal expansion coefficient aligns well with aerospace applications where exposure to fluctuating temperatures is a norm, ensuring component integrity despite changing environments.
In medical technology, Kovar stands out for being biocompatible and offering precise temperature regulation—attributes crucial for instruments adhering to exacting performance criteria. The telecommunications realm similarly depends on the stability and accuracy that Kovar offers within high-performance settings. These uses underscore the critical nature of machining kovar parts meticulously.
Kovars’ thermal expansion characteristics render it integral in crafting glass-to-metal seals within vacuum systems—a testament to its reliability across varying conditions—which solidifies its position as a pivotal resource in sophisticated technological implementations. Acknowledging these primary roles highlights the necessity of expertise in kovar machining practices.
Design Considerations for Kovar Machining
When working with Kovar machining, it’s essential to account for the alloy’s specific coefficient of thermal expansion. This consideration is key in preventing thermal and mechanical stress by ensuring that Kovar expands compatibly with the materials next to it. Such compatibility minimizes stress resulting from temperature changes and maintains both the stability and integrity of kovar components. Pre-machining annealing can also help reduce internal stresses, promoting better dimensional stability.
Improvements can be achieved through post-machining treatments like passivation, which mitigate oxidation issues while improving surface characteristics. These processes are important in making sure kovar parts adhere to precise specifications and function dependably for their intended uses. Attention to these elements during design contributes significantly toward attaining high levels of precision and quality necessary for optimal performance of kovar components.
Advanced Techniques for Complex Geometries
Sophisticated CNC methodologies are imperative for fabricating intricate shapes within Kovar materials. By spinning the workpiece or employing revolving cutting tools, CNC turning and milling facilitate the creation of detailed forms. Such procedures play a pivotal role in attaining the exactness and dimensional consistency that Kovar components demand.
The deployment of specialized tooling, notably carbide-based instruments, is instrumental in extending their operational life and enhancing performance during Kovar machining processes. It’s also recommended to apply post-machining surface treatments such as passivation to stave off oxidation and boost the durability of these components.
By harnessing these state-of-the-art techniques, operators can manufacture high-caliber complex geometries out of Kovar with unparalleled precision.
Summary
In this comprehensive guide, we’ve delved into the complexities and specialized techniques essential for achieving excellence in Kovar machining. Delving into the material’s makeup and characteristics as well as perfecting distinct machining processes while controlling heat production is fundamental to fabricate components with utmost precision and quality. Utilizing these detailed insights enables machinists to conquer the intricacies associated with kovar alloy and deliver parts that adhere to stringent standards.
It is crucial to recognize that effective Kovar machining hinges on a thorough understanding of its properties, choosing appropriate cutting tools, and implementing sophisticated CNC methods. With these tactics at your disposal, you can attain remarkable outcomes suitable for demanding applications. Continue striving for unsurpassed accuracy in your work involving Kovar. Let it stand out as a testament to high-precision craftsmanship.
Frequently Asked Questions
What makes Kovar alloy unique for machining?
Kovar alloy is unique for machining due to its low thermal expansion and high mechanical stability, making it especially suitable for precision applications in electronics, aerospace, and medical devices.
Why is heat generation a problem when machining Kovar?
Heat generation during machining Kovar is problematic due to its low thermal conductivity, which inhibits effective heat dissipation and can result in thermal expansion issues and increased tool wear.
What cutting tools are recommended for machining Kovar?
Carbide tools and high-speed steel tools are highly recommended for machining Kovar, as they provide the necessary durability to manage its abrasive characteristics.
How can CNC machining be optimized for Kovar?
Optimizing Kovar CNC machining can be achieved by leveraging advanced CNC technology, fine-tuning the cutting speeds and feeds, as well as using suitable coolants alongside sharp tools to improve both efficiency and accuracy.
What are the key applications of machined Kovar components?
The key applications of machined Kovar components are in electronic packaging, aerospace, medical devices, and telecommunications, due to Kovar’s stability and precision.
Start Your Next Project with LKprototype
LKprototype simplifies procurement for custom manufacturing, from 3D Printing to CNC Machined Parts and Vacuum Casting to prototype your product or parts, with a focus on speed and efficiency. Our platform provides instant quotes. With LKprototype, You can connect with the team to communicate your project to ensure quality and on-time delivery.
Start with an instant quote and experience how our technology and expertise can make custom part procurement faster and easier.