Are you trying to decide between using a lathe and a mill for your machining project? Understanding the key differences between these tools, including the lathe and mill, can help you choose the right one. This article will explain how lathes and mills operate, their unique features, and when to use each tool to achieve the best results.
Key Takeaways
Lathes are best suited for creating cylindrical shapes, while milling machines excel at producing complex geometries and intricate designs.
Understanding the power requirements and efficiency of lathes and mills is crucial for optimal performance and safety in machining tasks.
Selecting the appropriate machine involves evaluating project needs, including material type, workpiece complexity, and desired outcomes to achieve efficient and accurate machining results.
Understanding Lathes
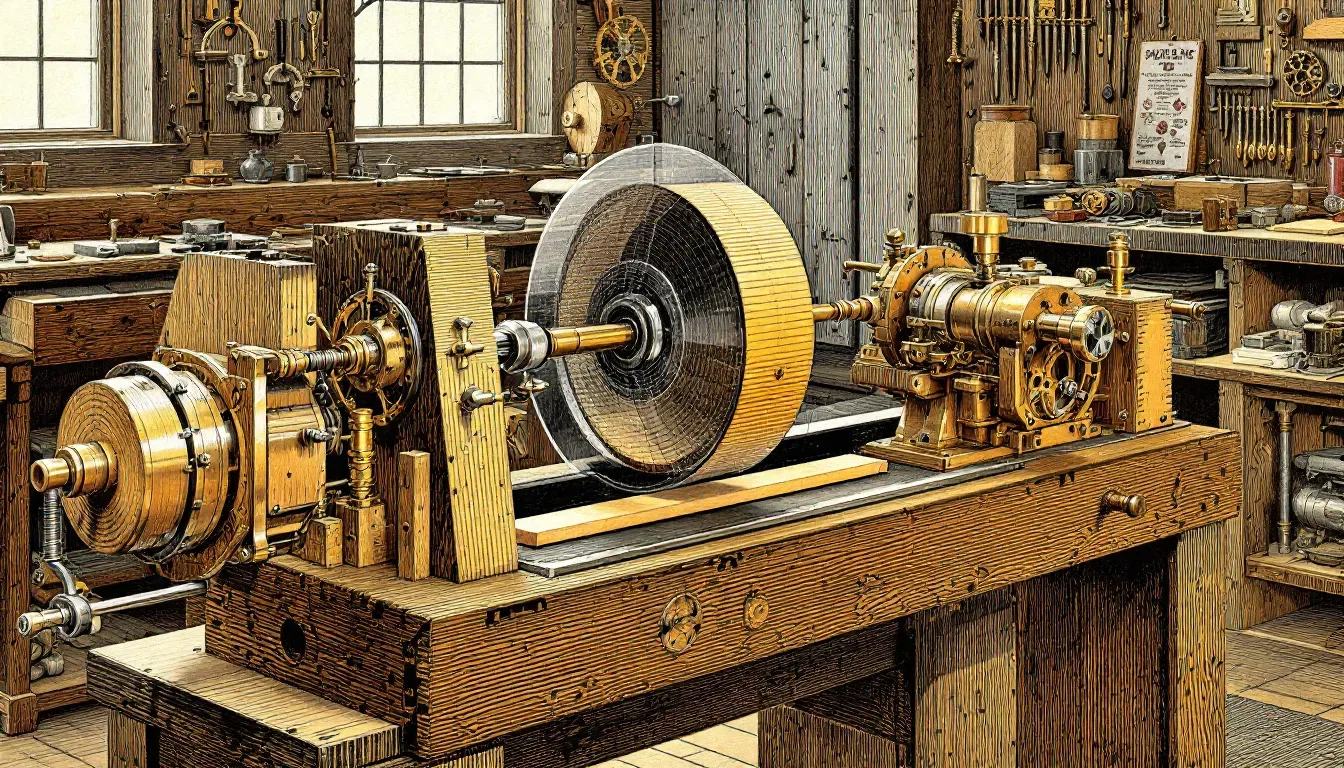
Lathes hold a pivotal role in the machining realm, celebrated for their proficiency in molding materials by spinning the workpiece while a fixed cutting tool trims it. This process provides meticulous removal of material, fostering the production of cylindrical shapes with outstanding precision. The attachment of the workpiece to a spindle is crucial as it guarantees stable and regulated rotations that are vital for meeting specific sizes and surface qualities.
These machines showcase an impressive range not limited to shaping metals. They’re equally adept at working with substances like acrylics and composite materials. Such adaptability renders lathes invaluable across different sectors, encompassing everything from automotive fabrication to fine arts creation. Understanding how lathes function is essential to fully recognize their significance and expansive capabilities within various manufacturing endeavors.
Key Features of Lathes
Lathes consist of several essential elements that synchronize to achieve accurate machining outcomes. The primary components include:
The bed, serving as the stable base and ensuring proper alignment.
The carriage, responsible for moving the cutting tool across the workpiece.
The headstock, which contains the spindle that secures and spins the workpiece.
The tailstock, providing extra support to elongated pieces.
And lastly, the faceplate is used to clamp down on a piece for it to be machined.
Each part contributes significantly to how well a lathe performs its duties.
Contemporary late models such as MLD - 1022 are outfitted with both types of chucks: three-jaw and four-jaw chucks. These accommodate an array of shapes sizes of different parts or material being worked upon Extending capabilities by allowing users adjust speeds from low at 50 rpm up to high end speed maxing out around 2250 RPM thus enabling tailor made settings suit every particular task needing carried through either simple turning projects intricate cuttings various sorts of intricate procedures.
When to Use a Lathe
Lathes are particularly adept at crafting accurately cylindrical items, positioning them as the preferred tool for fashioning objects such as shafts and axles that exhibit symmetrical characteristics. The rotation of the workpiece during operation facilitates even removal of material, crucial for manufacturing threads and detailed patterns. This rotating action is key to lathes’ ability to generate decorative details and mechanical connections with a high degree of precision.
The utility of lathes extends to shaping a variety of materials including acrylics and selected composite types, which broadens their application scope well beyond just metalworking tasks. For individuals engaged in either mechanical endeavors or the creation of art pieces, recognizing when employing a lathe could markedly enhance both the caliber and productivity levels associated with your projects.
Exploring Milling Machines
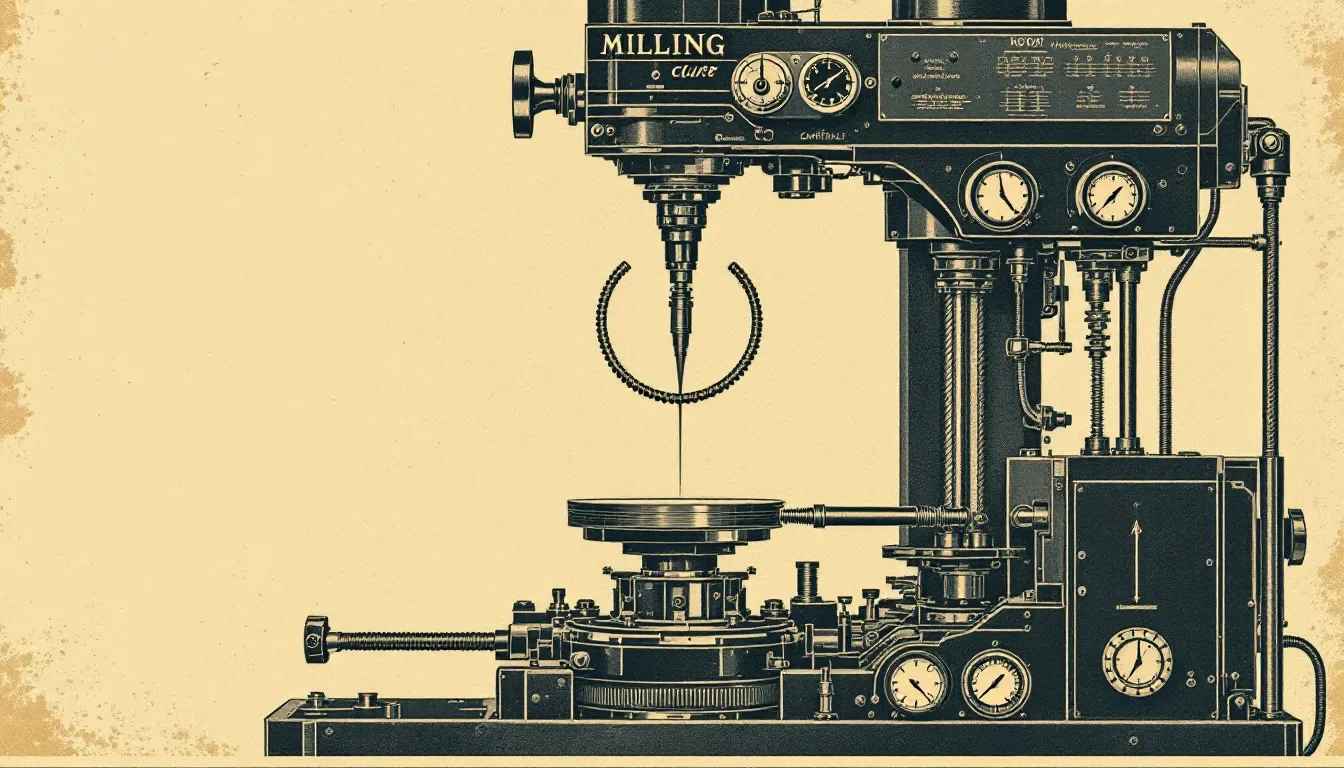
Milling machines stand as a fundamental element in the realm of machining, renowned for their proficiency in crafting intricate shapes and complex geometries. In contrast to lathes that rotate the workpiece against a stationary tool, milling machines secure the material being worked upon while a rotating cutting tool with multiple blades carves away at its surface. This method is conducive to shaping both flat and curved surfaces, rendering milling machines exceptionally adept at producing parts with elaborate geometries.
The adaptability of these machine tools is considerably expanded by their assortment — encompassing vertical mills, horizontal mills, and computer numerically controlled (CNC) mills — each meticulously crafted to fulfill distinct roles and specific uses within various applications. Such diversity guarantees that for nearly every conceivable machining task, from straightforward drilling operations to advanced manufacturing techniques, there exists an ideally suited milling machine designed to meet those precise needs.
Types of Milling Machines
Milling machines are designed in a variety of forms, each specialized for certain functions and uses. Vertical mills possess a spindle that is aligned vertically, securing the cutting tool in place, which makes them especially suitable for jobs needing high precision and straightforward access to the workpiece. In contrast, horizontal mills come with a spindle positioned horizontally and excel at more intense cutting operations on bulky items.
CNC mills stand at the forefront of milling advancements by delivering automated accuracy and adaptability. These machines incorporate computer numerical control (CNC) systems, making it possible to carry out intricate and consistent tasks without significant manual input.
No matter what type of mill is used, its core component—the spindle—is essential as it holds onto and spins the cutting tool effectively allowing for efficient removal of material from the workpiece.
Key Features of Milling Machines
Milling machines possess several integral features, which include:
A spindle that serves the crucial purpose of holding and rotating the cutting tool necessary for removing material.
The worktable provides a firm grip on the workpiece while permitting longitudinal movement throughout milling procedures, ensuring precise machining results.
Multiple axes of motion significantly contribute to the precision and overall capabilities of these machines.
Every one of these components is essential in facilitating an efficient milling process.
These machines are furnished with modifiable tables that allow for meticulous fine-tuning during operations. Together, this array of attributes equips milling machines with versatile functionality capable not only of straightforward cuts but also elaborate shape formation and detailed designs.
When to Use a Milling Machine
Milling machines excel in transforming materials into flat or curved surfaces, rendering them exceptionally suited for the fabrication of complex geometries and intricate designs. These machines are particularly adept at tasks that require elevated precision, such as the production of gears and various detailed parts. Numerous milling machines are outfitted with capabilities similar to a drill press, enabling them to carry out drilling operations as well.
In contrast to lathes—which specialize in generating cylindrical shapes—milling machines stand unmatched when it comes to crafting an assortment of forms and sophisticated features. Their adaptability is indispensable within sectors necessitating meticulous and exact machining processes. This includes fields like automotive manufacturing all the way through aerospace engineering.
Comparing Lathes and Mills

Grasping the distinctions between lathes and milling machines is essential in the field of machining. Lathes function by spinning the workpiece while a fixed cutting tool shapes it, which makes them perfect for crafting cylindrical forms. On the flip side, milling machines maintain a stationary position for the workpiece as they employ a revolving cutting tool to chip away material, enabling them to produce complex structures and detailed patterns.
Selecting either a lathe or milling machine typically hinges on what specific demands are posed by any given task. Projects involving cylindrical pieces often favor lathes due to their suitability for such shapes. Conversely, when one needs to generate flat surfaces with elaborate detailing, milling machines prove superior. Recognizing these distinct capabilities assists in choosing the appropriate equipment that will deliver both accuracy and effectiveness within your machining operations.
Material Removal Techniques
Eliminating excess material from a workpiece is an essential step in the machining process, aiming to sculpt it into the required shape and texture. Utilizing lathes for this purpose involves spinning the workpiece against a fixed cutting tool, which excels in producing round profiles. This approach facilitates uniform and precise material removal, rendering lathes perfect for assignments demanding tight precision.
Conversely, milling machines immobilize the workpiece while bringing a rotating multi-edge cutting tool into play to pare away its surface. This strategy shines when manufacturing flat planes or intricate shapes due to its broader range of achievable designs as the piece being worked on remains static.
Grasping these distinctive merits aids in determining which method best aligns with your particular project requirements.
Precision and Speed
The quality and efficiency of machined parts are greatly influenced by the precision and velocity at which machining occurs. Lathes have a tendency to work at elevated speeds. With milling machines, rendering them more suitable for mass production of uncomplicated cylindrical components. The swift operation associated with lathes can notably diminish the time needed for simpler manufacturing processes.
Nevertheless, how accurately both lathes and milling machines perform is heavily dependent on the proficiency of those operating them as well as their particular configuration. Although they may operate more slowly than lathes, milling machines can achieve remarkable precision when creating complex shapes and detailed designs. Their capacity for finely-detailed work makes them indispensable for assignments necessitating great precision.
In any machining endeavor, it’s imperative to strike an optimal balance between rapidity and accuracy in order to meet the anticipated outcomes successfully.
Cost and Efficiency
When determining whether to choose a lathe or a milling machine, it’s important to consider both cost and efficiency. Lathes are more affordable than milling machines, which makes them an attractive option for tasks involving cylindrical components. They have a simpler design that not only reduces maintenance complexity but also lowers the upfront costs associated with purchasing one. This affordability and ease of use make lathes well-suited for many machining projects where financial limitations must be taken into account.
Conversely, while milling machines may require a larger initial investment—particularly those designed for high precision—they can provide enhanced flexibility and facilitate the execution of numerous operations. This multifunctionality could lead to improved efficiency over time.
Milling machines justify their higher startup costs by offering greater versatility in performing complex and varied machining jobs. Recognizing these considerations regarding expenses and operational capabilities is crucial when making choices that best fit your project requirements within budgetary limits.
Power Requirements for Lathes and Mills
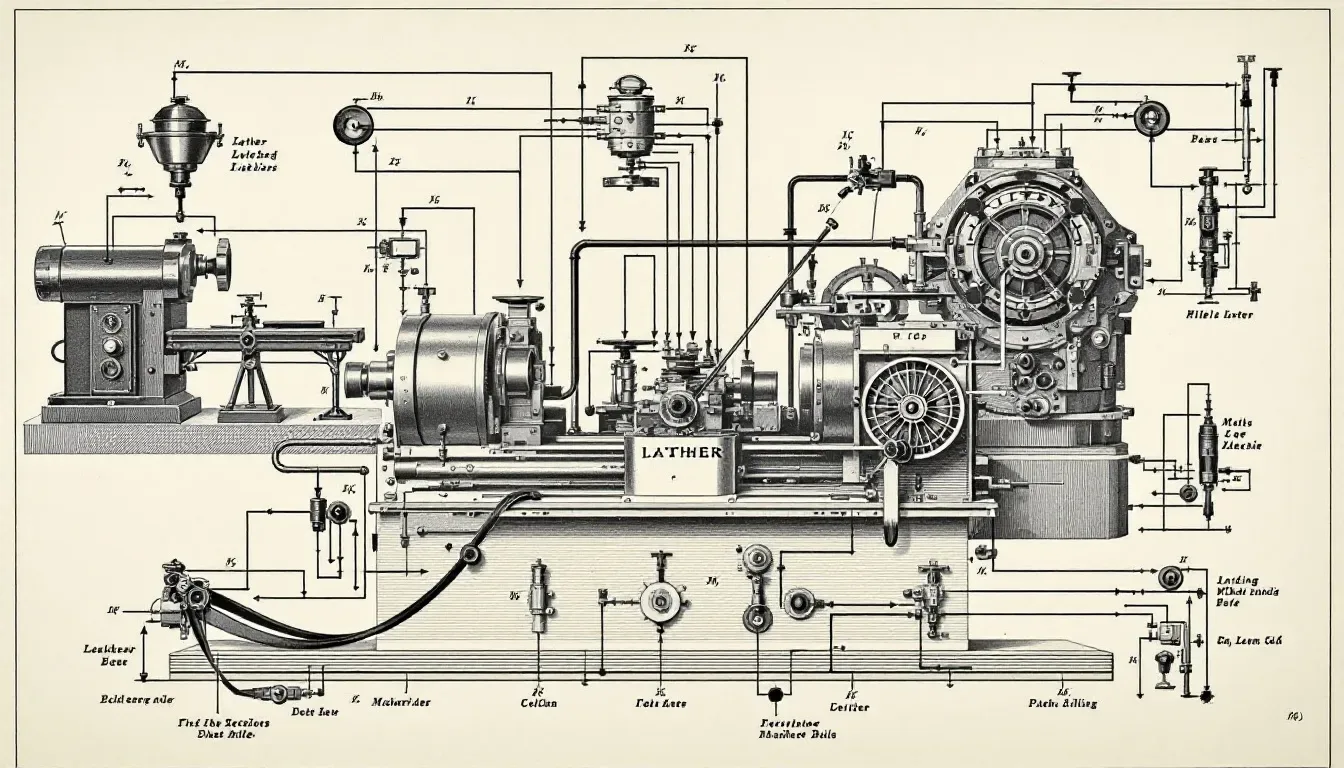
It’s crucial to consider the power needs for lathes and milling machines to guarantee their effective functioning. A reliable source of power is not only instrumental in enhancing performance, but also plays a key role in maintaining safety during machining processes. While single-phase power is typically employed for home use, three-phase electricity is often the choice for heavy-duty industrial equipment such as lathes and mills due to its superior efficiency and ability to handle larger loads. The assurance of a consistent and proper electrical supply can markedly improve these machines’ performance and durability.
A lack of adequate electricity can give rise to operational difficulties along with potential risks related to safety, highlighting the importance of utilizing suitable power converters while keeping voltage levels stable. By being aware of your machinery’s specific electric requirements, you contribute toward seamless operation that results in improved machining productivity as well as an extended life span for your equipment.
Single-Phase vs. Three-Phase Power
Industrial equipment such as lathes and milling machines often operate more effectively with three-phase power, which is recommended due to its capacity for managing higher loads efficiently. This type of power offers greater stability and efficiency compared to the single-phase supply commonly found in homes, thereby minimizing fluctuations in electricity that could negatively impact machine performance. The continuity of operations on a lathe or mill can be compromised by issues arising from utility power supplies. Hence, a consistent and reliable source of energy is essential.
By adopting three-phase power for industrial machining tools, machinists can achieve smoother and steadier functionality across their machinery. Such an investment guarantees that these high-performance machines are less likely to suffer from disruptions caused by electrical inconsistencies when undertaking rigorous tasks. As a result, this contributes significantly towards enhancing output rates as well as the accuracy within various machining endeavors.
Enhancing Performance with Proper Power Supply
Improving the function of milling machines and lathes necessitates a consistent and suitable power supply. Employing either digital or rotary phase converters can markedly boost the efficiency and accuracy of these pieces of equipment. These devices provide a steady flow of power to the machinery, diminishing variations that could affect both performance levels and operational safety.
Maintaining stable voltage is essential for ensuring both the safe operation and the durability of machining equipment. Three-phase electrical systems are especially beneficial as they help stabilize fluctuations in power, providing continuous torque which is critical for tasks that require heavy-duty machining.
By allocating resources towards reliable power supply solutions, you have the potential to significantly refine the precision and efficacy of your machining processes, yielding enhanced outcomes while extending the lifespan of your machinery.
Choosing the Right Machine for Your Project
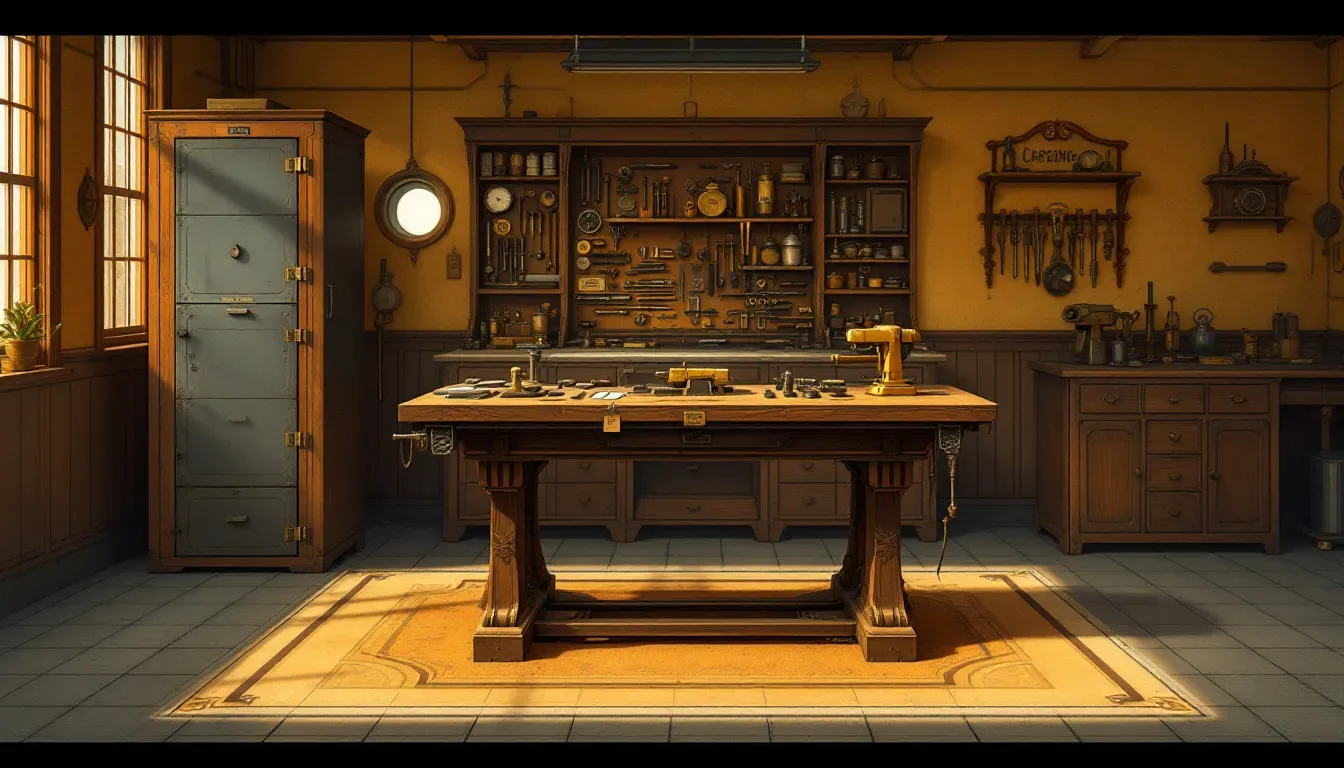
Choosing the appropriate equipment for your project requires a detailed analysis of your specific requirements alongside what the machinery can offer. It’s critical to take into account not only the nature of material, but also both dimensions and intricacy of the item being worked on, plus what you intend as an end result when working with either lathes or milling machines. Ensuring that these elements are in harmony with what a machine is capable of doing will guarantee precise and efficient outcomes from any machining processes.
It’s imperative to have reliable power sources when operating milling machines or lathes. A steady supply of power is key to avoiding disruptions that can affect both efficiency and accuracy during machining operations. By meticulously evaluating which machine fits your needs best and ensuring it aligns well with those capabilities, you’ll be able to secure superior performance for your projects.
Assessing Your Needs
When assessing your machining requirements, take into account the dimensions and intricacy of the workpiece, as well as the precision needed and the volume of production. By understanding these factors, you can make an informed decision about whether a lathe or milling machine is more appropriate for your specific application. For example, when high precision is required in crafting cylindrical components, opting for a lathe could be advantageous.
On the other hand, should your endeavor entail carving materials into elaborate shapes with detailed patterns, employing a milling machine would be preferable. Careful evaluation of your needs ensures that you choose equipment capable of achieving optimal outcomes for your particular machining operations.
Matching Machine Capabilities to Projects
It is essential to match the features of a machine with the requirements of your task for effective and precise results. Recognizing the unique capabilities of machines like lathes and milling mills, which include their ability to handle different materials and adopt various cutting methods, aids in selecting the appropriate machine for a project. Lathes are particularly adept at crafting parts with symmetrical designs, while milling machines specialize in creating flat surfaces as well as intricate shapes.
Ensuring that you choose machining equipment whose attributes correspond closely with your project’s needs not only yields high precision but also enhances efficiency critical for adhering to production schedules. This careful matching guarantees that machining processes proceed without a hitch and yield accurate results, contributing significantly to successful completion of projects.
Start Your Next Project with LKprototype
LKprototype simplifies procurement for custom manufacturing, Suitable for making your products or prototypes with a variety of materials, such as metal or plastic, silicone rubber, from 3D Printing to CNC Machined Parts and Vacuum Casting , with a focus on speed and efficiency. Our platform provides instant quotes. With LKprototype, You can connect with the team to communicate your project to ensure quality and on-time delivery.
Start with an instant quote and experience how our technology and expertise can make custom part procurement faster and easier.
Summary
It’s essential to comprehend the distinctions between lathes and milling machines when choosing the appropriate equipment for your machining tasks. Lathes are particularly suited for crafting parts with cylindrical shapes and symmetry, as they spin the material being worked on against a fixed tool used for cutting. In contrast, milling machines are adept at forming elaborate geometries and complex designs because they keep the material immobile while a rotating tool cuts away.
To attain effective and accurate outcomes, it is important to evaluate what you need specifically and find a match in these machine types’ capabilities. Making an informed decision about which power supply to invest in can greatly improve both efficiency and longevity of your machinery. Also considering cost-related aspects adds value to this process. Equipped with such insights, you have the assurance needed when selecting the ideal machine that will lead to successful results in your pursuits within machining.
Frequently Asked Questions
What are the primary differences between lathes and milling machines?
Lathes and milling machines are both used in manufacturing, but they differ fundamentally in their operation. Lathes spin the workpiece to sculpt cylindrical shapes, while milling machines hold the workpiece still and employ a rotating cutter to craft intricate geometries.
This core difference is what determines their respective uses within the manufacturing industry.
When should I use a lathe instead of a milling machine?
You should use a lathe instead of a milling machine when your project involves creating precise cylindrical shapes, such as shafts or threaded components, as lathes excel in producing symmetrical parts.
What types of milling machines are available, and what are their applications?
There are several types of milling machines available, including vertical mills, horizontal mills, and CNC mills.
Vertical mills excel in precision tasks, horizontal mills are suited for heavier cutting operations, and CNC mills are ideal for automated and complex machining needs.
How do power requirements impact the performance of lathes and milling machines?
Power requirements significantly affect the performance of lathes and milling machines, with three-phase power being the preferred choice for its efficiency and stability, leading to improved precision and minimized power fluctuations.
Thus, ensuring an adequate power source is essential for maximizing machine performance.
What factors should I consider when choosing between a lathe and a milling machine?
When deciding whether to use a lathe or a milling machine, take into account the material type, the dimensions and intricacy of the workpiece, required precision levels, and the volume of production needed.
Match these considerations with what each machine can perform in order to achieve maximum machining effectiveness and precision.