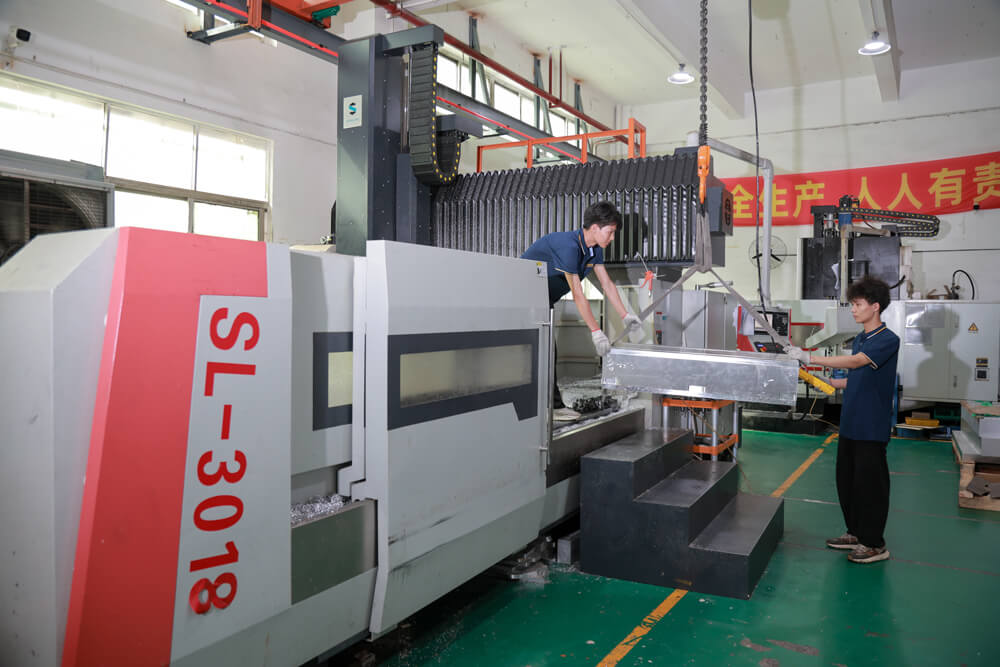
1. Introduction to CNC Machining Services
What are CNC machining services?
Precision engineering in CNC machining services, also known as precision machining, involves the use of computer-controlled machines to manufacture parts with high precision and accuracy. CNC machining processes are crucial in achieving precise manufacturing standards and certifications, highlighting operational advantages such as high accuracy and the ability to efficiently produce custom parts. These services are widely used across various industries due to their ability to produce complex and intricate designs. The cnc machining advantages include high accuracy, repeatability, and capability for continuous operation, making it ideal for on-demand production of both one-off and high-volume parts.Applications across industries: automotive, aerospace, electronics, and medical.
2. What is CNC Machining?
CNC machining is a subtractive manufacturing process that uses computer numerical control (CNC) machines to remove material from a workpiece. CNC machining often takes place in specialized machining centers equipped with advanced tools and technology. This process involves the use of a computer-controlled machine to execute a set of programmed commands, enabling the creation of complex designs and precise CNC machined parts. CNC machining is widely used in various industries, including aerospace, automotive, and medical devices, due to its high precision, accuracy, and speed. By leveraging advanced CNC machines, manufacturers can produce intricate components with tight tolerances, ensuring consistent quality and performance.
3. Types of CNC Machining Services
Common types of CNC machining services, each with unique machining capabilities, include turning, milling, and drilling. CNC milling is known for its precision in producing both simple and complex geometries, making it efficient for manufacturing custom prototypes and production parts quickly.
Technical characteristics and use cases of 3-axis, 4-axis, and 5-axis CNC machining. CNC turning specializes in machining cylindrical parts like pins, shafts, and spacers, offering high precision and quick delivery for prototypes and production parts across various industries.
4. CNC Machining Capabilities
Our CNC machining capabilities extend beyond standard CNC machines, incorporating advanced equipment such as grinders for smooth finishes, wire cutters for precision cuts, and EDM machines for intricate shapes. Our expert machinists achieve ultra-precise tolerances as tight as 0.01mm, ensuring the highest level of accuracy for your CNC machined parts. Additionally, our automated production lines deliver high-volume production efficiently, minimizing errors and keeping projects on track. We offer custom CNC machining services for both small batches and high-volume production, catering to a wide range of industries and applications.
5. CNC Machining Materials
We offer a wide range of CNC machining materials, each with unique material properties, including both metals and plastics, to meet diverse project requirements. Our metal options include aluminum, stainless steel, copper, and titanium, each offering unique properties such as strength, corrosion resistance, and lightweight characteristics. For plastic materials, we provide options like ABS, acrylic, polycarbonate, and PEEK, known for their durability, chemical resistance, and versatility. To further enhance the appearance and durability of our CNC machined parts, we offer various surface finishes, including anodizing, plating, and powder coating.
6. CNC Machining Surface Finishes
We offer a variety of surface treatments and finishes to enhance the appearance and durability of our CNC machined parts. Our surface finishes include anodizing, plating, powder coating, and media blasting, among others. Anodizing provides a corrosion-resistant coating, ideal for aluminum parts, while plating offers a decorative and protective layer for metals. Powder coating is a durable and chip-resistant finish, suitable for both metals and plastics. Media blasting provides a smooth and textured surface, enhancing the aesthetic appeal of the parts. We also offer custom surface finishes to meet specific requirements, ensuring your CNC machined parts meet your exact specifications.
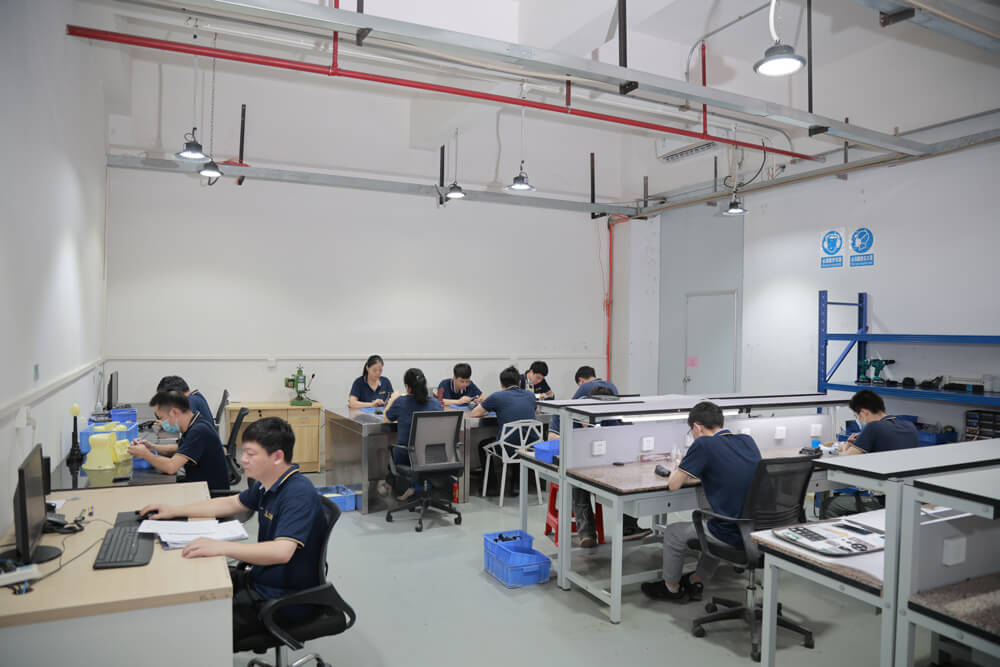
7. Design and Manufacturing Considerations
When designing parts for CNC machining, it’s essential to consider several factors to ensure efficient production and minimize costs. Here are some key design and manufacturing considerations:
Material Selection: Choosing the right material is crucial for the success of your CNC machining project. Metals like stainless steel and aluminum offer excellent strength and corrosion resistance, while plastics such as ABS and polycarbonate provide durability and chemical resistance. Selecting materials that are suitable for CNC machining can significantly impact the performance and longevity of your parts.
Tolerances: Specifying achievable tolerances is vital for ensuring the precision of CNC machined parts. Typically, CNC machining can achieve tolerances of +/- 0.005” or tighter. However, tighter tolerances may require additional machining processes or specialized equipment, which can increase CNC machining costs.
Complexity: Simplifying your design can help reduce machining time and costs. Avoid complex geometries that may require specialized machining processes or multiple setups. By streamlining your design, you can achieve efficient production without compromising on quality. Simplifying your design can help improve machining efficiency and reduce costs.
Wall Thickness: Ensuring adequate wall thickness is essential to maintain the structural integrity of your parts. Thin walls can lead to warping or deformation during the machining process. Designing with sufficient wall thickness helps prevent these issues and ensures robust CNC machined parts.
Corners and Edges: Designing corners and edges with a radius or chamfer can facilitate machining and prevent sharp edges. Rounded corners are easier to machine and reduce the risk of stress concentrations, enhancing the durability of your parts.
Holes and Pockets: When specifying hole sizes and pocket depths, consider the capabilities of CNC machines. Avoid small holes or deep pockets that may require specialized equipment. Designing with standard sizes can streamline the machining process and reduce costs.
Surface Finish: Specify surface finishes that are achievable with CNC machining, such as as-machined, media blasted, or anodized. The right surface finish can enhance the appearance and functionality of your parts, providing both aesthetic and practical benefits.
Production Volume: Consider the production volume when designing your parts. High-volume production may require specialized equipment or processes to ensure efficiency and consistency. Adjusting your design and manufacturing processes accordingly can optimize production and reduce costs.
Cost Reduction: Implementing design for manufacturability (DFM) principles can help reduce CNC machining costs. Simplify your designs, reduce material usage, and minimize machining time to achieve cost-effective production without sacrificing quality.
Collaboration: Collaborate with CNC machine shops and manufacturers to ensure your designs are manufacturable and meet production requirements. Working closely with experts can help you identify potential issues early and make necessary adjustments to optimize your CNC machining project.
By considering these design and manufacturing considerations, you can optimize your CNC machining project for efficient production, reduce costs, and ensure high-quality parts.
8. Key Factors in Selecting a CNC Machining Service Provider
Technical Capabilities: Evaluating equipment and machining expertise.
Quality Control: Ensuring strict inspection processes are in place.
Delivery Capacity: Assessing machining speed and project timelines.
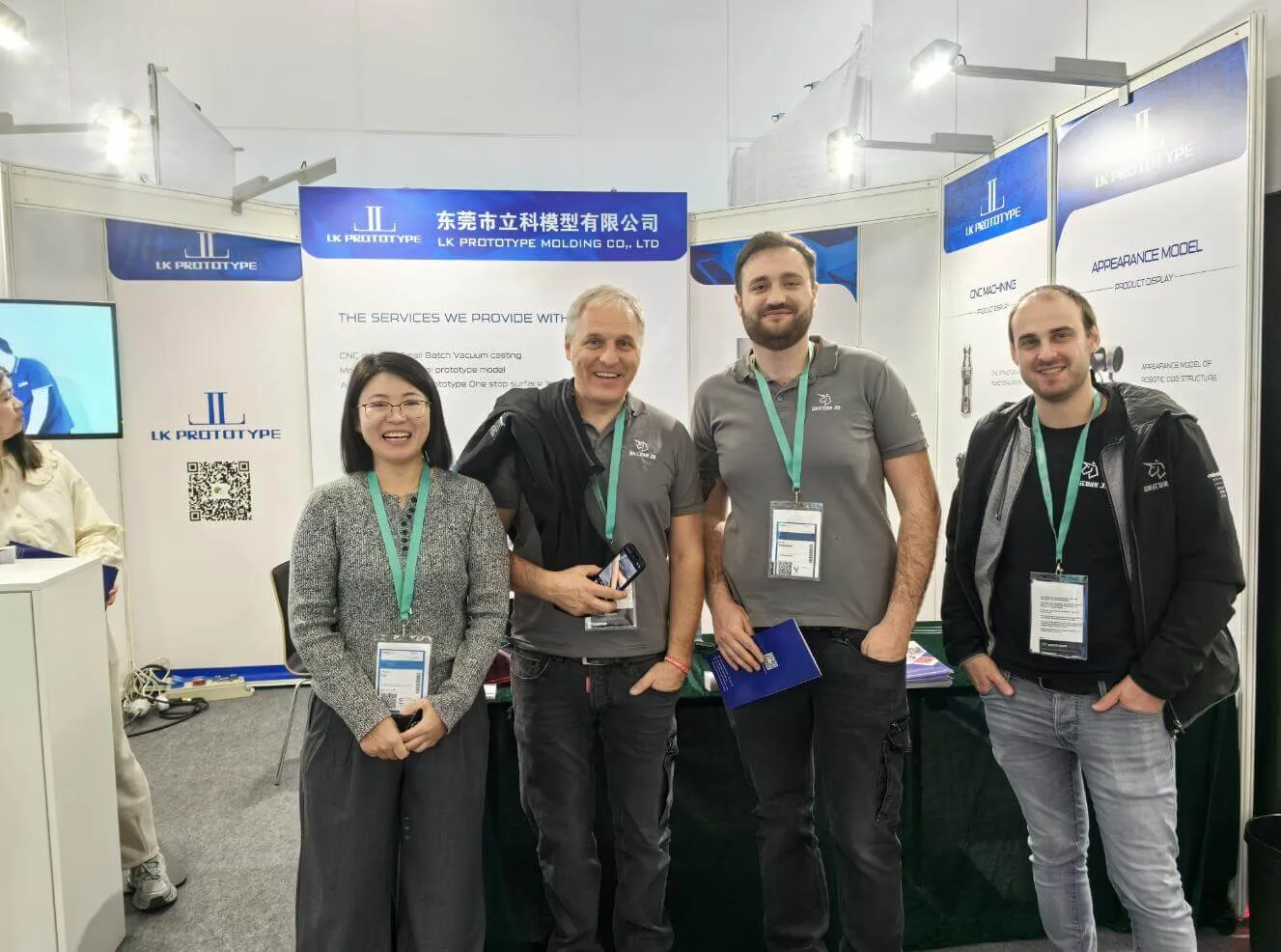
9. Choosing a CNC Machining Supplier
Choosing the right CNC machining supplier is crucial for the success of your project. With numerous options available, it can be overwhelming to select the best one. Here are some key factors to consider when choosing a CNC machining supplier:
Experience and Expertise: Look for a supplier with extensive experience in CNC machining and a proven track record of delivering high-quality parts. Ensure they have expertise in working with various materials, including metals, plastics, and composites. A seasoned supplier will be adept at handling complex projects and providing valuable insights to optimize your designs.
Equipment and Technology: A reliable supplier should have a range of CNC machines, including milling, turning, and grinding machines. They should also be equipped with the latest technology, such as computer-aided design (CAD) software and computer-aided manufacturing (CAM) software. Advanced equipment and technology ensure precision, efficiency, and the ability to produce intricate CNC machined parts.
Material Selection: Ensure the supplier has access to a wide range of materials, including stainless steel, aluminum, copper, and plastics. They should also be able to provide guidance on material selection based on your project requirements. The right material choice can significantly impact the performance, durability, and corrosion resistance of your CNC machined parts.
Tolerances and Accuracy: Check if the supplier can meet your required tolerances and accuracy standards. Look for suppliers who can achieve tight tolerances, typically +/- 0.001 inches or better. Precision is paramount in CNC machining, and achieving tighter tolerances ensures the quality and functionality of your parts.
Lead Time and Delivery: Consider the supplier’s lead time and delivery schedule. Ensure they can meet your project deadlines and provide flexible delivery options, such as expedited shipping. Timely delivery is essential to keep your project on track and avoid costly delays.
Quality Control: A reputable supplier should have a robust quality control process in place, including inspection and testing procedures. Look for suppliers who are ISO 9001 certified or have equivalent quality management systems. Rigorous quality control ensures that your CNC machined parts meet the highest standards of quality and reliability.
Communication and Customer Service: Effective communication is critical when working with a CNC machining supplier. Ensure they have a responsive customer service team and provide regular updates on your project status. Clear communication helps in addressing any issues promptly and ensures a smooth collaboration.
Cost and Pricing: Compare prices from different suppliers, but also consider the value-added services they offer, such as design optimization, material sourcing, and assembly. While cost is an important factor, the overall value provided by the supplier should be taken into account to ensure cost-effective production without compromising on quality.
Certifications and Compliance: Check if the supplier has relevant certifications, such as AS9100 for aerospace or IATF 16949 for automotive. Ensure they comply with industry-specific regulations and standards. Certifications indicate the supplier’s commitment to quality and adherence to industry best practices.
Reputation and Reviews: Research the supplier’s reputation online, reading reviews from previous customers. Check their ratings on platforms like Google or industry-specific directories. Positive reviews and high ratings are indicators of a reliable and trustworthy CNC machining supplier.
By considering these factors, you can select a reliable CNC machining supplier who can deliver high-quality parts on time and within budget. Remember to also ask about their CNC machining costs, corrosion resistance, and online CNC machining services to ensure they meet your project requirements.
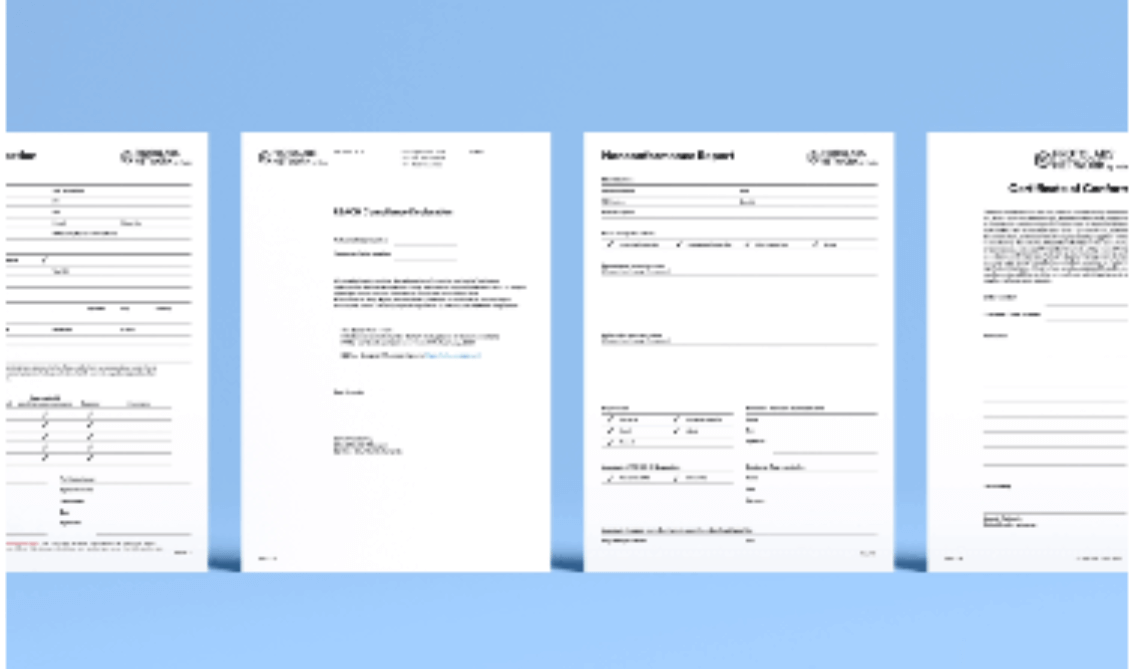
10. Quality Assurance and Certifications
At LKprototype, we take pride in our commitment to quality assurance and certifications. Our ISO 9001:2015, ISO 13485, IATF 16949:2016, and AS9100D certified quality management system ensures that our CNC machined parts meet the highest standards of quality and reliability. We also offer options to add inspections, hardware traceability, material certifications, and CoCs to provide our customers with added assurance. Our team of experienced engineers and machinists work closely with our customers to ensure that their CNC machining projects meet their exact specifications and requirements.
11. Cost Considerations and Budgeting
When it comes to CNC machining, cost considerations and budgeting are crucial. At LKprototype, we offer competitive pricing and flexible production options to meet our customers’ budget needs. Our online CNC machining service allows customers to get instant quotes and compare prices for different materials and production options. We also offer a range of cost-saving options, such as reducing material waste, optimizing part design, and using cost-effective materials. Our team of experts can work with customers to identify areas where costs can be reduced without compromising on quality.
CNC Machining Industry Applications
CNC machining has a wide range of industry applications, including aerospace, automotive, medical devices, and consumer electronics. In the aerospace industry, CNC machining is used to create precision components such as engine parts and satellite components, requiring high precision and reliability. In the automotive industry, CNC machining is essential for producing parts like engine blocks and gearboxes, ensuring durability and performance. The medical device industry relies on CNC machining for creating precise components such as surgical instruments and implants, where accuracy is critical. In the consumer electronics industry, CNC machining is used to manufacture components like phone cases and laptop parts, combining functionality with sleek design.
Advantages of CNC Machining Materials
High precision and consistency: Ensuring quality for complex parts. Proper material selection is crucial for ensuring the quality and performance of complex parts.
Quick delivery: Accelerating product development cycles.
Flexibility: Supporting small-batch and customized production needs.
To reduce CNC machining costs, consider optimizing your design by selecting appropriate materials and incorporating design features like corner fillets and avoiding undercuts.
Additionally, the cnc machining advantages include high accuracy, repeatability, and capability for continuous operation, which allows for on-demand production of both one-off and high-volume parts.
Best Practices for Collaborating with a Service Provider
Providing detailed design files and machining requirements. Using an online CNC machining service can provide instant quotes and streamlined ordering for custom parts, ensuring a more efficient process.
Maintaining clear communication and adjusting plans as needed.
Regularly evaluating results to ensure quality and timely delivery.
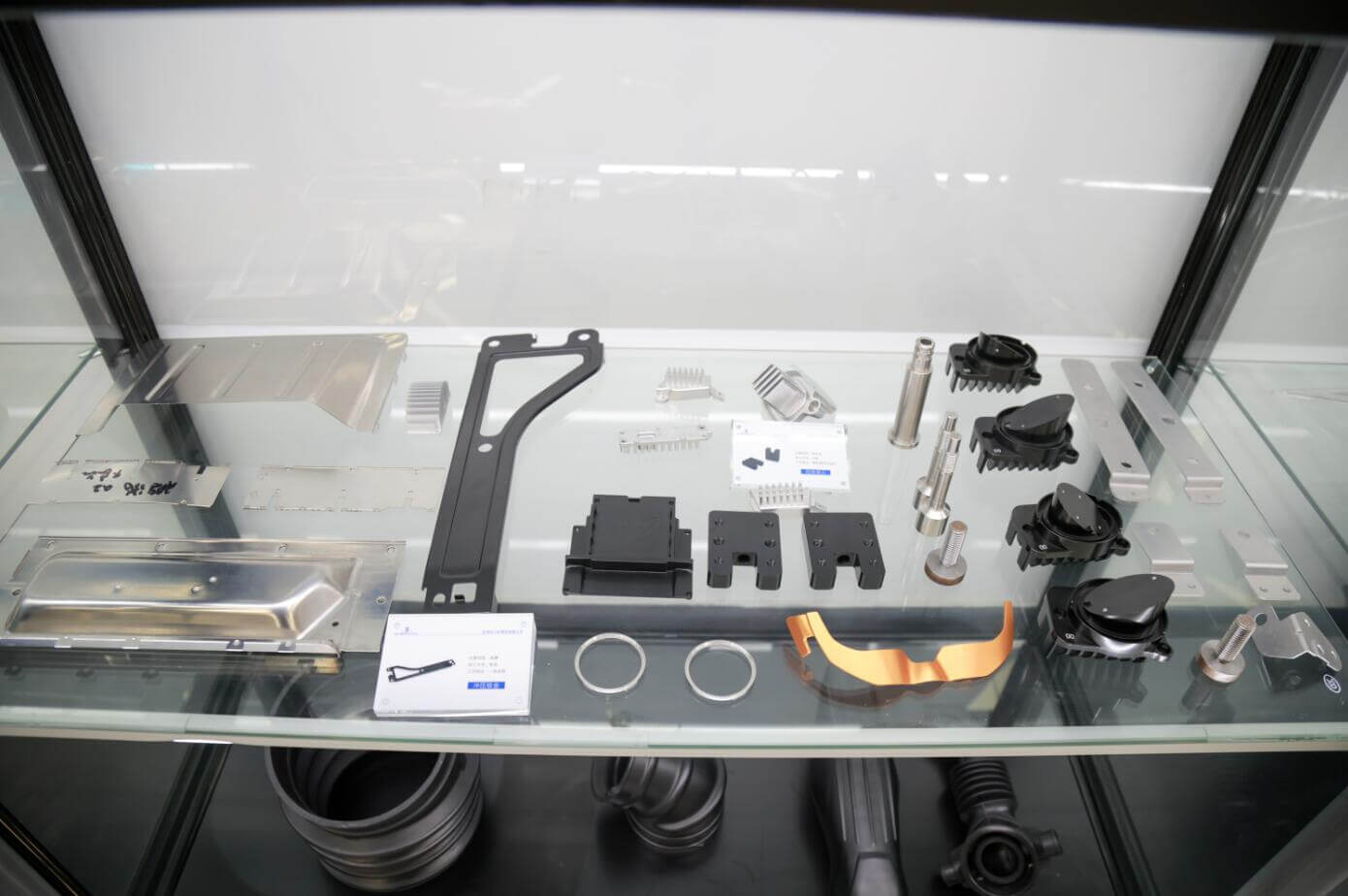
Case Study: Successful CNC Machining Projects
Real-life examples of successful machining projects (highlighting LKprototype) demonstrate high-quality and efficient machining services.
LKprototype excels in producing both prototypes and production parts rapidly, ensuring quality and reliability.
Technological Advancements in CNC Machining
The field of CNC machining is constantly evolving, with new technological advancements emerging every year. At LKprototype, we stay at the forefront of these advancements, investing in the latest CNC machines and software to ensure that our customers receive the highest quality parts. Some of the recent technological advancements in CNC machining include the use of artificial intelligence and machine learning to optimize machining processes, the development of new materials and coatings, and the integration of CNC machining with other manufacturing processes such as 3D printing.
Environmental Impact and Sustainability
At LKprototype, we are committed to reducing our environmental impact and promoting sustainability in our CNC machining operations. We strive to minimize waste and reduce energy consumption in our manufacturing processes, and we offer eco-friendly materials and production options to our customers. We also partner with suppliers who share our commitment to sustainability and environmental responsibility. By choosing LKprototype for your CNC machining needs, you can be confident that you are supporting a company that prioritizes the environment and sustainability.
Customer Support and Communication
At LKprototype, we pride ourselves on our exceptional customer support and communication. Our team of experienced engineers and machinists are available to answer any questions or concerns you may have about your CNC machining project. We offer a range of communication channels, including phone, email, and online chat, to ensure that you can reach us whenever you need to. We also provide regular updates and progress reports on your project, so you can stay informed and up-to-date on the status of your parts. Our goal is to provide our customers with the highest level of service and support, and we strive to exceed their expectations in every way.
Future Trends in Online CNC Machining Services
Future Trends in CNC Machining Services
The impact of digitalization and smart manufacturing on machining processes is profound. Advancements in machining technology continue to drive improvements in efficiency and quality. Online CNC machining services have revolutionized the industry by providing instant quotes, quick turnaround times, and high-quality standards, making them an integral part of smart manufacturing. These services cater to a wide range of industries through a network of suppliers, ensuring efficiency and reliability in their offerings.
The role of sustainability and eco-friendly practices in CNC machining.
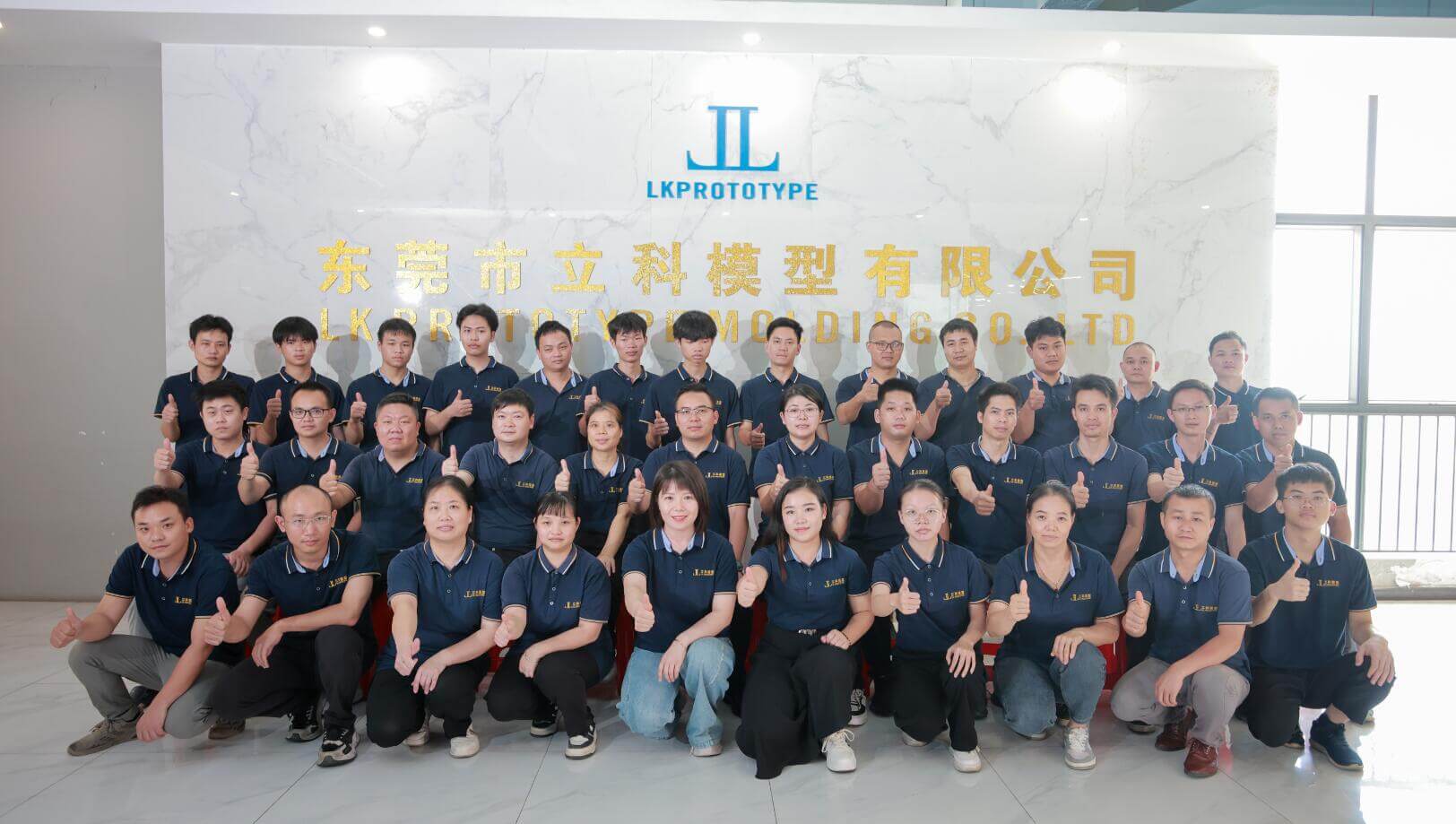
Conclusion:
CNC machining services are vital to modern manufacturing.
Choosing a professional supplier like LKprototype ensures superior quality, efficiency, and reliability for complex projects.