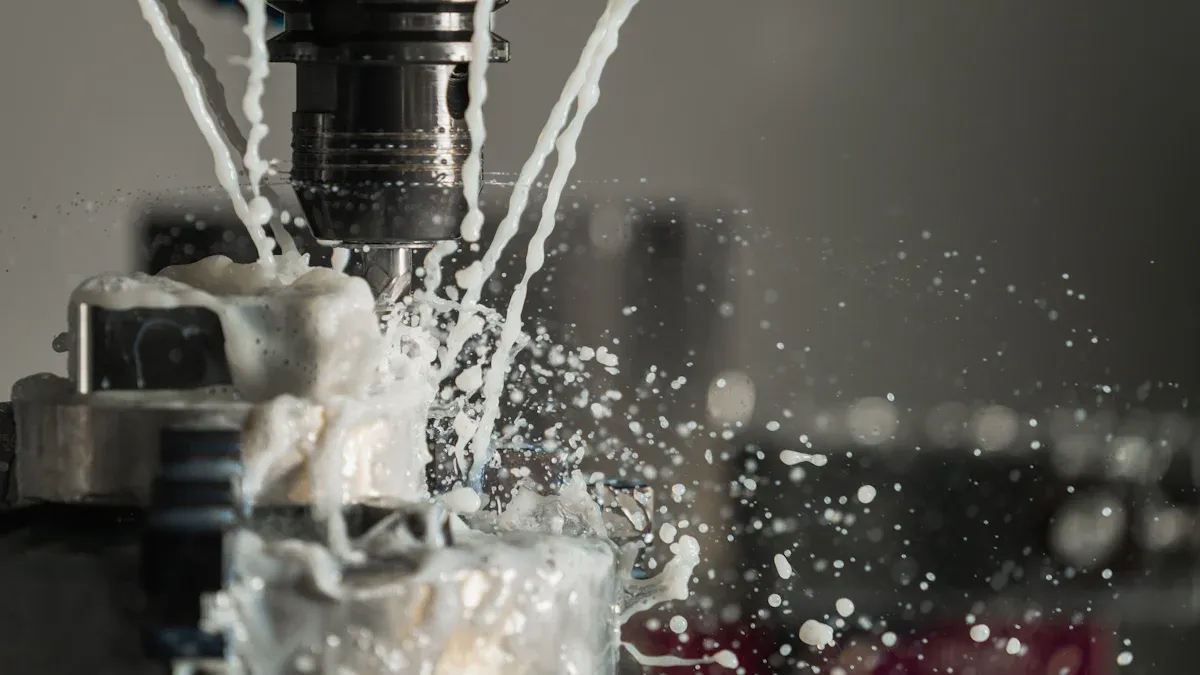
A CNC Wood Cutting Machine uses speed and accuracy for woodworking jobs. You can change settings like spindle speed, cutting depth, and feed rate to get different results. For example:
Spindle speeds from 8000 to 12,000 RPM work for many wood types.
Cutting depths between 0.08 and 0.20 inches make deeper cuts while keeping good quality.
Feed rates of 0.003 to 0.005 inches per tooth balance smooth surfaces and tool wear.
These settings help the machine cut solid wood and hardwood up to 150mm thick well. Knowing these settings lets you improve the machine for your needs.
Key Takeaways
Change spindle speed, cutting depth, and feed rate to match wood type and project needs.
Pick speed or precision based on your project. Use fast speeds for big jobs and slow speeds for detailed work.
Take care of tools and machine settings often to keep cuts clean and avoid extra costs from worn tools.
Try machine settings on scrap wood first to find the best setup and prevent errors.
Select the right CNC machine for your space, project size, and needed precision to work better and get good results.
Speed vs. Precision in CNC Wood Cutting Machines
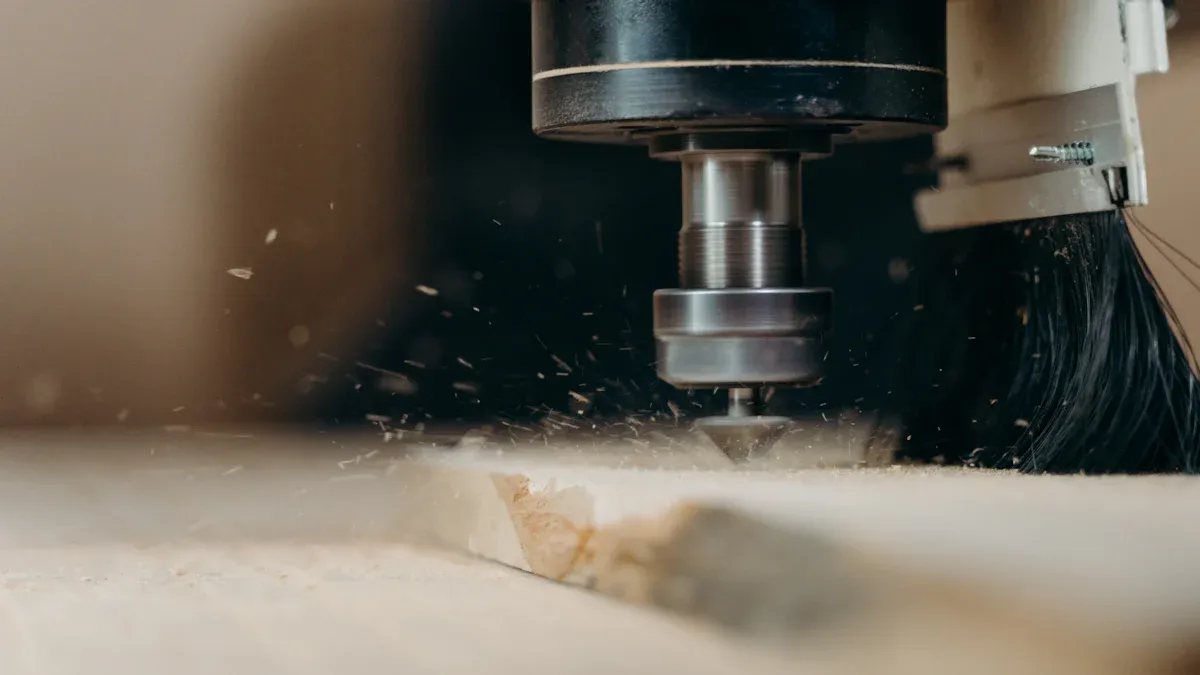
What is Speed in CNC Wood Cutting?
Speed means how fast the machine cuts wood. It is measured using Surface Feet per Minute (SFM). SFM shows how quickly the tool moves on the wood. Think of it like a speedometer for cutting. Changing SFM can make tools last longer and improve the wood's finish.
For example, higher SFM makes the tool cut faster. This saves time but may wear out tools faster or leave rough edges. Lower SFM slows cutting but gives better precision and tool life. Knowing how to adjust SFM helps the machine work better.
What is Precision in CNC Wood Cutting?
Precision means how exact and detailed the cuts are. It ensures the final piece matches the design with few mistakes. Precision depends on the machine's setup, tool quality, and material stability.
For example, a precise CNC machine can make detailed designs or perfect-fitting parts. This is important for fine woodworking or custom furniture. Precision improves quality and reduces wasted material by avoiding errors.
Why Are Speed and Precision Important?
Both speed and precision matter in woodworking, but their importance changes with the job. For mass production, speed is more important. Faster cutting makes more items quickly, which is good for high demand. But too much speed can lower quality.
For detailed projects like carvings or custom furniture, precision is key. Small mistakes can ruin the work. Balancing speed and precision is important for great results. A CNC machine lets you adjust settings to fit your project needs.
Factors Affecting Speed and Precision
Material Type and Its Properties
The material you use affects how fast and precise cuts are. Different materials need different spindle power levels for the best results. For example:
Softwoods and Plastics: Use 1 kW to 3 kW power. This avoids splintering or melting.
Hardwoods: Use 3 kW to 4 kW power. This gives smooth cuts because hardwoods are dense.
Composites and Advanced Materials: These need 4 kW to 6 kW power. Their roughness requires more strength.
Material traits like density, moisture, and fiber direction also matter. Moisture changes how tools cut the wood. Fiber direction affects surface smoothness and bonding. Keeping the room temperature and humidity steady helps materials behave consistently. This ensures accurate cuts.
Machine Settings and Calibration
Good machine settings and regular checks are key for quality cuts. Adjusting spindle speed, feed rate, and cutting depth helps match the machine to your needs. Studies show moisture and energy levels affect surface quality. For example:
Parameter | How It Helps | Study Source |
---|---|---|
Makes tools and settings work better | Hill et al. (2021) | |
Energy Levels | Lowers defects and improves surface finish | Kúdela et al. (2023) |
Fiber Orientation | Helps with bonding and smoother surfaces | Wagenführ and Scholz (2008) |
Regular checks keep the machine aligned and accurate. Advanced software can improve cutting paths, saving time and boosting efficiency.
Tool Quality and Maintenance
Good tools and care make cuts cleaner and more exact. High-quality tools reduce shaking, giving smoother results. Regular checks find problems early before they get worse. Predictive technology can warn about issues using machine data. Fixing parts early can save up to 40% in costs.
Tools like probes and sensors check sizes and tolerances during cutting. Real-time tracking allows quick fixes, reducing mistakes and waste. Using top-notch tools and keeping them in good shape ensures your CNC machine works perfectly every time.
Workpiece Thickness and Complexity
The thickness and design of your wood affect how a CNC machine works. Thicker wood needs more power and slower cutting to stay neat. Detailed designs need careful control and precise tools.
How Thickness Affects Cutting
Thicker wood needs changes in cutting depth and speed. Cutting too deep at once can harm the tool. Instead, make shallow cuts in steps to reach the needed depth. For example:
Thin Wood (up to 10mm): Use faster speeds and feed rates.
Medium Wood (10mm–50mm): Use balanced settings for good results.
Thick Wood (50mm and above): Use slower speeds to avoid overheating tools.
Tip: Always follow the manufacturer's advice for cutting settings. This keeps tools safe and results consistent.
Handling Complex Designs
Detailed designs like carvings need small, precise tools. Small tools work well for tight spaces but take longer. Advanced software can plan better tool paths to save time.
Balancing Thickness and Design
To get great results, balance thickness and design needs. For thick, detailed wood, focus on precision over speed. Test settings on scrap wood before starting your project. This reduces mistakes and saves material.
Note: High-quality tools and software help handle tough projects better.
Trade-offs in Application-Specific Scenarios
High-Speed Applications (e.g., Mass Production)
Speed is very important for making many items quickly. Industries like automotive and aerospace use CNC machines to meet high demand. Faster cutting saves time and helps produce more items. But, it can lower precision, especially for detailed designs.
For example, an automotive company added advanced CNC machines to its factory. This change cut production time by 30%. An aerospace company used CNC laser cutting to make lightweight parts. This improved material use and reduced waste.
Industry | Example Description | Result |
---|---|---|
Automotive | A car company added advanced CNC milling machines to its factory. | Production time cut by 30%. |
Aerospace | A plane company used CNC lasers to make lightweight parts. | Better material use and less waste. |
Optical | A maker of optical tools used robots and CNC machines to triple production. | Higher efficiency in manufacturing. |
High-speed cutting works well for mass production but needs careful checks. This prevents tool damage and keeps quality acceptable.
High-Precision Applications (e.g., Fine Woodworking)
Precision is key for projects like custom furniture or carvings. CNC machines for precision work make exact cuts and detailed designs.
For example, a well-tuned machine can cut with an accuracy of 0.0005". Many high-end machines keep tolerances between +/- .001" and .002". They aim for a working accuracy of .1mm or 4 thousandths, often reaching .2mm in real use.
Measurement | Accuracy Level |
---|---|
Dimensional Deviation | +/- .001" - .002" |
Working Target | .1mm or 4 thousandths |
Real Life Results | .2mm or better |
Machine Capability | 0.0005" |
Precision machines are great for jobs where small mistakes ruin the work. They focus on quality over speed to match designs perfectly.
Balancing Speed and Precision for Versatile Applications
Finding the right mix of speed and precision is important. Fast cutting boosts efficiency but can cause errors in detailed designs. On the other hand, focusing on precision slows production, which isn’t ideal for big projects.
For example, balancing these settings lets CNC machines handle both mass production and detailed tasks. Adjustable settings like spindle speed, feed rate, and cutting depth help match the machine to your needs. This flexibility allows switching between fast and precise work without losing quality.
Tip: Test your machine settings on scrap wood first. This helps you find the best balance and avoid mistakes.
Selecting the Right CNC Wood Cutting Machine
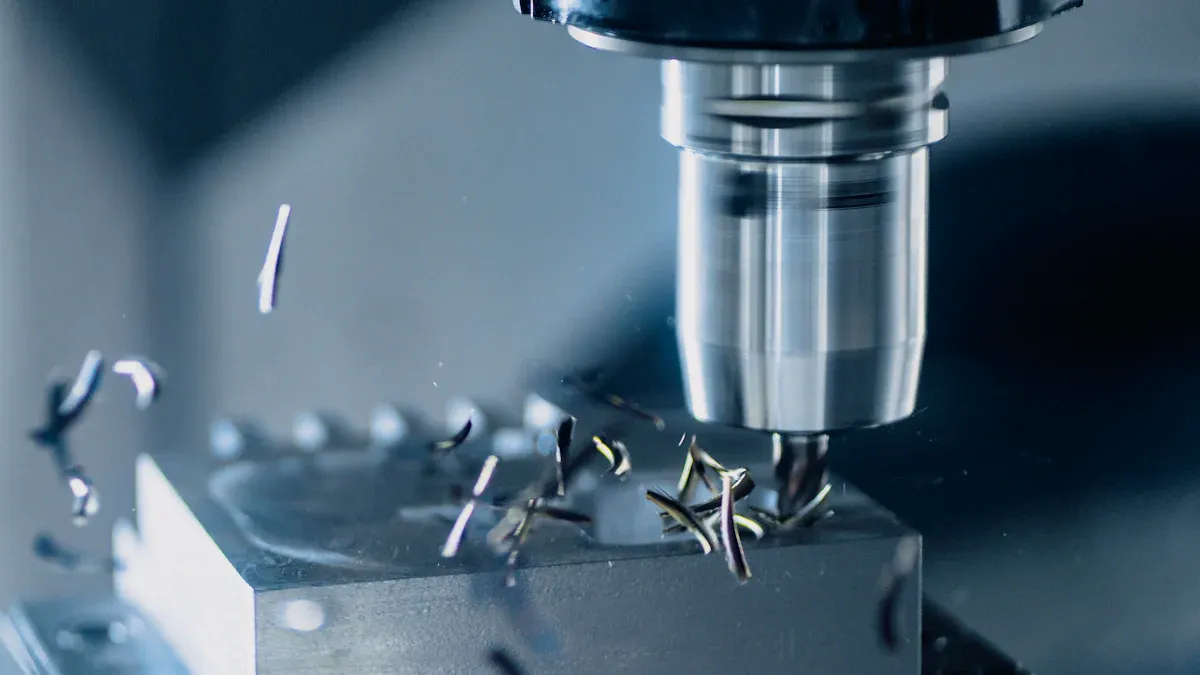
Understanding What You Need
Picking the right CNC wood cutting machine starts with knowing your needs. Each project is different, so matching the machine to your work is important. Think about these key points:
Requirement | What to Consider |
---|---|
Workspace Size | Check if the machine fits your workspace and can handle your workpieces. Make sure loading and using it will be easy. |
CNC Software | Pick software that turns designs into machine actions. Check if it works with your computer system and decide between open-source or brand-specific options. |
Spindle Choices | Choose between built-in spindles for better precision or attachable routers for a cheaper option. Know how each affects cutting quality. |
Dust Collection | Use a dust system to keep your workspace clean and safe. This helps the machine last longer and keeps the air healthy. |
Think about your project size and details when deciding. For example, large furniture needs a big workspace. Detailed designs need advanced software and precise spindles.
Checking Machine Features
After knowing your needs, look at the machine’s features. Focus on what affects how well it works and the quality of its output. Key things to check include:
Spindle Power: Stronger spindles cut through tough materials like hardwoods. Softer woods need less power.
Speed and Feed Settings: Machines with adjustable settings work better for different materials and designs.
Precision and Tolerance: Tight tolerances are important for projects needing exact cuts.
Build Strength: A strong frame reduces shaking, making cuts smoother and tools last longer.
Software Fit: Make sure the machine’s software works well with your design tools to avoid mistakes.
Tip: Test the machine with sample cuts before buying. This shows how it performs in real use.
How to Balance Speed and Precision
Getting the right mix of speed and precision is key for great results. Here are some simple tips to help:
Match the cutting process to your project. Think about the material, design, accuracy needed, how many items you’re making, and your budget.
Use smart toolpaths to save time. These paths cut down on extra tool movements while staying accurate.
Change spindle speed and feed rate based on the material. Faster speeds are good for softwoods, while slower speeds help with detailed designs.
Keep your tools sharp and your machine in good shape. This ensures steady performance.
Note: Try different settings on scrap wood first. This helps you find the best balance and avoid wasting materials.
Hidden Costs and Optimization Strategies
Tool Wear and Replacement Costs
Using a CNC wood cutting machine can lead to hidden costs. One major cost is replacing worn-out tools. Items like cutting tools and end mills need regular changes to keep cuts accurate. Businesses usually spend $500 to $5,000 each year on new tools. Maintenance, such as repairs and checks, adds another $1,000 to $5,000 annually.
Here’s a simple breakdown of these hidden costs:
Hidden Costs | Estimated Annual Amount |
---|---|
Tooling & Consumables | $2,500 |
Maintenance | $1,200 |
Software Licenses & Training | $1,500 |
Utilities (Power, Coolants) | $800 |
$6,000 |
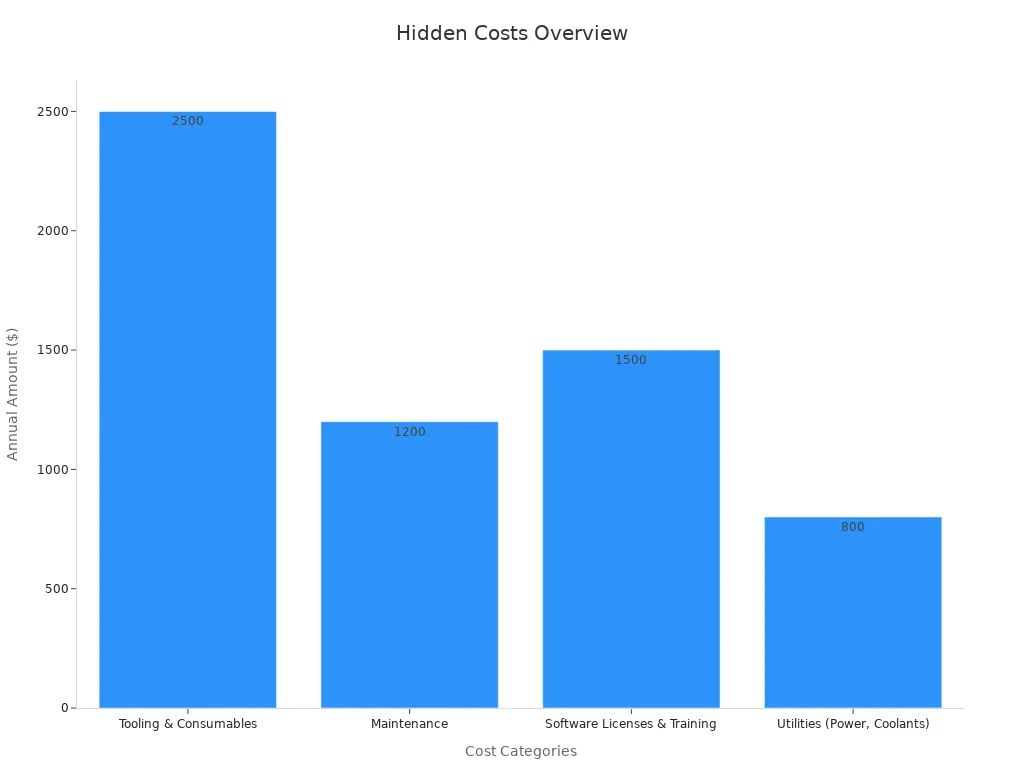
Knowing these costs helps you plan better and avoid surprises.
Energy Consumption and Efficiency
Electricity is another hidden cost that affects your budget. CNC machines use a lot of power, making up 15% to 20% of overhead costs. Switching to energy-saving machines can cut energy use by 20%, saving money over time.
Checking how efficiently your machine runs is also important. Using less energy lowers costs and improves production quality. Smarter energy use helps save money and supports eco-friendly practices.
Tip: Buy energy-efficient CNC machines and check their performance often to save more.
Strategies for Reducing Costs Without Compromising Quality
You can lower costs without losing quality by following these tips:
Design for Manufacture: Keep designs simple to match what CNC machines can do.
Material Selection: Pick affordable materials that still meet your project needs.
Tooling Optimization: Use sharp, well-maintained tools for better cuts and less downtime.
Batch Manufacturing: Make more parts at once to spread setup costs.
Efficient Toolpaths: Use advanced software to create faster, accurate cutting paths.
Note: Better toolpaths save time, protect tools, and improve finished parts.
By using these methods, you can save money while keeping your work high-quality.
Balancing speed and precision in a CNC wood cutting machine is key for great woodworking results. High heat and tool wear can damage tools faster, especially with wet wood. Moisture in wood can cause chemical reactions that dull tools. This makes it important to use the right settings. Tight tolerances need specific speeds and feed rates for accuracy.
Evidence Description | Key Points |
---|---|
High Heat and Tool Wear | Heat wears tools faster, especially with wet wood. |
Electro-Chemical Wear | Wet wood causes reactions that dull tools quickly. |
Tight Machining Tolerances | Correct speeds and feed rates improve accuracy. |
Use cutting speeds of 150 to 300 SFM for smooth surfaces.
Change feed rates and cut widths to match the material for better results.
By thinking about the material, machine settings, and hidden costs, you can pick the right machine for your needs. This helps you save money, work efficiently, and get high-quality results in your projects.
FAQ
What is the best CNC machine for beginners?
Choose a machine with simple software and easy controls. A small CNC router with basic options is great for starters. Look for safety features to learn confidently.
Tip: Practice on softwoods first before trying harder materials.
How often should you care for a CNC wood cutting machine?
Do basic care every week. Sharpen tools, clean dust, and check parts. Every three months, do a full check to keep it accurate and avoid problems.
Note: Regular care makes the machine last longer and saves on repairs.
Can a CNC machine cut all kinds of wood?
Yes, but settings must match the wood type. Softwoods need less power, hardwoods need more power and slower speeds, and composites may need special tools.
Wood Type | Suggested Power |
---|---|
Softwood | 1–3 kW |
Hardwood | 3–4 kW |
Composite | 4–6 kW |
How can you make cuts more precise?
Use sharp tools and check the machine often. Keep the material steady and use advanced software for better cuts. Test settings on scrap wood to get the best results.
Tip: Keep the area clean to stop vibrations that can mess up cuts.
Is CNC woodworking good for small businesses?
Yes, it lowers labor costs and reduces wasted materials. The starting cost is high, but faster and consistent work saves money over time.
Emoji Insight: 💡 CNC machines can make your business more efficient!