This guide will explore the most common CNC machining types and their applications in precision manufacturing.
Key Takeaways
CNC machining encompasses various machine types, including milling, lathes, and laser cutters, each suited for specific manufacturing processes and industries.
The selection of the appropriate CNC machine depends on factors such as material type, part complexity, and required precision, crucial for optimizing manufacturing efficiency.
CNC machining provides significant advantages like precision and uniformity, but it also poses challenges such as higher costs and system complexity, necessitating proper training for effective operation.
CNC Milling Machines
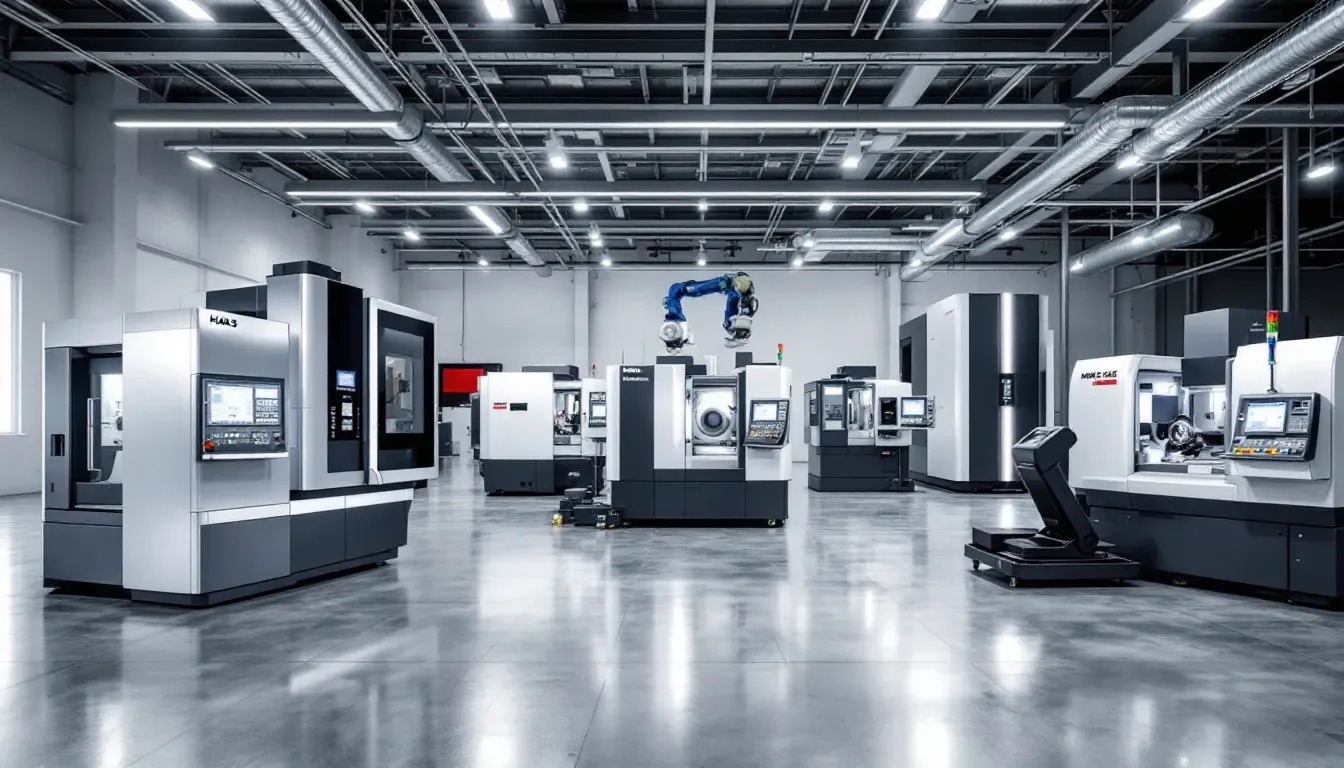
CNC machines, specifically CNC milling machines, are pivotal in the realm of CNC machining as they employ rotary cutting tools that move along multiple axes to sculpt materials according to programmed designs. These machines carry out a range of functions such as drilling and threading with great detail for complex parts creation. Acquiring premium-quality CNC equipment can significantly boost both the accuracy and efficiency brought about by a cnc machine. Within this domain, CNC mills are indispensable.
Available in diverse configurations ranging from basic 3-axis models (X,Y,Z) up to advanced 6-axis versions—which include an additional rotational axis—cnc milling machines offer extraordinary versatility allowing work on every plane of an object. The array of cutting tools utilized includes end mills, face mills, and various drills. All serving different purposes during fabrication processes. This demonstrates not only their precision but also their adaptability which makes them highly sought after across many sectors within manufacturing circles due to the variety among types of cnc machinery options available for use.
CNC Lathe Machines
CNC lathes secure and spin the material being worked on, while the stationary cutting tool performs its task with precision. This method of using a central spindle to rotate creates highly accurate cylindrical and conical objects, making CNC lathe machines perfectly suited for sectors requiring intricate and symmetrical components.
In CNC lathe operations, single-point cutting tools carry out tasks such as turning, sanding, and drilling. Items ranging from musical instruments like electric guitars to medical devices such as dental crowns are crafted using these machine tools. Due to their ability to produce parts more quickly and accurately than manual lathes, CNC lathes are particularly advantageous when creating uniform pieces.
CNC Drilling Machines
Rotating drill bits are utilized by CNC drilling machines to form cylindrical holes in workpieces. These machines are capable of carrying out not only drilling but also reaming and tapping on a variety of materials, including metal, wood, and plastic. This versatility allows them to meet diverse manufacturing requirements.
Components such as gear blanks, machined shafts, and hubs are fabricated using CNC drilling machines. They come in various forms like radial arm drill presses and upright drill presses. Each type provides unique benefits for particular applications. The precision and adaptability of CNC drilling make it an essential process in the manufacturing industry.
CNC Plasma Cutting Machines
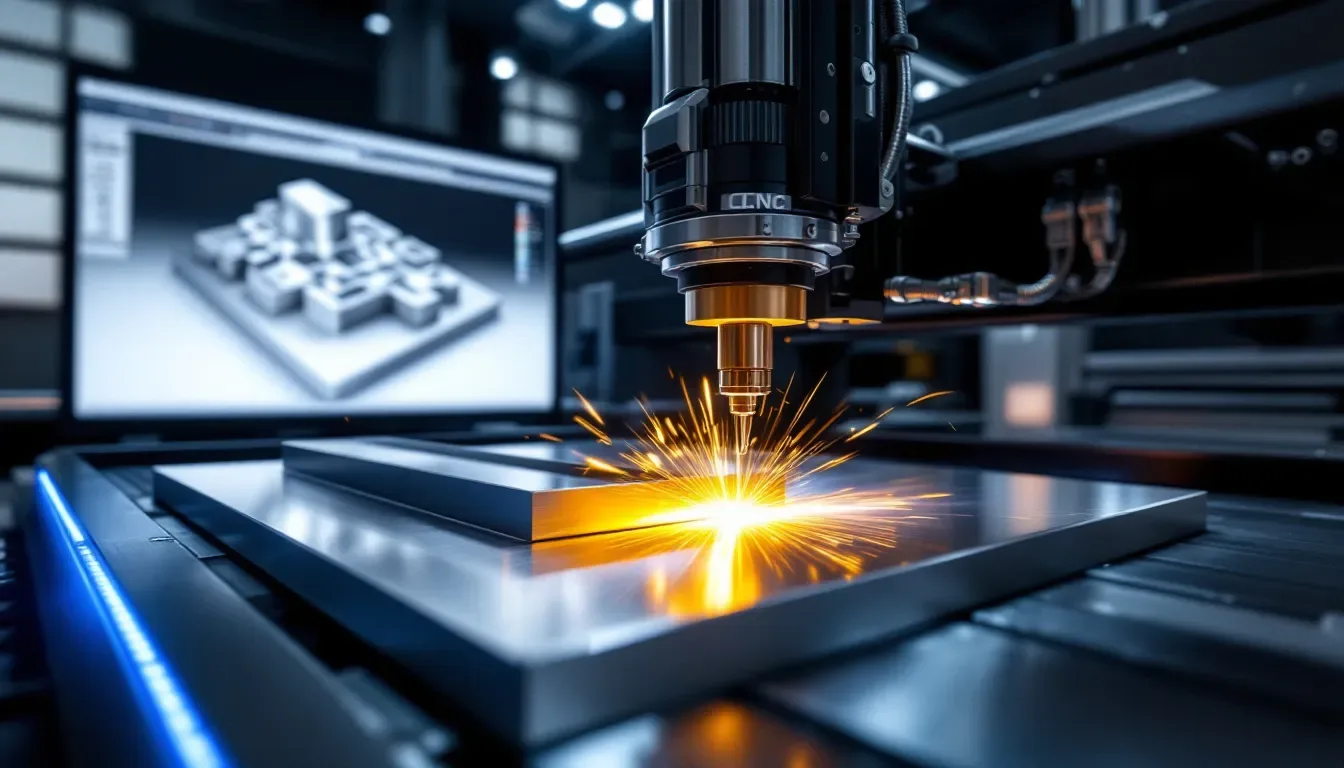
CNC plasma cutting machines operate by employing a potent plasma torch combined with an electrical discharge arc to slice through conductive substances such as metals and alloys. By forcing high-speed gas through a constricted nozzle, the plasma torch attains temperatures as elevated as 50,000 °F, enabling swift and meticulous cuts that might compromise the surface finish.
These CNC plasma cutters are widely utilized across various industries including automobile production, shipbuilding, and fabrication due to their ability to rapidly and effectively handle thick materials. Nevertheless, investing in a CNC plasma cutting machine requires substantial capital outlay. Prices vary from $12,000 to $300,000 based on their specifications and functionalities.
CNC Laser Cutting Machines
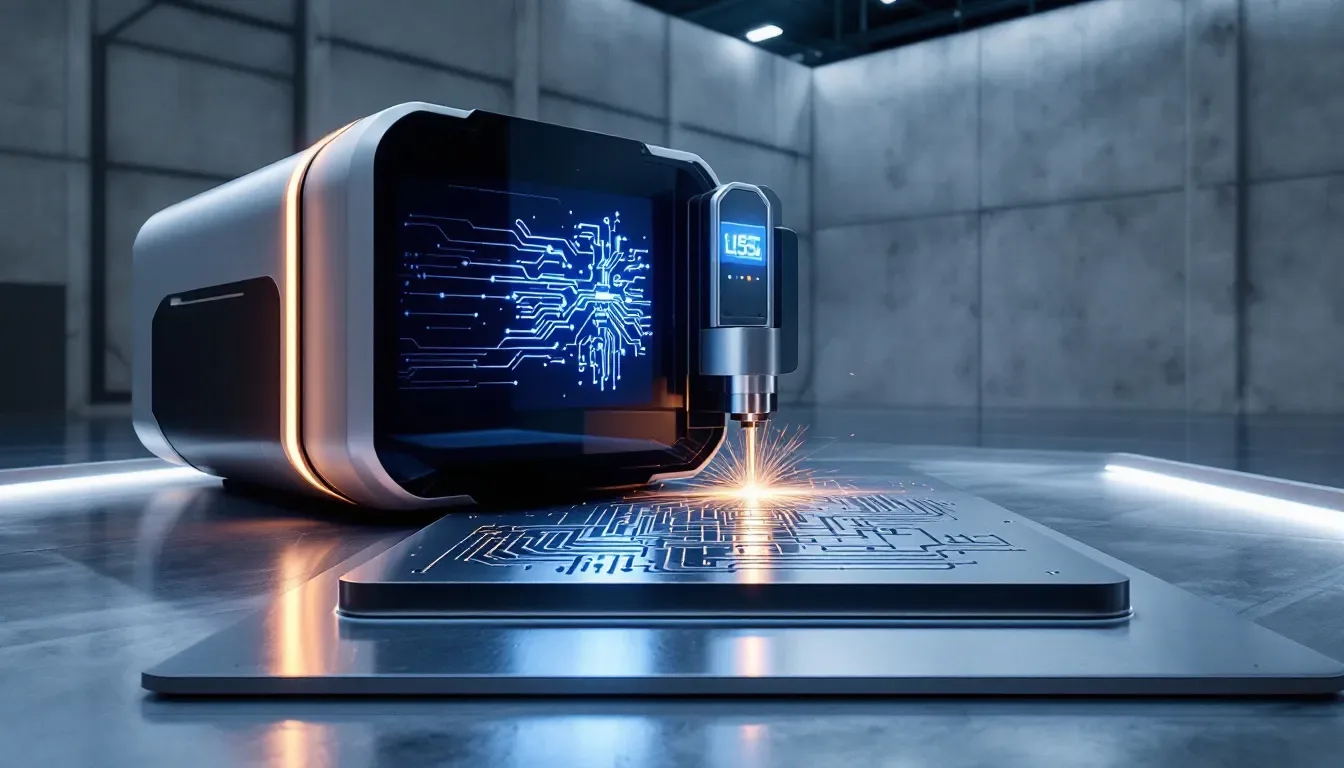
CNC laser cutters employ concentrated beams of light to accurately slice and mark a diverse array of materials such as metals, plastics, wood, and fabrics. They provide an unparalleled level of precision with tolerances ranging between +/- 0.1 mm and +/- 0.01 mm, which is superior to the accuracy achievable by plasma cutting.
There are various models of CNC laser cutting machines available that operate on gas, liquid or solid-state technologies tailored for particular tasks. These advanced tools can generate intricate patterns beyond the capabilities offered by conventional machining techniques – a feature especially critical in sectors like aerospace and medical technology. They deliver neat edges often without needing additional finishing steps - an attribute where they hold an edge over their counterparts: CNC plasma cutters.
CNC Electrical Discharge Machines (EDM)
CNC Electrical Discharge Machines (EDM) employ electrical discharges to meticulously erode material, enabling precise machining control. They are particularly adept at creating complex shapes and internal structures that conventional techniques struggle with. The versatility of a CNC electrical discharge machine is Highlighted by its capability to process any electrically conductive materials, encompassing even the most resilient alloys.
These machines generate electrical discharges capable of reaching temperatures from 8000°C to 12000°C, which effectively melts the material without causing distortion in the workpiece. Such high-precision operation renders EDM an indispensable tool for sectors that demand intricate and exact machining processes, including those in aerospace and medical device production.
CNC Grinding Machines
CNC grinding machines employ a spinning wheel to meticulously subtract material from metal, aiming for precise finishing. This is often achieved using wheels made of a ceramic blend. The process executed by these machines is versatile, enabling the production of diverse workpieces such as cylindrical items and it’s frequently utilized to deliver precision finishes on metallic components.
The techniques encompassed by CNC grinding range from surface and centerless grinding to internal and creep feed grinding, each tailored for distinct manufacturing needs. The machinery regularly produces intricate products like camshafts, ball bearings, and drive shafts. Although the rate at which material is removed may be slower, the rate at which material is removed may be slower. To other methods, CNC grinding remains indispensable for achieving exacting standards of quality in finished products.
CNC Waterjet Cutting Machines
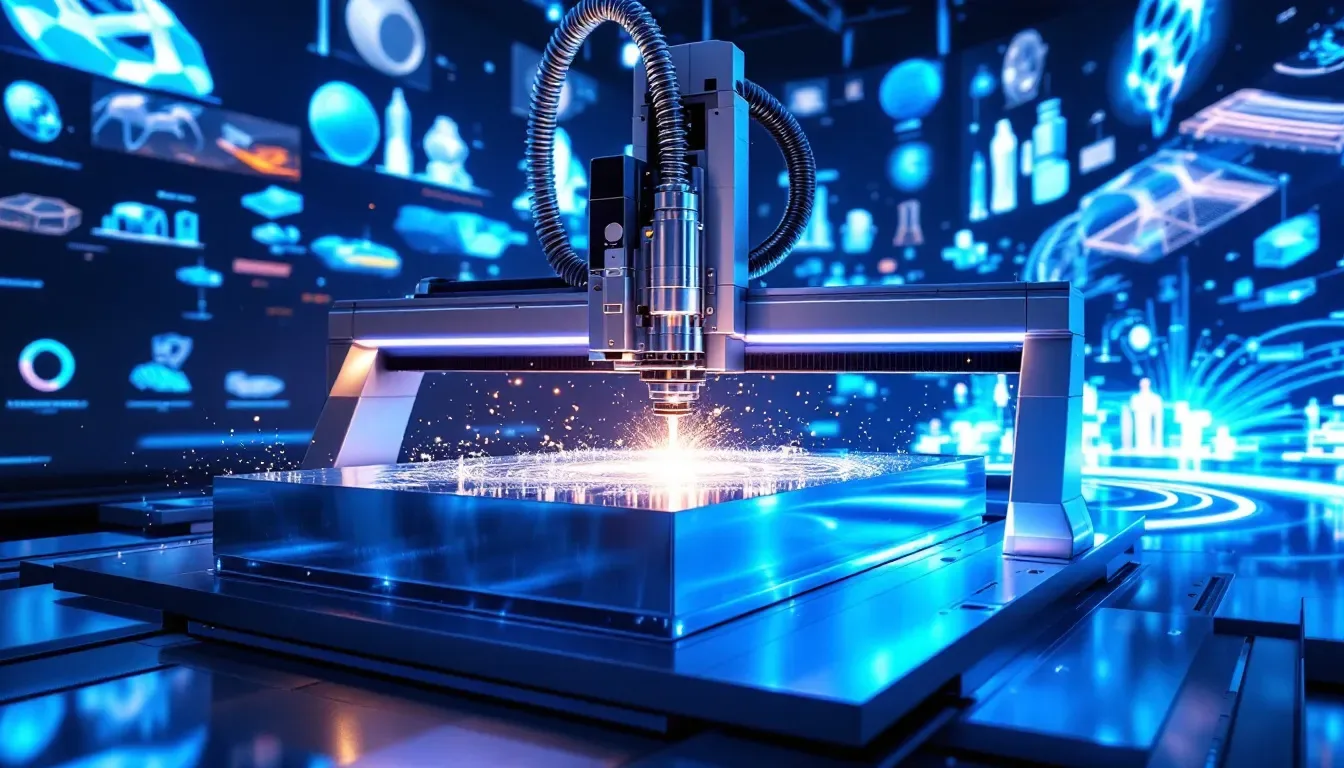
A CNC waterjet cutting machine employs high-pressure water streams as its principal cutting method, relying on high-pressure pumps to reach the required velocity of the jet. This slender stream of water wears down materials, making it possible to slice through hard substances up to 200 mm thick without producing any thermal effects.
This technique is adept at fashioning intricate designs while maintaining the wholesomeness of the material since it steers clear of thermal distortion and warping. For more challenging materials, adding abrasive substances into the mix with water can improve the efficacy of waterjet cutting. Nevertheless, in terms of speed compared to plasma and laser cutters, CNC waterjet machines fall behind, which might be a drawback within operations that prioritize rapid production cycles.
CNC Routers
Primarily, CNC routers serve the purpose of slicing and sculpting materials that are flat, such as wood, plastic, and soft metals. They hold significant utility in woodworking sectors for the creation of items like furniture, cabinets, musical instruments, signs, door engravings, and moldings due to their adeptness at cutting diverse materials and crafting shapes ranging from straightforward to intricate three-dimensional forms.
Wooden products along with plastics composite substances, and non-ferrous metallic elements frequently undergo CNC routing processes. The exactitude coupled with adaptability provided by these machines render them indispensable tools within industries where nuanced detailing and personalized design work is a necessity.
3D Printers
CNC 3D printers are primarily used for prototyping across various industries, relying on CAD and CAM processes for design. The manufacturing process, known as additive manufacturing, adds material layer by layer to create the desired shape. This technology is common in 3D printing shops and other constructions.
While 3D printing can produce complex components, it is generally slower and less suitable for mass production. High procurement and manufacturing costs are additional downsides. However, it remains valuable for producing functional prototypes and testing designs.
Multi-Axis CNC Machines
CNC machines equipped with multi-axis capabilities have the ability to maneuver along four or more axes, providing superior machining potential. These systems can vary from 4-axis configurations up to those that incorporate as many as 12 axes. This range in motion supports a diversity of manufacturing procedures and enables the crafting of elaborate features and sophisticated forms that might be unattainable using conventional techniques.
With their advanced movement abilities, multi-axis CNC machines minimize the necessity for repositioning workpieces, which enhances both uniformity and efficiency throughout production cycles. They are adept at fabricating complex geometries that may include undercuts and intricate contours—features that are particularly advantageous in sectors like medical technology and aerospace engineering.
These robust CNC units possess the capacity to handle an array of material types, broadening the horizons for design innovation within manufacturing practices.
Automatic Tool Changer CNC Machines
An Automatic Tool Changer (ATC) streamlines the process of replacing cutting tools by automating it, which boosts the efficiency of CNC machining operations. This system efficiently deals with bottlenecks related to tool changes by exchanging damaged or dull tools for those suited for specific jobs, thereby greatly increasing manufacturing velocity and shortening production lead times.
There are diverse designs for tool storage in ATCs, including rotary, linear, and chain-style configurations that cater to different requirements within CNC machinery environments. The adoption of such automated systems enables swifter cycle times and diminishes idle durations throughout the machining processes.
To maintain peak functionality and extend their service life, it’s crucial to conduct routine upkeep on CNC tool changers.
Selecting the Right CNC Machine Type
Choosing the right CNC machine type involves considering factors such as material type, part complexity, and required accuracy. Different industries, such as automotive and aerospace, have specific needs that influence the choice of CNC machines.
Matching the machine type to the task is crucial for optimizing performance and efficiency. For example, CNC lathes can perform milling, boring, and tapping operations in addition to standard turning.
Business size also plays a role; smaller shops may need fewer machines, while larger manufacturers require more advanced, multi-function machines.
Applications of CNC Machining
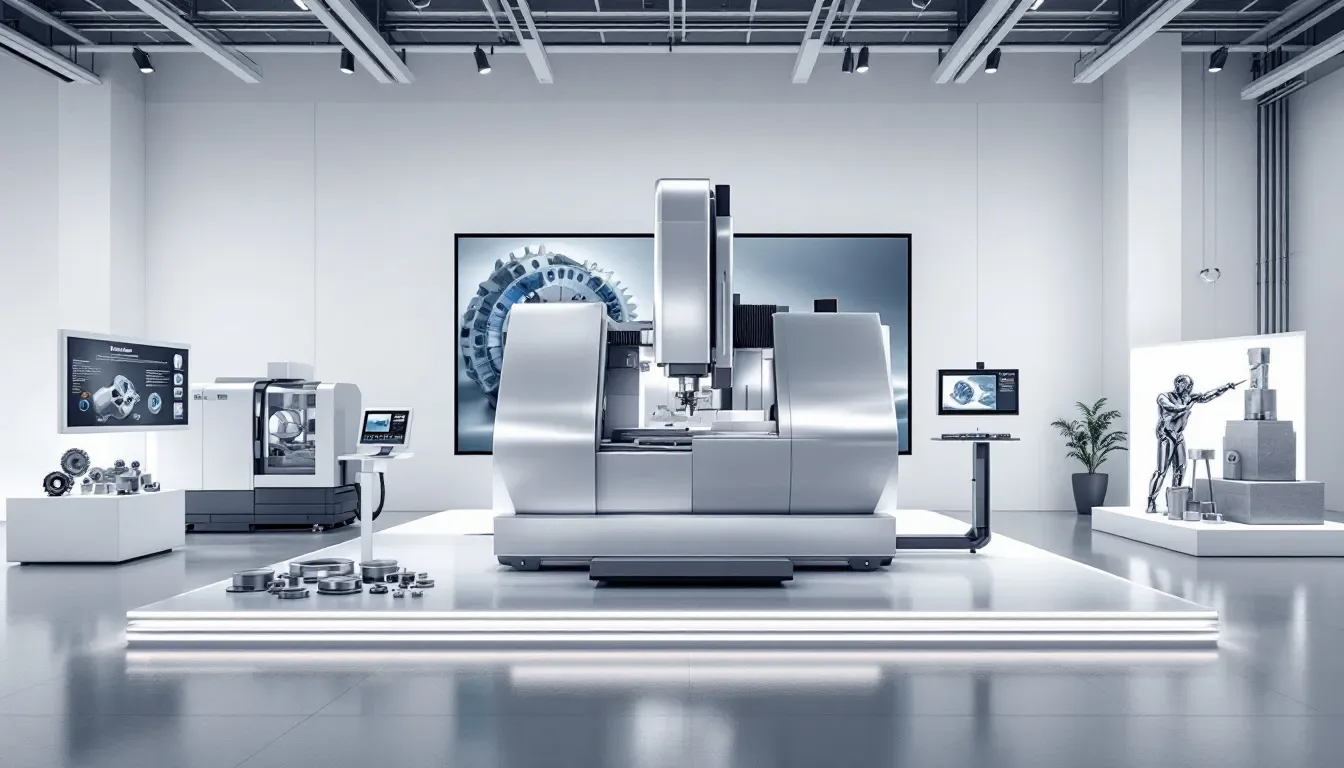
Multiple sectors, such as automotive, aerospace, medical devices, consumer electronics, and industrial equipment, utilize CNC machining extensively. In the realm of automotives, engine components and transmission systems are crafted using CNC grinding methods. Aerospace manufacturers depend on this technology to construct parts that are both lightweight and robustly durable, crucial attributes for ensuring aviation safety.
CNC grinding plays a pivotal role in the medical industry by facilitating the production of surgical tools and orthopedic implants with precision. Meanwhile, CNC 3D printing technologies have found applications across various fields including but not limited to medicine, space exploration industries like aerospace as well as automotive manufacturing due to their ability to create intricately complex pieces. The precise nature coupled with its adaptability makes CNC machining an essential asset in contemporary production processes.
Advantages and Limitations of CNC Machining
CNC machining ensures consistency in production and significantly reduces the likelihood of human mistakes. This technology excels at creating intricate shapes and patterns, making it applicable across various industries due to its adaptability. It can achieve a precision level that allows for manufacturing components with tolerances up to 0.004mm, which is crucial for sectors demanding high precision.
Although CNC machining comes with numerous benefits, it tends to be costlier compared to traditional methods. A thorough analysis of expenses is recommended. Its drawbacks include potentially elevated running costs and the complexity inherent in CNC systems might present operational challenges.
To utilize computer numerical control (CNC) machines effectively, comprehensive training is critical for accurate operation.
Summary
Exploring the various types of CNC machines has shed light on their extensive functionalities and uses within numerous fields. Ranging from CNC milling machines to multi-axis CNC variants, each category brings its own set of benefits and plays an integral role in contemporary production methods. The progress of CNC machining is fueled by technological advancements coupled with increasing demands for meticulousness and productivity.
Recognizing the distinctions among different types of CNC machinery is vital for selecting the appropriate equipment tailored to particular manufacturing requirements. The significance of CNC technology in critical industries such as automotive, aerospace, and medical cannot be emphasized enough. It facilitates the creation of superior-quality, accurate parts that are fundamental for these areas.
Looking forward, we can expect ongoing refinement and amalgamation of CNC techniques to Revolutionize manufacturing practices—bolstering creativity while enhancing efficiency. By tapping into the possibilities offered by advanced machining strategies like those provided by modern-day cnc systems—including 5-axis machines—and their continual updates remain at the forefront in this swiftly evolving industrial arena.
Frequently Asked Questions
What are the primary advantages of CNC machining?
The primary advantages of CNC machining include unmatched precision, enhanced efficiency, and the capability to produce complex shapes and designs while minimizing human errors.
These factors significantly improve overall production efficiency.
Which industries benefit the most from CNC machining?
CNC machining is a critical manufacturing process for industries such as automotive, aerospace, medical devices, consumer electronics, and industrial equipment. It facilitates the creation of custom components with high precision that are vital to their operations.
How does a CNC milling machine differ from a CNC lathe machine?
CNC milling machines utilize rotating multi-point cutting tools to shape materials, making them suitable for complex designs, while CNC lathe machines rotate the workpiece against a stationary cutting tool, excelling in creating cylindrical and conical shapes.
Therefore, the primary distinction lies in the tool motion and the types of shapes they produce.
What factors should be considered when selecting a CNC machine type?
When selecting a CNC machine type, it is crucial to consider the material to be processed, part complexity, required accuracy, budget constraints, and industry-specific requirements.
These factors will ensure that the chosen machine meets your operational needs effectively.
Can CNC 3D printers be used for mass production?
CNC 3D printers are generally not ideal for mass production due to their slower speeds and higher costs, making them more suitable for prototyping and complex designs instead.
Still, need help? Contact Us: lk@lkprototype.com
Need a PROTOTYPE or PARTS machining quote? Quote now