Understanding the right CNC file format is crucial for precision machining. Key formats like G-code, STEP, and DXF ensure your CNC projects run smoothly and accurately. This article will guide you through these essential formats and their roles in CNC machining.
Key Takeaways
The essential CNC file formats for precision machining include G-code, STEP, and DXF, each serving unique roles in maintaining accuracy and compatibility.
Conversion of CAD files into CNC-compatible formats through CAM software is crucial for precise machining instructions and reduces the risk of errors.
Effective communication with CNC technicians and detailed preparation of CAD files are vital for successful project outcomes, ensuring designs are accurately translated into high-quality machined parts.
Essential CNC File Formats for Precision Machining
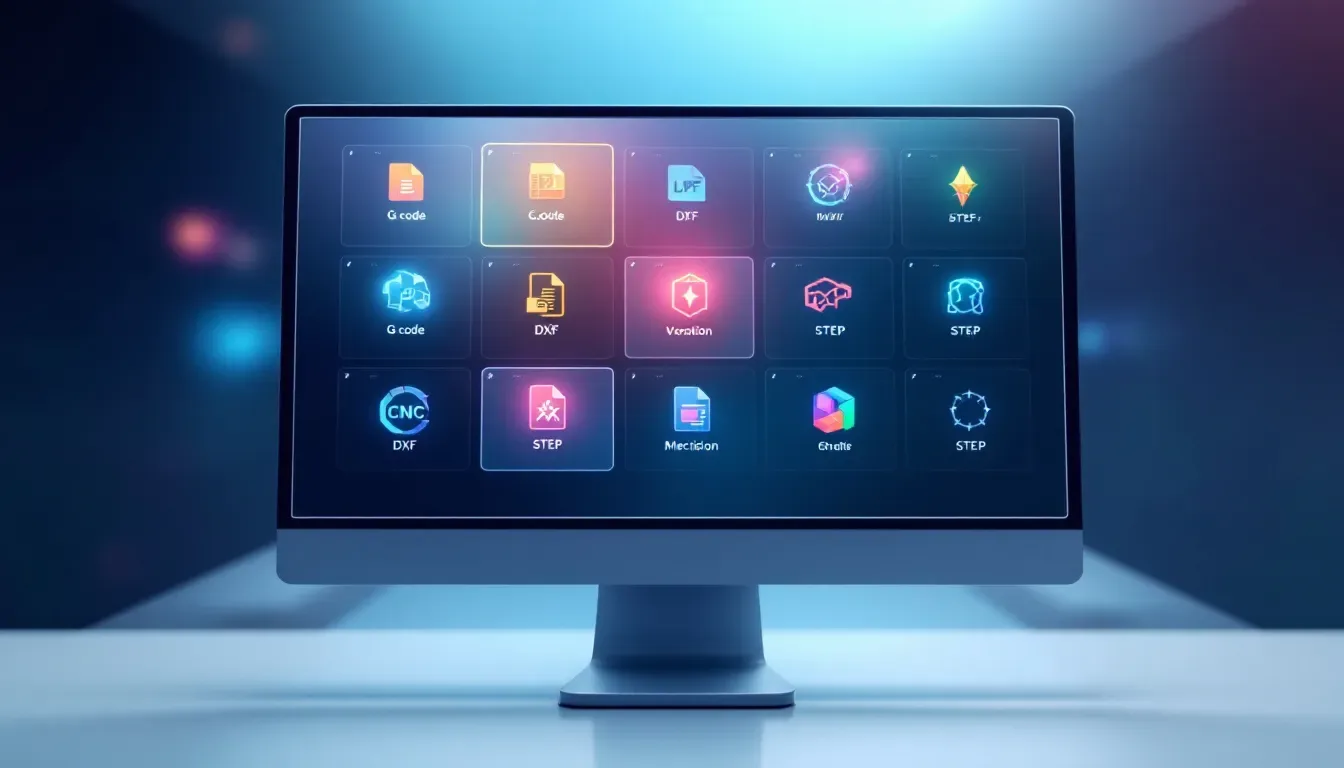
The foundation of precision in CNC machining is established by employing the appropriate file formats. These essential digital plans provide detailed instructions to CNC machines, ensuring that each action — from cutting and drilling to precise positioning — is performed with exactness. The utilization of vital CNC file formats like G-code, STEP, and DXF is integral in this meticulous process. By selecting the right file format for a given task, not only does one enhance accuracy, but also significantly reduces potential errors while transforming complex designs into superior-quality physical pieces.
Ensuring that these file formats are compatible plays a pivotal role in the success of any CNC project. When compatibility issues arise, they can cause inefficiencies during machine operation which may negatively impact the finished product’s quality. This section delves into three paramount CNC file formats: G-code, STEP and DXF. Illuminating their distinct functions as well as how they contribute to achieving perfection within precision machining tasks.
G-code Files
G-code functions as the vital file format for CNC machining, acting as the command center for automated machine tools. This file contains intricate directives governing how CNC machines move and operate to maintain precision and uniformity in production processes. It outlines everything from coordinate allocation and feed rate settings to precise pathing of cutting tools, eliminating any potential misunderstanding.
The versatility of G-code files is a significant advantage. They can be produced via specific software or crafted by hand for tailor-made programming requirements. Such adaptability provides operators with the ability to meticulously adjust the parameters of their machining operations on-the-fly. Even simple text editors have the capability to revise a g code file, allowing alterations that are both swift and straightforward when fine-tuning procedural instructions.
Imagine you’re tasked with crafting a perfectly sized circular pocket—this is where G-code proves indispensable. It prescribes every detail necessary for this undertaking: guiding tool placement across X, Y, and Z coordinates and regulating motion speed—all pivotal factors in fulfilling stringent standards demanded by CNC machining accuracy.
STEP Files
The STEP format is recognized as a global standard for the exchange of 3D model data, renowned for its wide-ranging compatibility with different CAD software. This format enables precise and efficient sharing of complex design information, maintaining fidelity to every detail during the transition from concept to production. The versatility afforded by numerous CAD software programs’ ability to export in STEP format makes it an ideal option for professionals such as designers and engineers when dealing with product data exchange.
A key attribute of the STEP format is its capacity to handle advanced features like conveying color specifications. In this context, the AP242 iteration of STEP stands out due to its extended functionality, positioning itself as the premier selection for projects that demand intricate and exact 3D models.
Such comprehensive adaptability coupled with enriched capabilities renders STEP files essential within CNC machining processes, where they serve as critical conduits for product data movement between various software applications.
DXF Files
Developed by Autodesk for CAD data exchange, DXF files are the preferred format for 2D designs within the realm of CNC machining. These files have been finely tuned to serve in applications such as laser cutting where achieving utmost accuracy in two-dimensional design is crucial. The essence of employing a DXF file lies in its smooth interoperability across diverse software platforms, which amplifies its effectiveness and versatility for assorted tasks associated with CNC machining.
Specifically in laser cutting operations, DXF files deliver the necessary exactitude ensuring that each incision aligns perfectly with intricate blueprints thus creating impeccable physical counterparts. Owing to their broad adaptability and precision, DXF files hold a fundamental role within the domain of CNC machining processes.
Understanding Other Common CAD File Formats
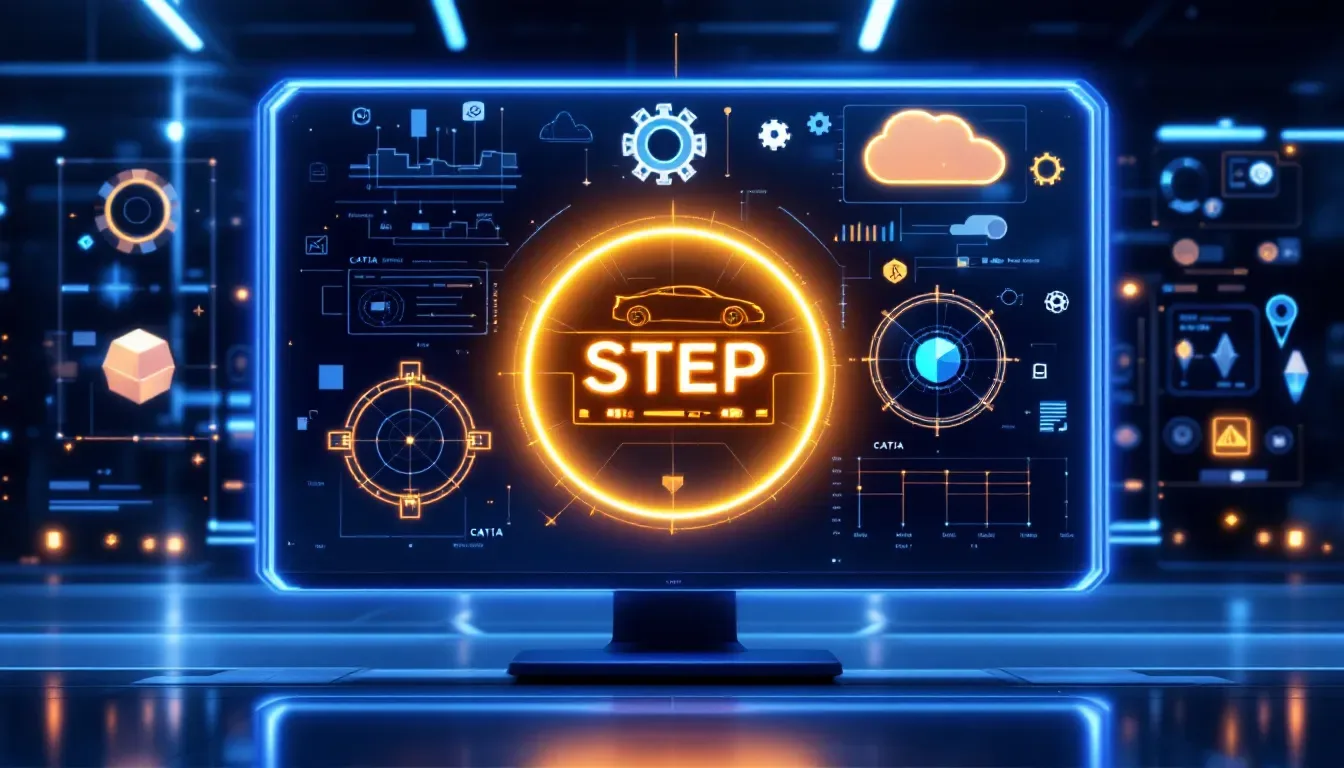
G-code, STEP, and DXF files are crucial in the CNC machining world. A range of other prevalent CAD file formats also substantially contributes to the capabilities within this field. These distinct formats each possess unique attributes and uses that enrich CAD/CAM technology as a whole. A deeper understanding of these can simplify navigation through complex CNC projects.
Take IGES format for instance. It is steeped in historical importance as an early means for exchanging CAD data. Though not as streamlined as newer formats like STEP, IGES files persist due to their comprehensive detail level and continued compatibility with legacy systems.
STL files stand out in 3D printing scenarios by capturing the external surfaces of objects but face practical limitations during application in CNC processes because they rely on triangular mesh geometry that may not be ideal for all types of machining jobs.
Formats proprietary to specific software such as SLDPRT used by SolidWorks provide advanced design features when operating within those platforms. Nevertheless, sharing designs or interacting with different software ecosystems introduces obstacles since SLDPRT stands as SolidWorks’ default file format yet might not translate well outside its native environment.
We will Explore these widely recognized CAD file formats along with how they interface with the practice of CNC machining throughout this discussion.
IGES Files
The Initial Graphics Exchange Specification, commonly known as IGES format, represented a trailblazing approach for the interchange of CAD data. Despite technological advancements, the relevance of IGES files persists owing to their capacity to encapsulate intricate details and their sustained legacy compatibility. The ability of these files to accommodate substantial information renders them valuable in conveying complex designs inherent in drawing exchange formats.
When measured against contemporary formats such as STEP, IGES files tend not to be as streamlined in operation and might fall short on compatibility stakes occasionally. Despite this comparative inefficiency, one cannot dismiss the historical importance they hold or their ongoing utility across specific sectors where they remain employed.
STL Files
STL files, an abbreviation for Stereolithography, play a crucial role in the realm of 3D printing. These files efficiently depict the exterior contours of objects through a framework composed of triangular meshes, thus they are exceptionally suitable for prototype development and expedited manufacturing processes. This specific attribute might present challenges when utilized within CNC machining contexts.
When working with STL file formats, CAM software may encounter difficulties processing their triangular mesh geometry configuration. This issue could lead to discrepancies during the actual CNC machining operations. There can be a degradation in detail and exactness upon converting designs into STL format due to simplifications made on complex surfaces.
In spite of these potential drawbacks linked with precision and interpretation by CAM systems during fabrication stages via CNC machinery tools. STL files continue to hold significance as an instrumental resource in forging models for 3D prints and crafting prototypes swiftly.
Proprietary CAD Formats
CAD software often employs proprietary formats, like the one utilized by SolidWorks, which provide specialized benefits within their own software ecosystems. These proprietary CAD formats can bolster design functionality and improve efficiency for users working within the same CAD package. Obstacles arise when there’s a need to exchange designs or use them on various platforms.
These proprietary cad formats may result in compatibility difficulties and obstruct cooperative efforts, particularly when varied iterations of CAD software come into play. Despite such hurdles, these unique CD formats maintain a crucial role in both design and manufacturing processes specific to their corresponding software environments.
Converting CAD Files for CNC Machining
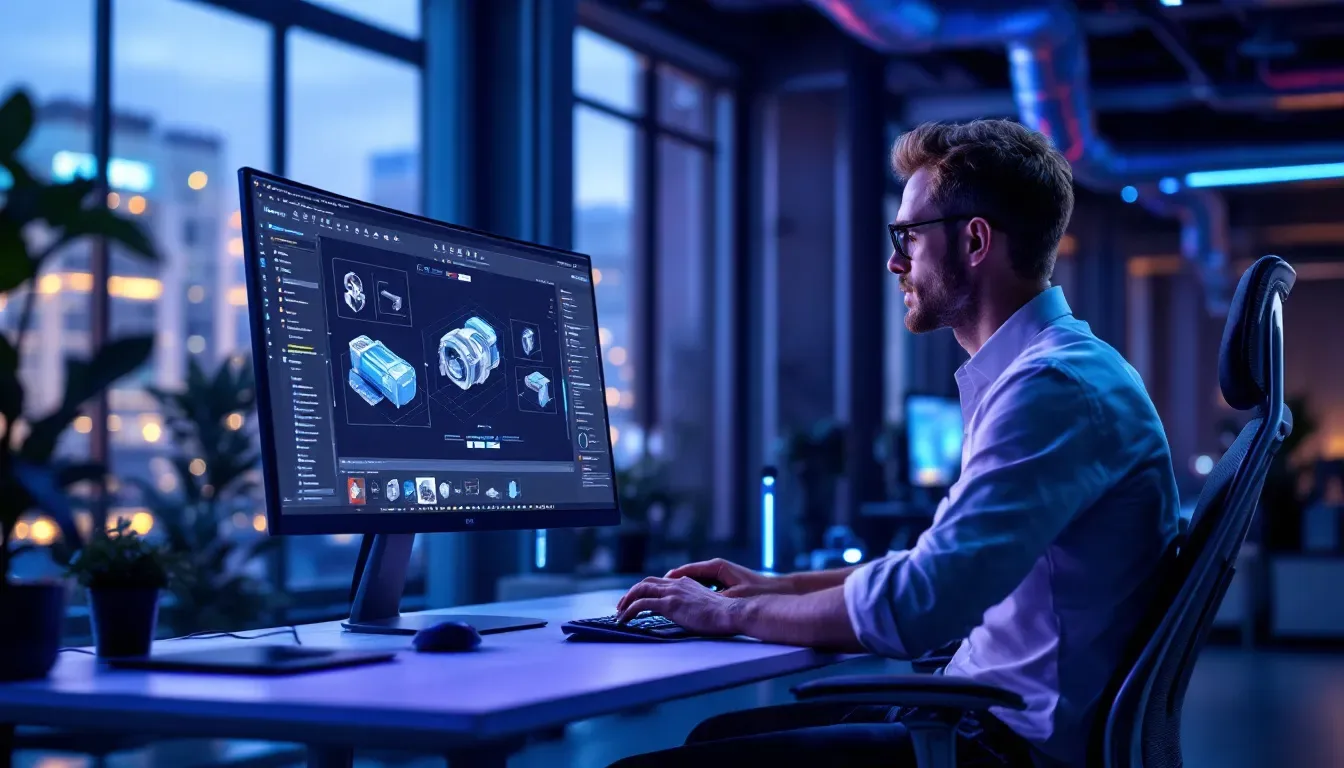
The transformation of CAD files into formats compatible with CNC machinery is an essential phase in the production workflow. These machines mandate that 3D models be transmuted into G-code to furnish exact directives for machining operations. Such a process guarantees the design’s intricacies are precisely replicated in the manufactured item.
In this context, CAM software emerges as vital by translating CAD files into G-code and optimizing the manufacturing sequence. It automates this translation, negating manual coding requirements, diminishing error probabilities, and bolstering productivity.
Grasping how CAD files undergo conversion and deploying apt CAM software is critical for efficacious CNC machining outcomes.
CAM Software Programs
CAM software serves as an essential intermediary, translating CAD designs into G-code that CNC machines can understand and execute. It facilitates this process by embedding machining parameters such as the selection of cutter types and dimensions directly into the CAD file, thus optimizing the production workflow. The precision with which CAM software carries out this task ensures that CNC machines accurately reflect design intentions during operation.
The seamless fusion of CAM software with CAD systems is pivotal for a fluid progression from conceptualization to physical creation. This integration enables immediate modifications and enhancements within the design framework, improving both effectiveness and exactitude in executing CNC projects. Choosing appropriate CAM software plays a significant role in determining the quality and triumph of your manufacturing pursuits.
Conversion Best Practices
Adhering to best practices when transforming CAD files for use in CNC machining is crucial. Implementing a consistent and clear file naming system helps avoid mix-ups, allowing for precise tracking of designs and the corresponding G-code. Opting for CAD software that supports various formats and integrates effortlessly with CAM software can significantly boost workflow productivity.
It is critical to perform diagnostic assessments on your files before initiating the machining process. These checks are vital for detecting and rectifying any errors that may be present. Simulating the CNC operation beforehand offers an additional layer of verification by uncovering potential problems before actual production commences. Delivering concise and comprehensive instructions to those operating CNC machines enhances the quality of outcomes while minimizing error margins.
Choosing the Right CAD Software for CNC Projects
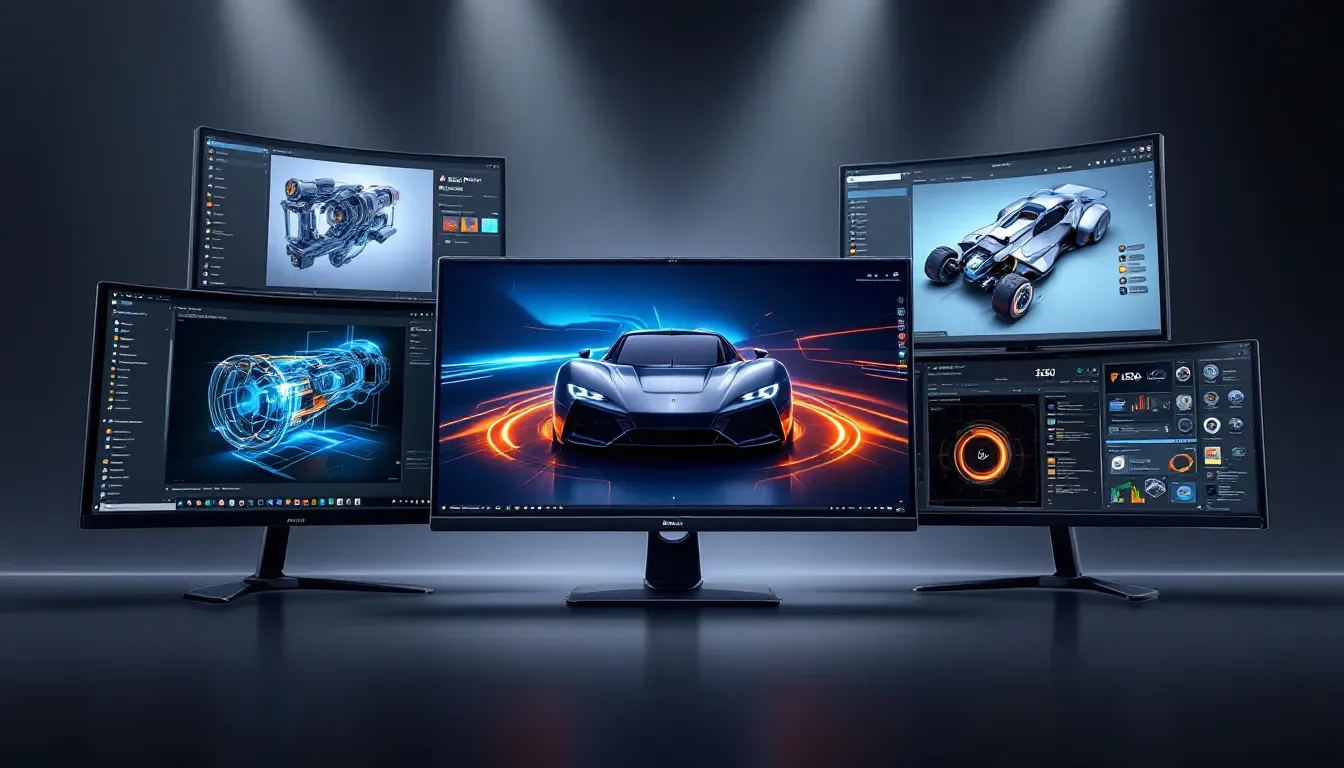
Choosing the appropriate CAD software for your CNC projects is essential and can greatly influence the outcome of your machining tasks. It’s important to evaluate characteristics like ease of use, integration potential, as well as critical features such as generating and simulating toolpaths. An intuitive interface combined with robust customer service can drastically reduce the time required to become proficient in new CAD software.
It’s vital to consider scalability and compatibility with multiple file formats when selecting CAD software. This ensures that you are prepared for future expansion while maintaining flexibility across different CNC projects. Opting for a program that supports a variety of file formats will ensure smooth interoperability during CNC machining processes.
Popular CAD Packages
Numerous CAD packages that are prevalent in the industry for CNC machining applications include AutoCAD, which is highly regarded due to its design flexibility and compatibility with various file types including DWG and DXF files commonly utilized in CNC processes. SolidWorks is another extensively employed piece of CAD software known for saving files as SLDPRT, providing advanced design functionality within its platform.
Fusion 360 has been gaining traction owing to its comprehensive 3D modeling capabilities along with support for a broad spectrum of file formats like DXF and STEP. These essential CAD packages provide the necessary tools and features required to craft accurate and intricate designs intended for CNC projects.
Evaluating Software Features
When assessing the capabilities of CAD software, it’s essential to consider how well it integrates with CAM software. This integration is key for simplifying the transition from design models to CNC machining instructions. Design solutions that incorporate built-in CAM functionality can automatically refresh G-code whenever there are updates in the model, thus directly translating design alterations into precise machining commands. Such a tight integration between CAD tools and CAM applications is fundamental for ensuring accuracy and efficiency throughout CNC machining processes.
Compatibility with a variety of file formats is crucial when selecting CAD software to ensure smooth operation within CNC manufacturing contexts. The ability to support multiple file formats enhances flexibility and ensures seamless interaction across diverse CAD systems, which also facilitates collaboration among different designers and engineers involved in a project.
Delivering Your CAD Files to a CNC Studio
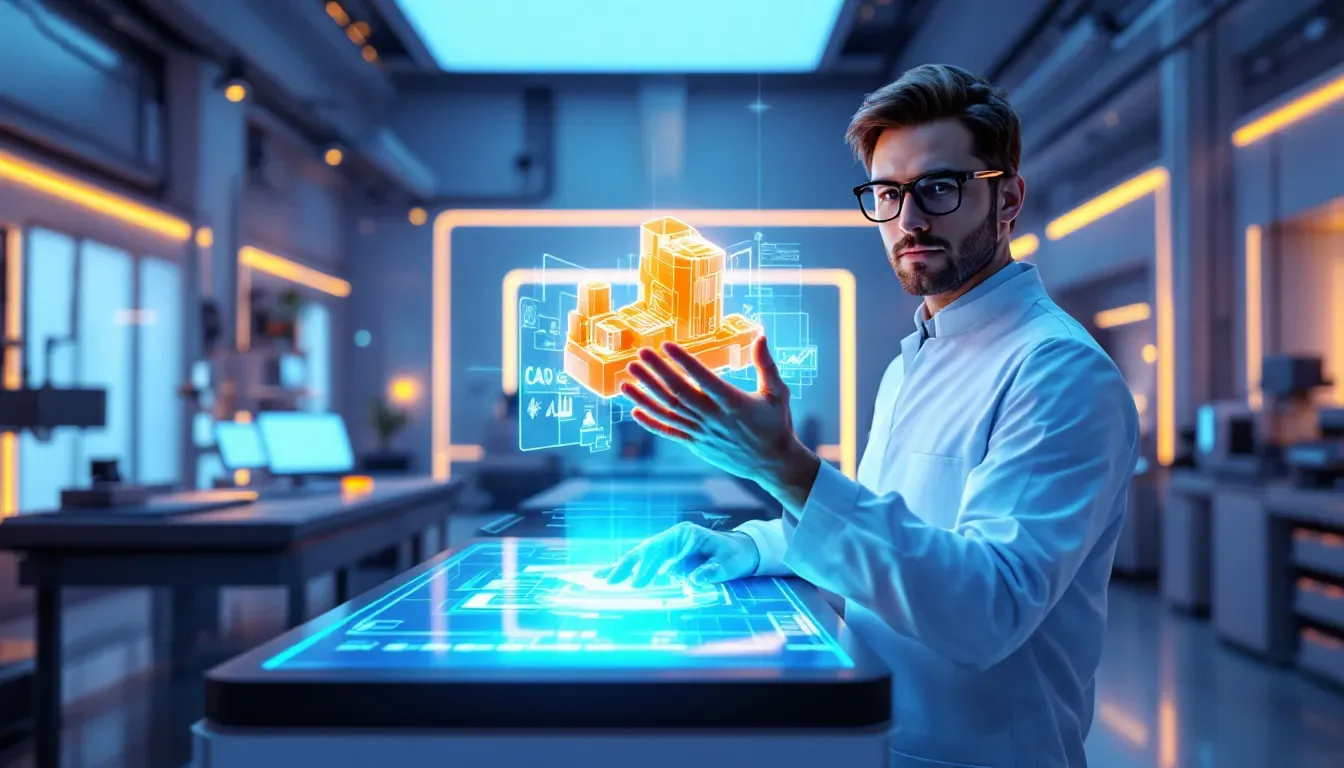
Transferring your CAD files to a CNC workshop is an essential part of the process for realizing your designs in physical form. These files are crucial for generating visual models within CNC projects, enabling swift alterations that obviate the need for tangible prototypes. To acquire an accurate quote from a CNC service provider, you must specify details such as material preferences, desired quantity, expected timeframe, and any special requirements.
When seeking a quote for your 3D project, ensure you upload your design using a compatible file format. This will facilitate receiving an estimate tailored to your needs. Be aware that supplying G-code created by yourself carries potential risks—it might not be calibrated properly for specific machinery and can often lack credibility with professionals. Effective dialogue with CNC technicians along with furnishing explicit specifications plays a key role in achieving precision-machined results.
File Preparation Tips
To get your CAD files ready for a CNC studio, you need to follow a few critical procedures. Initially, confirm that the CAD files are saved in a format that the CNC machine can read without causing errors during processing. It’s also advisable to strip away any superfluous layers from the CAD file. This streamlines the information and guarantees that only necessary details are used.
Providing a technical drawing with key measurements and tolerances alongside your file is incredibly helpful for those operating the CNC machinery. Such comprehensive plans serve as guidance on design expectations, helping to eliminate potential confusion and ensuring that the final product adheres precisely to your outlined specifications.
Communication with CNC Technicians
Ensuring successful outcomes for your machining endeavors hinges on the quality of interaction with CNC technicians. Should a client’s design be ambiguous, a seasoned CNC professional might opt to reproduce it using their proprietary software, potentially incurring an additional setup fee. Grasping the fundamental data within a technical illustration is crucial for precision in both machining and gauging.
To reduce mistakes and improve the overall machining workflow, transparent discussions regarding project specifications, especially precise tolerances or measurements, are imperative. By providing exhaustive technical details and keeping communication channels open with CNC experts, you can facilitate the precise conversion of your concept into an exceptional machined component.
Protecting and Managing CNC Design Files
It is essential to secure and organize your CNC design files to protect your intellectual property and guard against the illicit use or stealing of your unique designs. Establishing robust protection strategies for these files will contribute to their security and durability.
In this segment, we’ll delve into key backup tactics and reliable storage options that will aid in the proficient handling of your CNC design files. Adhering to these recommended practices can safeguard your precious designs, guaranteeing they remain readily available whenever necessary.
Backup Strategies
Maintaining consistent backups is crucial in safeguarding your CNC design files against unexpected deletion or damage. Opt for open format standards while storing these backups to circumvent any future issues related to software or hardware compatibility, thereby guaranteeing the continued availability and functionality of your files through changes in technology.
Incorporating frequent backup practices with a commitment to open formats reduces the danger of data disappearance and promotes enduring usability. Emphasizing routine backups coupled with the implementation of open format standards serves as an essential protective measure for your CNC design files.
Secure Storage Solutions
It’s essential to use secure digital file management systems that employ encryption and have limited access when safeguarding confidential CNC design files. The added protection of encryption shields your designs from unwelcome viewing, keeping them private. Utilizing encrypted cloud storage services also grants the advantages of increased control over who can access your files while providing the convenience of accessing them remotely.
Implementing physical security strategies is crucial for safeguarding hard copies or external drives containing CNC files. This could involve storing these items in locked cabinets or designated secure areas. By integrating both digital and physical protective measures, you ensure a comprehensive shield around your precious CNC design files, preventing unauthorized entry and potential harm.
Summary
Selecting the appropriate file format for CNC is vital to ensure meticulous and efficient outcomes in machining tasks. The role of G-code, STEP, and DXF files is indispensable as they guide CNC machines towards producing precise and uniform results. By comprehending the distinct characteristics and uses of these formats, you can pinpoint the optimal file type that aligns with your specific project requirements.
The translation process conducted by CAM software plays a pivotal role in converting CAD designs into formats digestible by CNC equipment. Adhering to conversion best practices while keeping open lines of communication with CNC professionals enhances component quality. It’s also important to safeguard your valued CNC design files against loss or damage through consistent backups and employing robust storage systems.
To sum up, gaining proficiency in the nuances of various CNC file formats along with their related procedures greatly influences the achievement rate within your machining ventures. Through applying suitable tools and methodologies, it’s possible to realize both accuracy and efficiency necessary for transforming groundbreaking concepts into tangible products.
Frequently Asked Questions
What is the best file format for CNC machining?
The best file formats for CNC machining are G-code for machine control, and STEP or DXF for 3D and 2D designs.
Select the format that aligns with your project requirements for optimal results.
How do I convert CAD files to CNC-compatible formats?
To convert CAD files to CNC-compatible formats, use CAM software to generate G-code from your CAD designs, accurately translating them into machining instructions.
This ensures compatibility with CNC machinery.
What are the challenges of using proprietary CAD formats?
Proprietary CAD formats often lead to compatibility issues that hinder external sharing and collaboration across different platforms. This can disrupt workflow and communication among team members and stakeholders.
Why is it important to back up CNC design files regularly?
It’s essential to maintain regular backups of CNC design files to avoid unintentional deletion or damage, thereby preserving the security of your work.
Using open format standards for these backups can also reduce the risk of encountering compatibility problems in the future.
How can I ensure the security of my CNC design files?
To protect the integrity of your CNC design files, employ secure digital file management systems with encryption and cloud-based storage solutions. Reinforce this digital security by using physical containment strategies such as cabinets that lock.
Adopting these methods will robustly defend your design files against illicit access.
Still, need help? Contact Us: lk@lkprototype.com
Need a PROTOTYPE or PARTS machining quote? Quote now