Looking for the top CNC equipment manufacturers? This article covers the leading companies, their specialties, and why they stand out in the industry.
Key Takeaways
CNC machines enhance precision and efficiency in manufacturing by automating processes and executing tasks directly from CAD files.
Leading CNC equipment manufacturers such as Yamazaki Mazak, Trumpf, and DMG MORI are recognized for their innovative technologies and quality machinery, catering to various industries.
Automation in CNC machining, including robotic systems and automated tool changers, significantly improves productivity and reduces manual labor, though challenges like initial investment remain.
Understanding CNC Equipment
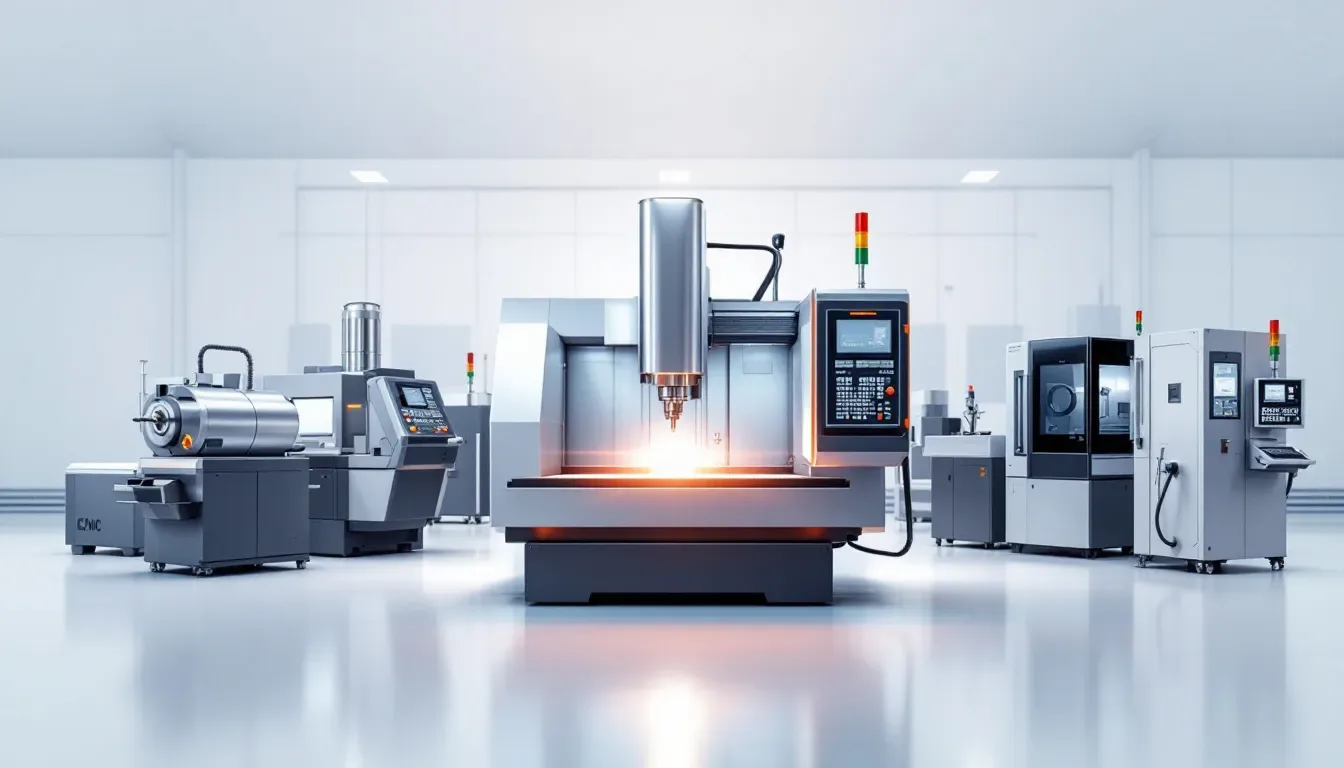
A CNC machine is a computer-controlled automatic power tool engineered to carry out various production processes with unparalleled accuracy and effectiveness. The essence of CNC machining lies in the use of programmed tools that operate straight from CAD (Computer-Aided Design) files, ensuring all operations are conducted according to exact specifications. This level of automation significantly elevates both speed and quality while improving precision, rendering CNC machines vital for contemporary manufacturing.
The procedure for programming these machines starts with crafting a digital design through CAD software. Subsequently, this design gets converted into G-Code—the primary language directing CNC machinery—which outlines the necessary cutting instructions. Software predating computers in the realm of CNC machining streamlines tasks by reducing manual involvement and upholding uniformity across productions.
CNC machining stands out due to its capacity to manage an extensive array of materials efficiently with minimal waste produced during milling, turning, drilling or cutting applications. Machines integral within this technology such as milling machines, CNC lathes, routers along with water jet cutters, plasma cutters and electric discharge machines are each tailored for distinct functions offering high precision workmanship.
These versatile pieces extend their functionality through operation on multiple axes. Typically three-axis mills and lathes are common examples showcasing their capability at producing intricate designs involving complex geometries making them particularly suitable when working on diverse materials like wood plastic or metal.
Industries such as aerospace electronics have come to rely heavily on the consistency provided by precise efficient capabilities offered by CNC equipment, which has become instrumental where consistently superior repeatable outputs remain crucial.
Leading CNC Equipment Manufacturers
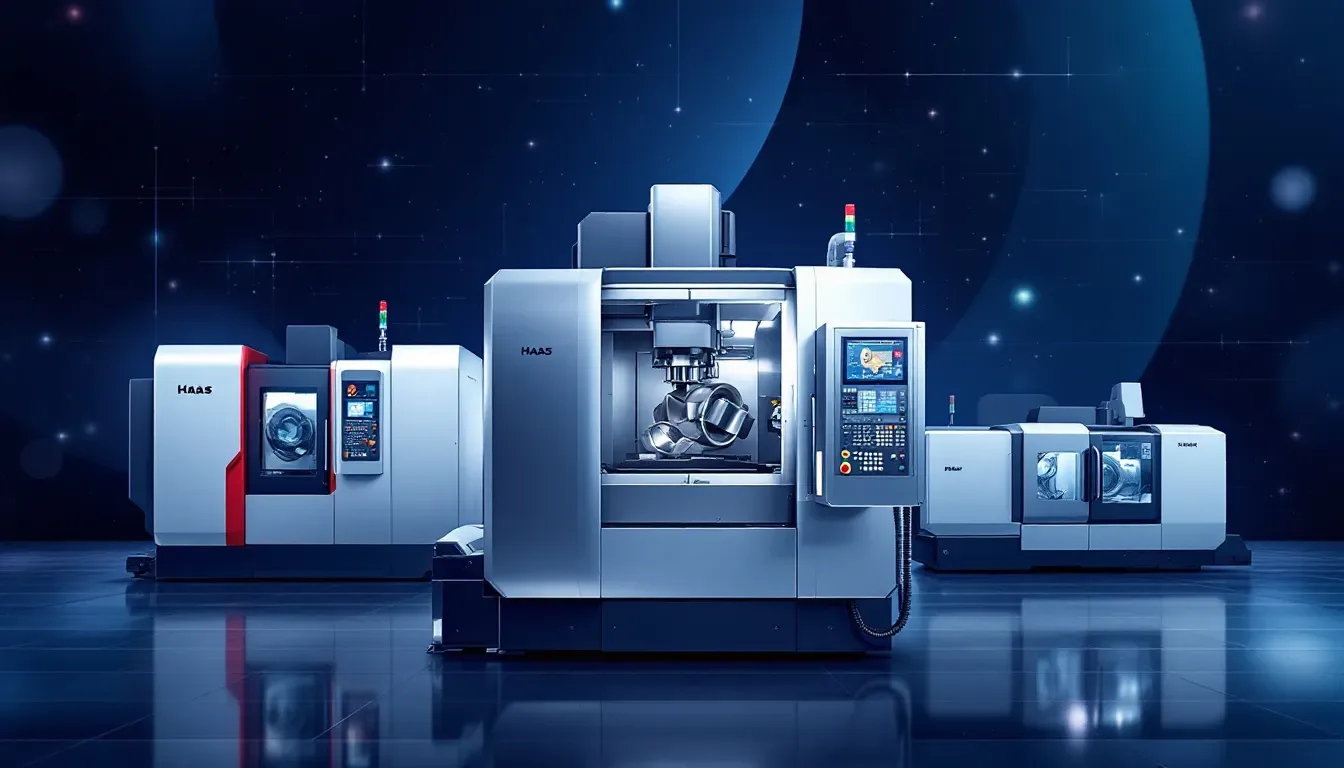
Within the bustling arena of CNC machinery, several manufacturers have risen to prominence by setting benchmarks in innovation, quality, and dependability. The global forefront of CNC equipment production is spearheaded by these notable entities.
Yamazaki Mazak
Trumpf
DMG MORI
Haas Automation
Okuma Corporation
Each enterprise boasts a storied legacy and has cultivated an esteemed reputation for superior performance.
Assessing the caliber of after-sales support and services offered by a manufacturer is crucial to ensuring enduring contentment with their products. We will now explore the distinguishing factors that separate these leading manufacturers from the rest.
Yamazaki Mazak (Japan)
Established in 1919 and operating from Oguchi, Japan, the Yamazaki Mazak Corporation has been at the forefront of the CNC machine tool industry. Throughout its history, Mazak has introduced an expansive array of CNC machining solutions that include multi-tasking machines, five-axis machining centers, CNC turning centers as well as both vertical and horizontal machining centers. These products serve a myriad of sectors including machinery manufacturing, automotive production, aerospace development, energy management, electronics fabrication and medical equipment.
Mazak’s dedication to pioneering new technologies is apparent through their ongoing creation of high-precision equipment for advanced applications. Their innovative multi-tasking machines combine several processes into one platform, which boosts efficiency while reducing preparation time needed between tasks. Meanwhile, their five-axis machining centers deliver extraordinary precision ideal for crafting intricate parts.
Globally, various industries depend on Mazak’s reliable heavy-duty construction along with cutting edge technology in their apparatuses. Expanding capabilities within CNC Machining mazac corporation continues to reinforce its leading position within this crucial sector.
Trumpf (Germany)
Trumpf stands as a leading force in the realm of global manufacturing technology, renowned for its command over industrial laser machines and sophisticated CNC machining techniques. With an emphasis on laser systems, Trumpf’s offerings are essential to precision-driven CNC processes like cutting, engraving, and modifying surfaces. The company’s industrial lasers ensure unparalleled accuracy that results in consistently precise cuts and detailed engravings on various materials.
Embedded within the heritage of German engineering prowess is Trumpf’s reputation for producing durable and dependable machinery. They provide an extensive range of lasers such as carbon dioxide, solid-state, and fiber lasers designed to meet a wide array of industrial requirements while maintaining their position at the cutting edge of technological advancements.
DMG MORI (Germany + Japan)
DMG MORI represents a powerful fusion arising from the strategic partnership between Germany’s Demag, boasting 143 years of engineering excellence, and Mori Seiki from Japan, renowned for their 65-year legacy in machine tools. This alliance marries German technical prowess with Japanese meticulousness to dominate the CNC machinery market. Offering cutting-edge solutions across a variety of manufacturing requirements, DMG MORI is especially noted for its high-caliber milling machines that cater to sectors such as aerospace and automotive.
Possessing over three decades of expertise in laser processing technology, DMG MORI caters to international corporations and stands out for its precise machine tools—positioning it firmly within the upper echelons of sophisticated manufacturing circles. The company’s portfolio features demagesen precision machine tools celebrated for their dependability and state-of-the-art functions.
By drawing on the core strengths inherent in both Demag and Mori Seiki heritage, DMG MORI propels forward CNC machining innovation to satisfy the rigorous production demands present within contemporary industry landscapes.
Haas Automation (USA)
Founded by Gene Haas in 1983 and headquartered in Oxnard, California, Haas Automation has expanded to become a leading CNC machine tool manufacturer within the United States. The company’s extensive product line includes an array of CNC machinery such as vertical and horizontal machining centers, CNC lathes, rotary tables, 5-axis machining centers for complex shapes, mold-making machines, and specialized toolroom lathes.
Haas is recognized for producing highly reliable and precise CNC machine tools that cater to diverse industries requiring turning capabilities and tasks necessitating high precision. Illustrating their substantial output capabilities, in 2006 alone saw over 12,500 units from their range being manufactured.
With a dedicated focus on quality enhancement as well as technological advancement throughout its operation history, which spans decades now. This esteemed player within the sphere serves up solutions known both for efficiency and accuracy thus meeting various manufacturing needs effectively across numerous applications found today’s marketplace demand spectrum wide indeed!
Okuma Corporation (Japan)
Established in 1898 with its headquarters situated in Oguchi, Aichi Prefecture, Japan, Okuma Corporation stands as one of the most venerable and respected producers within the CNC sector. The company focuses on fabricating CNC lathes and multi-tasking machines while prioritizing accuracy and productivity across their entire product range.
Reaching a significant landmark in 1937, Okuma was distinguished as the premier entity in Japan to achieve an unparalleled output value for machine tool products. Their enduring legacy coupled with continuous advancements have positioned them as a dominant force within the worldwide market for CNC machinery, catering to diverse sectors by offering dependable and high-caliber machines.
Specialized CNC Machine Tools
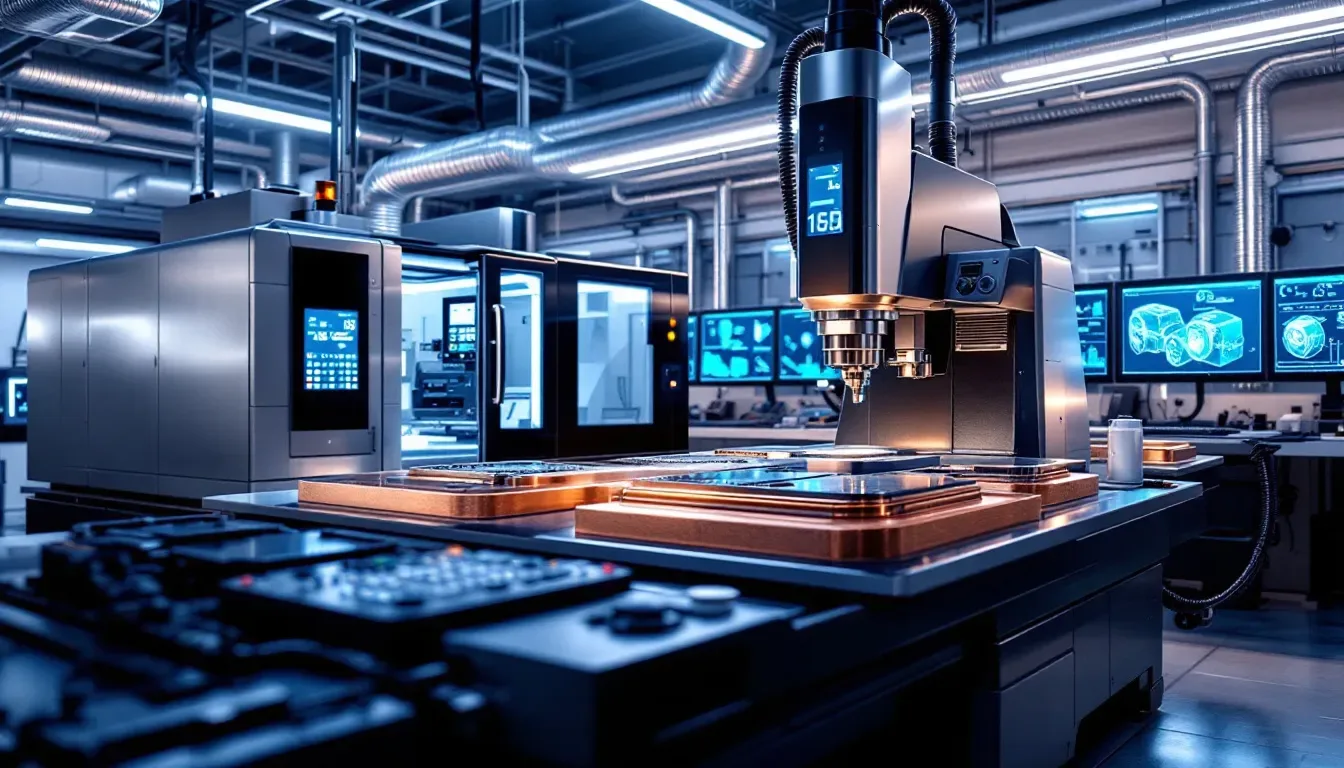
CNC equipment is specialized for various manufacturing tasks rather than being universally applicable. This range of tools includes specific types such as CNC lathes, milling machines, and routers, each with their own set of applications and benefits.
We should delve into the unique machine tools that have revolutionized contemporary production processes.
CNC Lathes
CNC lathes play an essential role in the precision machining of cylindrical components within contemporary manufacturing, offering versatility for a range of applications and facilitating turning operations. Brands like Okuma provide an array of equipment, including CNC lathes, vertical and horizontal machining centers, turning centers, gantry machines, as well as CNC grinders.
Okuma extends its machinery offerings to include multitasking machines that integrate both milling and turning functions. This combination enhances manufacturing efficiency and precision by allowing smooth transitions between various operations. The indispensability of CNC lathes is particularly evident in sectors where high accuracy and operational efficiency are paramount.
CNC Milling Machines
CNC milling machines are indispensable in contemporary manufacturing, facilitating the creation of parts with intricate geometries and precise specifications. These machines employ computer numerical control to direct a range of cutting tools for exact machining processes. Industries such as aerospace, automotive, and medical heavily rely on CNC milling for fabricating complex components.
These advanced machines are renowned for their ability to adhere to stringent tolerances and craft fine details, positioning them as perfect candidates for tasks demanding high precision. Their adaptability also proves beneficial in prototype development and the production of limited quantities due to their competence in processing diverse materials and configurations.
With functionalities encompassing drilling, slicing, and forming materials among others, milling machines serve as an invaluable asset within sectors necessitating meticulous precision alongside sophisticated machining capabilities.
CNC Routers
CNC router machines are extensively utilized in the woodworking industry for producing complex designs and patterns. These machines vary from 3-axis to 6-axis, each offering incremental advancements in complexity and detail accuracy. While a 3-axis CNC router cuts across three dimensions, adding an axis with a 4-axis machine allows for more advanced rotations along different planes.
Machines equipped with high-speed, 3-axis motion controllers are often recognized as the most adaptable when it comes to performance. In contrast, CNC routers that operate on four or five axes introduce additional spindle movements across multiple planes. This capability advances their machining potential and enables them to craft precise three-dimensional components.
In scenarios demanding higher productivity levels, the CNC Multi-Head Router is designed to run several spindles at once, thereby markedly enhancing output rates. Such routers incorporate built-in control over these spindles supporting concurrent operations of between two and eight spindles while featuring automatic transitioning capabilities which contribute to operational efficiency by minimizing idle times.
Advanced CNC Technologies
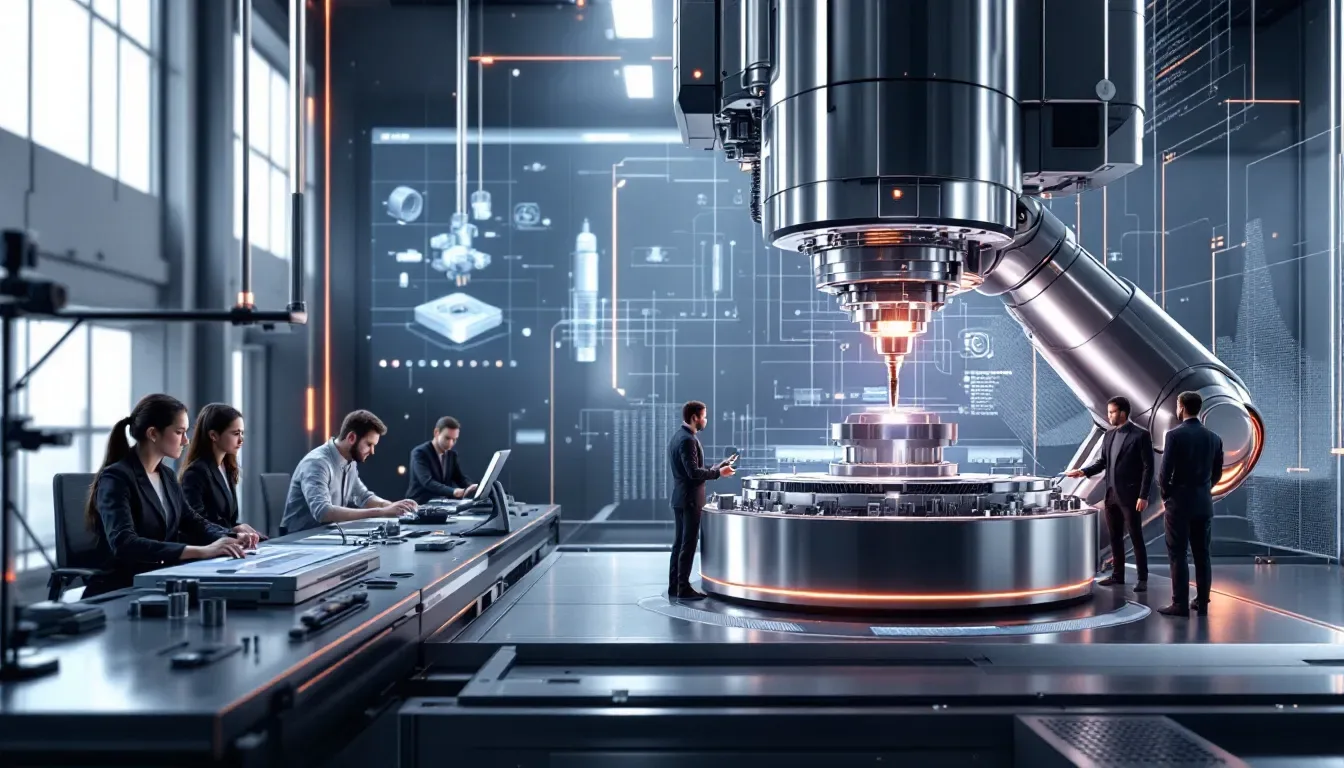
The field of CNC machining is in a constant state of advancement, as emerging technologies expand the limits of what can be achieved. Incorporating techniques from additive manufacturing and harnessing laser processing along with ultrasonic machining are at the forefront, improving accuracy, productivity, and adaptability in production processes.
We should explore these progressive technologies within CNC machining further.
Additive Manufacturing
Additive manufacturing, often referred to as 3D printing, marks a transformative evolution from the conventional CNC machining approach. This method diverges from traditional subtractive techniques that carve out material, by constructing parts through a layer-by-layer addition process which enhances design versatility and conserves materials more effectively. As such, CNC manufacturers are beginning to incorporate these additive strategies alongside time-honored methods for fabricating structures with intricate geometries while also minimizing excess material use.
This fusion of additive manufacturing within the realm of CNC machining paves the way for crafting elaborate shapes that were once challenging or even unattainable. The synergy between these processes augments overall production agility, enabling the creation of complex components characterized by high precision and reduced waste—a revolutionary advancement in today’s manufacturing landscape.
Laser Processing
Technologies related to laser processing are crucial for CNC machining, as they provide the capability to execute high-precision tasks like cutting, engraving, and modifying surfaces. The accuracy and adaptability offered by industrial laser machines from manufacturers such as Trumpf have made them indispensable for jobs demanding precision.
Within its assortment of laser offerings, Trumpf features different types including carbon dioxide lasers, solid-state lasers, and fiber lasers tailored to meet particular industry requirements. These devices significantly augment CNC machining processes through their ability to perform highly precise cuts. This allows producers the flexibility to handle various materials with both exactitude and productivity.
Ultrasonic Machining
Ultrasonic machining excels in sculpting challenging materials such as ceramics and glass due to its use of high-frequency oscillations, which accurately excise material. This advanced technology is perfect for tasks that necessitate complex and precise incisions.
Utilizing ultrasonic machining enables producers to attain exceptional accuracy and refined finishes on substrates that typically resist conventional CNC techniques. Such a technique is exceedingly beneficial within sectors where exactitude and preservation of the material’s inherent quality are crucial, including aerospace and medical technology industries.
Automation in CNC Machining
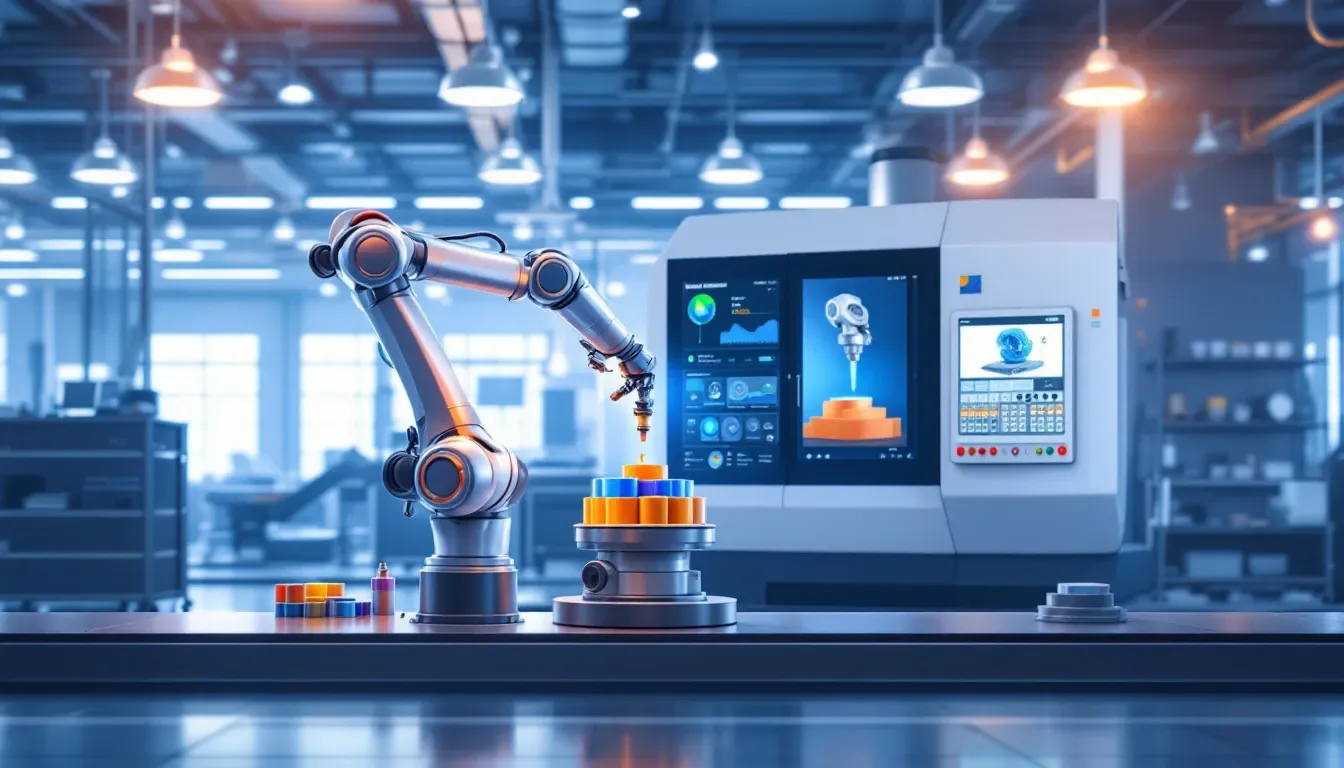
The CNC machining realm is undergoing a revolution thanks to automation, which boosts efficiency, diminishes the need for manual input, and accelerates production rates. The incorporation of cutting-edge technologies and robotics into CNC machines facilitates their operation with scant human oversight, thereby improving accuracy while lowering the expense associated with manufacturing.
We should delve into the principal elements that underscore the significance of automation within the context of CNC machining.
Automated Tool Changing
Automated systems for changing tools are transforming the landscape of CNC machining, significantly diminishing the downtime throughout production runs. By slashing tool change time by as much as 80%, these innovative systems enable machines to maintain more continuous operation with fewer stops.
Incorporating automated tool changers bolsters productivity by permitting CNC machines to carry out tasks without breaks, thus liberating operators to focus on other essential responsibilities. The smooth interchange between tools afforded by these systems amplifies efficiency and versatility in handling a variety of manufacturing operations.
Process Integration
Incorporating process integration within the realm of CNC machining ensures a coherent workflow, reducing the potential for holdups and inaccuracies. This approach interlinks different stages of manufacturing, fostering better communication and information transfer throughout the production sequence, which in turn elevates the uniformity in quality output.
By taking an integrated stance on processes during CNC operations, efficiency is markedly enhanced as every production phase is refined to maximize both velocity and precision. Adopting this comprehensive perspective on fabrication not only augments productivity but also diminishes error rates, leading to end products that are distinguished by their superior quality and dependability.
Robotic Automation
The introduction of robotic automation in CNC machine shops enables round-the-clock operation with scarce interruptions, thereby substantially boosting output. Robots are proficient at managing operations like the loading and unloading of materials, which optimizes the workflow associated with CNC machines and diminishes the requirement for manual intervention.
Incorporating robotic systems can lead to a decrease in labor expenses and an increase in precision within manufacturing processes. Nevertheless, obstacles such as substantial upfront costs for investment and the necessity for specialized training might impede the adoption of automated solutions.
Despite these impediments, it’s clear that robotic automation contributes significant advantages to CNC machining by enhancing operational efficiency and equipping businesses with improved capacity to adapt to market needs swiftly.
Choosing the Right CNC Equipment Manufacturer
Choosing an appropriate manufacturer of CNC equipment is essential to guarantee high standards of quality, dependability, and productivity in your production operations. Important aspects to consider are the experience level of the manufacturer, their track record for reliability, the proficiency possessed by their workforce, and the caliber of materials they employ.
It’s important that we delve into what factors ought to be given precedence while selecting a manufacturer for CNC equipment.
Quality and Reliability
When choosing a manufacturer for CNC equipment, the importance of both quality and reliability cannot be overstressed because these attributes are essential for ensuring that components last and machines are sturdy. Companies that possess certifications like AS9001 and ISO 9001 demonstrate their dedication to upholding stringent quality benchmarks.
In assessing a company specializing in CNC machining, it is crucial to place greater emphasis on qualities such as dependability, service excellence, and overall machine quality rather than simply focusing on cost. Machines of superior caliber guarantee extended operational life and diminish the chances of mechanical failures, thereby bolstering productivity levels and optimizing efficiency across operations.
Customer Support and Services
When selecting a manufacturer for CNC equipment, the quality of customer support and services is paramount. Manufacturers commonly provide an array of manufacturing services that encompass prototyping, finishing processes, assembly, as well as extensive support across the entire product lifecycle.
In assessing potential manufacturers, it’s essential to take into account their provision of documentation, training opportunities, technical assistance, and accessibility to spare parts. The presence of a strong support infrastructure is crucial to swiftly address problems when they arise in order to reduce machine downtime and sustain high levels of production efficiency.
Scalability and Customization
When choosing a CNC machining company, it is important to consider the scalability and customization capabilities. A company must be capable of adjusting its operations to handle orders of varying sizes while also being able to accommodate unique design requirements, which is vital for catering to different manufacturing necessities.
Enhancing CNC machines with customization features can significantly improve their utility for particular tasks. The combination of scalable services, tailor-made solutions, and robustness guarantees that these machines are equipped to confront the rigorous requirements of contemporary production processes.
Summary
In summary, the advent of CNC machines has been a game-changer for contemporary manufacturing processes, providing unmatched levels of accuracy, efficiency and adaptability. Industry front-runners such as Yamazaki Mazak, Trumpf, DMG MORI, Haas Automation and Okuma Corporation are at the forefront due to their pioneering technologies and superior quality machinery.
When it comes down to selecting an appropriate manufacturer for CNC equipment, various aspects should be taken into account including machine quality, dependability of operation, level of customer service provided by the company, as well as capacity for scaling up operations and tailoring them to specific requirements. By giving precedence to these considerations when choosing a provider, manufacturers are better equipped in securing top-of-the-line CNC machinery that will elevate productivity and spur innovation within their respective fields.
Frequently Asked Questions
Who is the largest manufacturer of CNC machines?
Yamazaki Mazak is the largest manufacturer of CNC machines globally, consistently leading the industry since its founding in 1919.
Its prominence is particularly noted in Japan as well.
What are the key benefits of CNC machining?
CNC machining offers critical advantages including heightened accuracy and efficiency. It also minimizes excess material use and supports process automation.
As a result, this technology is extremely valuable across multiple manufacturing scenarios.
Who are the top CNC equipment manufacturers?
The top CNC equipment manufacturers are Yamazaki Mazak, Trumpf, DMG MORI, Haas Automation, and Okuma Corporation. These companies are recognized for their advanced technology and quality in the CNC industry.
What types of CNC machines are available?
CNC machines are primarily categorized into milling machines, lathes, routers, water jet cutters, plasma cutters, and electric discharge machines.
Each type serves specific manufacturing needs and applications.
How does automation enhance CNC machining?
Automation in CNC machining significantly enhances efficiency by reducing manual labor, increasing production speed, and improving precision, ultimately resulting in lower production costs.
Still, need help? Contact Us: lk@lkprototype.com
Need a PROTOTYPE or PARTS machining quote? Quote now