Acrylic CNC machining uses computer-controlled devices to accurately cut and shape acrylic materials. It provides precision, reduces material waste, and speeds up production compared to manual methods. In this article, you’ll learn about the advantages, key properties, and best practices for achieving high-quality results in acrylic CNC machining.
Key Takeaways
CNC machining offers high precision and speed for acrylic, significantly reducing material waste and production costs, making it an efficient manufacturing method.
Key properties of acrylic, including its transparency, impact resistance, and lightweight nature, contribute to its widespread use in industries such as automotive, medical, and construction.
Implementing best practices in CNC machining, such as using appropriate tools and managing feed rates, is essential to prevent issues like stress cracking and ensure high-quality finished acrylic components.
Advantages of CNC Machining Acrylic
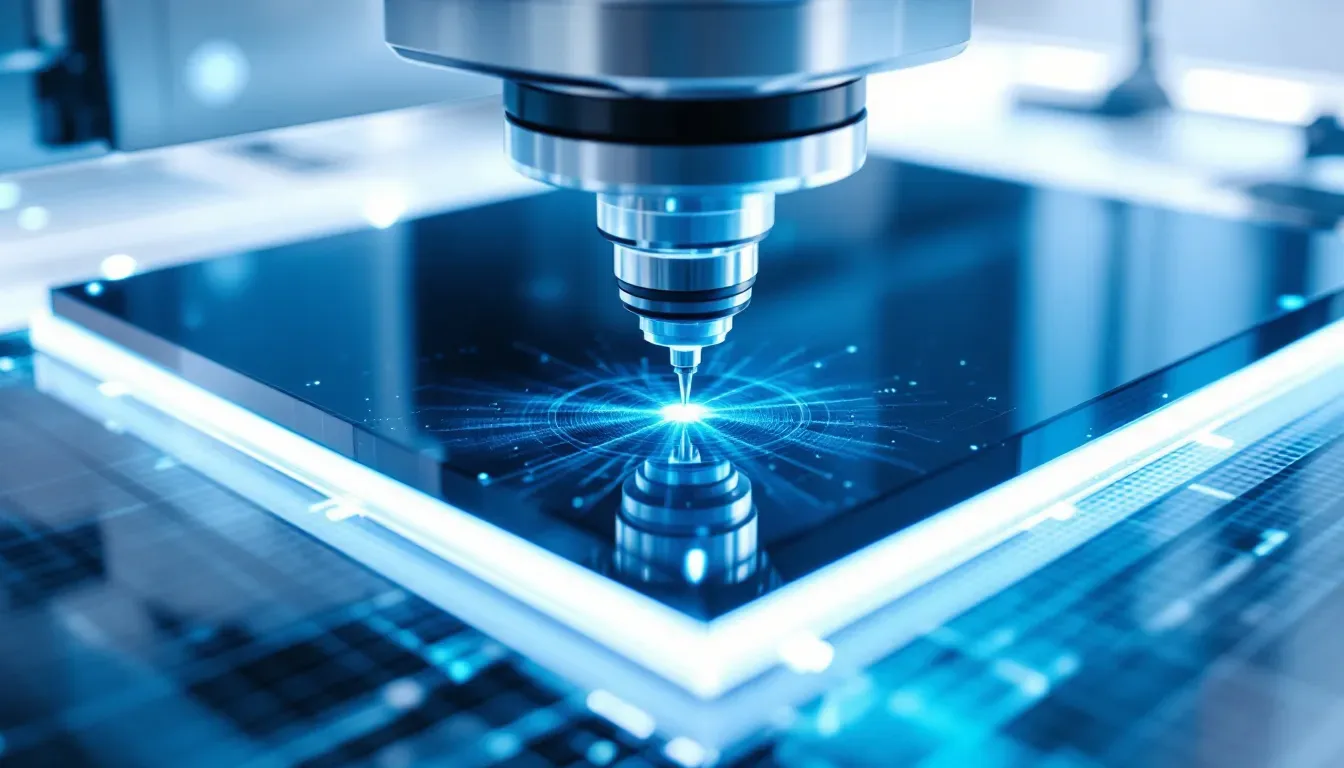
CNC machining excels in the precision cutting of acrylic, delivering accurate and precise clean edges along with exacting dimensions that are vital for applications demanding strict tolerances and complex patterns. The process improves production velocity significantly when compared to traditional manual techniques, thus showcasing CNC acrylic machining’s enhanced benefits.
The efficiency of CNC machinery aids in reducing material waste by limiting excess off-cuts and scrap materials. This reduction contributes to both cost savings as well as a more environmentally friendly manufacturing approach. Consequently, this makes CNC technology an economically advantageous choice for fabricating superior-quality acrylic components swiftly while keeping wastage at a minimum.
Precision and Accuracy
CNC machining boasts outstanding accuracy, with the capability of cutting to tolerances as tight as a few thousandths of an inch. This level of precision ensures that components fit perfectly in their designated uses. The sophisticated multi-point tools utilized in CNC milling and CNC cutting machines facilitate the creation of complex designs characterized by excellent optical clarity and clean-cut edges, which are enhanced through the use of advanced CNC mills and precise manufacturing techniques.
The high-speed execution coupled with precision during CNC machining processes guarantees exactness when performing detailed engraving on acrylic materials. By adopting correct cutting directions along with keen-edged tools, one can achieve razor-sharp shapes that maintain accurate dimensions without any jagged edges—thereby preserving the inherent optical clarity of acrylic materials.
Efficiency and Speed
The utilization of CNC machining for acrylic streamlines the manufacturing process, outpacing conventional manual techniques. This acceleration in production not only slashes the time required to meet demands, but also adeptly manages substantial orders within stringent deadlines.
By rapidly fabricating high-quality acrylic parts, productivity is heightened while maintaining excellence. The efficiency stems from meticulous cutting designs inherent in CNC machining that curtail excess and decrease the amount of discarded material, effectively minimizing waste.
Material Waste Reduction
CNC machining employs meticulous cutting patterns that lead to minimal excess material and scrap, rendering the process both eco-friendly and economical. By optimizing how material is utilized, it enables the creation of precise acrylic components with reduced waste, offering environmental advantages as well as considerable cost reductions for manufacturers.
The process utilizes an optimal level of force during cutting, which prevents damage to the material and bolsters precision. This efficient use of materials eliminates superfluous melting and augments the quality of the end product.
Cost-Effectiveness
CNC machining streamlines the manufacturing process by cutting down on waste and boosting production velocity, which results in considerable savings, reduced labor expenses, and faster completion times through improved management of materials and schedules.
Such cost reductions render CNC machining a highly appealing choice for companies that seek to economically manufacture top-notch acrylic components. The precise incisions made during the process lead to minimal material loss, amplifying the economical advantages offered by CNC machining when working with acrylic.
Key Properties of Acrylic Material
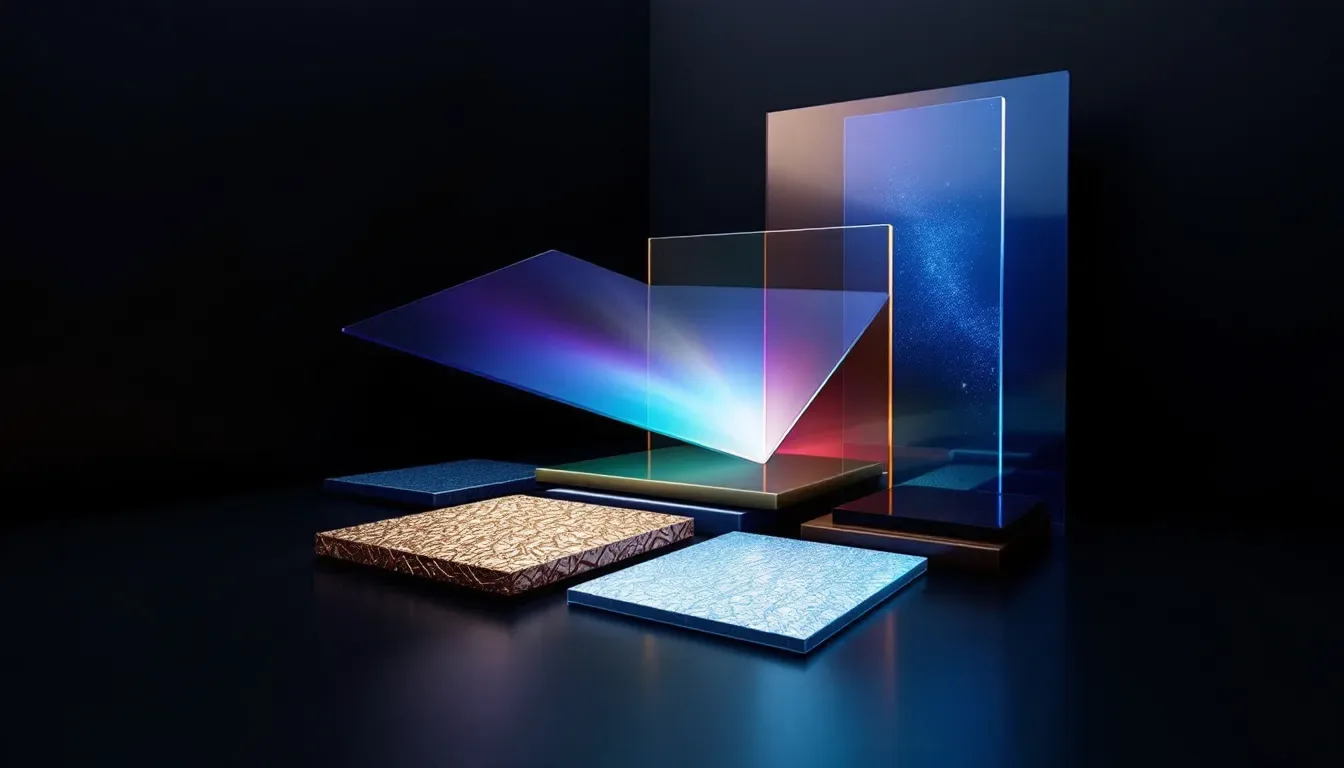
Polymethyl methacrylate, commonly known as acrylic or PMMA, is a thermoplastic that softens under heat, which greatly facilitates its processing through CNC machining.
Its popularity stems from characteristics such as:
Clear visibility
Sturdiness
Durability
Resistance to impacts
Thanks to these features, it’s an excellent substitute for glass in numerous uses due to being both lighter and stronger—qualities that enhance performance in various industries.
CNC machined acrylic components are extensively utilized across fields like the automotive industry, healthcare sector, and signage businesses because of their adaptability coupled with outstanding optical transparency. These parts stand out for being transparent and durable while remaining light. The precision and high quality of CNC acrylic parts are particularly prized within these markets.
Transparency and Optical Clarity
Acrylic outshines polycarbonate in terms of optical clarity, thus it’s superb for uses where high transparency is crucial. It boasts a refractive index of 1.49 and can transmit up to 92% of visible light, making it an exceptional choice for crafting light tubes, lenses, and display cases.
The precision with which CNC machining crafts acrylic components contributes significantly to their optical purity by ensuring shapes are exact and edges are pristine. This level of detail ensures that the resulting products are both aesthetically pleasing and practical for diverse applications ranging from complex designs to straightforward lighting fixtures.
Durability and Impact Resistance
Acrylic boasts an impressive level of impact resistance, exceeding that of glass by more than a factor of ten. This renders it incredibly durable and functional for myriad uses. Upon experiencing forceful contact, acrylic tends to break into sizable chunks with blunt edges, which helps minimize the chance of injury. Its inherent strength equips acrylic to endure a wide range of pressures and impacts.
The outstanding toughness and durability found in acrylic sheets position them as prime choices for scenarios requiring strong materials that last over time. These sheets preserve their exceptional optical clarity while resisting damage from UV light and adverse weather conditions, thereby proving especially advantageous for outdoor use or under demanding circumstances.
Lightweight Nature
Acrylic possesses a much lower weight compared to glass, which simplifies the process of handling and setting it up. Due to its lightness, not only does installation become faster, but also there is a decrease in associated labor expenses.
Such an advantage proves particularly valuable in scenarios where managing and moving materials with ease are key factors, including sectors like construction and the automotive industry.
CNC Machining Processes for Acrylic
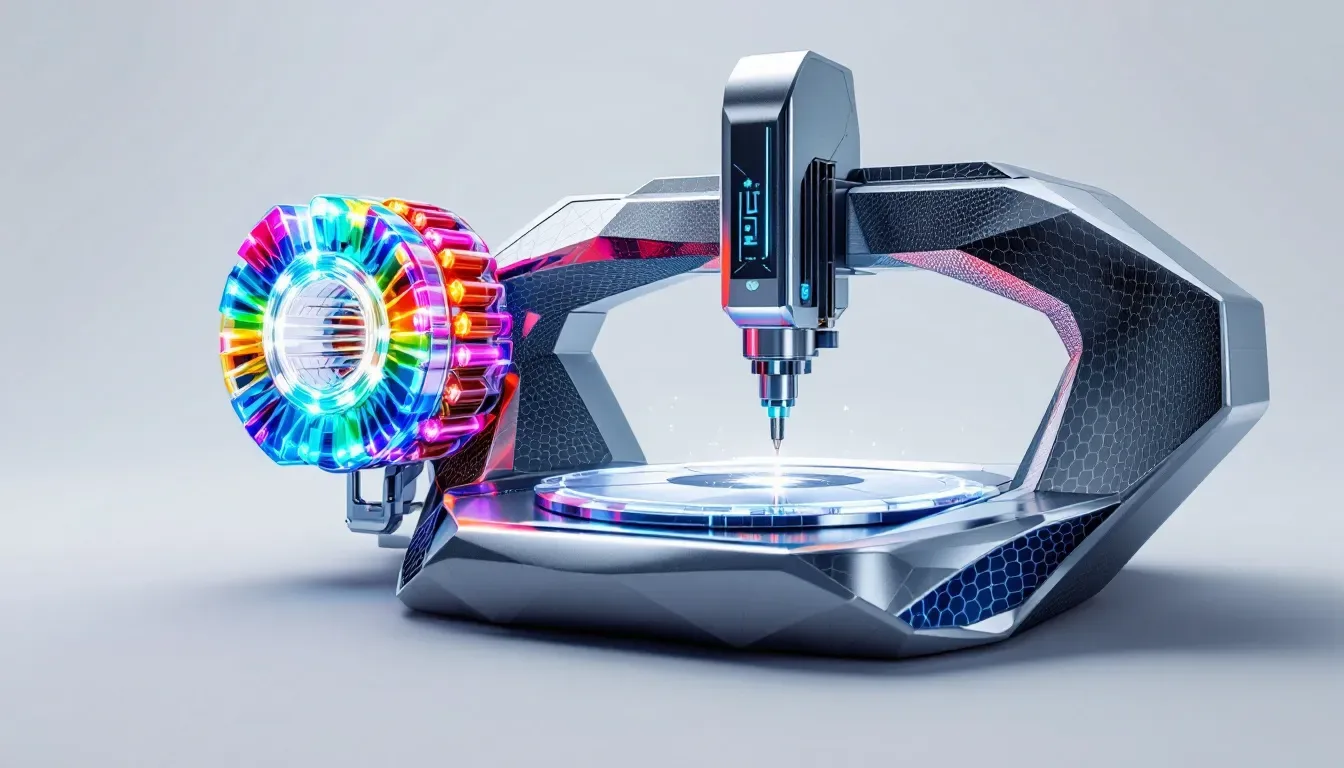
CNC machining excels at producing complex parts with a refined finish and exceptional accuracy, which is particularly suitable for the creation of acrylic components. Depending on the requirements specified by clients, various techniques like milling, turning, and engraving are employed. The flexibility of acrylic makes it conducive to effortless shaping and molding when subjected to machining processes while maintaining careful application of force to circumvent any potential damage.
It’s essential to utilize sharp and sturdy cutting tools when CNC machining acrylic in order to avoid melting the material and enhance the quality of cuts. Subsequent sections will elaborate on CNC milling, turning, and engraving procedures, shedding light on their distinct methodologies as well as advantages they offer.
CNC Milling Acrylic
Through the process of CNC milling, material is systematically carved away from an acrylic sheet by spinning cutting implements. This can encompass a range of cuts such as superficial or profound incisions, and circumferential trimming. In this method, the direction in which the machine propels the sheet aligns with that of the rotating apparatus to facilitate refined and exact slicing.
To attain a requisite level of transparency in parts crafted from CNC machined acrylic, it might be essential to carry out additional polishing post-machining. This step guarantees that not only do these components comply with precise dimensional specifications but also exhibit an attractive glossiness upon completion.
CNC Turning Acrylic
A single revolving cutting instrument is employed in CNC turning to precisely carve material from a spinning acrylic workpiece, resulting in cylindrical shapes.
The process is advantageous for producing rounded or tubular components out of acrylic, ensuring uniformity and precision in the finished products.
CNC Engraving Acrylic
CNC engraving meticulously etches elaborate designs onto acrylic surfaces, resulting in accurate and sharp details perfect for personalized creations and branding purposes. The process involves rapid cutting that ensures the engravings are both neat and precise.
Employing durable, finely honed tools, CNC engraving accomplishes a high level of detail while maintaining the strength of the acrylic material. This technique is utilized for crafting decorative objects, signs, and various items where intricate engraved embellishments are essential to improve aesthetic attractiveness.
Best Practices for CNC Machining Acrylic
Utilizing appropriate instruments and methods tailored for acrylic is crucial to minimize machining mishaps and improve the final product’s quality. Establishing ideal feed rates is essential in preventing material from melting or shattering, which ensures smooth cutting edges. The use of vacuum tables or soft jaws, along with proper fixturing, helps keep the workpiece steady and aligned during processing for accurate cuts.
Adhering to these recommended practices can diminish difficulties and enhance results when CNC machining acrylic materials. Subsequent sections offer comprehensive instructions on choosing suitable cutters, determining optimal feed rates, and carefully controlling cutting depth to achieve superior outcomes.
Selecting the Right Cutter
Employing premium, keen-edged tools tailored for machined acrylic improves precision and diminishes the likelihood of chipping. It’s essential to choose appropriate cutters that will lead to optimal outcomes by considerably minimizing stress cracking potential, which in turn preserves the quality and structural soundness of the end product.
The selection process for the right cutter should take into account both edge rake angles as well as cutting depth to ensure precise cuts with clean edges. Utilization of carbide tools along with other fitting cutting instruments elevates the caliber of acrylic parts produced, streamlining and enhancing effectiveness throughout manufacturing operations.
Setting Optimal Feed Rates
Setting the correct feed rates balances speed and cutting pressure to prevent workpiece breakage during CNC machining of acrylic. Proper spindle speeds and feed rates prevent overheating and manage heat generation.
Incorporating cooling methods like air or coolants helps avoid overheating, vital for effective CNC machining of acrylic. Adjusting cutting speed and feed rate controls heat and prevents acrylic melting.
Monitoring Cutting Depth
It is crucial to carefully control the cutting depth during CNC machining of acrylic in order to attain the correct dimensions while avoiding damage such as chipping or cracking. It’s important for operators to frequently verify and adjust the tool’s positioning, along with calibrating machine settings before initiating any cuts.
Maintaining an accurate cutting depth not only improves the quality of the final product, but also prolongs the lifespan of your tools. By vigilantly overseeing and modifying the cutting depth when necessary, individuals operating CNC machines can guarantee uniform, superior-quality outcomes when machining acrylic.
Applications of CNC Machined Acrylic Parts
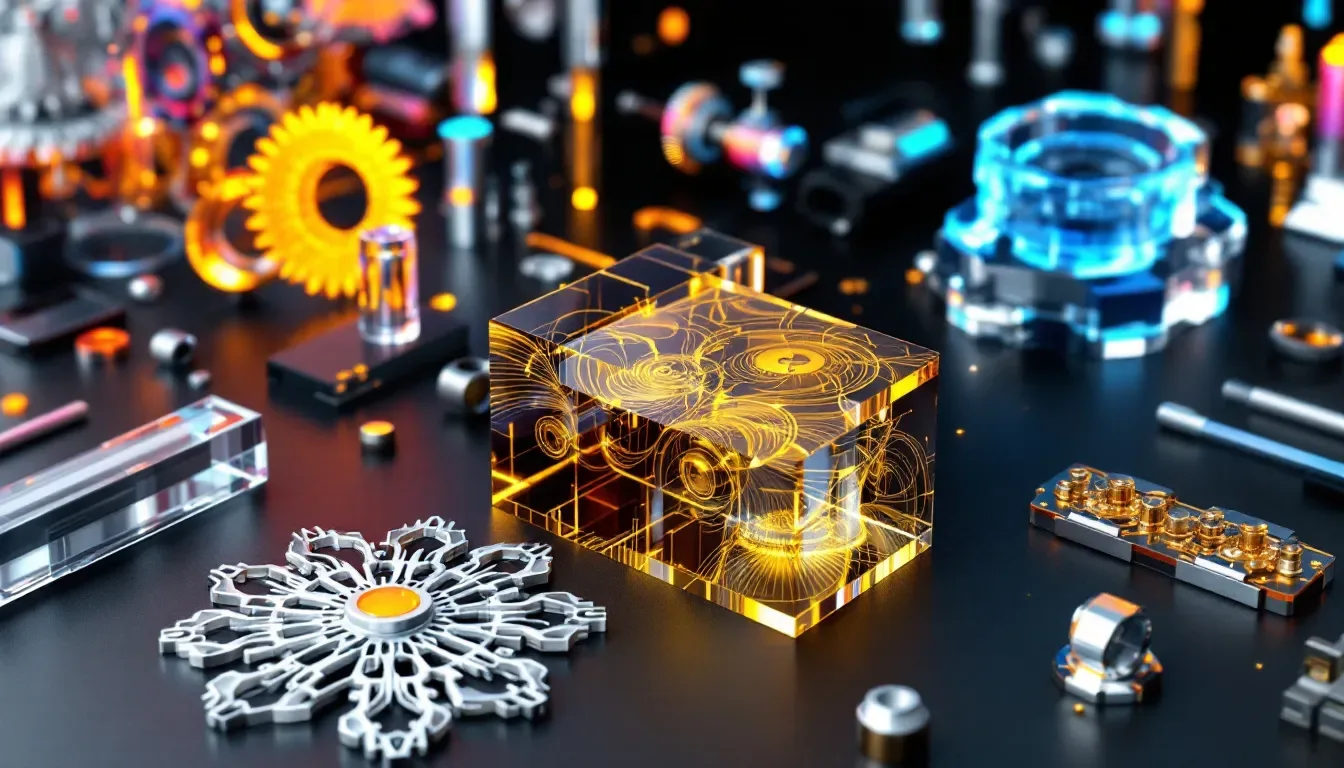
Parts created from CNC machined acrylic are utilized extensively throughout numerous sectors due to their adaptability, superb optical clarity, and robustness. These characteristics render them perfectly suited for use in:
Signage and display creation
Production of automotive parts
Manufacture of medical devices
The field of construction and architecture
CNC machining’s automated process guarantees uniform excellence across various acrylic components, establishing its dependability for applications that demand high precision.
The succeeding segments will delve into the distinct roles played by CNC machined acrylic parts within diverse industries, underscoring the advantages they provide as well as their practical applications.
Signage and Displays
Due to its transparency and visually pleasing qualities, acrylic is widely chosen for creating signs and display materials. It lends itself well to crafting eye-catching, robust signage that can be used in both interior and exterior spaces.
Acrylic’s resistance to different climatic conditions contributes to its durability, which is ideal for outdoor sign applications. In general, using acrylic for signage not only facilitates efficient visual messaging but also adds an element of aesthetic charm across various environments.
Automotive Components
Acrylic boasts widespread application within the automotive sector, prized for its lightweight and robust impact-resistant qualities.
Notable automobile elements crafted from acrylic include:
Windows on cars
Vehicle body panels
Protective fenders
Windshields for motorcycles
Encasements for internal vehicle lights as well as turn signals
Employing acrylic in car parts promotes improved fuel economy due to its reduced weight while also providing exceptional visibility owing to its optical clarity.
In essence, acrylic is a pivotal material in contemporary car manufacturing, marrying visual appeal with functionality and protection across an array of components. Its tenacity and ability to withstand force render it an ideal selection for vehicular uses, promising enduring efficiency and safeguarding occupants.
Medical Devices
Acrylic is commonly used in the medical industry for:
cabinets
incubators
glove boxes
other devices
This is due to its durability, abrasion resistance, and impact resistance. Its easy maintenance and high compatibility with biologics make it highly preferred in the healthcare sector.
Acrylic’s high compatibility rate with biologics makes it ideal for applications like filling dental cavities and other medical devices that require clear visibility and sterility.
Construction and Architecture
Acrylic is utilized in the building industry due to its attractiveness and ability to withstand UV degradation when integrated into façade designs. Its reduced weight renders it ideal for crafting doors, canopies, and additional architectural components. The use of acrylic panels has grown within contemporary architecture owing to their aesthetic appeal coupled with practical advantages like resistance to weather conditions and robustness.
In construction applications, acrylic stands out for its capacity to produce eye-catching functional architectural elements such as facades that merge intricate shapes and geometries while maintaining excellent optical clarity. This versatility establishes acrylic as an essential resource across various sectors, aiding in the creation of pioneering design features and construction methodologies.
Surface Finishing Techniques for Acrylic
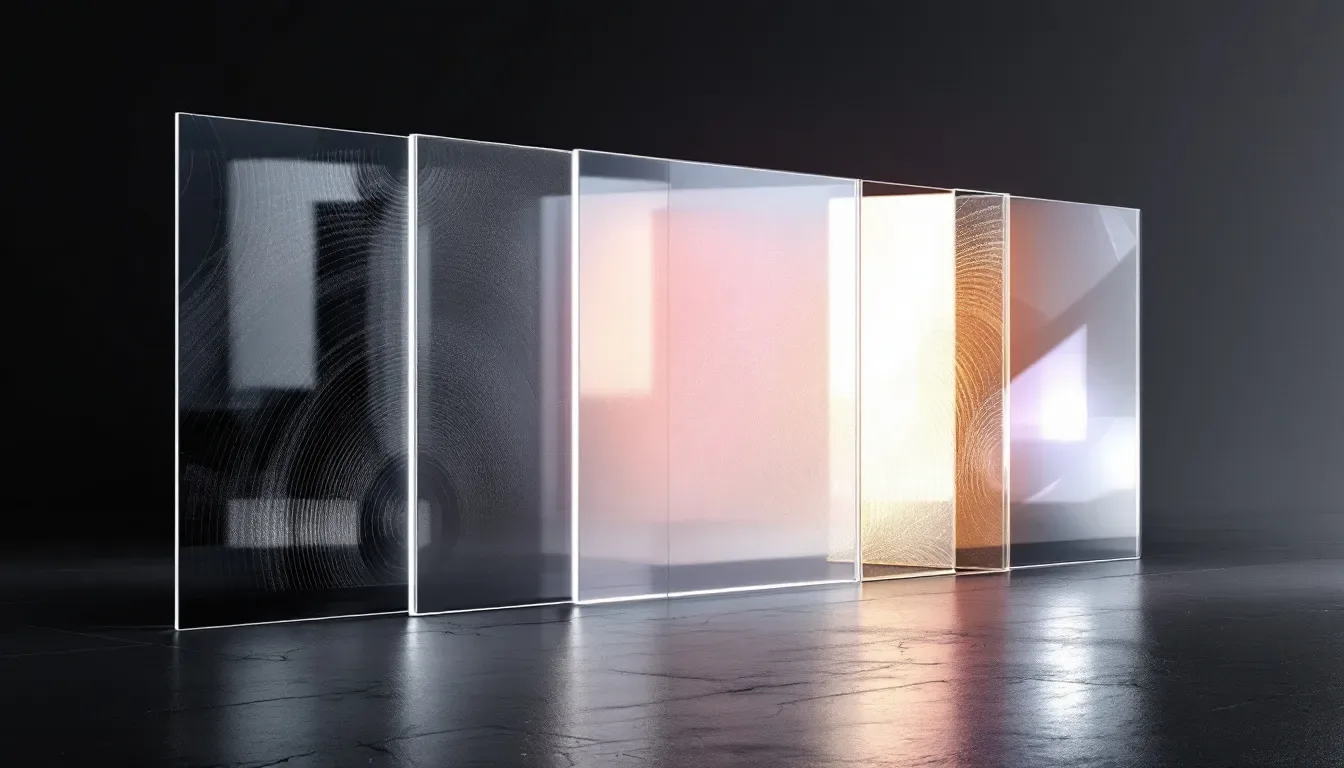
Various finishing methods can be employed to augment both the aesthetics and practical attributes of CNC machined acrylic components after they have been crafted. These approaches serve to not only elevate the visual appeal of these parts, but also boost their operational capabilities and longevity.
Subsequent sections will delve into typical finishes, bead blasting, and tailor-made polishing as principal techniques for refining the surfaces of CNC machined acrylic pieces.
Standard Finish
The typical finish applied to CNC machined acrylic parts aims to diminish the visibility of tool marks, transforming them into swirl patterns that enhance the material’s aesthetic by creating a more uniform surface.
Employing this finishing technique on machined acrylic not only renders it more visually appealing, but also represents an economical approach to ensure that these components fulfill established quality criteria.
Bead Blasting
Using small glass beads, beads blasting achieves a uniform matte surface on acrylic materials by eliminating surface flaws. This process is excellent for hiding slight scratches and marks from tools, resulting in an evenly finished acrylic workpiece.
When the desired outcome is a non-reflective finish, beads blasting comes in handy as it improves the aesthetic appeal of machined acrylic parts.
Custom Polishing
Custom polishing significantly enhances the visual, physical, and aesthetic attributes of CNC-machined acrylic components. This refinement process employs chemical agents or wet sanding to attain a highly polished and lustrous surface finish. Such methods are perfectly suited for uses where elevated optical clarity and a refined look are paramount, including in the manufacturing of display cases and optical lenses.
Manufacturers that opt for custom polishing can elevate both the functional performance and visual appeal of their acrylic parts, ensuring adherence to stringent quality benchmarks. Not merely an improvement in appearance, this finishing technique also bolsters the resilience and overall functionality of machined acrylic pieces, rendering them apt for a variety of rigorous settings.
Choosing Between Cast and Extruded Acrylic
Grasping the distinctions between cast and extruded acrylic is essential for choosing the appropriate material for particular uses. Cast acrylic boasts enhanced optical clarity and greater flexibility, whereas extruded acrylic offers more consistent dimensional stability and is less expensive. Each kind of acrylic brings distinct benefits to the table and aligns with various machining processes as well as intended applications.
In-depth discussions in forthcoming sections will delve into the properties of both cast and extruded acrylic, equipping readers with comprehensive knowledge to make educated choices tailored to their individual demands and objectives.
Characteristics of Cast Acrylic
Manufactured by polymerizing the methyl methacrylate monomer within a mold, cast acrylic boasts elevated melting points beneficial for CNC machining. This polymerization method yields a rigid framework of cast acrylic, enhancing its stability while being machined. The resulting steadiness permits adherence to stringent tolerances during CNC operations, suitable for applications that demand high precision.
When compared to extruded acrylic, cast acrylic demonstrates enhanced rigidity and reduced susceptibility to bending or chipping throughout the machining process. Its outstanding optical clarity coupled with robustness positions it as an ideal material choice for projects that necessitate not only precise engineering but also superior visual aesthetics—such as in the crafting of lenses, sophisticated display enclosures, and other essential components demanding exacting standards.
Characteristics of Extruded Acrylic
Extruded acrylic offers a cost-effective alternative to cast acrylic, making it an attractive choice for budget-conscious projects. This material boasts enhanced dimensional stability that ensures even sheet thickness, which is advantageous for uses where uniformity of the material’s properties is essential. Nevertheless, compared to cast acrylic, extruded acrylic exhibits reduced rigidity which may impact its performance in some applications.
Although it may not be as rigid, extruded acrylic benefits from simpler processing and polishing capabilities that facilitate more economical finishing methods. Its combination of affordability and ease of manufacturing renders it appropriate for numerous applications, especially when financial considerations are paramount.
Tips for Preventing Common Issues in CNC Machining Acrylic
It is essential to keep a cool environment when machining acrylic in order to avoid melting and distortion. To effectively control the heat produced, operators should ensure they manage feed rates appropriately and utilize cutters that are sharp and strong, crafted specifically for acrylic use. Adhering to this advice aids in averting typical problems like stress cracking by managing thermal output and guaranteeing correct clamping.
In subsequent sections, detailed advice will be given on how to sidestep issues such as stress cracking while also supervising thermal output during CNC machining of acrylic. This guidance aims at facilitating the attainment of superior outcomes through ensuring accurate fixturing.
Avoiding Stress Cracking
To diminish the incidence of stress cracking in acrylic, it is crucial to implement incremental temperature alterations while machining. The utilization of light pressure throughout the machining process can also aid in averting the onset of stress cracks. By carefully controlling temperatures and exerting suitable pressure, operators are able to considerably lessen the likelihood of stress cracking occurring within acrylic materials.
The issue of stress cracking poses a considerable threat to the structural soundness of acrylic parts, both during and after their machining processes. Adherence to optimal practices, coupled with employment of proper tools and methods, enables machine operators to safeguard not only long-term durability but also maintain high-quality standards for finished products involving acrylic.
Managing Heat Generation
Employing cutters that are sharp and sturdy, and specially engineered for acrylic, is key to effectively controlling the heat produced during machining. It is vital to adjust feed rates appropriately in order to strike a balance between velocity and force, thereby averting the liquefaction of the acrylic material. Vigilant oversight of cutting depth guarantees accuracy in dimensions while also preventing an overaccumulation of heat which could impair the acrylic.
Inhibiting stress cracking throughout the process of machining preserves the structural soundness of parts made from acrylic. The correct application of fixturing aids in staving off vibrations and misalignments, which might otherwise provoke undue thermal generation leading to failure within the material.
Ensuring Proper Fixturing
It is essential to secure the acrylic workpiece adequately to avoid vibrations and misalignment during CNC machining, which can result in inferior products. If fixtures are tightened excessively while machining, it may cause the parts to deform and produce features that do not meet tolerance specifications. Employing vacuum tables or soft jaws along with appropriate fixtures allows operators to keep the workpiece aligned and stationary, thereby ensuring precise cuts and top-notch final results.
Ensuring proper fixture setup guarantees that the acrylic remains stable throughout its entire CNC machining process. This stability minimizes mistakes and boosts the end product’s quality significantly. Adhering to these optimal practices enables operators to consistently achieve dependable outcomes when performing CNC machining on acrylic materials.
Summary
CNC machining provides a multitude of benefits when shaping acrylic, such as exceptional accuracy, operational efficiency, minimized wastage of materials, and overall cost reduction. Acrylic’s inherent characteristics—its clarity, strength, and lightness—render it an excellent choice for a variety of uses in sectors including the automotive industry, healthcare field, advertising signage production and building construction. Mastery over various CNC machining methods along with familiarity with optimal practices and techniques for surface finishing is crucial to secure top-notch quality and improve both functionality and visual appeal of fabricated acrylic components.
Opting between cast or extruded acrylic according to particular project needs while adhering to practical advice can greatly enhance CNC machine operations’ effectiveness. The insights provided by this guide will equip you with the necessary skills to excel in creating precision-crafted acrylic pieces through CNC technology. Thereby assuring that your endeavors adhere strictly to superior standards for excellence in craftsmanship and meticulous detail orientation.
Frequently Asked Questions
What are the main advantages of CNC machining acrylic?
CNC machining acrylic provides high precision, efficiency, and cost-effectiveness while minimizing material waste, making it an ideal choice for producing quality acrylic components.
How does CNC milling differ from CNC turning when machining acrylic?
CNC milling removes material from a flat sheet of acrylic with rotating cutting tools, while CNC turning shapes a rotating acrylic workpiece into cylindrical forms using a single cutting tool.
Thus, the primary difference lies in the shapes produced and the methods of material removal.
What are the key properties of acrylic that make it suitable for CNC machining?
Acrylic’s key properties, including transparency, rigidity, toughness, impact resistance, and lightweight nature, make it highly suitable for CNC machining, ensuring high precision and durability in various applications.
How can I prevent stress cracking in acrylic during CNC machining?
To prevent stress cracking in acrylic during CNC machining, it is essential to manage temperature and pressure carefully by ensuring gradual temperature changes and using sharp, robust cutters designed for acrylic.
Implementing these practices will significantly reduce the risk of stress cracks.
What are the differences between cast and extruded acrylic?
Cast acrylic is known for its excellent optical clarity and stiffness, which makes it perfect for uses that demand clear visibility. On the other hand, extruded acrylic provides better stability in dimensions and is more economical, making it appropriate for a wide range of applications.
These characteristics dictate the specific functions each type of acrylic is best suited for.
LKprototype has many years of experience manufacturing prototype parts for clients in the aerospace, automotive and consumer electronics industries, among others. Please contact us for a quick quote on any project.
Still, need help? Contact Us: lk@lkprototype.com Need a PROTOTYPE or PARTS machining quote? Quote now