4 axis CNC machines add a rotational axis to traditional CNC machining, making them capable of complex and precise parts. Industries like aerospace and medical devices rely on them for their versatility. This article covers how 4 axis CNC works, its benefits, and comparisons with 3 and 5 axis machines.
Key Takeaways
4-axis CNC machining enhances precision and efficiency by incorporating an additional rotational axis, allowing for complex geometries to be produced without repositioning the workpiece.
Compared to 3-axis and 5-axis machines, 4-axis CNC machines provide a balanced option for intricate part production that requires both versatility and cost-efficiency.
Regular maintenance and care are vital for the optimal performance and longevity of 4-axis CNC machines, ensuring high-quality results and minimizing operational disruptions.
Understanding 4 Axis CNC Machining
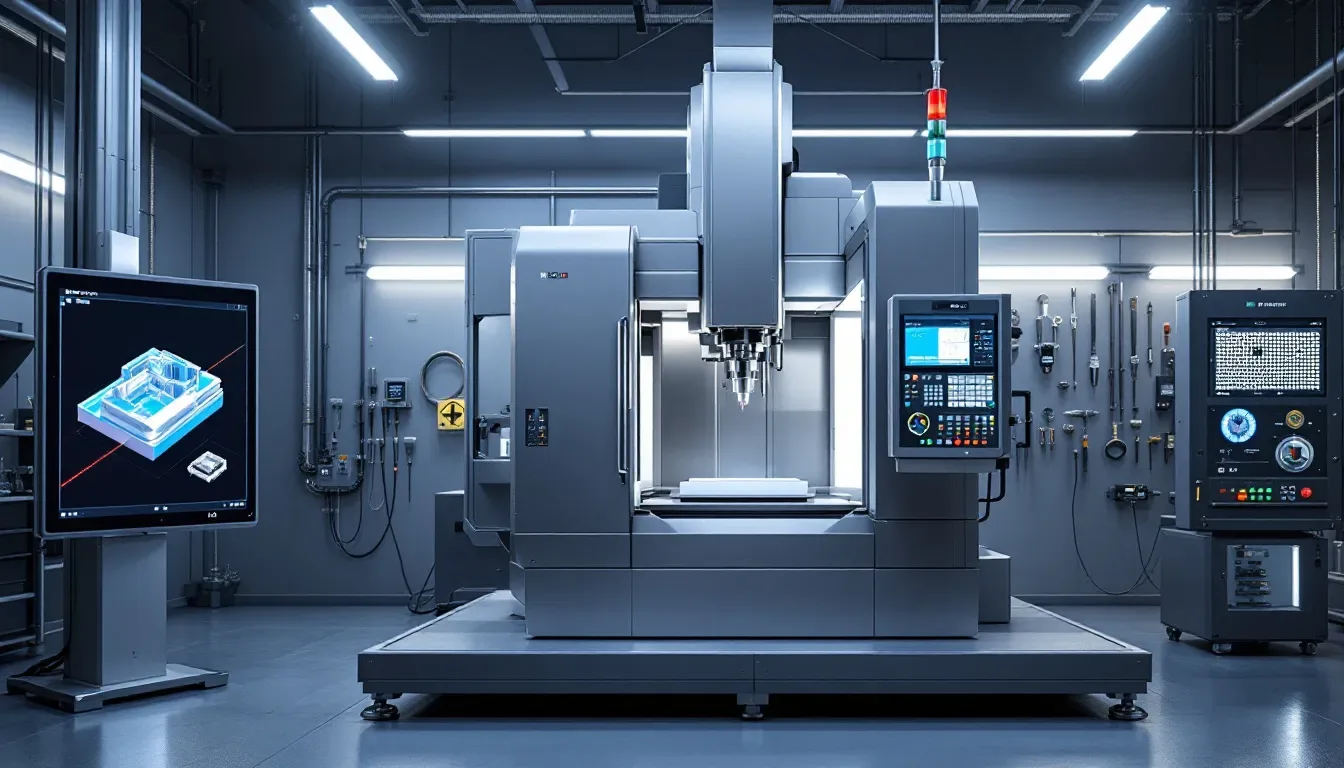
CNC machining has been elevated to a new level with the introduction of 4-axis technology, which is pivotal for manufacturing intricate components with exceptional accuracy. In contrast to conventional 3-axis CNC machines that traverse along three linear axes (X, Y, and Z), 4-axis CNC machines introduce an additional axis of rotation called the A-axis. This allows for the workpiece to revolve around the X-axis — a key advancement for fabricating complex shapes that would be difficult or impossible on traditional setups.
The versatility offered by these machines through their ability to pivot at multiple angles is especially advantageous in sectors where precision and sophisticated configurations are critical requirements. This includes industries like aerospace, medical device production, and automotive manufacturing. For example, within aerospace applications specifically, utilizing 4th axis machining is indispensable when producing components such as turbine blades and airframe parts demanding adherence to strict safety standards.
Adding a fourth rotational dimension means that parts can be machined from different orientations without necessitating multiple setups—streamlining operation times while simultaneously ensuring consistent rotation during processing. The result? An acceleration in workflow coupled with diminished margin for error translates into superior quality products alongside increased profitability margins for manufacturers leveraging these advanced CNC capabilities.
How Does 4 Axis CNC Compare to 3 and 5 Axis Machines?
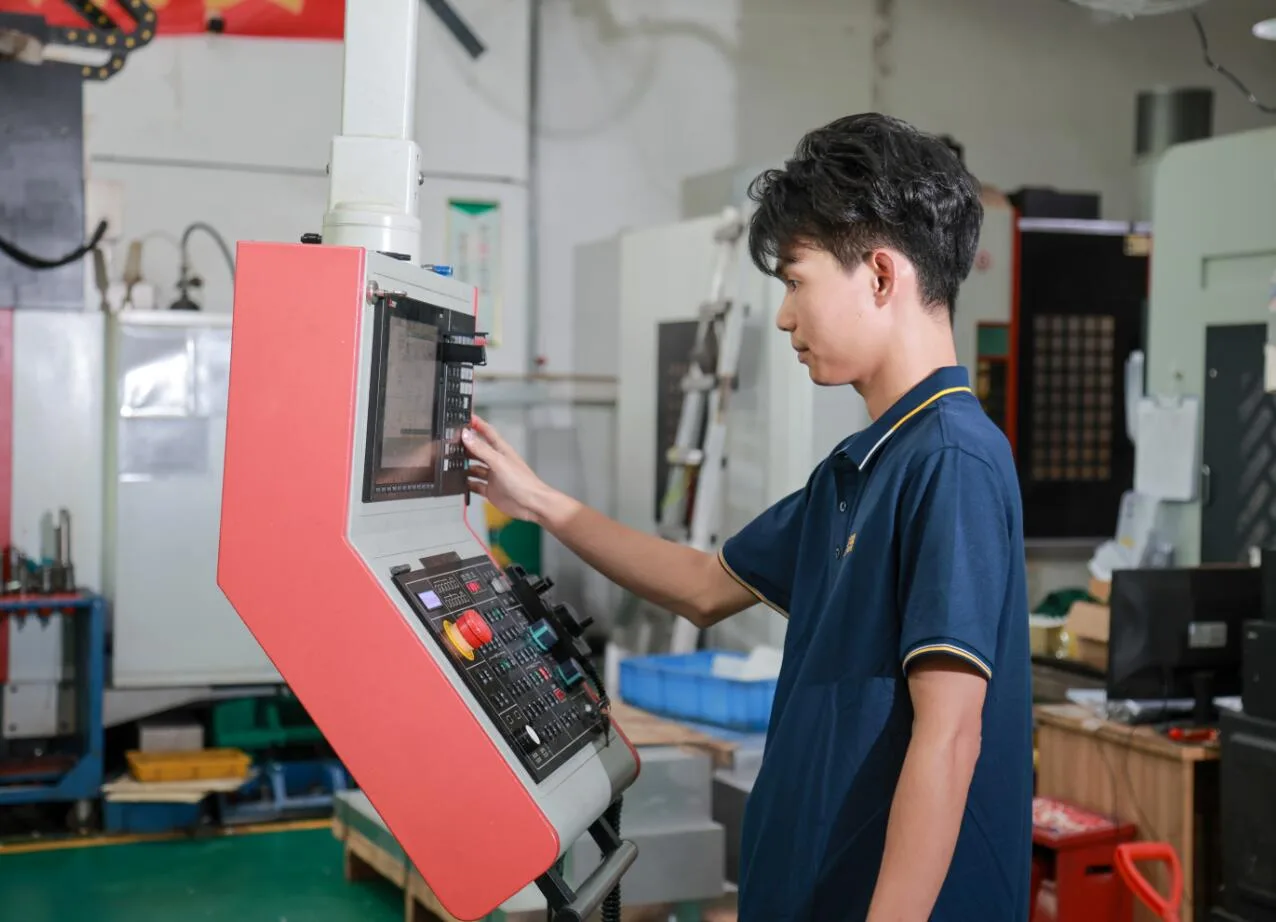
When examining the distinctions between 4-axis CNC machines and their 3-axis and 5-axis variants, it’s clear that each has different capabilities suitable for specific tasks. A typical 3-axis CNC machine maneuvers along the X, Y, and Z axes. This restricts its capacity to produce intricate geometries. Although these machines are adept at simpler jobs, crafting angled cuts often requires multiple setups—resulting in a process that can be both time-intensive and error-prone.
Adding a fourth dimension of movement with the introduction of an A-axis—the rotational axis around the X axis—4th axis CNC machines excel in fabricating more complex shapes with greater efficiency and precision. For instance, where creating angled features on a three-axial setup requires several configurations leading to increased labor hours—a single-setup procedure on a four-axial platform significantly streamlines production times.
Moving up in complexity is represented by five-axial machining, which involves operating across two main types: simultaneous milling involving all axes including B and C (the two rotational ones), as well as index milling combining linear motion plus positional rotation using just two rotations instead—all providing superior precision shaping alongside capable handling of extensive complexities ideal for sophisticated applications commonly known as “five axises”.
Despite being unmatched regarding versatility when dealing with convoluted designs or curved forms—owing mostly to its hefty price tag alongside demand for higher-level programming expertise—not every job necessitates such elaborate machinery. Thus presenting four axial units like quintessential middle-ground options balancing proficient functionality against economic considerations effectively within reach especially considering most nuanced yet practical manufacturing needs calling only for competent geometry management without needing extreme intricacy levels typically associated with “axis cnc” performances.
Key Components of a 4 Axis CNC Machine
Grasping the essential elements of a 4-axis CNC machine is crucial for proficiently operating it and fully leveraging its capabilities. Each part plays an integral role in ensuring these machines provide superior performance and precision.
Key components encompass the A-axis, which is central to their functionality, along with the cutting tool paired with the spindle, and also include systems designed for securing the workpiece in place.
The A Axis
CNC machines equipped with a fourth axis, known as the A-axis, offer rotational movement along the X-axis. This extra dimension greatly enhances the machine’s ability to create intricate shapes and designs. By allowing the workpiece to turn during operations, multiple aspects can be machined without needing to manually reposition it—boosting both versatility and productivity.
Specifically, this feature of 4-axis CNC technology simplifies tasks such as machining cylindrical components, which might prove challenging or even unattainable using a mere 3-axis setup. The incorporation of an A-axis is especially beneficial for jobs demanding angled features or complex cuts, solidifying its role as an invaluable component in contemporary CNC machinery.
Cutting Tool and Spindle
In a 4-axis CNC machine, the cutting tool and spindle are vital for maintaining precision and efficiency. The spindle secures the cutting tool and traverses along three axes in a linear fashion, offering meticulous control throughout the machining process. This arrangement facilitates complex cuts and detailed operations that are indispensable for crafting parts of high quality.
The efficiency and accuracy of the machining process also hinge significantly on the design and material composition of the cutting tool. Selecting appropriate cutting tools and spindles tailored to match specific materials being machined is crucial. It ensures peak performance from both workpiece and CNC equipment alike while fostering production of precise parts with minimal wear inflicted upon the machinery.
Workpiece Fixturing
Maintaining the stability and accuracy of a workpiece during machining operations is essential, as it significantly reduces vibrations and guarantees that the workpiece stays firmly fixed. This practice is key to attaining superior quality outcomes.
When working with 4-axis CNC machinery, employing specialized fixturing devices such as tombstones becomes commonplace. These tools can secure several components at once, streamlining setup modifications. Such methods boost not only stability but also operational efficacy by enabling faster production rates and heightened precision in machining tasks.
Benefits of Using 4 Axis CNC Machines
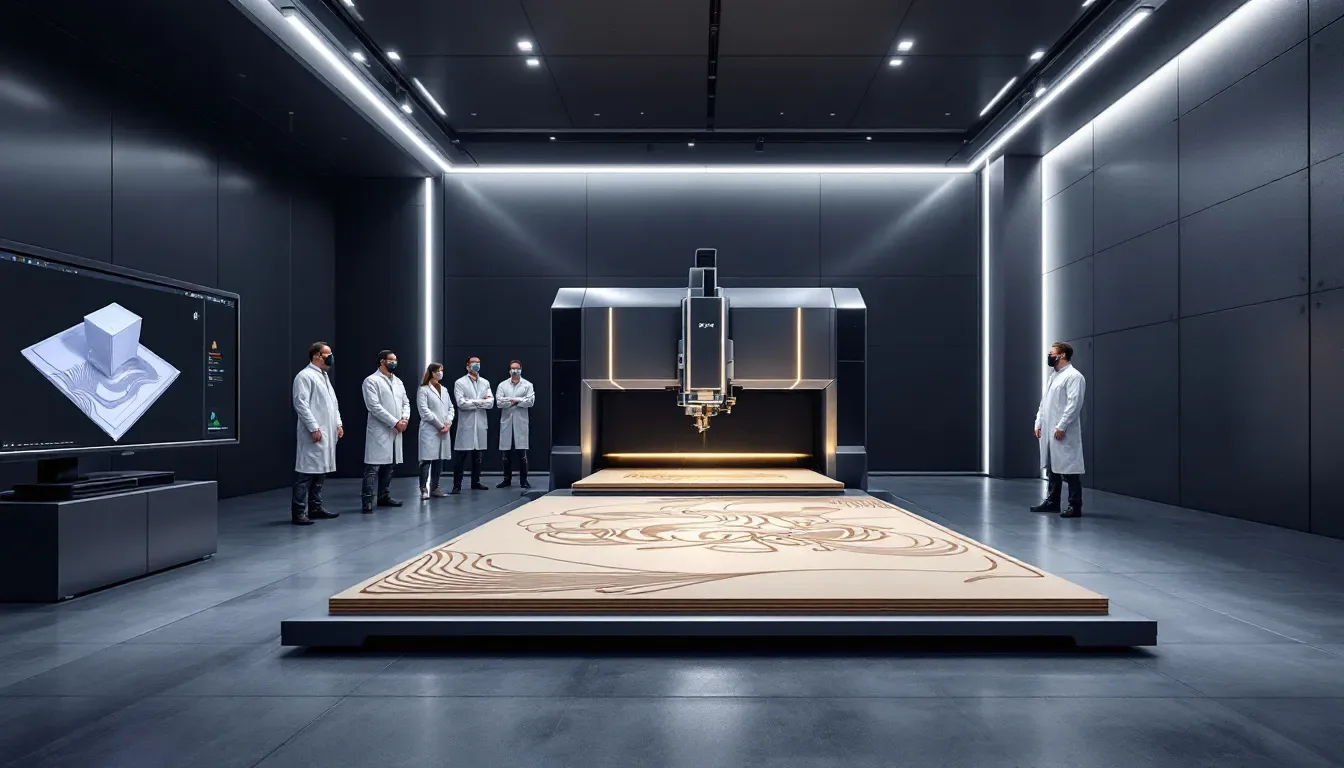
Utilizing 4-axis CNC machines offers a range of significant and beneficial impacts. A primary advantage includes the substantial decrease in the time it takes to produce parts, as these machines can perform machining from various angles within one operation, thus minimizing the necessity for repeated repositioning of the workpiece and consequently reducing setup times.
The enhanced capabilities provided by these machines lead to greater precision due to their ability to access different faces of a material continuously, which results in less waste and heightened profitability. The versatility that allows them to handle complex designs without needing complicated fixtures renders 4-axis CNC machinery essential for fabricating components with intricate details.
Advanced machining abilities enable manufacturers to craft elaborate shapes with reduced setups. This improvement not only increases efficiency but also diminishes potential errors. Cumulatively, these advantages make investment into 4-axis CNC technology extremely valuable for manufacturing operations aiming at bolstering accuracy, productivity, and overall effectiveness.
Applications of 4 Axis CNC Machining
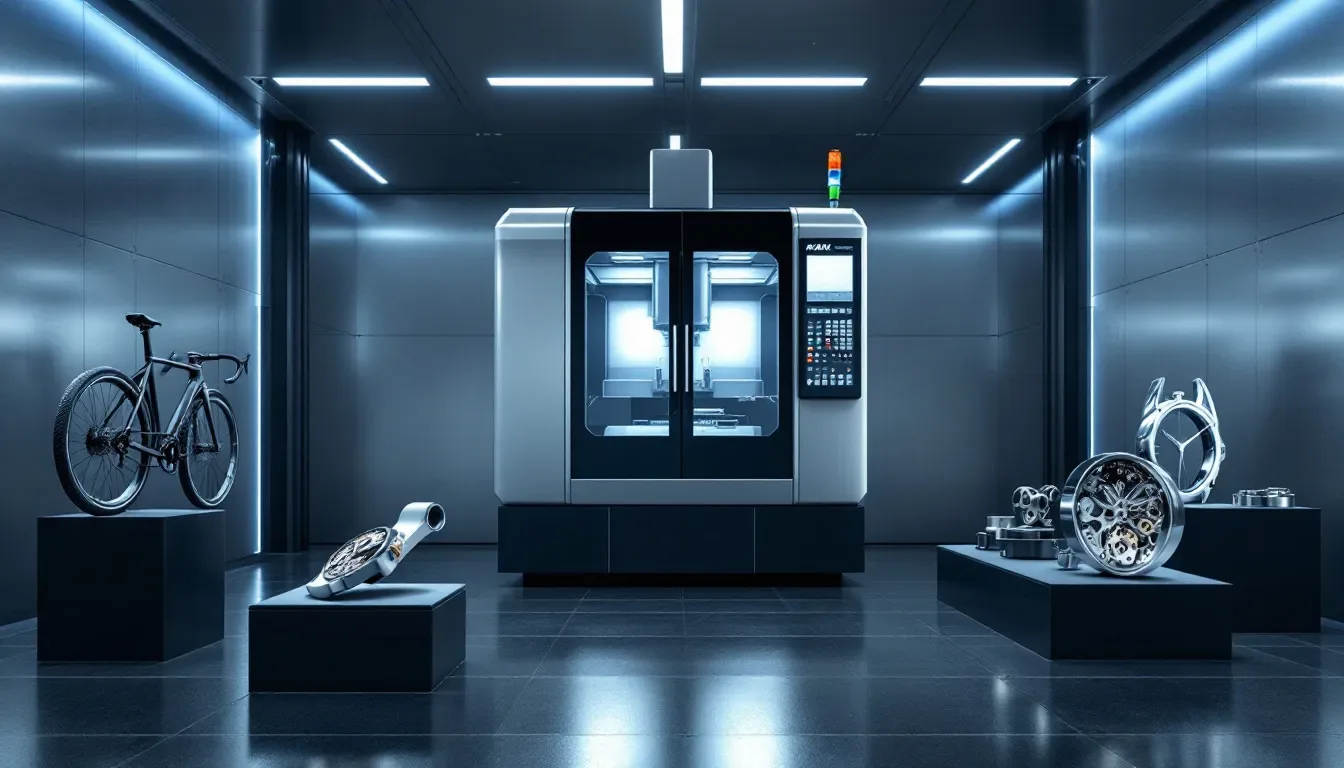
Four-axis CNC machining is highly adaptable and can be used in numerous sectors for a variety of purposes. These uses span from sculpting detailed artworks to crafting essential aerospace parts, constructing medical apparatus, and assembling components within the automotive industry.
Machines equipped with 4-axis CNC capabilities are particularly adept at manufacturing parts that are both intricate and meticulously precise.
We will delve into particular instances showcasing the application of four-axis CNC machining in these critical areas of industry throughout subsequent sections.
Aerospace Industry
The aerospace sector requires exceptionally high levels of precision and the capacity to produce complex shapes. This is where 4-axis CNC machining becomes essential, particularly in the creation of turbine blades and engine parts that adhere strictly to safety and performance requirements. Crafting components that are both strong and light contributes significantly to improving fuel economy as well as the overall functionality of aircraft.
Specifically, producers employ machines capable of 4-axis CNC operations for fabricating sophisticated airframe pieces along with turbine blades, achieving a balance between meticulous accuracy and production efficiency. Such advanced capabilities ensure compliance with the intense specifications demanded by aerospace applications, thereby enhancing aircraft safety while boosting their operational effectiveness.
Medical Devices
The health care sector depends significantly on the capabilities of 4-axis CNC machining to manufacture complex parts that adhere to stringent safety and efficiency criteria. This technique is crucial in crafting precise surgical tools and implants, which guarantees their operability and dependability.
As an illustration, orthopedic implants and dental prosthetics are fabricated using 4-axis CNC machines, allowing for the creation of intricate shapes while preserving superior surface finishes. Such precision is vital for devices like surgical instruments where exactness is imperative for assuring positive results during medical procedures.
Automotive Sector
In the realm of automotive manufacturing, 4-axis CNC machining plays a crucial role in streamlining production processes by enabling swift creation of exact precision parts. This advanced capability is essential for fabricating intricate automobile components like camshafts and engine elements efficiently and with great precision.
The advantage for manufacturers lies in their capacity to concurrently produce oversized components, which translates into considerable reductions in time and enhancements to production timetables. Employing 4-axis CNC machines within the automotive industry guarantees that parts adhere to rigorous quality demands, leading to an overall enhancement in vehicle performance and dependability.
Selecting the Right 4 Axis CNC Machine
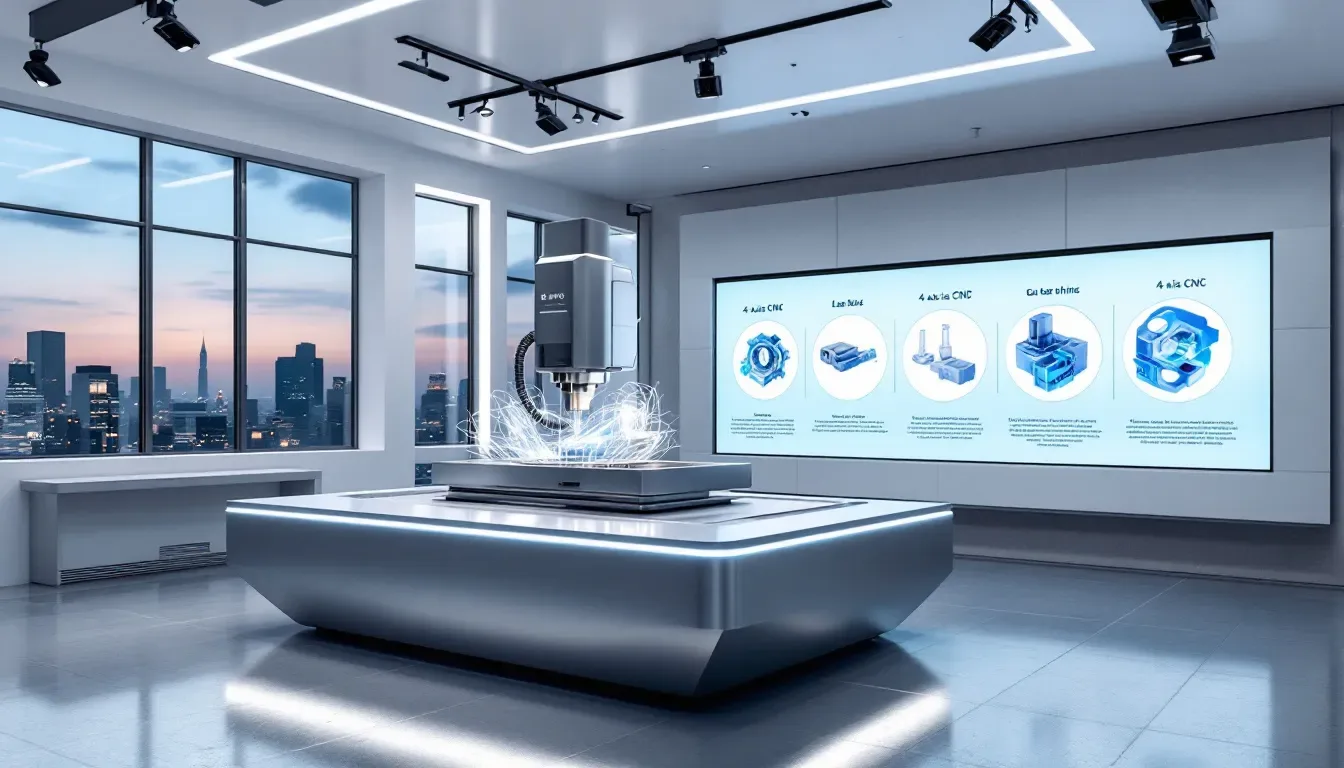
Selecting the appropriate 4-axis CNC machine requires careful thought about various key aspects. The addition of an axis to a machine, transforming it into a 4-axis model, results in more complex machining operations and often entails a greater financial outlay than its 3-axis counterparts. It is important to evaluate the quantity of production and ensure that the selected machine can handle the anticipated volume efficiently, possibly incorporating automation for tasks with higher output demands.
Material compatibility is another essential consideration when choosing your CNC machine. Ensuring that materials are suited to the specific capabilities and tool requirements of your CNC equipment is paramount for achieving top-notch performance and high precision levels. For instance, LKprototype has proven their ability by handling both extensive and minimal batches of machined metal parts effectively—underscoring how critical it is to pair material processing needs with what your chosen machinery can offer.
Lastly, one must take into account additional features like state-of-the-art controllers or tailor-made fixturing systems which can significantly bolster a 4-axis CNC machine’s functionality while enhancing productivity as well. Opting for equipment tailored to meet unique operational demands plus considering scalability vital for long-term success will ensure maximum returns from your investment in advanced cnc technology.
Enhancing Capabilities with Accessories
Augmenting 4-axis CNC machines with the addition of accessories can markedly elevate their functional performance and adaptability. For example, using advanced controllers may boost both precision and flexibility during operation, thereby facilitating more intricate machining projects. Specialized fixturing systems play a crucial role in securing workpieces firmly, which translates to enhanced stability and precision throughout the machining cycle.
By integrating accessories such as laser engravers into a CNC machine’s setup, you can broaden its capabilities to encompass tasks like engraving, thus unlocking opportunities for producing complex designs and precise detailing. Choosing appropriate accessories that align with your particular requirements can convert an ordinary 4-axis CNC machine into an exceptionally versatile and proficient instrument equipped for tackling diverse applications.
Maintenance and Care for 4 Axis CNC Machines
To guarantee the effective performance and durability of 4-axis CNC machines, consistent maintenance and care are imperative. Tasks performed daily should consist of monitoring levels of lubrication and hydraulic oil, purifying machine exteriors, and applying grease to components in motion. Conducting these regular checks can avert malfunctions while preserving peak functioning.
On a monthly basis, it’s advisable to carry out expert inspections that include cleaning filters and eliminating debris from vital sections such as the pallet changer. This action helps maintain fluid operations by preventing contamination.
Semi-annual upkeep requires exchanging old hydraulic oil with new one, as well as cleansing the coolant tank to expel any build-up of sludge or metal fragments. Such comprehensive cleanliness sustains operating efficiency for the machine whilst averting possible complications.
Yearly assessments should encompass backlash testing alongside scrutiny into how aligned the machinery is. This combats inaccuracies during cutting processes. Verifying that there’s an accessible inventory of spare parts is essential so operational interruptions remain brief through prompt component exchanges when necessary.
Adopting a minimum quantity lubrication system could enhance both tool lifespan and surface quality owing to diminished frictional heat generation. It is also crucial to review if power demands for your CNC device meet available electrical resources at its specific location among other utility requirements.
Faithfully conducted maintenance not only prolongs your apparatus’ service life, but also assures sustained high-performance yielding consistently superior outputs.
Case Study: Successful Implementation of 4 Axis CNC Machining
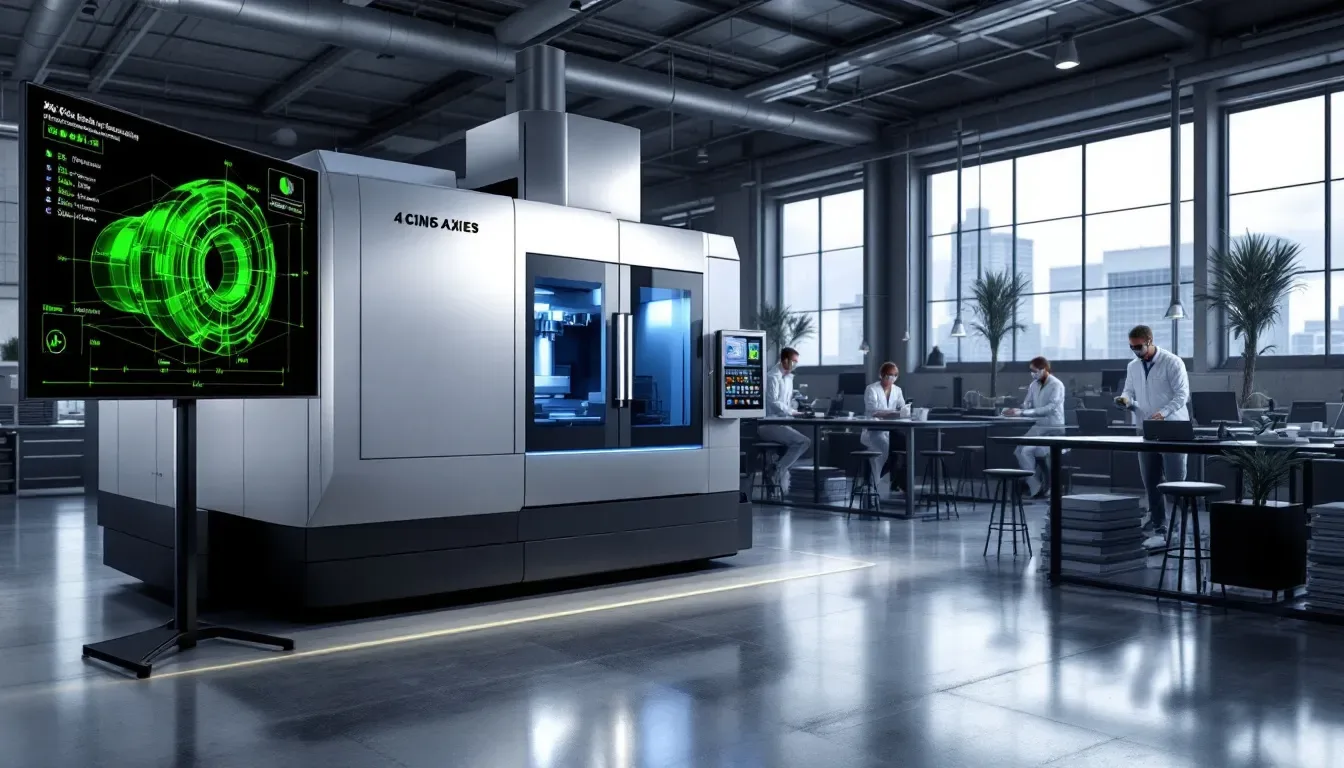
A prominent aerospace manufacturer adopted four-axis CNC machining to improve their production capabilities and remain competitive in the market. Previously, the firm encountered substantial delays in manufacturing and was restricted by their ability to craft complex geometries for aerospace components.
In response to these hurdles, the company made a significant investment in cutting-edge 4-axis CNC machines while providing extensive training for its operators and setting up rigorous quality control protocols. This calculated move not only enhanced their efficiency in production, but also allowed them to fabricate more intricate and accurate parts.
The outcomes were striking as the company saw a surge of 30% in production efficiency along with marked reductions in time required for manufacturing. This particular case underscores how pivotal four-axis CNC machining can be, demonstrating its capacity to spur innovation and elevate productivity within the realm of industrial manufacturing.
Summary
4-axis CNC machining stands as a notable breakthrough in the realm of manufacturing technologies, characterized by its exceptional precision and operational efficiency. By grasping the distinctive features that set it apart from other CNC machinery and recognizing its essential components, manufacturers are equipped to utilize this technology for fabricating intricate and superior quality products.
Owing to advantages such as shorter production cycles and improved accuracy, 4-axis CNC machines constitute a prudent investment for numerous sectors. These industries range from aerospace to medical device production, along with automotive manufacturing – all can immensely benefit from the vast applications offered by 4-axis CNC machining. To fully tap into these capabilities, selecting an appropriate machine supplemented with suitable accessories and ensuring diligent maintenance is crucial for manufacturers aiming at outstanding performance outcomes.
Frequently Asked Questions
What are the key differences between 3-axis, 4-axis, and 5-axis CNC machines?
CNC machines are distinguished by the number of axes they use: 3-axis machines operate using three linear axes, labeled X, Y, and Z. In contrast, 4-axis CNC machinery adds a rotational A axis to increase complexity in operations. 5-axis machines expand their capabilities with two additional rotational axes known as B and C, which allow for advanced simultaneous milling of complex 3D forms.
What industries benefit the most from 4-axis CNC machining?
Aerospace, medical devices, and automotive industries benefit the most from 4-axis CNC machining, as it enables the production of intricate and precise components essential to their applications.
How does the A-axis enhance the capabilities of a 4-axis CNC machine?
By incorporating the A-axis, a 4-axis CNC machine is granted the capability to rotate around the X-axis. This feature allows for the creation of complex shapes and geometries during machining processes without necessitating reorientation of the workpiece.
Such an enhancement substantially elevates both versatility and productivity in various machining tasks.
What factors should be considered when selecting a 4-axis CNC machine?
When selecting a 4-axis CNC machine, it is essential to consider the complexity of the machining process, production volume, material compatibility, and the potential need for automation.
These factors will ensure that the machine meets your specific operational requirements.
What maintenance tasks are essential for 4-axis CNC machines?
Regular maintenance activities for 4-axis CNC machinery involve checking lubrication levels every day, having experts conduct inspections each month, replacing hydraulic oil twice a year, and performing alignment as well as backlash evaluations annually.
Carrying out these procedures is vital to guarantee the best functioning and extended lifespan of these machines.