A 2 axis CNC machine operates on the X and Y axes to cut, drill, and engrave materials with precision. These machines are vital in industries like automotive and aerospace for crafting intricate parts. In this guide, we’ll dive into the types of 2 axis CNC machines, their features, and how they can benefit your projects.
Key Takeaways
2 Axis CNC Machines offer precision manufacturing capabilities for various industries through X and Y axis movements, enabling intricate designs and complex parts.
The three primary types of 2 Axis CNC Machines—vertical, horizontal, and gantry—each serve different purposes and have unique advantages, such as ease of operation and cost-effectiveness.
Key advantages of 2 Axis CNC Machines include increased precision, enhanced productivity, and cost-effectiveness, making them essential for small to medium-scale manufacturing.
Understanding 2 Axis CNC Machines
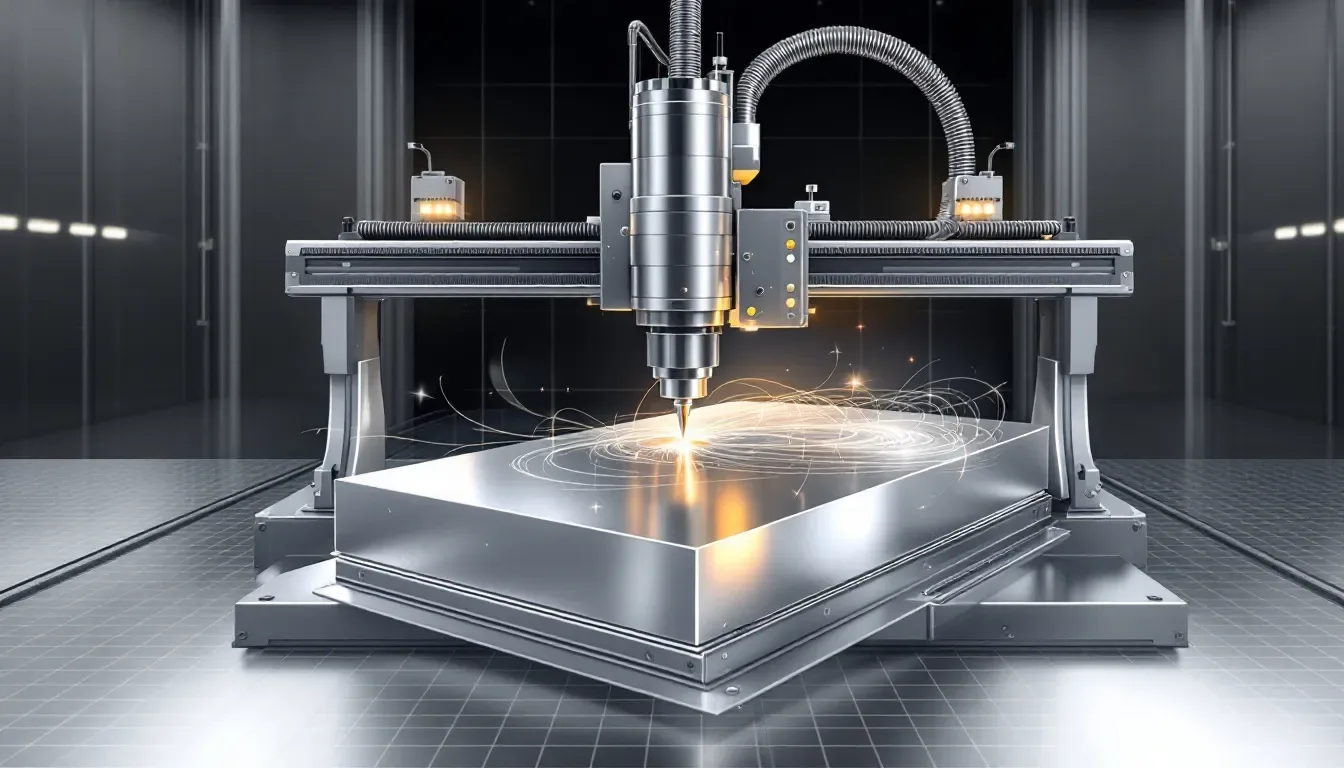
The 2 Axis CNC Lathe stands as a cornerstone in the realm of precision manufacturing, epitomizing the advancements in modern mechanics. Equipped to perform functions such as cutting, drilling, and engraving on a multitude of materials with outstanding accuracy, these machines utilize their primary X and Y axes for meticulous control. This enables them to fabricate complex components and elaborate designs with ease—whether it be carving an intricate wooden piece or executing detailed metalwork according to strict specifications. Such tasks are readily accomplished thanks to the adaptability inherent in two-axis CNC lathes.
Their utility extends beyond sheer capability. 2 axis CNC machines are instrumental in producing both basic ornaments and sophisticated artistic structures alike. The extensive versatility possessed by these devices renders them indispensable across numerous sectors that range from automotive production to aerospace engineering all the way through consumer electronics assembly.
Delving into fundamental operations unveils Prospects for elevating manufacturing precision—a testament to how these versatile machining tools can redefine conventional practices within various industries where utmost control is paramount.
Types of 2 Axis CNC Machines
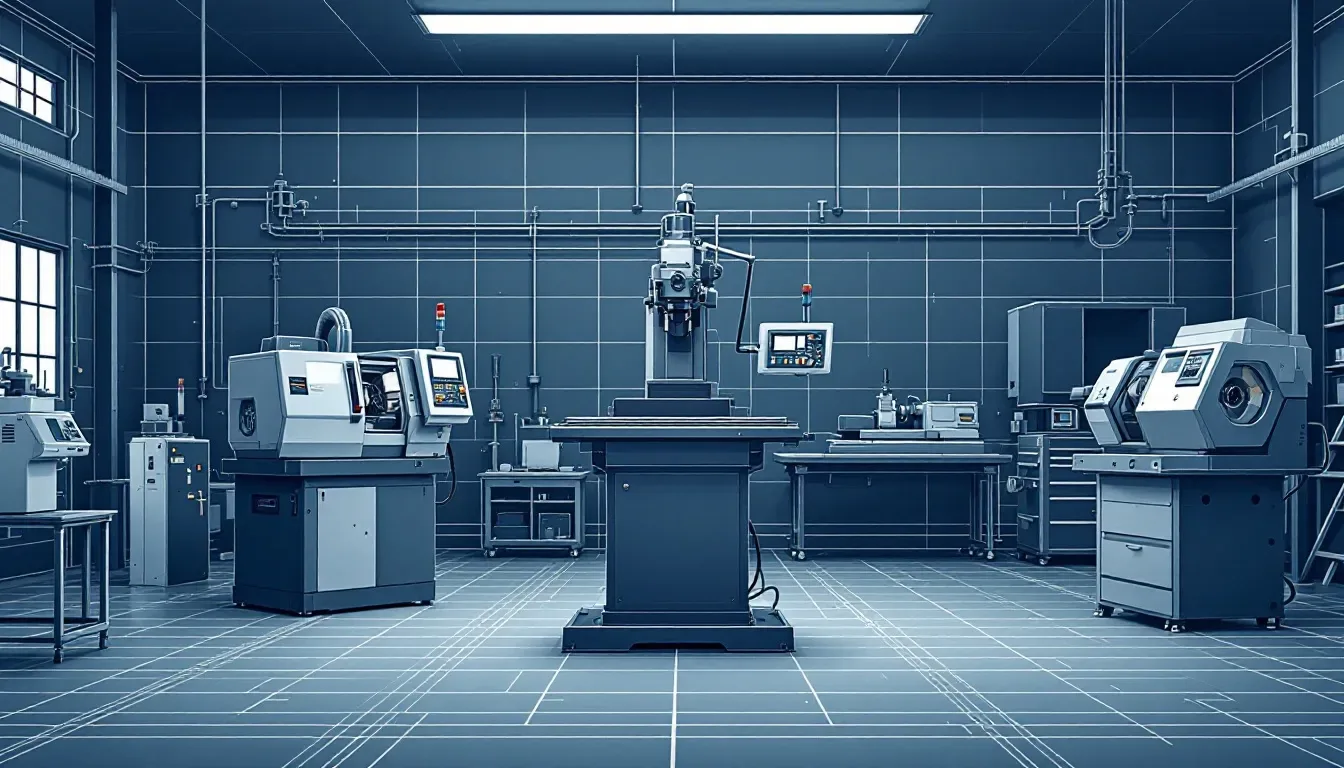
There are three prominent varieties of 2 axis CNC machines: vertical, horizontal, and gantry. Each one offers distinct benefits and is suited for specific uses. Vertical models are favored due to their straightforward operation and ease of maintenance. Horizontal types boast sustained accuracy, making them perfect for achieving meticulous cuts. There’s a possibility that parts may warp as a result of vibrations.
On the other hand, gantry-style machines are recognized for being cost-effective options frequently utilized in production environments. They offer an expansive working space which is apt for larger scale projects. Understanding these differences can assist you in choosing the appropriate machine tailored to your requirements.
Key Features of 2 Axis CNC Machines
When examining the capabilities of 2 Axis CNC machines, certain characteristics are notably significant. These machines conventionally function along two dimensions, utilizing the X and Y axes to execute movements with high precision. These devices feature a robust table designed for carrying out machining operations and are equipped with several tool positions that can manage diverse tasks.
The meticulous machining of the table is vital in guaranteeing accurate placement of the workpiece—this factor is imperative for achieving precise results during operation. We will explore these attributes more comprehensively in subsequent sections.
X Axis and Y Axis Movements
Movements along the X and Y axis form the foundation of 2 Axis CNC Machines. This control over tool positioning translates into increased precision and uniformity in manufactured parts. Ensuring that the bed is aligned parallel to the spindle guarantees that during z axis machining, the workpiece maintains its parallelism, which is vital for executing exact cuts.
Having a bed square to its pathways boosts cutting accuracy even more. Such alignment plays an essential role in reducing mistakes while optimizing process dependability. The capability for precise movements permits manufacturers to maintain elevated levels of quality and consistency across their products.
Spindle Speed and Control
Another essential element in CNC machining is the spindle speed, which significantly influences the cutting effectiveness and the quality of surface finishes produced. The presence of an extended spindle nose on a 2 axis CNC lathe improves machining precision and accommodates more substantial tooling options, thereby boosting control over spindle speed. Such meticulous management is crucial for attaining stricter tolerances and enhancing the quality of finished products.
The ability to fine-tune spindle speed plays a pivotal role in amplifying efficiency during machining operations. Tailoring this variable according to both material properties and targeted finish refines the overall cutting process, guaranteeing outcomes that are noticeably superior.
Stepper Motors and Electronics
Stepper motors serve as the pivotal components in CNC machinery, offering meticulous governance of movement essential for assorted machining tasks. They transform electrical impulses into segmented rotational actions, which allows for the precise placement of machining tools. The incorporation of sophisticated electronics with these stepper motors facilitates consistent and dependable performance across a range of scenarios.
Equally important is the selection of software, which amplifies control versatility and boosts operational productivity. Features such as customizable settings and joystick-driven control techniques can markedly enhance the functionality of 2 Axis CNC machines.
Together, these aspects underpin the exceptional precision and dependability that epitomize contemporary CNC machining processes.
Advantages of Using 2 Axis CNC Machines
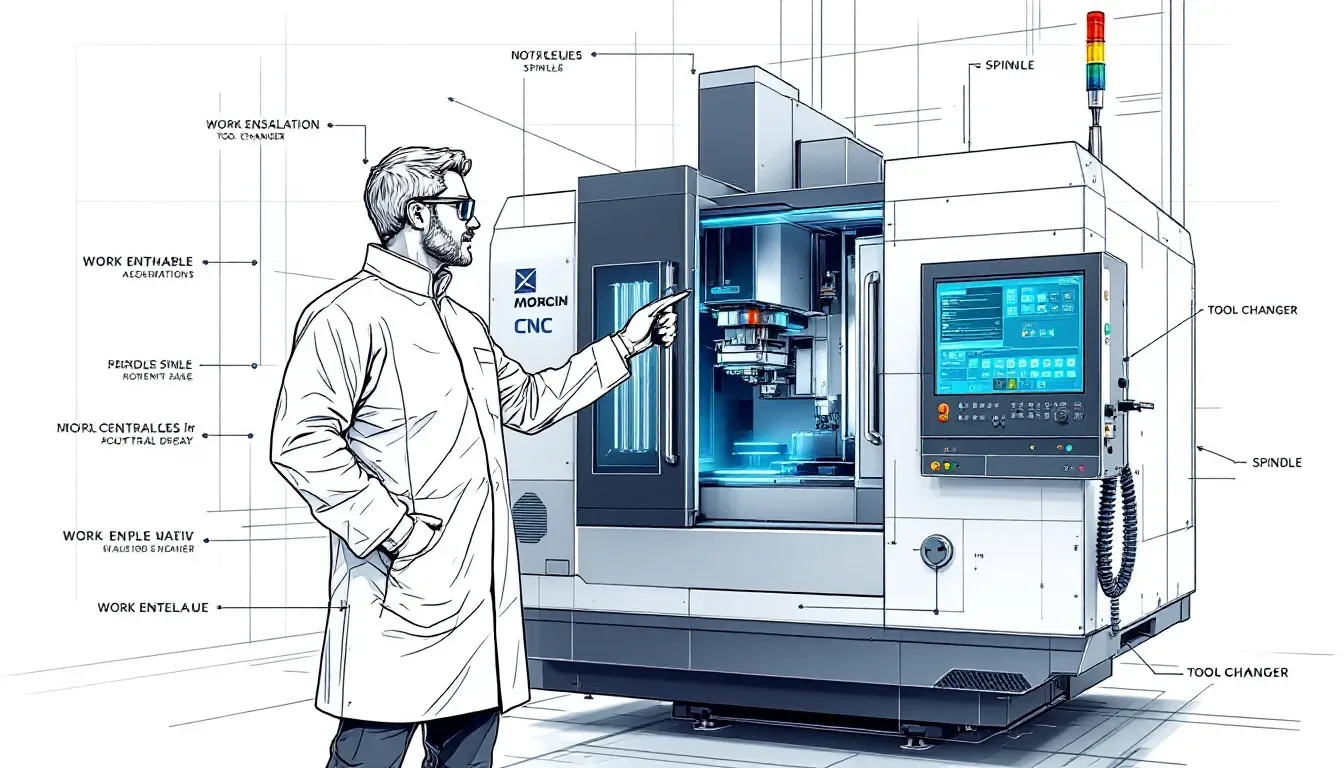
Machines equipped with 2 axis CNC technology offer numerous benefits, such as improved accuracy, boosted efficiency in production, and economic savings. These attributes render them essential across diverse sectors.
We will delve into a deeper examination of these advantages to understand their significance better.
Increased Precision and Accuracy
2 Axis CNC machines are celebrated for their precision and accuracy, as they utilize stepper motors to meticulously govern the movement and positioning of cutting tools. This meticulous control is essential when crafting intricate geometries to meet precise specifications—a requirement paramount in industries that demand high precision like aerospace and automotive.
These machines offer superior repeatability, which ensures uniformity among parts throughout production batches. Evaluating the linear motion accuracy and repeatability is vital in determining a CNC machine’s precision level and securing consistent outcomes during operation.
Enhanced Productivity and Efficiency
The 2 Axis CNC Machines offer notable benefits in the form of heightened productivity and efficiency. They facilitate rapid waste removal from the workpiece, which cuts down on production duration. Optimizing spindle speed is key to maximizing material removal rates and achieving preferred surface finishes, thereby boosting efficiency.
A decrease in the required number of setups helps elevate productivity by reducing idle periods. This aspect is especially advantageous for projects with low volume since abbreviated setup durations expedite overall production timelines. The adoption of standardized tool holders along with a methodical arrangement lessens setup times while enhancing consistency across operations.
Cost-Effectiveness
The economic benefits of 2 Axis CNC Machines are significant. Although these machines have a higher initial investment compared to manual alternatives, owing to their enhanced features, they tend to be more economical than their multi-axis counterparts over time. The yearly expenses associated with the ownership and operation of a 2 Axis CNC Machine typically fall between $1,000 and $10,000.
Given the superior accuracy, productivity, and consistency these machines provide, this outlay is considered reasonable. For small to medium-sized operations focused on precision manufacturing, the cost-efficiency presented by 2 Axis CNC Machines renders them an appealing choice for many businesses.
Applications of 2 Axis CNC Machines
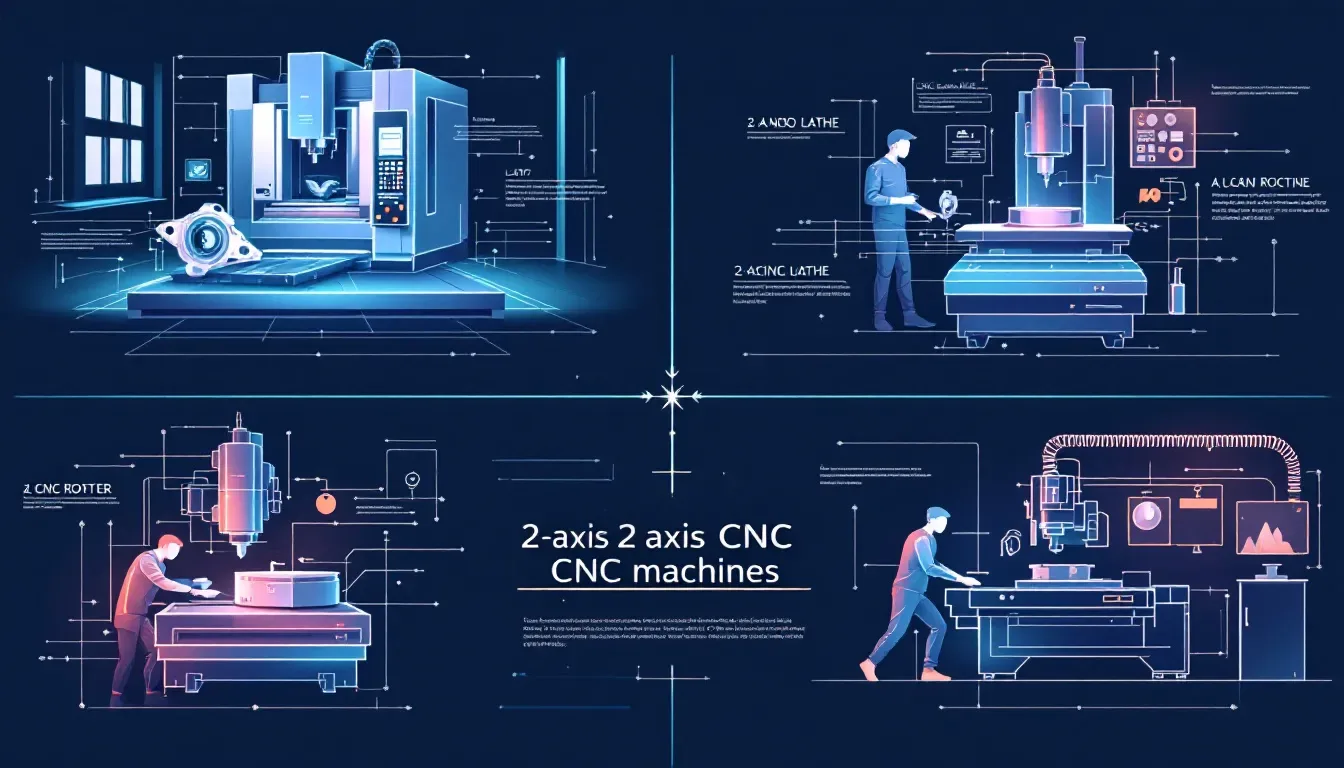
2 Axis CNC. Machines are utilized in multiple sectors, encompassing the aerospace, automotive, and consumer electronics industries. In aerospace, these machines enable the production of intricate parts such as turbine blades and engine components due to their exceptional accuracy. The automotive industry relies on them for crafting essential elements like gears and bearings.
Manufacturers within the consumer electronics realm leverage 2 Axis CNC Machines to craft detailed pieces that form part of devices such as smartphones and tablets. These machines greatly reduce the time it takes to produce these components, making them ideal for precision manufacturing at a small or medium scale.
For optimal performance outcomes with these machines, it is imperative to have knowledge about which materials they can effectively work with.
Choosing the Right 2 Axis CNC Machine
Choosing the right 2 Axis CNC Machine involves considering several factors, including machine capabilities, software and control systems, and material compatibility.
Detailed guidance on these considerations follows.
Assessing Machine Capabilities
Evaluating the potential of a machine necessitates examining its variety, capabilities, positioning, available software choices, and cost. For precision in machining tasks, it is essential to have a level table and accurately aligned bed. Machines that operate with two axes are particularly beneficial for straightforward projects and rapid preparation phases. They are ideal for novice users or operations on a smaller scale.
For optimal accuracy and efficiency during calibration processes, skilled technicians play an indispensable role. The use of calibration instruments that align with national standards can significantly improve the trustworthiness of measurement outcomes.
Evaluating Software and Control Systems
Enhancing the performance of a machine involves assessing both the control systems and software. Software customization enables users to adapt the machining process according to particular project needs. Diverse control methods, including computer and joystick interfaces, offer flexible ways to operate a CNC machine with efficacy.
Selecting appropriate software and controls markedly improves operational flexibility and efficiency, which helps achieve preferred results in CNC machining operations.
Considering Material Compatibility
Ensuring that the correct materials are used is essential for achieving maximum efficiency and longevity of CNC machines. Assistance from specialists, such as those at Sharp Industries, can be invaluable in choosing the right CNC machines that are compatible with specific materials. With an extensive selection of over 65 certified materials provided by companies like LKprototype, there is a broad spectrum available to cater to various CNC machining needs.
The length of the spindle nose plays a significant role in improving precision during the machining process, allowing it to utilize larger tools effectively. This not only enhances compatibility with different materials, but also boosts the overall accuracy of the machining task.
Operating and Maintenance Tips for 2 Axis CNC Machines
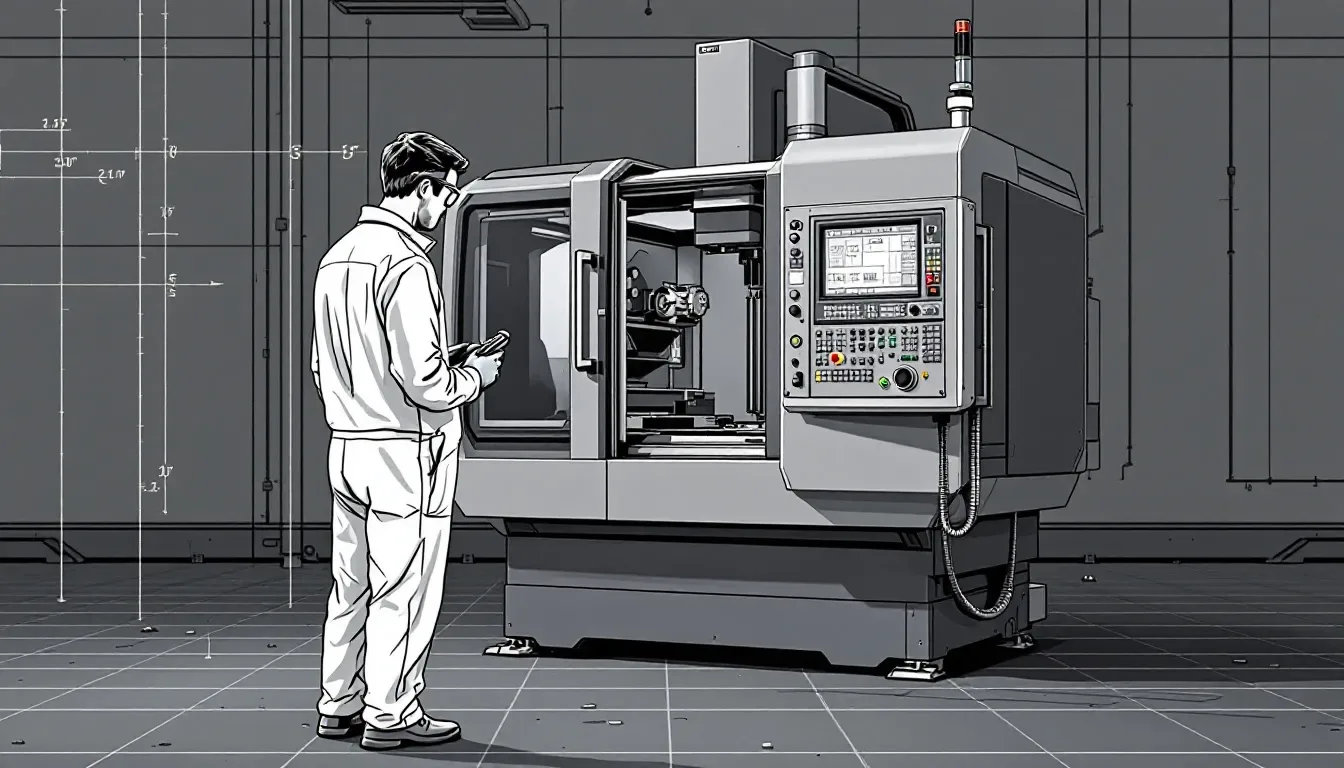
Efficient operation and maintenance of 2 Axis CNC Machines require regular calibration, proper tooling, and routine maintenance.
Detailed tips on these aspects follow.
Regular Calibration and Testing
Frequent calibration maintains the precision and accuracy of CNC machines. A calibration schedule every three to six months helps identify deviations before significant errors occur.
This practice keeps machines within production standards.
Proper Tooling and Setup
Proper tooling and setup ensure efficient and accurate machining operations. Regular inspection and cleaning can significantly extend the life of a 2 Axis CNC Machine. Post-use cleaning helps maintain optimal performance and longevity.
Correct setup of tools and workpieces directly impacts the quality and precision of the final product. Proper tooling minimizes errors and maximizes efficiency.
Routine Maintenance Practices
Regular upkeep extends the service life and dependability of 2 Axis CNC Machines. Ensuring that these machines are properly lubricated reduces wear, promoting seamless functioning. By routinely oiling the moving components, mechanical breakdowns can be avoided, thus boosting the efficiency of machining operations.
Adhering to a systematic maintenance routine aids in detecting possible problems promptly, which guarantees optimal performance from your equipment.
Summary
In summary, the 2 Axis CNC machine stands out as an essential tool in numerous sectors due to its exceptional precision, efficiency, and affordability. This guide has thoroughly delved into the crucial attributes of these machines along with strategies for selecting and maintaining the right model. Harnessing the capabilities of advanced manufacturing becomes attainable by integrating 2 Axis CNC technology into your processes, opening doors to enhanced possibilities.
Frequently Asked Questions
What are the main types of 2 Axis CNC Machines?
The main types of 2 Axis CNC machines are vertical, horizontal, and gantry machines, each offering distinct advantages for various applications.
Understanding these types can help you choose the right machine for your specific needs.
How do 2 Axis CNC Machines ensure precision and accuracy?
Utilizing stepper motors for regulated movements of the tool, 2 axis CNC machines deliver precision and accuracy. These machines also feature beds that are precisely aligned to ensure consistent machining.
The synergy of these components ensures that each project produced by a 2 axis CNC machine meets high standards of quality.
What industries commonly use 2 Axis CNC Machines?
2 Axis CNC Machines are commonly used in the aerospace, automotive, and consumer electronics industries for manufacturing complex and precise components.
What should I consider when choosing a 2 Axis CNC Machine?
When choosing a 2 Axis CNC machine, prioritize its capabilities, software compatibility, and the types of materials it can handle to effectively meet your requirements.
This will ensure you make an informed decision that aligns with your project needs.
How often should I calibrate my 2 Axis CNC Machine?
You should calibrate your 2 Axis CNC machine every three to six months to ensure optimal precision and accuracy. Regular calibration helps maintain the quality of your work and prolongs the lifespan of the equipment.
Still, need help? Contact Us: lk@lkprototype.com
Need a PROTOTYPE or PARTS machining quote? Quote now