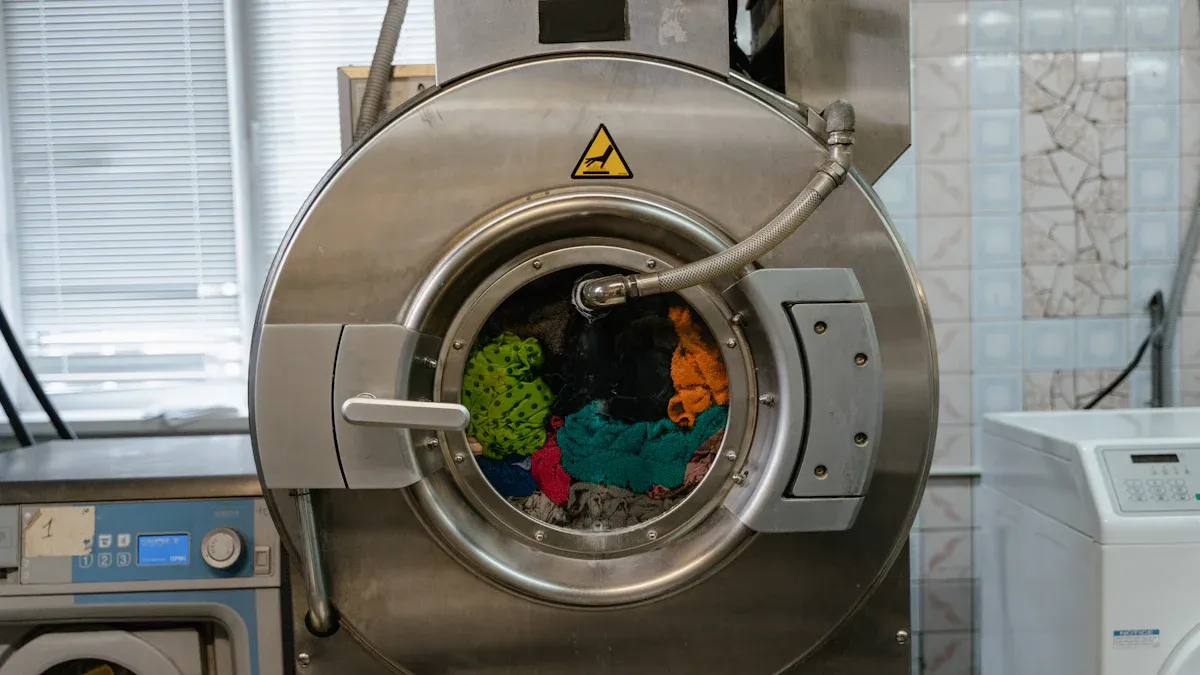
Vacuum casting uses silicone molds and vacuum chambers to make detailed parts. It is helpful for creating small batches that look like final products. This process makes prototypes very accurate and meets industry rules.
The vacuum casting market is growing fast. It was worth $1.5 billion in 2022 and may grow 7.5% each year until 2030. Industries like cars, planes, and healthcare use vacuum casting to make high-quality parts. It works quickly and saves money, so manufacturers like it for making precise parts fast.
Key Takeaways
Vacuum casting is great for making detailed models and small amounts. It saves money and works well for car and health industries.
The steps include making silicone molds, mixing materials, removing air bubbles, and casting in a vacuum to make high-quality parts with fewer mistakes.
Polyurethane resins and elastomers create strong, bendable, and heat-safe parts. These are used in things like medical tools and gadgets.
Letting the parts cure and removing them carefully is very important. This keeps the parts strong and stops damage to the mold.
Vacuum casting works well for small projects but has limits. Molds wear out, and it’s not good for making lots of items.
Vacuum Casting Process
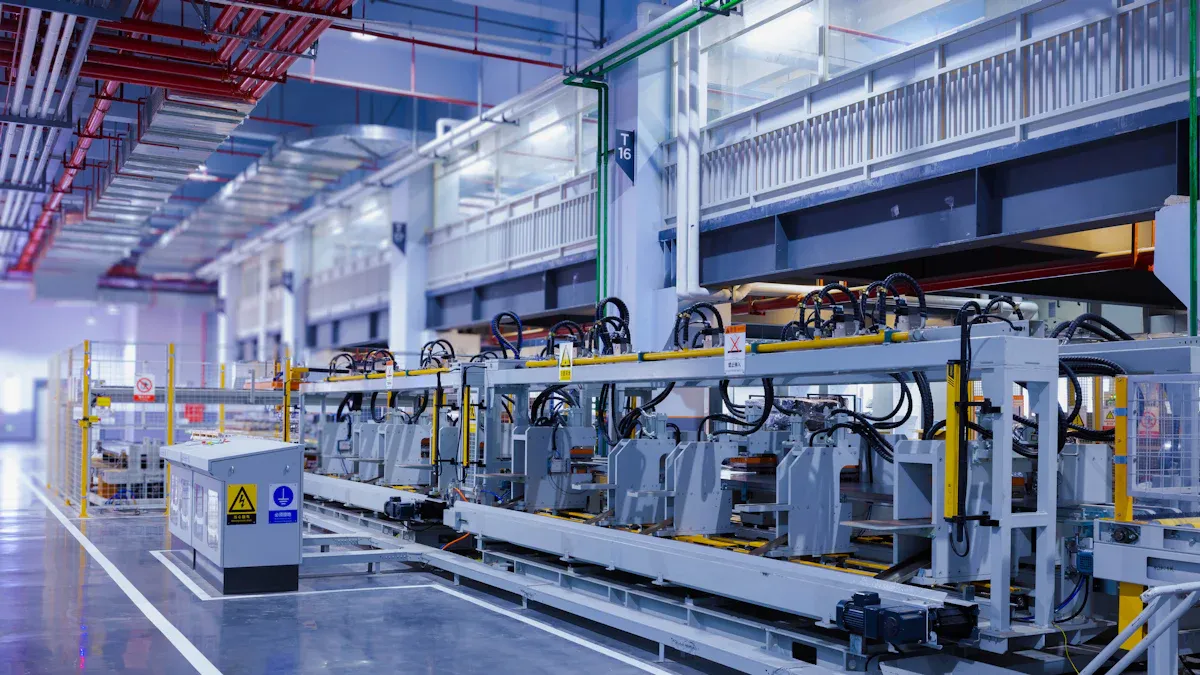
Mold Preparation
The first step is getting the silicone mold ready. A master model is made first, acting as a pattern for the mold. This model can be created using 3D printing, CNC machines, or other methods. Once the model is done, liquid silicone is poured around it to make the mold. Silicone is strong and bendable, so it captures tiny details well.
After the silicone hardens, the master model is carefully removed. This leaves a hollow space shaped like the model. The mold's surface can be adjusted to look shiny, dull, or smooth. But remember, silicone molds wear out after making 20-25 good parts and need replacing.
Tip: Make sure the mold walls are at least 0.75 mm thick. For better results, aim for 1.5 mm thickness.
Material Mixing and Degassing
Mixing the material is key for accurate vacuum casting. Usually, polyurethane resin is mixed with other ingredients to get the right properties. Polyurethane is popular because it’s strong, flexible, and heat-resistant.
After mixing, the material is degassed to remove air bubbles. This step ensures the final part is smooth and high-quality. Degassing is done by placing the material in a vacuum chamber. The low pressure pulls out trapped air.
Studies show using gases like argon during degassing improves part quality. But the process must be done gently to avoid defects. Proper degassing makes parts more accurate and reduces flaws in the finished product.
Casting Under Vacuum
Casting under vacuum is the main part of the process. After degassing, the material is poured into the silicone mold. The mold is placed in a vacuum chamber, where air pressure is lowered. This removes bubbles and helps the material fill every detail.
The vacuum chamber works at pressures between 20 and 100 mbar. For best results, the mold should reach 50 mbar in 0.5 to 1 second. This quick pressure change stops air pockets and helps the material flow evenly.
Once the mold is filled, the material starts to harden. Depending on the resin, curing can take hours. After curing, the part is removed, showing a detailed and precise product.
Note: Vacuum casting is great for custom projects needing accuracy and fast results. It’s a cost-effective way to make small batches between prototypes and mass production.
Curing and Demolding
Curing and demolding are the last steps in vacuum casting. These steps make sure the part is strong and safely removed.
Curing the Material
After pouring the material into the silicone mold, curing starts. This means letting the material harden and settle. To get better results, heat the mold to 40°C. The heat helps the material harden evenly and avoids problems. Depending on the resin or elastomer, curing takes 8 to 16 hours.
It’s important to wait during this step. If you rush, the material might not harden fully. This can make the part weak or less accurate. Always follow the instructions for curing time and temperature to get the best results.
Demolding the Part
When curing is done, it’s time to demold. This means taking the part out of the silicone mold. Gently pull the mold edges to avoid tearing or damage. For detailed molds, you might need to cut carefully to remove the part without harm.
Silicone molds are soft, so removing parts is easier. But handle the mold gently to make it last longer. Good demolding keeps the mold safe and the part smooth and detailed.
Tip: Check if the material is fully cured before demolding. Removing it too soon can ruin the part or leave marks in the mold.
Why Curing and Demolding Matter
These steps are very important for making good parts in vacuum casting. Proper curing makes the material strong and long-lasting. Careful demolding keeps the details and smooth finish of the part. Together, these steps help make vacuum casting a great way to create prototypes and small batches.
Materials in Vacuum Casting
Polyurethane Resins
Polyurethane resins are very useful for vacuum casting. They help make strong and accurate parts for testing and small production. These resins are tough, heat-resistant, and great for projects needing strength.
When using polyurethane resins, think about shrinkage and wall thickness. Shrinkage is about +0.15% because of heat changes. For small parts, walls should be at least 1 mm thick. Bigger parts need thicker walls for better results.
You can also choose different surface looks, like satin or matte. But sharp edges or tiny text might look a bit rounded after casting. Polyurethane resins are affordable and work well for making prototypes.
Description | Details |
---|---|
Tolerances | ± 0.015 inches per inch or ± 0.003, whichever is greater |
Shrinkage Rate | +0.15% due to thermal expansion |
Wall Thickness | Minimum 1 mm for small parts; larger parts require thicker walls |
Surface Quality | Satin or matte finishes achievable; internal features may show grow lines |
Feature Definition | Sharp corners and text may appear rounded |
Elastomers
Elastomers are stretchy materials perfect for vacuum casting. They are used to make seals, gaskets, and soft-touch parts. These materials fit well in silicone molds and show fine details while staying flexible.
Adding natural fibers, like sisal, makes elastomers stronger. This improves their stretch, tear resistance, and hardness. Reinforced elastomers are great for parts that face wear or heavy use.
Did you know? Adding fibers also makes elastomers last longer and stay flexible. This is important for making precise and durable parts in vacuum casting.
Elastomers are great for creating soft, strong parts that work well and look good.
Transparent Materials
Transparent materials are important for vacuum casting, especially when clarity is needed. They are used for lenses, covers, and parts where seeing through is key. These materials let light pass through easily, working well across many light ranges.
For example, indium tin oxide and carbon-based materials allow light between 300–1100 nm. This makes them useful in many industries. Transparent materials also work well with silicone molds, keeping details clear.
Material Type | Optical Transmittance | Wavelength Range |
---|---|---|
Indium Tin Oxide | High | 300–1100 nm |
Silver Films | Variable | Different wavelengths |
Gold Films | Variable | Different wavelengths |
Carbon-based Materials | Wide range | 300–1100 nm |
Carbon Nanotube Films | Varies with density | 300–1100 nm |
Transparent materials are key for making clear and detailed parts that meet both design and function needs.
Heat-Resistant Materials
Heat-resistant materials are important in vacuum casting for hot conditions. These materials are great for industries like cars and planes. Parts in these fields often face very high temperatures.
A common choice is heat-resistant polyurethane resin. This resin stays strong and keeps its shape in heat. It’s used for making engine covers, heat shields, and other hot-area parts.
Another option is silicone-based elastomers. These materials handle heat well and stay flexible. They are perfect for seals, gaskets, or parts that need to bend and resist heat.
Tip: Always check the highest temperature a material can handle. This helps ensure it works well for your needs.
Special composites are also heat-resistant. They mix strong fibers with resins to last longer. These are ideal for parts needing strength and heat resistance.
Material Type | Max Temperature Tolerance | Common Uses |
---|---|---|
Polyurethane Resin | Up to 150°C | Engine covers, heat shields |
Silicone Elastomers | Up to 250°C | Seals, gaskets |
Fiber-Reinforced Composites | Up to 300°C | Aerospace components |
Using heat-resistant materials makes sure your parts survive tough conditions. This makes vacuum casting a good way to create strong and useful prototypes.
Applications of Vacuum Casting
Automotive Industry
Vacuum casting is very important in making car parts. It helps create strong and precise parts like dashboards and bumpers. These parts improve how cars work and keep them safe.
This process is great for testing designs before mass production. It works well for small batches, letting companies meet customer needs quickly.
Evidence Type | Description |
---|---|
Importance of High-Quality Components | Strong car parts last longer, work better, and make driving safer. |
Market Dynamics | Vacuum casting offers precision, small batch options, and fair costs for car makers. |
Using vacuum casting saves money while keeping car parts strong and reliable.
Aerospace Sector
The aerospace field depends on vacuum casting for light and strong parts. It’s used to make detailed items like air ducts and fuel system parts. These need to be very accurate and consistent.
Vacuum casting makes lightweight parts that meet safety rules.
The growing aerospace industry increases the need for this technology.
It creates detailed parts, which are key for planes and spacecraft.
This method ensures aerospace parts are safe and perform well. Its ability to make custom, detailed items is vital for this industry.
Consumer Goods and Electronics
Vacuum casting has changed how gadgets and electronics are made. It helps create detailed parts for small and complex devices.
Precision and Detail: It makes parts with tiny details, perfect for electronics.
Material Versatility: Many materials can be used, like those similar to plastic or rubber.
Cost-Effective Prototyping: It’s a cheap way to make test models and small batches.
Quick Turnaround: Prototypes can be ready in about a week.
Prototyping and Testing: It helps make test models to check designs before production.
Custom Enclosures: It creates precise cases to protect electronic devices.
Connector and Component Manufacturing: Small parts made this way work reliably.
For wearable tech, vacuum casting is used for smartwatches and fitness trackers. It helps make light, strong, and comfy parts quickly and in small amounts.
Vacuum casting shows its value in making consumer goods and electronics. It lets companies create new products with speed and accuracy.
Medical Devices and Equipment
Vacuum casting is very important in making medical parts. It helps create accurate and dependable components for tools and machines. This method works well for testing designs and making small batches where precision matters.
Why Vacuum Casting is Important for Medical Use
Medical tools need parts that follow strict rules. Vacuum casting makes detailed and consistent parts, perfect for complex designs. It’s used to make items like surgical tools, prosthetics, and diagnostic equipment.
Here’s why vacuum casting is popular in medical manufacturing:
Accuracy: It creates parts with fine details and exact sizes.
Material Versatility: You can pick materials that are safe and easy to clean.
Cost Efficiency: It saves money for testing and small-scale production.
Quick Turnaround: Prototypes can be made in just a few days.
Tip: Always choose materials that meet medical safety standards for the best results.
Common Uses in Medical Devices
Vacuum casting is used in many medical areas. Here are some examples:
Prosthetics and Orthotics
Vacuum casting makes strong and light prosthetic limbs. It allows custom designs for a perfect fit. Braces and supports also benefit from this process.Surgical Instruments
Surgical tools need to be very precise. Vacuum casting makes tools with smooth surfaces and exact shapes, ensuring they work well during surgery.Diagnostic Equipment
Parts for devices like imaging machines and blood testers need high-quality materials. Vacuum casting ensures these parts meet strict standards.Medical Enclosures
Cases for medical devices must be tough and light. Vacuum casting creates strong, detailed enclosures using durable materials.
Materials Used in Medical Vacuum Casting
Picking the right material is key for medical parts. Materials must be safe, strong, and able to handle cleaning. Common choices include:
Material Type | Key Features | Common Uses |
---|---|---|
Biocompatible Resins | Safe for human contact | Prosthetics, surgical tools |
Transparent Polyurethanes | Clear and durable | Diagnostic equipment covers |
Heat-Resistant Elastomers | Withstand sterilization temperatures | Medical enclosures, seals |
Note: Always check if the material meets medical rules before using it.
Benefits of Vacuum Casting in Medical Manufacturing
Vacuum casting has many advantages for making medical parts:
Customization: Parts can be designed to fit each patient’s needs.
Speed: Prototypes are made quickly, helping improve designs faster.
Quality: The process creates smooth and detailed parts.
These benefits make vacuum casting a trusted choice for medical manufacturing.
Challenges to Keep in Mind
Even though vacuum casting is useful, there are challenges:
Material Limitations: Not all materials are safe for medical use.
Durability: Silicone molds wear out after making several parts.
Regulatory Compliance: Make sure all materials and steps follow medical rules.
By solving these issues, you can make the process work even better.
Callout: Vacuum casting is a key step between testing and production, helping create new medical devices.
Advantages and Limitations of Vacuum Casting
Advantages of Vacuum Casting
Vacuum casting has many benefits for making parts. It creates very detailed and accurate pieces. This helps prototypes look like real products, making testing easier.
The process is also affordable for small amounts. Unlike other methods, it uses silicone molds, which are cheap and quick to make. This makes it great for creating a few parts without spending too much.
You can use many materials with vacuum casting. Options include resins, elastomers, and heat-resistant materials. This lets you make parts with different features, like strength or transparency.
Another benefit is the fast production time. Prototypes or small batches can be ready in just days. The process also reduces waste by using only the material needed for each part.
Tip: Choose vacuum casting for accurate, affordable prototypes or small batches with custom materials.
Limitations of Vacuum Casting
Vacuum casting has some downsides to think about. Silicone molds don’t last long. They can only make 20-50 parts before wearing out, so new molds are often needed.
Thick mold walls can cause problems. They might trap air bubbles during curing, which can ruin the parts. Even curing is important to avoid this issue.
Flaws in the master model or mold can also be a problem. Any mistake will show up in every part made. Checking the master model and mold carefully is very important.
Lastly, vacuum casting isn’t good for making large amounts. It works well for small batches but isn’t efficient for mass production.
Note: Think about your project’s needs and limits before using vacuum casting.
Vacuum casting is a trusted way to make detailed prototypes. It’s great for small production runs and uses flexible materials. This process is precise and affordable for making limited parts.
More people want lightweight cars and better electronics. This makes vacuum casting even more important. By 2025, the vacuum aluminum casting market could reach $2.5 billion. By 2033, it might grow past $4 billion. This shows how useful it is in modern manufacturing.
In the future, better materials and automation will improve vacuum casting. This technology will stay important for making accurate and creative prototypes.
FAQ
What is vacuum casting used for?
Vacuum casting is used to make test models and small batches. It’s great for cars, planes, and medical tools needing accuracy.
How long does the vacuum casting process take?
It usually takes 8 to 16 hours to finish. Heating the mold can make the curing step faster.
Can vacuum casting handle transparent materials?
Yes, it works well with clear materials. It’s often used for making lenses, covers, or see-through parts.
How durable are silicone molds in vacuum casting?
Silicone molds last for 20 to 50 uses before breaking down. Treat them gently to make them last longer.
Is vacuum casting cost-effective for large production runs?
No, it’s better for small amounts. For big projects, methods like injection molding work better.