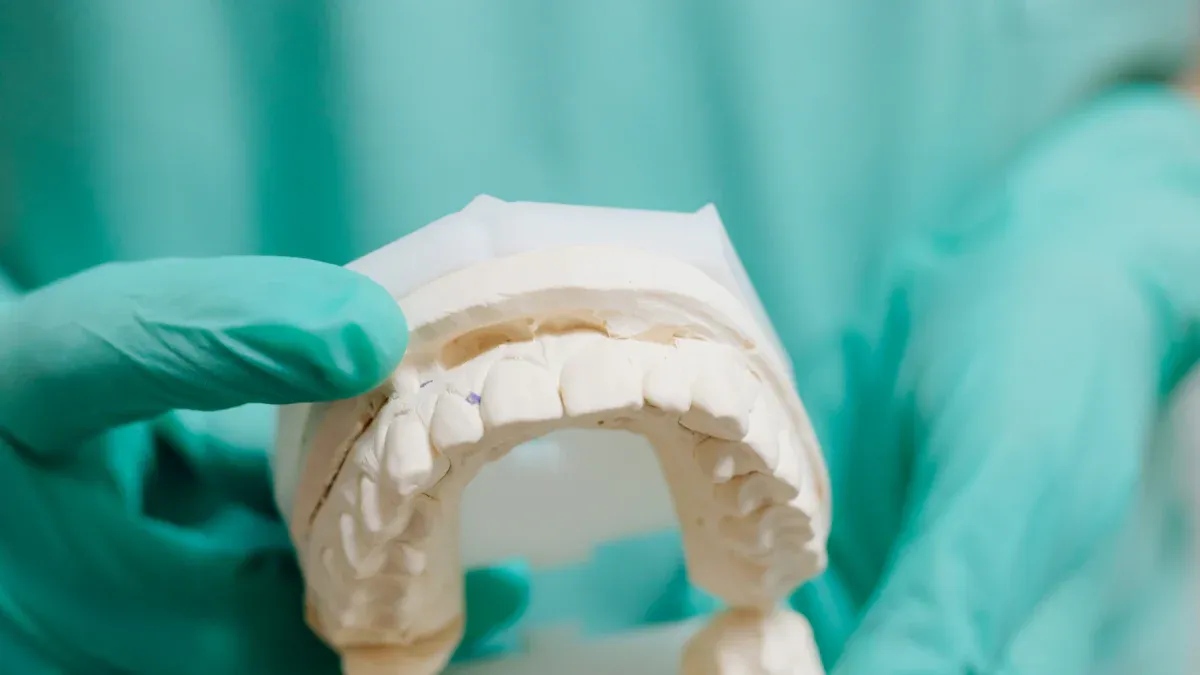
Urethane rubber casting is an effective method for creating flexible molds. These durable molds are crafted using liquid urethane rubber casting, making them ideal for replicating intricate designs with precision. The process achieves size tolerances within ±0.010” to ±0.020”, which, while less precise than injection molding, still delivers reliable results.
This technique is particularly beneficial for developing and testing new products. A single mold can produce 1–10 parts daily, depending on the type of urethane rubber casting used and the complexity of the part's design. The entire process, from start to finish, typically takes just a few weeks, making it a practical solution for small to medium production runs. It’s a cost-effective and time-saving option for manufacturers.
Key Takeaways
Urethane rubber casting is a cheap way to make flexible molds. It works well for small or medium production projects.
This method copies details very well, so it’s great for prototypes, machine parts, and art props.
Preparing materials correctly and letting them cure is very important. Always work in a dry place for the best results.
Urethane rubber is useful for many things, like car parts, movies, and factories.
You can reuse molds, which saves time and money. This makes urethane casting a good choice for both experts and hobbyists.
What is Urethane Rubber Casting?
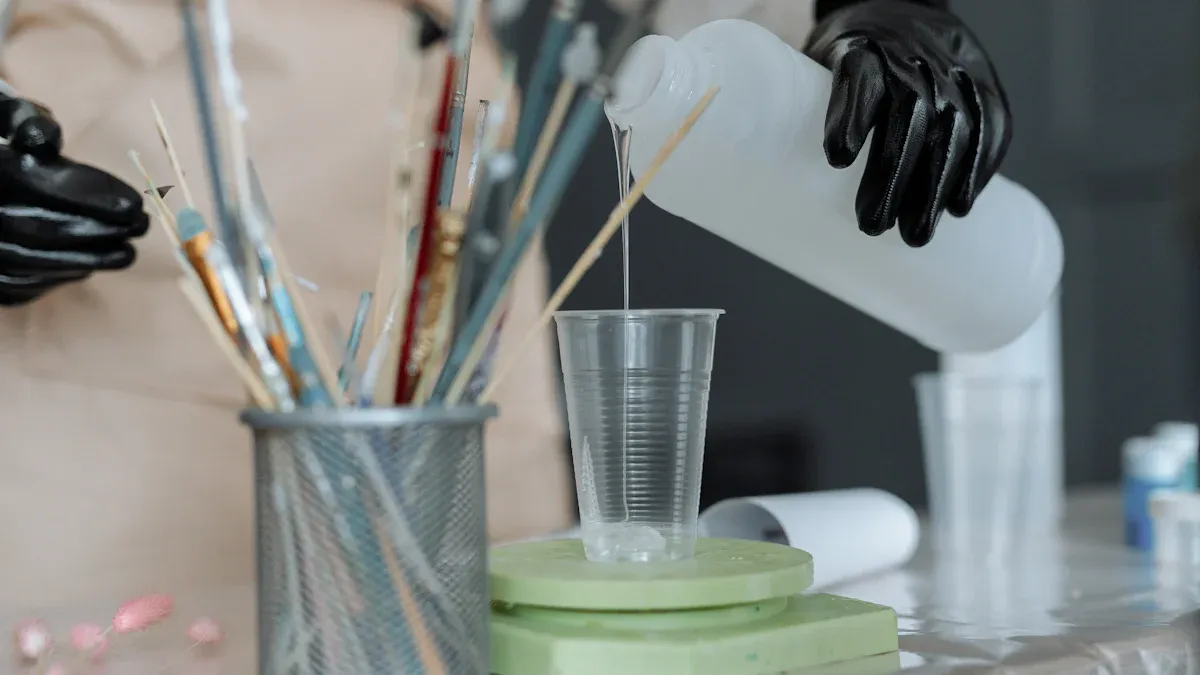
Definition and overview
Urethane rubber casting uses liquid polyurethane to make molds or parts. These molds are strong, flexible, and great for detailed designs. This process works well for making small to medium amounts of items. It copies fine details while keeping the material stretchy and tough. Many industries, like cars, building, and movies, use it because it’s useful and saves money.
Demand for urethane casting is growing worldwide. For instance, the market for cast polyurethane elastomers may rise from $8.43 billion in 2025 to $13.96 billion by 2034. This growth shows the need for lightweight and durable materials in many fields.
Key characteristics of urethane rubber
Polyurethane rubber has special traits that make it popular for casting. It’s strong like metal, flexible like rubber, and lasts like plastic. It resists oil, grease, scratches, and hits, so it’s good for tough jobs. Its stretchiness lets it keep its shape after many uses, making it last a long time.
These features make urethane casting great for parts that face rough conditions. Whether you need industrial parts or custom tools, polyurethane rubber works well and lasts.
Differences between urethane casting and other methods
Urethane casting is cheaper and more flexible than other methods. For small production runs, it costs less than injection molding. It also makes high-quality parts faster with good accuracy. Unlike CNC machining, which has limited design options, urethane casting handles complex shapes easily.
Here’s a simple comparison of urethane casting and other methods:
Casting Method | Cost | Speed | Design Options | Material Strength |
---|---|---|---|---|
Urethane Casting | High | Fast | High | Similar to plastics |
CNC Machining | Medium | Medium | Medium | Many material choices |
Injection Molding | Low (small runs) | Slow | Low | Stronger parts |
This table shows why urethane casting is a top choice. It’s affordable, quick, and flexible, making it perfect for prototypes and small batches.
How Does Urethane Rubber Casting Work?
Making the mold
The first step is to make a mold. A master pattern is designed as a template for the mold. This pattern can be made from wood, plastic, or metal. The material depends on how detailed and strong the mold needs to be. Silicone molds are often used because they are flexible and stable. They also reduce shrinking and copy details well from the master pattern.
To create the mold, liquid silicone resin is poured over the master pattern. Once it hardens, the mold is carefully removed. This leaves a hollow space that matches the original design. This mold is then used to cast polyurethane parts.
Tip: Make sure the master pattern is smooth and flawless. Any mistakes will show up in the mold and final cast.
Getting the polyurethane ready
After the mold is done, the polyurethane material is prepared. It comes in two liquids: resin and hardener. These are mixed in equal amounts, making it simple to measure.
Polyurethane has many benefits during preparation:
Benefit/Characteristic | What It Means |
---|---|
Low Viscosity | Fewer air bubbles when mixing. |
Mixing Ratios | Easy to measure, equal parts. |
Hardens quickly, ready in 20-30 minutes. | |
Green Stage | Can adjust while still soft, good for tricky molds. |
Ease of Use | Great for small projects and crafts. |
Compatibility | Works with fillers and colors. |
Health & Safety | Safer than some resins, but clear types can be risky. |
Memory Retention | Keeps shape during curing, allows small fixes. |
When mixing, stir gently to avoid air bubbles. For better results, use a vacuum chamber to remove trapped air before pouring.
Pouring the material into the mold
Once the polyurethane is mixed and bubble-free, pour it into the mold. Pour slowly and steadily to fill all parts of the mold. This helps capture fine details.
For very detailed designs, vacuum casting can be used. This method ensures smooth finishes and copies textures well. The quality of the master pattern also matters. A well-made pattern improves the mold’s detail and accuracy.
Note: Always pour in a clean space to avoid dirt or dust. This keeps the results consistent.
After pouring, the material starts to harden. During this time, the polyurethane can still be adjusted slightly. This is helpful for complex or multi-piece molds.
Curing the cast
After pouring polyurethane into the mold, curing starts. This step hardens the material and gives it final properties. Curing happens through a chemical reaction between resin and hardener. This reaction changes liquid polyurethane into a solid, flexible material. The curing time and temperature are very important for good results.
Key factors that affect curing include:
Temperature: Curing happens between 70 and 100°C. Higher heat makes curing faster, while lower heat slows it down.
Time: Curing can take 20 minutes to several hours. Some advanced systems cure in just 10 seconds.
Polyurethane concentration: Higher amounts lower the mold's maximum heat due to dilution.
Follow the manufacturer’s instructions for the best curing conditions. Use an oven or heat chamber to keep temperatures steady. Keep the mold dry, as moisture can ruin the curing process and weaken the material.
Tip: Watch the curing process carefully. Uneven curing can cause defects like warping or missing details.
Demolding and finishing
Once the polyurethane is fully cured, remove it from the mold. This step, called demolding, must be done gently to avoid damage. Flexible molds, like silicone ones, make this easier since they can be peeled away softly.
Steps for safe demolding:
Make sure the polyurethane is fully hardened. Press lightly to check if it’s firm and not sticky.
Carefully loosen the mold’s edges. Using a release agent can make this easier.
Slowly peel the mold away from the cast, starting at one corner.
After removing the cast, check for any small flaws. Fix issues like extra material or rough edges during finishing. Sanding, trimming, or polishing can improve the look and function of the part. If painting or coating, clean the surface first to remove dirt.
Note: Handle molds carefully during demolding. Reusable molds can make many casts, so keeping them in good shape saves time and money.
Finishing improves how your polyurethane cast looks and works. Whether for industrial parts or creative props, careful finishing ensures a polished, professional result.
Benefits of Urethane Rubber Casting
Cost-efficiency for low to medium production
Urethane rubber casting is a cheaper way to make parts. It uses reusable silicone molds instead of expensive tools. This lowers the starting costs a lot. You can make good-quality parts without buying pricey machines.
This method also saves time. One mold can make many parts daily. It’s great for testing designs or making small batches. For businesses or hobbyists, urethane casting is a smart and affordable choice.
Material versatility for various applications
Urethanes are very adaptable materials. They can be soft and bendy or hard and strong. This makes them useful in many industries, like cars or movies.
Soft urethanes are great for molds with tiny details. Silicone molds help copy even the smallest textures. This lets you make parts that look and work like injection-molded ones.
Why urethanes are great for casting:
Work well with fillers and colors for custom looks.
Can act like rubber or plastic.
Good for both useful and decorative items.
High durability and flexibility
Urethane rubber lasts a long time and bends easily. It doesn’t wear out or get damaged by oil or grease. This makes it perfect for tough jobs. Urethane parts keep their shape and work well over time.
Its flexibility means molds and parts won’t break after many uses. Whether for factory tools or creative props, urethane rubber stays strong and reliable.
Tip: Keep urethane materials dry and at a steady temperature for longer life.
Ability to copy fine details
A great thing about urethane rubber casting is how well it copies tiny details. Whether you’re making a model, decoration, or useful part, this method ensures every small texture or pattern is perfectly recreated.
Urethane rubber molds are both flexible and accurate. They can bend around tricky shapes and capture fine details from the original design. For instance, if your design has patterns like wood grain, fabric, or raised letters, urethane rubber copies them very clearly.
Tip: Always keep your original design clean and smooth. Any mistake on it will show up in the final product.
Why urethane rubber casting is great for detail work:
Low viscosity of the material: The liquid flows easily into tiny spaces, filling every part of the mold.
Compatibility with silicone molds: Silicone molds are very detailed and work well with urethane rubber, keeping designs sharp.
Controlled curing process: The material hardens without shrinking or bending, keeping the design true.
This makes urethane rubber casting perfect for art, building, and manufacturing. You can make lifelike props, detailed models, or molds for concrete and resin.
Note: For super precise projects, use vacuum casting. It removes air bubbles and improves surface quality.
With urethane rubber casting, you can create even the most detailed designs. Its accuracy and dependability make it a top choice for fine work.
Limitations of Urethane Rubber Casting
Sensitivity to moisture during curing
Urethanes react badly to moisture while curing. Even tiny water amounts can mess up the chemical reaction. This may cause bubbles, weak areas, or incomplete hardening. To prevent this, work in a dry space and keep materials free of moisture.
Store urethane materials properly to avoid problems. For example:
TPU resins must have less than 0.02% moisture before use.
Keep TPU in a cool, dry place below 30°C.
Too much moisture can ruin the material and make casting harder.
By keeping moisture levels low, you’ll get better results and longer-lasting molds.
Limited shelf life of materials
Urethane materials don’t last forever. You need to use them quickly. Air, heat, or humidity can make them go bad over time. Proper storage is very important.
To keep materials in good shape:
Seal them tightly in containers.
Store them in a cool, dry place.
Keep them away from sunlight and high heat.
If stored wrong, materials may lose quality. This can lead to bad casts or wasted supplies.
Potential for shrinkage or deformation
Shrinkage or bending can happen while curing due to heat. Urethanes are easier to work with than injection molding but still need careful planning. Wall thickness, mold shape, and heat control affect the final product’s accuracy.
Thicker molds may shrink unevenly because of extra heat. The chemical reaction creates heat, which can change the mold’s size. But urethane casting is more flexible and avoids major shrinkage compared to injection molding.
To reduce these problems, design molds with even wall thickness and good angles. This helps spread heat evenly and lowers the chance of bending.
Tip: Test your mold design first to spot shrinking or bending issues before making many casts.
Applications of Urethane Rubber Casting
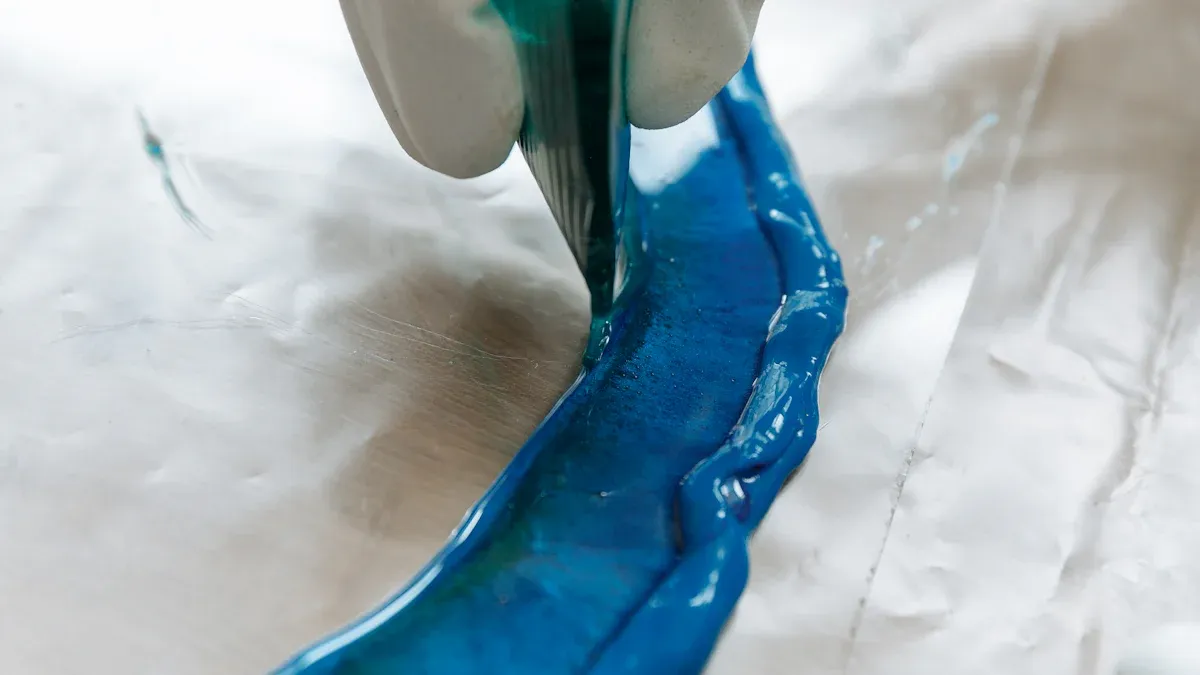
Prototyping and product development
Urethane rubber casting is great for making prototypes fast. It helps test designs without spending too much money. This method is perfect for creating car prototypes that need to be strong and precise. You can copy small details and make parts that act like injection-molded plastics.
This process lets you try different designs and materials. For instance, you can make soft or hard prototypes based on your needs. This flexibility makes it useful for industries like cars, electronics, and consumer products where speed and creativity matter.
Tip: Use urethane rubber casting to improve your prototypes. Make sure they meet your design goals before mass production.
Industrial components and machinery parts
Urethane rubber casting works well for tough industrial parts. It resists wear, chemicals, and heat, making it good for hard jobs. You can create parts that handle impacts and rough conditions, lasting a long time.
This method costs less and is faster than older manufacturing ways. You can make custom tools, fixtures, or replacement parts easily. Urethane rubber can be shaped into many forms and sizes, making it very useful for factories.
Why urethane rubber casting is great for industrial parts:
Combines rubber and plastic traits for better performance.
Handles tough jobs in high-stress places.
Makes strong parts that last over time.
Using urethane rubber casting can save time and improve production. It’s a smart choice for keeping your operations running smoothly.
Mold making for concrete, plaster, or resin
Urethane rubber casting is excellent for making molds for concrete, plaster, or resin. Its flexibility and strength help copy detailed designs perfectly. Whether you’re making concrete stamps or resin molds, urethane rubber gives consistent results.
Different urethane rubbers work for different molds. Softer rubbers are good for tricky shapes, while harder ones are better for flat or strong molds. Here’s a table showing some popular options:
Product Name | Working Time | Demold Time | Hardness (Shore A) | Application |
---|---|---|---|---|
75-80 RTV Liquid Urethane Mold Rubber | 45 Minutes | 24 Hours | 80 | Best for flat molds with little detail, good for concrete stamps. |
74-30 RTV Liquid Urethane Mold Rubber | 30 Minutes | 24 Hours | 30 | Great for flexible molds with detailed shapes. |
75-60 RTV Liquid Urethane Mold Rubber | 15 Minutes | 12 Hours | 60 | Medium hardness, good for molds needing some flexibility. |
75-90 RTV Liquid Urethane Mold Rubber | 10 to 15 Minutes | 24 Hours | 90 | Hardest type, best for strong concrete molds. |
Polygel 35 Self Thickening RTV Liquid Urethane Rubber | N/A | Overnight | N/A | Ideal for brush-on molds for plaster or wax. |
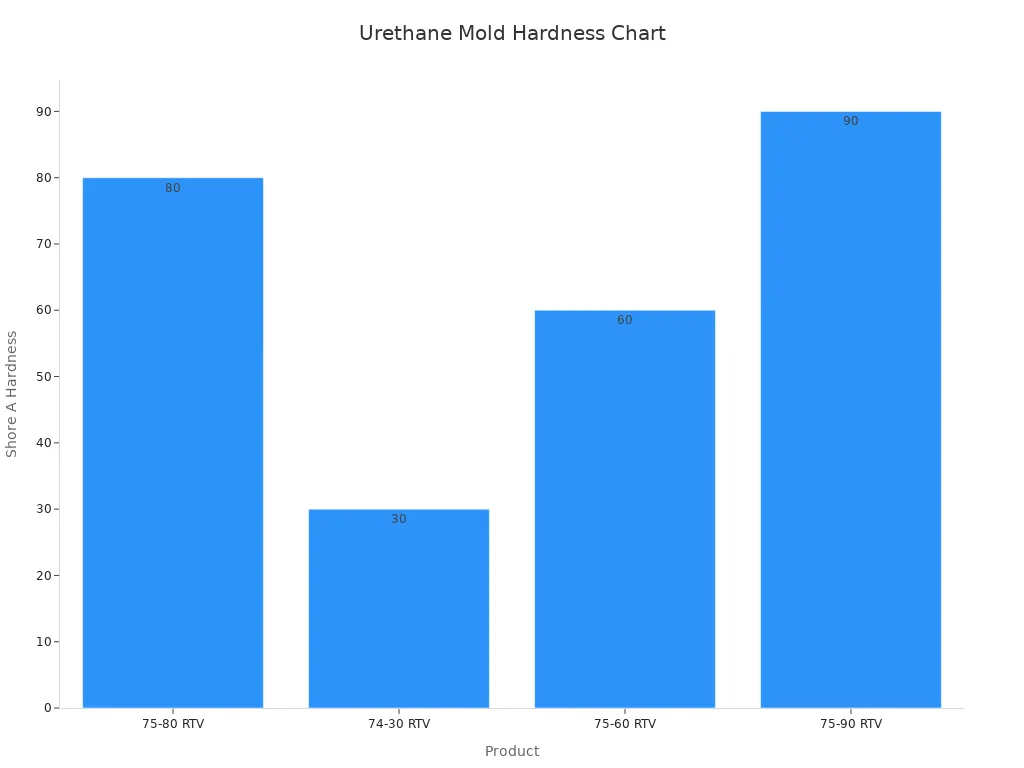
Urethane mold rubbers are great for copying details and lasting a long time. Artists, builders, and manufacturers love them for their projects.
Note: Pick the right urethane rubber for your mold’s shape and the material you’ll cast.
Special effects and props in entertainment
Urethane rubber casting is key for making movie and theater props. It helps create realistic replicas, flexible molds, and strong props for repeated use. This method copies tiny details, like skin textures, scales, or fabric patterns, perfectly.
For example, you might need a mask with wrinkles or a prop weapon with designs. Urethane molds capture these details, making the final product look real. The material is lightweight but strong, so props are easy to handle during filming or performances.
Why urethane rubber casting works well for entertainment:
Realistic textures: Copies small details for lifelike props.
Durability: Props last long, even with heavy use.
Versatility: Works with materials like resin, foam, and plaster.
Tip: Start with a high-quality master pattern. A good pattern ensures the mold captures every detail.
Whether for a big movie or a school play, urethane rubber casting brings ideas to life. Its precision and flexibility make it a favorite for entertainment projects.
Custom tools and fixtures for manufacturing
In factories, urethane rubber casting is great for making custom tools. It’s perfect for small jobs where other methods cost too much or take too long. You can design molds to create tools that fit specific needs.
For instance, you might need a tool to hold odd-shaped parts during assembly. Urethane molds make precise tools that fit well and don’t break. The material’s flexibility lets tools adjust to different shapes without damage.
Benefits of urethane rubber casting in manufacturing:
Cost-effectiveness: Reusable molds save money on tools.
Customization: Make tools that match exact needs.
Durability: Tools stay strong after many uses.
Note: Store molds in a cool, dry place to keep them lasting longer.
Using urethane rubber casting in manufacturing saves time and money. It helps create reliable tools and fixtures that meet your exact needs.
Urethane rubber casting is a smart way to make strong, bendable molds and parts. This process includes steps like making molds, pouring materials, and finishing. It’s useful because it saves money, works with many designs, and copies tiny details well. Many industries, like factories, movies, and building, use this method.
Tip: Try urethane rubber casting for your next project. It’s great for making prototypes, molds, or special tools. This method is quick, dependable, and cost-effective.
Its flexibility makes it a great choice for both experts and hobbyists.
FAQ
How should you store urethane rubber materials?
Keep urethane rubber in sealed containers in a cool, dry spot. Avoid sunlight and moisture to keep the materials in good shape. Storing them properly helps them last longer and work better.
Tip: Follow the maker’s storage instructions for the best results.
Can urethane rubber molds be reused?
Yes, you can use urethane rubber molds many times. They are strong and flexible, so they keep details after several uses. Be gentle when removing casts to prevent damage.
Note: A release agent can help molds last longer.
How can you stop air bubbles in the cast?
Stir the resin and hardener slowly to avoid bubbles. Use a vacuum chamber to remove trapped air before pouring. Pour the mix steadily to get a smooth, bubble-free cast.
Is urethane rubber casting safe?
Urethane rubber casting is safe if you follow safety rules. Wear gloves and work in a ventilated space to avoid touching or breathing fumes. Some materials need extra care, so read the safety sheet first.
Can you add color to urethane rubber casts?
Yes, you can mix pigments or dyes into the liquid urethane. This lets you make casts in custom colors. Check that the color works with the urethane for the best results.
Tip: Test a small amount first to see the color.