If you’re navigating the world of product development, understanding the various rapid prototyping types is essential. From proof-of-concept and low-fidelity to high-fidelity, looks-like, and works-like prototypes, each type serves a unique function in design and testing. This article breaks down these types and shows you when and how to use them effectively.
Key Takeaways
Rapid prototyping is essential in product development, enabling quick iterations and varying levels of fidelity to validate design and functionality effectively.
Different types of prototypes, including low-fidelity, high-fidelity, works-like, and looks-like, serve specific purposes in the development process, from concept validation to final testing.
Material selection and the use of advanced prototyping techniques, such as 3D printing and laser sintering, are critical to producing high-quality prototypes that accurately represent the final product.
Overview of Rapid Prototyping Types
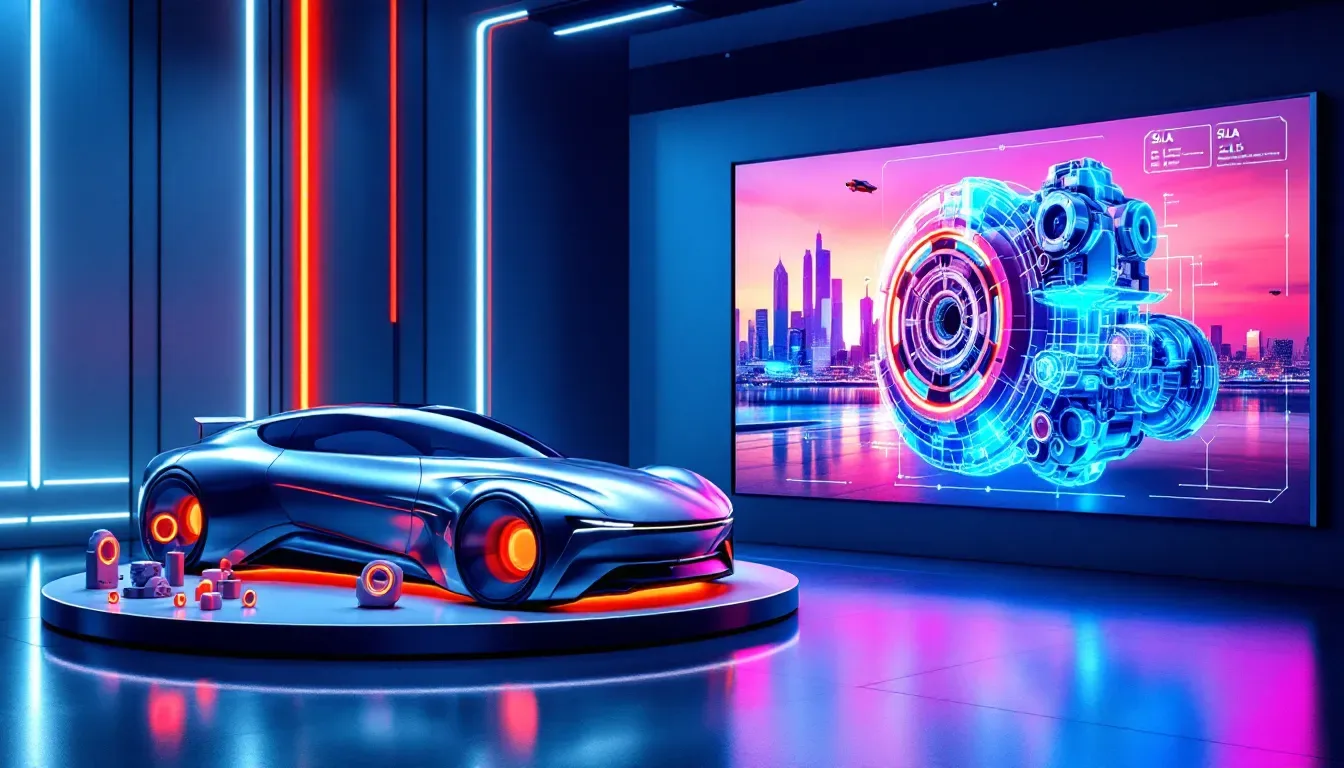
Rapid prototyping plays an integral role in the contemporary arena of product development, characterized by the expedited fabrication of a rapid prototype utilizing computer-aided design software. This technique is pivotal for confirming that both aesthetic and practical aspects of a product adhere to required specifications prior to its transition into mass production. The adaptability inherent in rapid prototypes makes them particularly useful across different scopes of work, ensuring their effectiveness irrespective of project or design diversity.
The automotive, aerospace, healthcare, and consumer electronics industries have greatly benefited from advancements in rapid prototyping. It has enabled these fields to accelerate the innovation cycle by facilitating prompt modifications and enhancements during development stages. With a spectrum that spans from basic low-fidelity sketches to intricate high-fidelity models, various types of rapid prototypes offer tailored levels of detail and functional capacity for distinct requirements.
Gaining insight into each type’s particular applications within the product development process is vital when choosing an appropriate method for your endeavor. Whether you seek a rudimentary proof-of-concept prototype for initial idea assessment or require advanced models designed to evaluate user engagement thoroughly, every category fulfills its own special niche within this methodology. In this guide we will explore such diverse types, focusing on how they can be strategically utilized based upon their respective advantages.
Proof-of-Concept Prototypes
In the early phases of product development, proof-of-concept prototypes play a critical role. They are crafted to test and affirm initial concepts and hypotheses, determining whether the product idea is worth pursuing prior to committing extensive resources into its full-scale development. The central objective of a proof-of-concept prototype is not only to show that an idea can be actualized, but also to provide a physical model for stakeholders’ assessment.
Constructed with simplicity in mind, these prototypes focus solely on emulating the functionality of the intended product rather than perfecting its design—a distinct characteristic setting them apart from subsequent stages in prototyping processes. This method facilitates prompt user feedback since individuals tend to be more open when discussing preliminary versions.
Focusing meticulously on functionality, how it will be manufactured, and market acceptance is paramount when validating designs effectively through proofs of concept. Engaging in this practice enables teams to pinpoint and correct defects at an early stage or even discard ideas that prove impractical—thus crucially shaping decision-making during development. Such preemptive checks are vital for aligning products with real-world consumer needs while averting expensive modifications later on as projects advance towards completion.
Low-Fidelity Prototypes
Simplistic in nature, low-fidelity prototypes emphasize the basic contours and structure of a product. These initial representations serve as the preliminary visual drafts that aid in evaluating early design ideas, laying down groundwork for subsequent detailed versions. Crafted through rudimentary paper sketches or elementary digital wireframes, these prototypes capture fundamental layouts without engaging with complex details.
The cost efficiency and simplicity of crafting low-fidelity prototypes stand out as their main benefits. Design groups can swiftly cycle through modifications and polish concepts without sinking substantial resources or time into development at this stage. This characteristic renders them particularly suitable for use during the nascent phase of the design process when exploring varied options and soliciting early-stage user feedback is paramount.
Although uncomplicated, low-fidelity prototypes are vital within the prototyping trajectory. They pinpoint significant flaws at an embryonic stage to avoid expensive overhauls along in development. By offering an elemental visual guide, they afford stakeholders a glimpse into the tentative direction of the project’s design, allowing them to contribute insightful feedback prior to progressing towards more intricate and fully operational prototypes.
High-Fidelity Prototypes
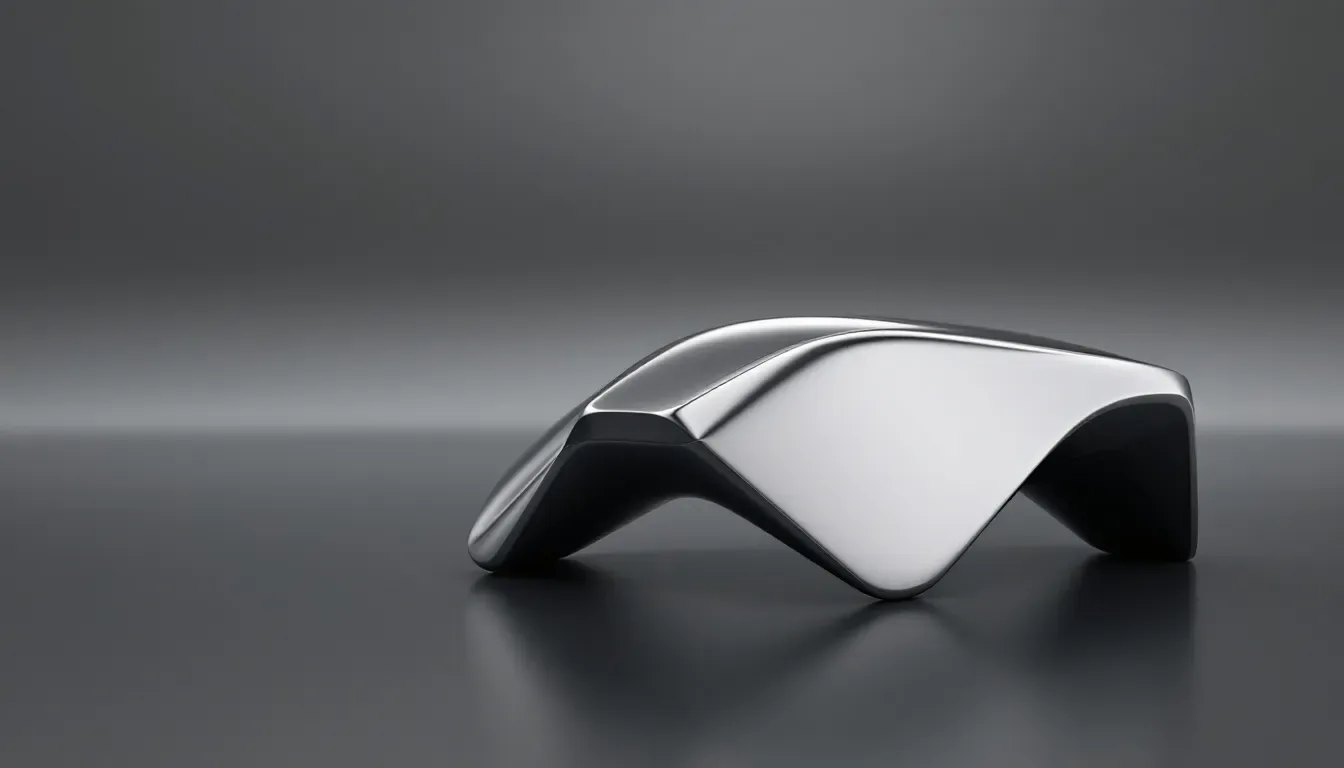
High-fidelity prototypes are sophisticated, highly detailed simulations that mimic the final product’s appearance and behavior. They play a crucial role in assessing user interfaces and actions by offering end-users an authentic interaction with them. With advanced visual elements and genuine content, these prototypes gather valuable insights from users to refine the usability testing phase.
The key advantage of employing high-fidelity prototypes lies in their capacity to preempt expensive errors. Along the product development path. Through these elaborate interactive representations, design crews can detect and rectify possible flaws promptly. This minimizes repeated revisions, thus accelerating the entire cycle of product creation.
Prior to initiating mass production processes, developers and engineers use high-fidelity prototypes as benchmarks for confirming how products will function. These models facilitate cooperative efforts within teams through immediate visualization opportunities concerning design plans. In essence, high fidelity prototypes act as pivotal conduits transitioning projects from idea stages all the way to completion while ensuring conformity with both aesthetic standards and operational specifications.
Looks-Like Prototypes
Prototypes often prioritize visual aspects of a product, concentrating on its aesthetics. These models, sometimes referred to as appearance prototypes, are crafted to embody the final product’s dimensions, form and key structural characteristics visually. Although they lack mechanical functionality, their foremost objective is to depict the aesthetic design.
Utilized for demonstrating the product’s visual appeal to stakeholders and prospective clients, these looks-like prototypes serve as physical exemplars of the item’s style and texture. They play an important role in soliciting feedback about the design overall so that any necessary modifications can be made before finalization. This phase is critical in making sure that the end-product resonates with both user expectations and intended aesthetic qualities.
In spite of not being tailored to functional testing activities, looks-like prototypes are central within rapid prototyping processes. They lay groundwork for enhancing how a product appears and verify adherence against established criteria pertaining to both visuals and ergonomics prior production stages set forth by companies or entrepreneurs seeking market penetration success. Positioning strong visual identities at the forefront through focused attention on stylistic components during early development phases is imperative for achieving such outcomes.
Works-Like Prototypes
Prototypes that focus on operational capabilities, known as works-like prototypes, aim to replicate the core functions of a product rather than its aesthetic features. These prototyping iterations concentrate on assessing and validating how well mechanical and technical elements perform by incorporating vital systems like electrical, mechanical, and thermal components for thorough testing.
The central objective with works-like prototypes is to verify that products operate correctly in practical situations. This aspect of the prototyping process is indispensable for uncovering potential functional flaws early on, allowing for modifications prior to commencing mass production. Concentrating on functionality at this phase helps confirm that all technical specifications and performance criteria are satisfactorily met.
Within the realm of rapid prototyping processes, works-like prototypes significantly contribute to evaluating true product performance. By substantiating key mechanical and technical attributes early in development stages through such models, design teams gain valuable insights enabling them to polish their designs according to user demands and standards. Their inclusion is pivotal not just for fine-tuning purposes, but also assuring dependability and function in the end product.
Engineering Prototypes
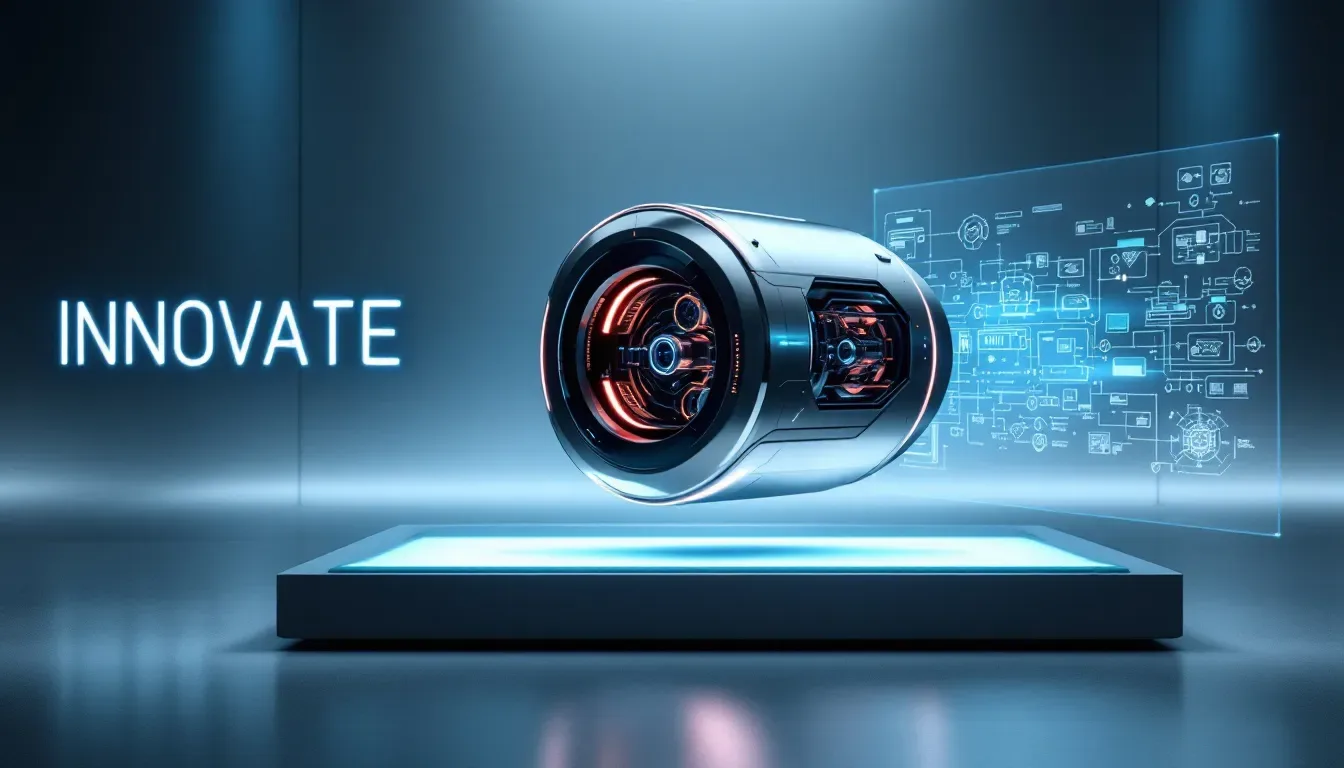
Prototypes in engineering are pivotal for evaluating a product’s structural integrity, its viability in manufacturing, and the efficiency of its assembly procedures. Such prototypes play an indispensable role in verifying that the end-product can be produced with ease while complying with all relevant industrial norms within the production cycle. For components made up of multiple pieces, it is essential to account for appropriate tolerances to facilitate seamless integration.
Rapid prototyping technology significantly impacts the creation of engineering prototypes by swiftly transforming digital models into tangible parts. Rapid prototyping is instrumental in uncovering potential issues related to manufacturability early on and aids in confirming design accuracy before proceeding to extensive production runs. This verification stage through rapid prototyping helps prevent costly postponements and modifications by ensuring that any major obstacles are addressed beforehand.
Engineering prototypes serve as a crucial checkpoint for validating both design specifications and functional requirements necessary for ensuring quality assurance standards are met prioritizing manufactureability and simplification of assembly processes. These preliminary versions help optimize subsequent stages within the manufacturing workflow guaranteeing high-quality results consistent with industry expectations—setting the groundwork vital for initiating reliable mass production without hindrances linked to effectiveness or conforming output standards during scalability efforts.
Validation Testing and Manufacturing Prototypes
Prototypes used for validation testing are crafted to mimic the final product closely, guaranteeing they fulfill all necessary specifications before proceeding with large-scale manufacturing. Employed for limited production runs, unique custom solutions, and specific sub-assembly applications, these prototypes accommodate particular demands within the development stage. Through extensive testing enabled by validation testing prototypes, manufacturers can confirm that their products will operate effectively and dependably.
The importance of 3D printing in the realm of validation testing cannot be overstated as it allows for swift and effective fabrication of physical models. This innovative method is instrumental in evaluating design tolerances and verifying a concept’s practicality to certify compliance with requisite standards ahead of initiating mass production processes. To 3D printing, vacuum casting is commonly utilized to create plastic and rubber parts vital for functional trials aimed at confirming prototype performance adequacy.
Choosing appropriate materials when creating validation testing prototypes is pivotal since material characteristics should emulate those planned for final assembly resins as closely as possible. By doing so, designers ensure that these early representations accurately exhibit how the end-product would function under real-world conditions—making this phase indispensable for certifying fulfillment of requirements while also promoting efficient manufacture.
Rapid prototyping instruments empower designers and engineers not just in enhancing their offerings but also in swiftly addressing any emerging problems during ongoing production cycles. Validation test prototypes play an integral part by providing a concrete depiction of what’s envisioned ensuring alignment between initial designs against functionality demands—a proactive measure averting costly changes or setbacks. Down the line.
Material Selection for Rapid Prototyping
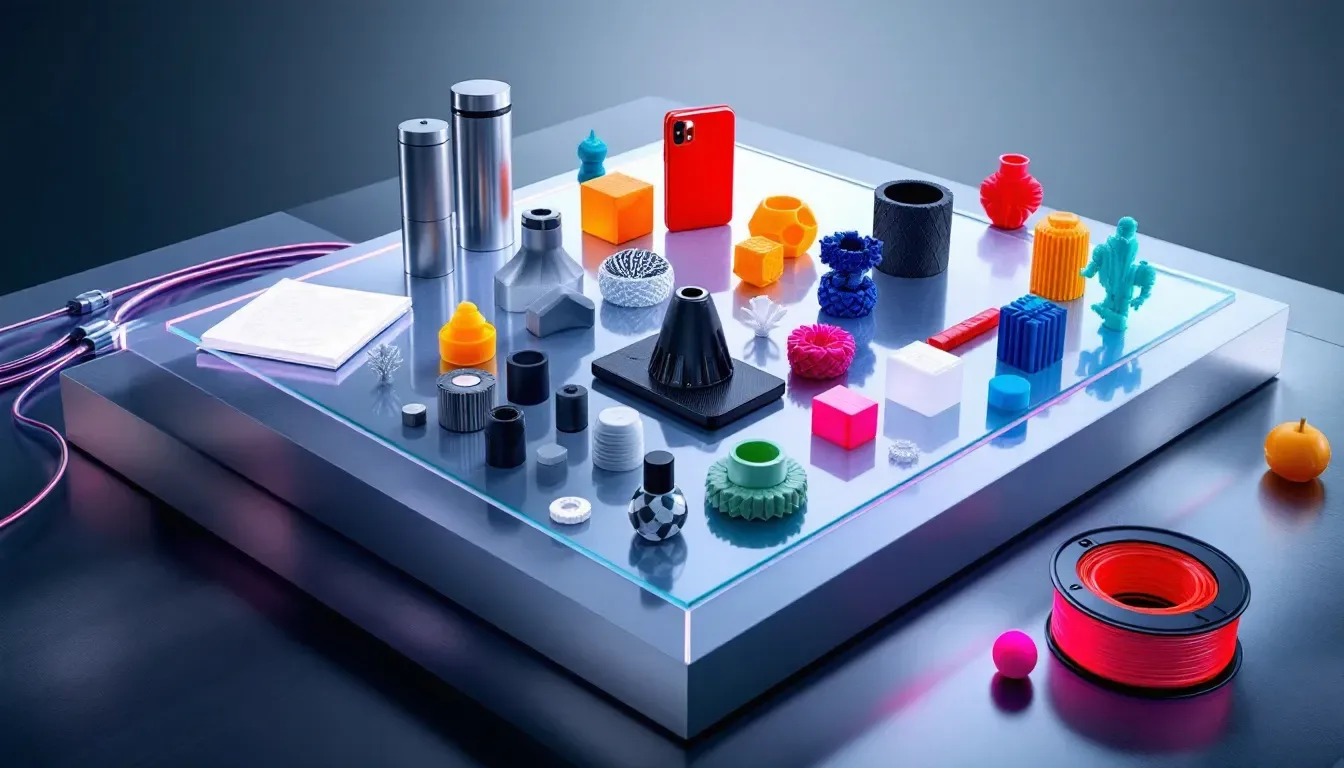
The selection of materials is a vital element in the rapid prototyping process, with choices hinging on specific requirements such as durability and pliability. The use of advanced materials allows engineering prototypes to simulate the characteristics of final production components, providing an accurate evaluation of how the end product will perform.
Prior to choosing:
When picking out materials for functional prototypes, it’s essential to focus on traits like resistance to scratches and distortion. For prototypes that need efficient heat management or dissipation, selecting materials with superior thermal conductivity is critical. The surface finish quality greatly influences both aesthetic appeal and functionality when considering material options.
Subsequent considerations should include:
Materials for functional prototype construction must be chosen based on factors such as:
Scratch and deformation resistance
Thermal conductivity levels suited for heat control
Surface finish quality which heavily impacts visual charm and practicality
Grasping how different materials react thermally is imperative in preventing any warping during temperature fluctuations. Typical resources utilized for crafting appearance-focused prototypes encompass items like cardboard, clay, as well as 3D-printed elements—selected according to cost consideration, timing needs, and anticipated visual effects. The adoption of eco-friendly substances also plays a more prominent role within rapid prototyping endeavors due to growing ecological awareness.
To ensure that physical models are relevantly representative. Mirroring properties found in intended production resins when choosing prototype material can prove beneficial towards achieving this goal effectively. Through meticulous contemplation over these attributes alongside project specifications, designers can fabricate high-caliber mockups accurately reflecting what’s envisioned for their ultimate creation.
Role of Software in Rapid Prototyping
The role of software in the rapid prototyping process is crucial. Computer-Aided Design (CAD) software enables the creation of intricate 3D models that are pivotal for producing precise and operational prototypes, which can undergo evaluation and improvement throughout their development.
Prototypes benefit from simulation software that permits virtual trials and assessments, allowing designers to gauge how a prototype will perform prior to initiating physical production. By discovering potential flaws early on in the product development cycle with this technology, expensive modifications are minimized and conformity with all necessary specifications is more likely.
Slicing software plays an important role in transforming 3D models into data files suitable for use with 3D printers during the rapid prototyping process. It’s essential for actualizing the printing phase by making sure prototypes are manufactured accurately and competently.
Utilization of these sophisticated tools boosts both effectiveness and quality within rapid prototyping activities, leading to faster progression through design iterations as well as improved end results.
Common Rapid Prototyping Techniques
Rapid prototyping is a fundamental component in contemporary product design processes, offering an array of strategies for swiftly and effectively fabricating physical prototypes. Among the prevalent methods are Vacuum Casting 3D printing, CNC machining, and Stereolithography—all designed to meet specific requirements based on anticipated results. These approaches differ in terms of material choice, intricacy of use, and practical application with an emphasis on decreasing the time taken for development while encouraging creative design solutions.
Techniques such as Stereolithography (SLA), Fused Deposition Modeling (FDM), and Laminated Object Manufacturing (LOM) provide targeted options tailored to varying demands within rapid prototyping. They serve critical roles when it comes to crafting precise models or large-scale components with high levels of detail—offering designers the versatility necessary to select a technique that aligns optimally with their project’s specifications.
The decision-making process regarding which rapid prototyping technique to employ depends upon factors including cost-effectiveness, speed of execution, materials compatibility, as well as the desired level of fidelity for the prototype being developed. The integration of specialized software intended specifically for these innovative prototyping technologies contributes significantly towards improving both workflow efficiency and final product quality—enabling superior iteration in designs. Comprehending these common rapid prototyping techniques becomes essential when determining the most suitable approach for any given project.
Stereolithography (SLA)
Stereolithography (SLA) stands as the pioneering technique in commercial 3D printing, which solidifies photosensitive liquid resin layer by layer using a laser. This method is renowned for its high precision and ability to capture intricate details, lending itself well to the production of visually impressive prototypes. A variety of resins are employed within SLA processes such as those that yield toughness and durability, flexibility, elasticity or rigidity catering to specific needs of different projects.
The meticulousness with which SLA operates makes it an exceptional option for crafting prototypes where accuracy and aesthetic quality are paramount. It excels particularly in scenarios where complex patterns and flawlessly smooth surfaces are required, guaranteeing both functionality and striking visual impact in the finished prototypes.
Fused Deposition Modeling (FDM)
Fused Deposition Modeling (FDM), a 3D printing technique prevalent in both professional and personal use, builds components by layering melted thermoplastic filament. As the process involves melting and depositing thermoplastic resins to construct parts layer after layer, it has become a favored method for producing solid and practical objects within the realm of fused deposition modelling.
One significant benefit of employing FDM printers lies in their capacity to fabricate strong, durable pieces intended for actual application. Consequently, FDM stands out as an optimal solution when there’s a need to craft functional prototypes that can undergo rigorous testing regarding performance and longevity. By tapping into the capabilities offered by FDM technology, designers have the ability to create high-quality prototypes that faithfully mimic the functionality expected from the end product.
Selective Laser Sintering (SLS)
Selective Laser Sintering (SLS) employs selective lasers to fuse powder material together, forming robust components with elaborate shapes and details. This process provides a host of benefits such as reduced costs per unit, enhanced productivity, substantial build capacities, and the capacity for crafting complex geometries. Various materials like PA11, PA12 normal or 40% glass-filled versions along with carbon-filled PA12 and TPU are available in SLS printing, offering designers considerable flexibility when picking the most suitable substance for their project.
While there are many upsides to using Selective Laser Sintering (SLS), one should be mindful that parts made through this method can exhibit brittleness stemming from internal porosity. It’s an aspect worth considering when deciding if SLS is the appropriate choice for certain applications. Nevertheless, its capability to produce sturdy parts featuring intricate designs establishes Selective Laser Sintering as a highly valuable technology in numerous prototyping scenarios.
Advanced Rapid Prototyping Techniques
Sophisticated rapid prototyping techniques play an essential role in confirming design decisions and evaluating the suitability of production strategies, particularly within additive manufacturing processes. Methods such as binder jetting and Direct Metal Laser Sintering (DMLS) are instrumental for fabricating components with high strength and complex designs. The selection among these methods is influenced by a variety of elements like financial limitations, material specifications, and intricacy of design.
As a cost-effective solution for constructing metal prototypes, binder jetting stands out due to its economical advantages when measured against other similar approaches. Conversely, DMLS employs powerful lasers to meld metal powder into solid parts, which is exceptionally suitable for producing items that require elaborate shapes along with substantial durability.
Recognizing the distinct benefits and constraints associated with each of these progressive techniques enables designers to make well-informed choices tailored to meet the specific demands of their projects effectively.
Direct Metal Laser Sintering (DMLS)
The process of Direct Metal Laser Sintering (DMLS) involves the use of a powerful laser beam to fuse metal powder, resulting in parts that are both robust and meticulously crafted. Renowned for its ability to fabricate components with intricate internal features and complex geometries, which are challenging to produce using conventional manufacturing techniques, this method is particularly effective at crafting lightweight parts.
For projects necessitating components with superior strength and elaborate configurations, DMLS serves as an indispensable asset within the rapid prototyping landscape.
Multi Jet Fusion (MJF)
Utilizing inkjet technology, Multi Jet Fusion (MJF) administers a binding agent onto powdered layers and subsequently applies heat to solidify the material. The distinct fusing approach inherent to this method allows for more evenly distributed mechanical strength throughout the parts in contrast with alternative technologies.
For crafting high-quality prototypes that maintain uniform mechanical properties, MJF proves itself as an essential asset within the repertoire of rapid prototyping techniques.
Digital Light Processing (DLP)
Digital Light Processing (DLP) represents a form of rapid prototyping technology, employing a digital projector to solidify photopolymer resins. Its primary benefit in the context of rapid prototyping lies in its ability to deliver speed while maintaining high resolution.
Employing this method is particularly advantageous for those looking to fabricate detailed and accurate prototypes swiftly. As such, it serves as an essential resource for designers requiring the production of superior quality prototypes with time efficiency.
Selecting the Right Rapid Prototyping Method
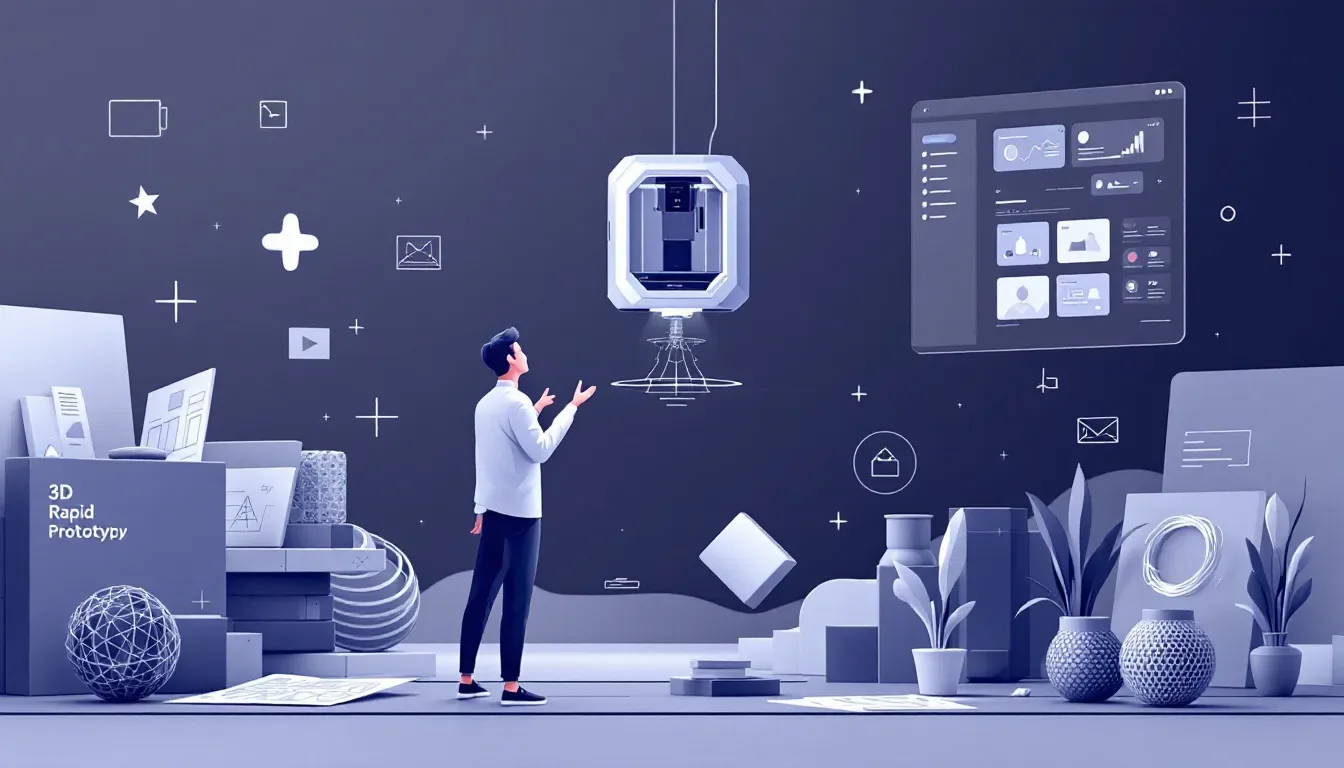
Choosing an appropriate rapid prototyping process necessitates evaluation of several vital elements. The type of material is pivotal in determining the suitable prototyping approach, as different materials possess distinct characteristics that may impact how a prototype functions. Important aspects to take into account include specific project requirements, the inherent properties of materials, and intended results. By grasping these considerations, designers are able to identify the most fitting rapid prototyping technique for their needs.
The functionality of a prototype must mirror that of the final product. Its manufactureability and market feasibility are essential components within any prototyping method. The number of prototypes needed also plays a significant role in assessing which prototyping technologies will provide cost-effective solutions. Designers can achieve both effectiveness and efficiency in their rapid prototyping by acknowledging these key factors.
By employing CAM software, digital designs from CAD files can be translated into operational commands used during CNC machining processes, thus boosting both flexibility and accuracy throughout various stages of producing physical parts swiftly through different types or methods available under rapid protoyping umbrella, all aiming at enhancing speed while refining product design cycles.
In this way, this way,
Designers have capabilities.
To forge high quality prototypes that faithfully align with envisioned attributes belonging to eventual commercial products they plan on launching soon after iterative phases come full circle successfully using select methodology deemed best suited for each unique case scenario tackled along development pathway explored attentively.
Common Mistakes to Avoid in Rapid Prototyping
Mistakes in the realm of rapid prototyping can disrupt the development flow and cause expensive rework. A frequent error includes failing to establish clear goals for a prototype, leading to wandering focus and misdirection. Another oversight is neglecting proper material selection, which might compromise the functionality and fidelity of the model. By deliberating on materials’ characteristics in alignment with project demands, designers are better equipped to sidestep these common errors.
Breezing through validation steps may cause missed opportunities for learning and persisting unverified hypotheses. Creating overly complex initial prototypes is counterproductive as it consumes time and resources that could be used gathering pivotal user feedback instead. It’s crucial to define concrete metrics for success that aid in evaluating whether a prototype achieves its intended objectives after rigorous testing under actual usage conditions.
Failing to account for scalability during early stages can present major challenges when increasing production scale later on. Relying solely on internal critiques might introduce bias, obscuring potential defects within a product. Hence tapping into external viewpoints becomes necessary at times. Utilizing simpler low-fidelity models helps uncover interface design problems sooner thus lowering developmental risks overall. This approach underscores efficient strategies aimed at streamlining prototype creation while steering clear of typical stumbling blocks.
Summary
To recapitulate, rapid prototyping stands as an influential asset that expedites the product development cycle while mitigating the incidence of expensive errors. By grasping the array of rapid prototypes along with their tailored uses, designers are empowered to pinpoint the most fitting rapid prototyping technique for their specific venture. Ranging from conceptual models to meticulously detailed representations, each category fulfills a distinctive role within the prototype creation stage of product evolution.
The selection of materials and incorporation of cutting-edge software emerge as pivotal elements in refining the rapid prototyping process. Through meticulous consideration of material characteristics coupled with sophisticated software applications, designers have the capacity to forge high caliber prototypes that closely emulate the envisioned end-product. By familiarizing themselves with prevalent rapid prototyping techniques—and incorporating advanced approaches such as Direct Metal Laser Sintering (DMLS) and Multi Jet Fusion (MJF)—the efficiency and output quality during prototype fabrication can be considerably enhanced.
By judiciously choosing an appropriate method for creating quick prototypes and sidestepping typical pitfalls, those who design can ascertain both functionality and dependability in their mock-ups. This extensive overview has shed light on various facets of rapid prototying including its advantages and contextual usage—equipping you with knowledge essential for fully leveraging rapdi preotypign in your quests towards product innovation.
Frequently Asked Questions
What is rapid prototyping?
Rapid prototyping is the quick development of prototypes through computer-aided design, which is crucial for validating a product’s design and functionality prior to mass production.
This process enhances efficiency and reduces costs in product development.
What are the different types of rapid prototypes?
The different types of rapid prototypes encompass proof-of-concept prototypes, low-fidelity prototypes, high-fidelity prototypes, looks-like prototypes, works-like prototypes, and engineering prototypes.
Each type serves a specific purpose in the development process, enabling effective and efficient design iterations.
How do I select the right rapid prototyping method?
To select the right rapid prototyping method, it is essential to evaluate factors such as project requirements, material properties, and the desired functionality.
A well-informed decision will ensure that the chosen method aligns with the specific goals and constraints of your project.
What role does material selection play in rapid prototyping?
Choosing the right materials is crucial for rapid prototyping because it influences how well the prototype will perform and whether it meets specific project criteria, like durability and surface finish.
Ensuring that suitable materials are used guarantees that the end product operates as planned.
What are some common mistakes to avoid in rapid prototyping?
To guarantee an efficient rapid prototyping process, defining precise goals, selecting materials with caution, conducting comprehensive validation, steering clear of excessive complexity in design (over-engineering), contemplating the potential for scaling up production and incorporating feedback from external sources is critical.
Disregarding these elements can greatly obstruct the progress of prototyping and influence the ultimate outcome negatively.
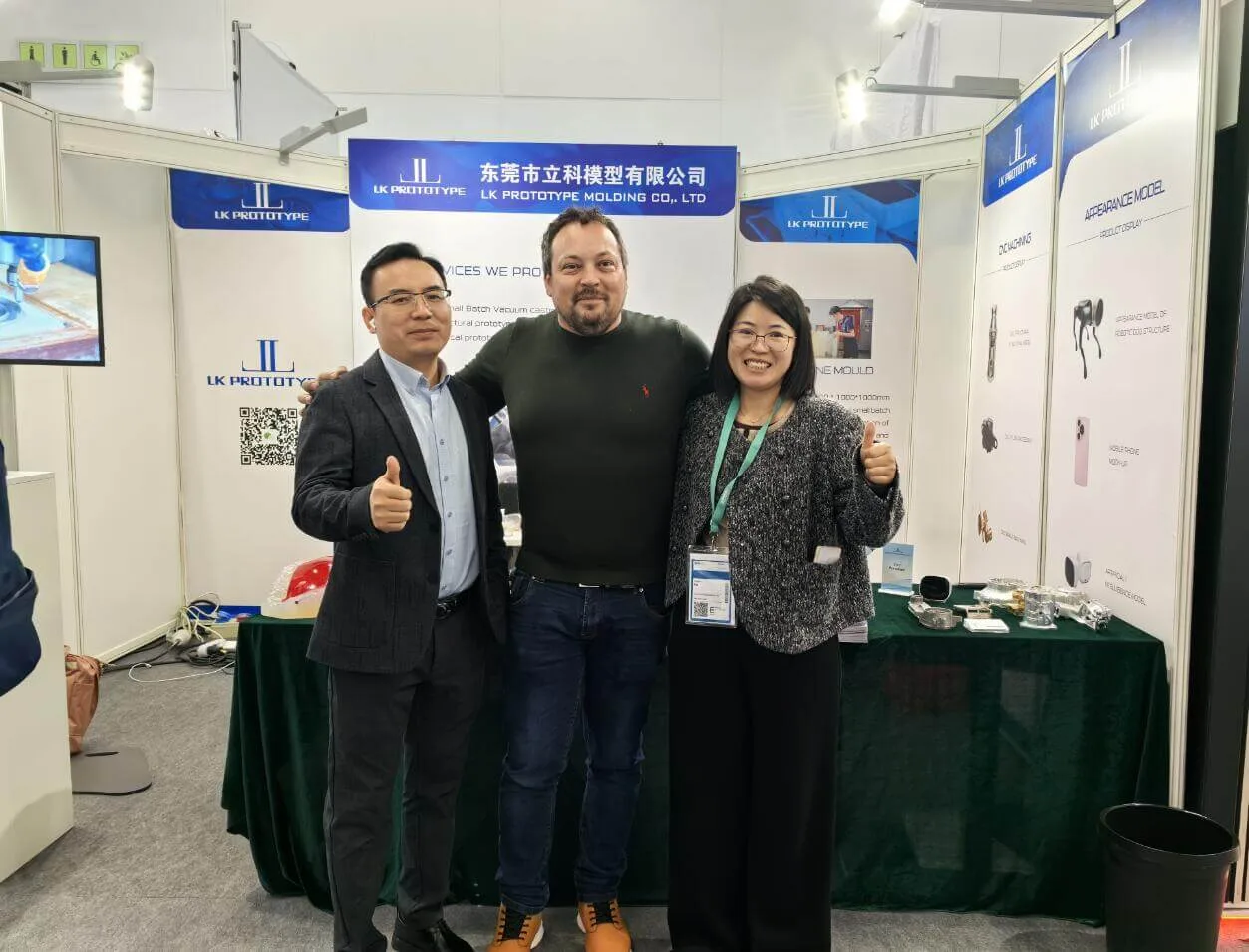
Start Your Next Project with LKprototype
LKprototype simplifies procurement for custom manufacturing, Suitable for making your products or prototypes with a variety of materials, such as metal or plastic, silicone rubber, from 3D Printing to CNC Machined Parts and Vacuum Casting , with a focus on speed and efficiency. Our platform provides instant quotes. With LKprototype, You can connect with the team to communicate your project to ensure quality and on-time delivery.
Start with an instant quote and experience how our technology and expertise can make custom part procurement faster and easier.