Prototyping manufacturing helps you develop products efficiently. You create early test versions to spot and fix issues, saving time and money before mass production. This article explores best practices and techniques in prototyping manufacturing.
Key Takeaways
Prototyping manufacturing is essential for identifying design flaws early, reducing risks, and accelerating product development.
The selection of the right prototyping method and materials significantly impacts the functionality, cost, speed of the product development process.
Emerging trends, including advanced materials and automation, are enhancing prototyping efficiency and enabling the development of complex, high-quality prototypes.
What is Prototypeing Manufacturing?
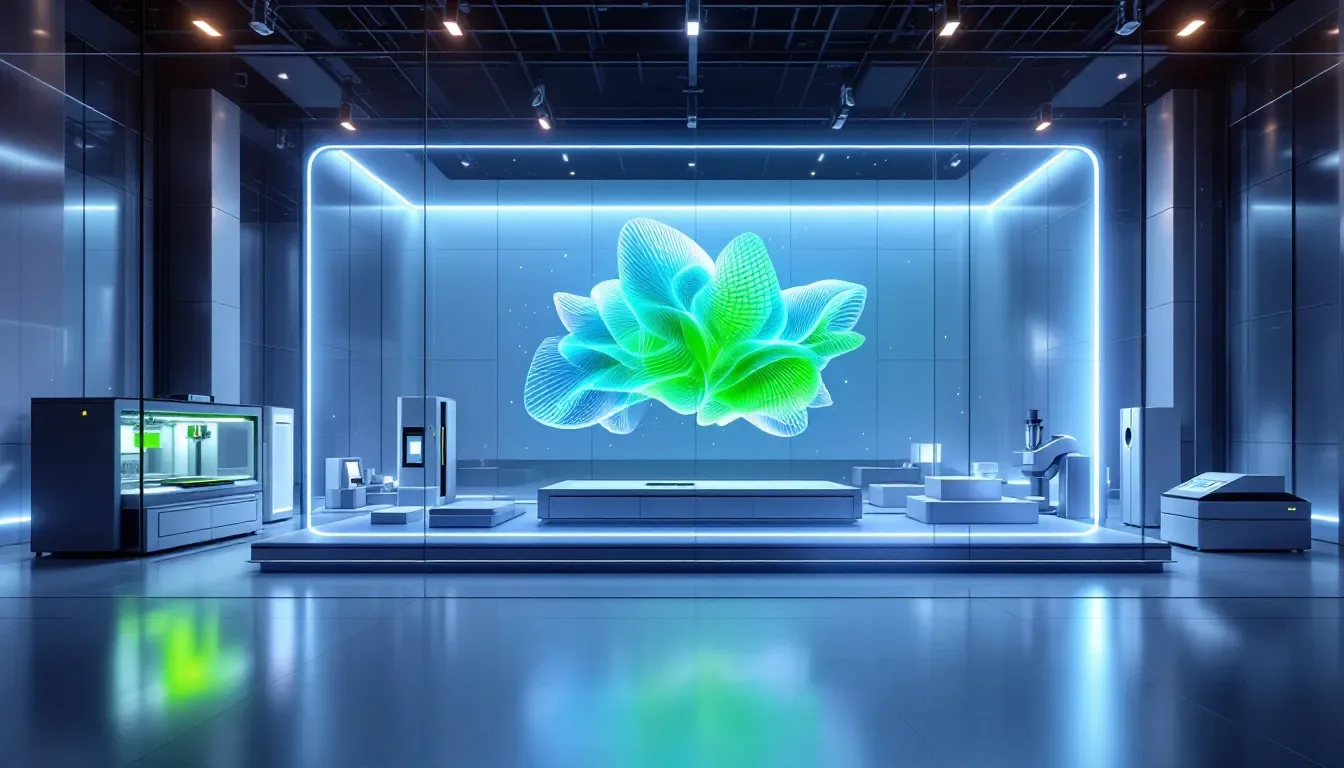
Manufacturing prototypes involves the creation of preliminary models of a product to assess its design and functionality ahead of full-scale production. The main goal is to detect any potential issues early in the process, which can save both time and money. By committing resources to prototype development, companies can accelerate their overall development pace, nurture innovation, and avoid costly errors.
Prototypes are indispensable within the product development cycle for enhancing products and expediting the journey from concept to market ready goods. Entrepreneurs and designers rely on them not only for visualizing what a final product will look like, but also for identifying defects as well as soliciting feedback from potential users. This repetitive refining process increases productivity by cutting down design iterations while promoting creativity.
When it comes to creating prototypes, it’s crucial that they serve their intended purpose effectively without compromising on speed or budget-friendliness when bringing a product closer to launch. Specialists in prototyping play an essential role here. They assist in spotting obstacles at inception stages, tailoring designs with mass production in mind (optimization), and fine-tuning performance outcomes.
Types of Prototypes
Within the prototyping process, a variety of prototype models are utilized for different objectives. Proof-of-concept prototypes serve to show that an idea or concept is viable by affirming its potential to evolve into a working product.
Looks-like prototypes concentrate on emulating the appearance of the final product. They provide an opportunity for designers to scrutinize and refine the product’s visual elements.
Conversely, engineering prototypes are crafted with a focus on verifying both how well the product functions and how it will be manufactured in practice.
Key Benefits of Prototyping Manufacturing
The development of a prototype is crucial for several reasons.
It allows for cost savings in the long run.
Early detection of problems lowers developmental risks and avoids expensive errors.
Through this iterative process, swift adjustments and enhancements are made, elevating both function and user interaction.
Progressions in material science have led to prototypes that boast increased durability and adaptability. Efficient prototyping accelerates the introduction of new products to market, allowing firms to maintain their competitive edge in swiftly evolving sectors.
The Prototyping Manufacturing Process
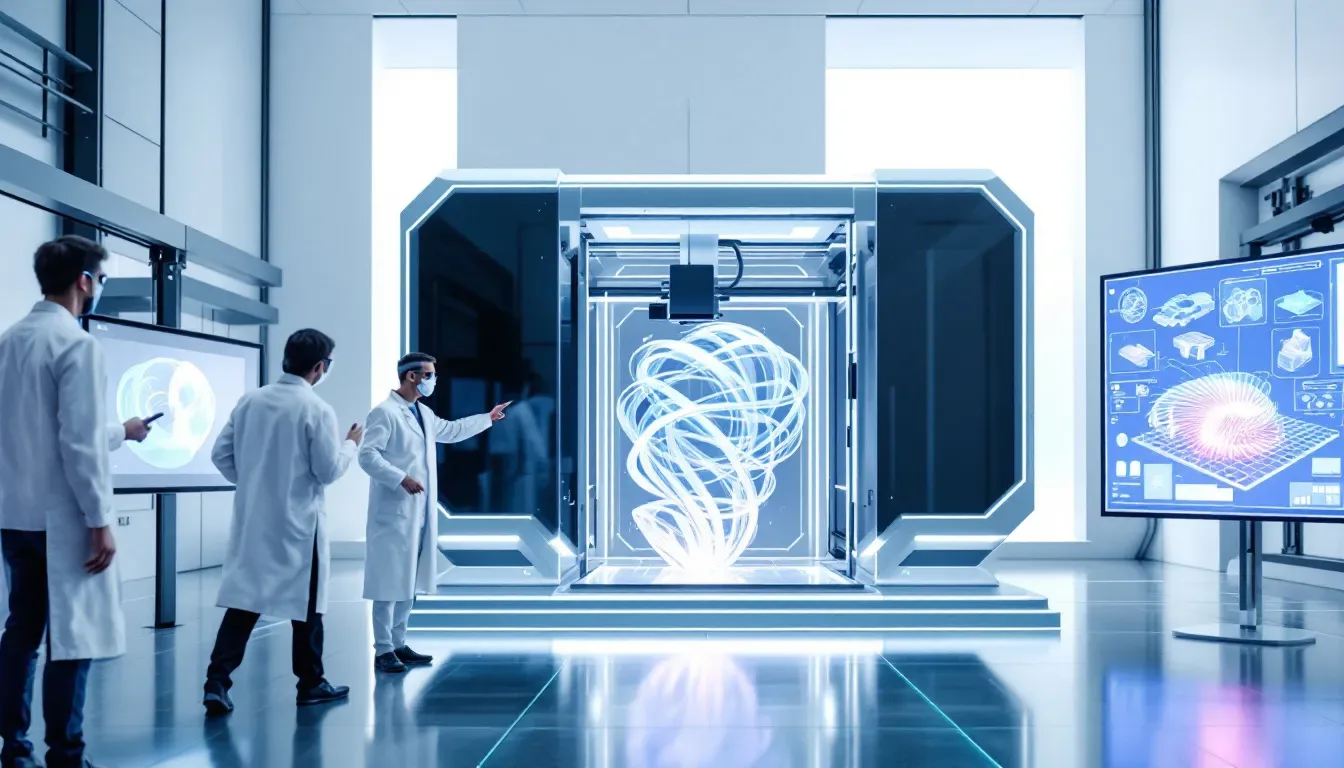
The manufacturing process for prototyping starts with the following steps:
Conceptualization and design
Choosing materials
Techniques in rapid prototyping
Assembling and combining parts
Conducting tests and making revisions
Every phase is essential to make sure that the prototype aligns with the desired specifications and performs as expected.
As digital tools become more prevalent, they are streamlining the production of rapid prototypes by enhancing efficiency across all stages of design and manufacture. Augmented reality (AR) and virtual reality (VR) technologies are broadening the scope of how prototyping can be applied throughout every stage of production lifecycle management.
Conceptualization and Design
In the commencement of the prototyping process, brainstorming sessions play a vital role as they enable teams to delve into imaginative concepts and pioneering approaches. This early phase is fundamental in establishing the groundwork for the prototype’s initial development.
As progress moves into the design phase, computer-aided design (CAD) modeling becomes instrumental in detailing each component’s configuration and bringing a visual representation of the prototype to life. Although CAD models are proficient at providing precise insights regarding dimensions and forms, they might not encapsulate all practical engineering intricacies.
Consequently, it is imperative during this stage to meticulously evaluate how individual components will coalesce while ensuring that these visual prototypes stay true to what is envisioned for the final product.
Material Selection
Selecting the right materials is a vital aspect of the prototyping process as it affects the prototype’s function, expense, and authenticity. Considerations like expense, accessibility, and robustness are essential when selecting materials for prototypes. The choice of material greatly determines how well the prototype will perform and its ultimate success.
Prototypes need to exhibit key qualities such as durability, pliability, thermal consistency, resistance to chemicals, and aesthetic resemblance. By choosing materials that are designed for use in the final product early on can help evaluate expenses more accurately and prevent unexpected complications during development.
Rapid Prototyping Techniques
The rapid prototyping process encompasses a range of techniques designed to quickly construct scale models from 3D CAD data. Manufacturing rapid prototyping methods such as 3D printing, CNC machining, and vacuum casting each serve specific purposes within this framework. For instance, with its use of materials like plastic, rubber, and nylon for constructing prototypes, 3D printing is recognized for being cost-effective despite its potential limitations in durability and dimensional precision when compared to machined prototypes. Overall efficiency is bolstered by the accelerated nature of these processes.
CNC machining stands out for generating precise and finely detailed prototypes from an array of substances that include both metals and plastics. Although it requires more financial investment and time than its counterpart, 3D printing, it compensates with unmatched accuracy along with a broader material selection option available at hand. Meanwhile, vacuum casting finds utility in fabricating mid-range performance components using silicone molds.
By merging additive methodologies such as 3D printing with subtractive ones exemplified by CNC machining into one integrated approach, you can optimize resource usage while also cultivating prototypes that are much more adaptable across various applications. This comprehensive strategy employs the respective advantages inherent in each process to manufacture high-quality prototype versions efficiently.
Assembly and Integration
The process of assembling and integrating prototypes requires the careful placement and fastening of parts, confirming their correct alignment, and verifying that they work well together. It’s important to thoroughly review the orientation and insertion of each element to confirm that all components mesh properly and perform as expected.
Evaluating separate modules prior to their integration can pinpoint problems within the assembly phase for prototypes. To successfully navigate challenges in assembly, it is crucial to maintain a structured approach to assembly, provide detailed instructions, and employ trained professionals.
Testing and Iteration
The manufacturing of prototypes enables creators to assess and authenticate their concepts by producing a range of physical models prior to initiating mass production. The aim of conducting tests during the prototyping phase is to uncover any problems before transitioning into full-scale production. This repetitive process requires several iterations, each using observations from real-world testing to improve the prototype.
By incorporating results and insights garnered from testing back into the design cycle, development teams can align with project objectives as well as user expectations. Rapid prototyping facilitates swift alterations in designs informed by user feedback, which is pivotal for ensuring that a product launch achieves success.
Choosing the Right Prototyping Method
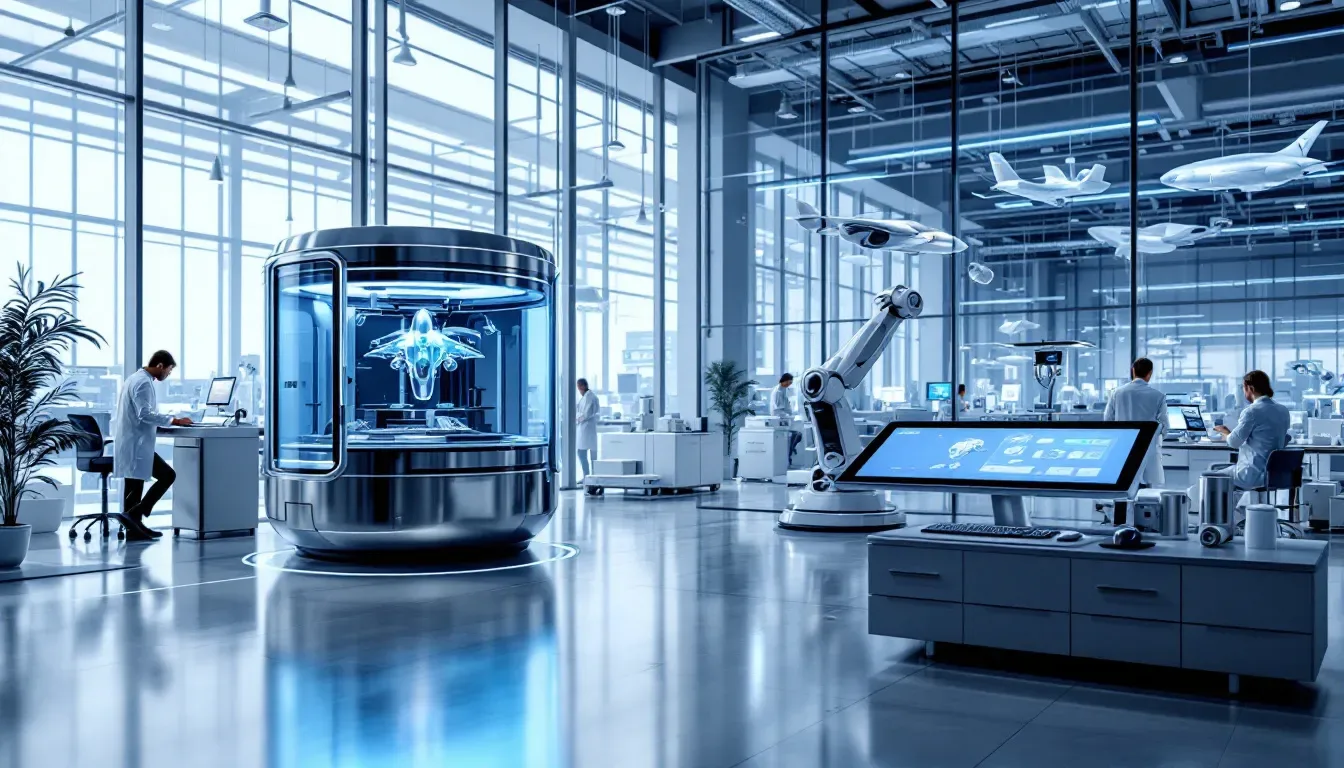
Choosing the appropriate prototyping technique is essential for a successful prototype manufacturing process. It’s important to ensure that various factors such as the project’s objectives, budget constraints, timeline demands, and required features of the prototype are all in harmony with the selected approach. Aligning these elements closely with your method can greatly influence how well your prototype turns out.
In particular scenarios like when only a handful of parts are needed sporadically or when large components necessitate unique materials not typically on hand, it may be advantageous to consider outsourcing rapid prototyping efforts. When making this decision, one must carefully weigh aspects including what you aim to achieve with your prototype, its capabilities after production and what options external services can provide.
Additive Manufacturing Processes
Additive manufacturing technology, including 3D printing, enables the crafting of complex designs that traditional manufacturing processes may not be capable of producing. This approach is well-suited for rapid prototyping because it allows for swift modifications after real-world testing.
Common additive manufacturing methods include Selective Laser Sintering (SLS) and Fused Deposition Modeling (FDM). SLS offers almost flawless fusion between layers, whereas FDM typically exhibits less robust layer bonding. Precision in metal additive manufacturing can be improved through CNC post-processing techniques, which play a crucial role in refining the prototyping process.
Subtractive Manufacturing Methods
Subtractive manufacturing methods, such as CNC machining, are best suited for producing highly accurate and high-functioning prototypes. CNC prototypes are generally superior to 3D printing in terms of accuracy and material selection. LKprototype, for example, offers more than 65+ certified materials for CNC prototypes.
One downside of CNC machining is that cosmetic finishing can entail considerable and costly hand finishing. Additionally, CNC machining takes longer and costs more than additive manufacturing, which can affect the timeline for functional testing.
Hybrid Approaches
In prototyping manufacturing, hybrid strategies integrate both additive and subtractive methods to capitalize on the advantages of each technique. The goal is to increase flexibility within the manufacturing process, which facilitates a more adaptable prototype creation cycle.
Merging technologies such as 3D printing (an example of an additive manufacturing process) with subtractive processes yields prototypes that are intricate and exact. Advantages of adopting these hybrid methodologies include enhanced quality of prototypes, shortened timeframes for production, and access to an expanded selection of materials for use.
Tips for Selecting Prototyping Materials
It is crucial to choose appropriate materials for prototypes as they play a significant role in fulfilling the functional, visual, and financial constraints of the prototype. Prototypes are frequently made from popular materials such as metal alloys, plastic, and wood. The selected material influences not only the cost and functionality, but also how accurately the prototype represents the intended design.
The broad classifications of prototyping materials include metals, plastics, ceramics, composites, and natural substances. Selecting a material with full awareness of its performance attributes—such as durability and pliability—is essential for making an educated choice that aligns with specific requirements.
Matching Functional Requirements
For prototypes to successfully test the functionality of the final product, it’s crucial that their materials closely mimic those used in the finished item. This includes considering functional requirements, aesthetic appeal, and constraints related to fit or limitations when selecting materials.
Recognizing how material selections can affect performance and where compromises might be necessary is a key part of this process. Employing usability testing and gathering user feedback are essential steps in confirming that these material choices align with the practical needs of the final product.
Budget Considerations
Creating rapid prototypes on your own may be the most cost-effective strategy and enables more precise control over expenses. Starting with a limited quantity of prototypes before verifying demand can lead to efficient budget management.
Cost reduction can also be achieved by streamlining designs and utilizing readily available components, easing financial burdens. Employing materials that mirror those used in final production can prevent additional expenses and delays due to repeated alterations.
Readily Available Materials
Opting for materials that are readily available can expedite the acquisition process and diminish expenses during prototyping. For early stages of prototype creation, materials such as paper and plastic, which are easily accessible, tend to be advisable. This strategy guarantees that shortages do not hinder the progress of the prototyping process.
As businesses aim to enhance sustainability in product development, there is an increasing trend towards employing recycled substances within rapid prototyping. The adoption of sustainable materials not only curtails environmental impact but may also cut down on costs.
Transitioning from Prototype to Mass Production
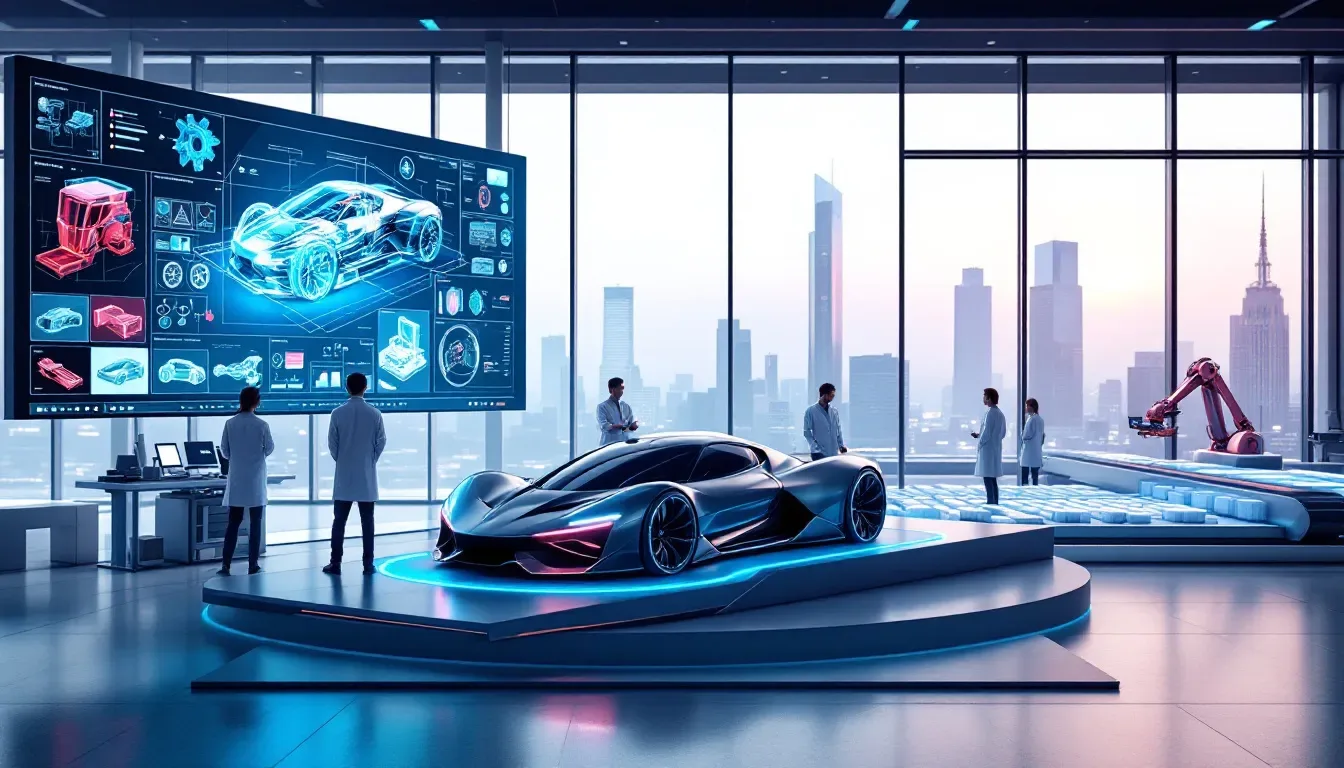
Transitioning from prototyping to mass production involves intricate changes to design, the methods of manufacturing, and quality assurance protocols. This stage presents the greatest risk within the product development process and demands meticulous strategy and implementation.
Leveraging prototypes enhances the design’s confirmation via user input, guaranteeing that market requirements are satisfied by the final product. When executed effectively, a proficient prototyping process can expedite market entry while minimizing risks throughout various stages of development.
Scaling Processes
When transitioning from development to mass production, it’s crucial to navigate new challenges and factors. It is essential for smooth scaling of production to maintain clear and precise communication with manufacturing partners regarding schedules and anticipated outcomes.
To scale up production efficiently, implementing thoughtfully designed procedures early on can be greatly beneficial. If not carefully overseen, outsourcing rapid prototyping may result in elevated expenses and extended timeframes.
Ensuring Quality and Consistency
Maintaining high standards of quality and uniformity is vital when moving from the prototyping stage to full-scale mass production, which forms a cornerstone for the triumphant introduction of any new product. The practice of prototyping serves an integral role in spotting design issues promptly, which helps diminish future expenses and prevent hold-ups as the product progresses through its manufacturing lifecycle.
Incorporating principles of Design for Manufacturability (DFM) right from the early stages of prototype development is key to refining product designs for easier production. Establishing a strong collaboration with manufacturing partners during this phase greatly contributes to achieving consistent quality throughout your item’s creation.
Future Trends in Prototyping Manufacturing
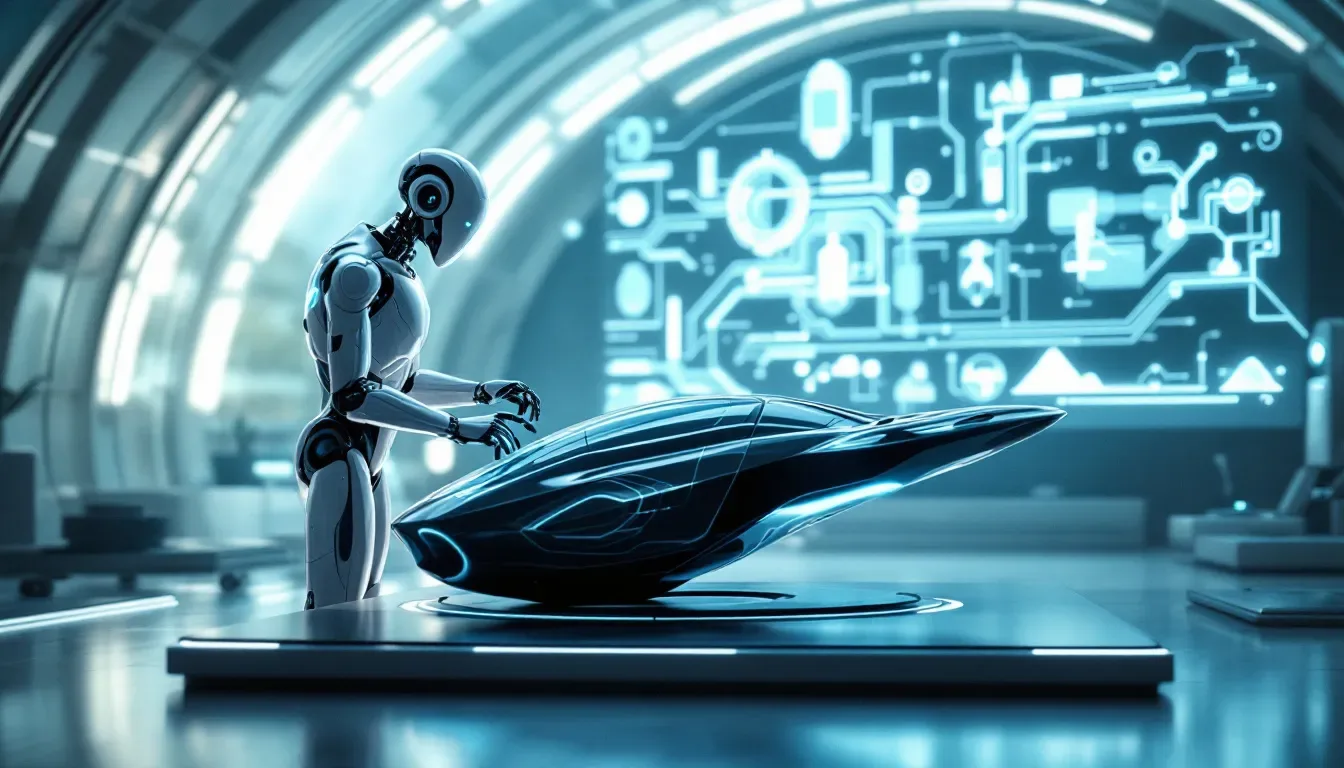
Current trends in the field of prototype manufacturing are leaning towards processes that are streamlined, cost-efficient, and flexible. These improvements promise to transform the sector by simplifying the introduction of novel products to market more rapidly.
By incorporating cutting-edge materials and automated technology into prototyping, substantial shifts are being observed within this area. Anticipated outcomes include increased strength, versatility, and enhanced quality of prototypes—setting the stage for a new generation of intricate and superior-performing goods.
Advanced Materials
Continual progress in material science is resulting in the creation of cutting-edge materials that improve the strength and flexibility of prototypes. These new materials, including innovative plastic composites and metal alloys, facilitate the fabrication of prototypes that accurately represent the characteristics expected from the end product.
This advancement in material technology is especially advantageous for sectors where precision and robustness are crucial, like medical devices and aerospace. By utilizing these advanced materials, manufacturers can construct prototypes featuring intricate details and complex geometries that challenge what was previously achievable using conventional manufacturing methods.
Automation and AI
The incorporation of automation and artificial intelligence into the development of prototypes is optimizing workflow procedures, resulting in more precise and expedited creation of prototypes. By improving efficiency within prototype production workflows, these advancements ensure that tasks are executed with greater speed and accuracy.
Incorporating AI into prototyping methods bolsters predictive maintenance capabilities while minimizing disruptions in production lines. This evolution in technology is revolutionizing the field of prototyping by enabling the rapid manufacturing of superior-quality prototypes with enhanced exactitude.
Summary
The manufacturing of prototypes is a crucial component within the product development cycle, providing substantial advantages including reduced costs, minimized risks, and expedited market entry. By gaining insights into various prototype models, mastering the steps entailed in prototyping, and prioritizing the selection of appropriate materials and techniques, companies can greatly improve their developmental endeavors.
Looking ahead to what’s on the horizon for this field. Innovations in material science coupled with advancements in automation and artificial intelligence are poised to transform prototyping manufacturing fundamentally. Companies that adopt these emerging trends will be well-positioned to accelerate innovation processes and deliver superior products more quickly than ever before—securing an advantageous position within their respective markets.
Frequently Asked Questions
What are the key benefits of prototyping manufacturing?
Prototyping manufacturing significantly reduces development risks and costs, while speeding up the time-to-market for new products. This approach also enables early identification of issues, allowing for rapid refinements that enhance functionality and overall user experience.
What are some common rapid prototyping techniques?
Rapid prototyping employs various methods such as 3D printing, CNC machining, and vacuum casting. Each technique comes with distinct advantages that suit particular requirements of different projects.
Choosing the appropriate method is essential for achieving a prototype that is both effective and created efficiently.
How does material selection impact the prototyping process?
In the prototyping process, choosing the right materials is of paramount importance because it has a direct impact on the functionality, cost-effectiveness, and authenticity of the prototype. Giving meticulous attention to attributes such as durability, elasticity, and heat resistance guarantees that the prototype conforms to intended design specifications and performance objectives.
What are the challenges of transitioning from prototype to mass production?
Moving from a prototype stage to full-scale mass production can be fraught with difficulties, including the need to tweak designs, perfect manufacturing processes, and improve quality assurance measures.
To overcome these obstacles successfully, it’s crucial to maintain clear communication with manufacturing partners and place high importance on designing products that are easy to manufacture.
How are automation and AI transforming prototyping manufacturing?
Automation and AI are transforming prototyping manufacturing by streamlining workflows and enhancing the accuracy and speed of prototype development.
This results in the production of high-quality prototypes with improved efficiency.
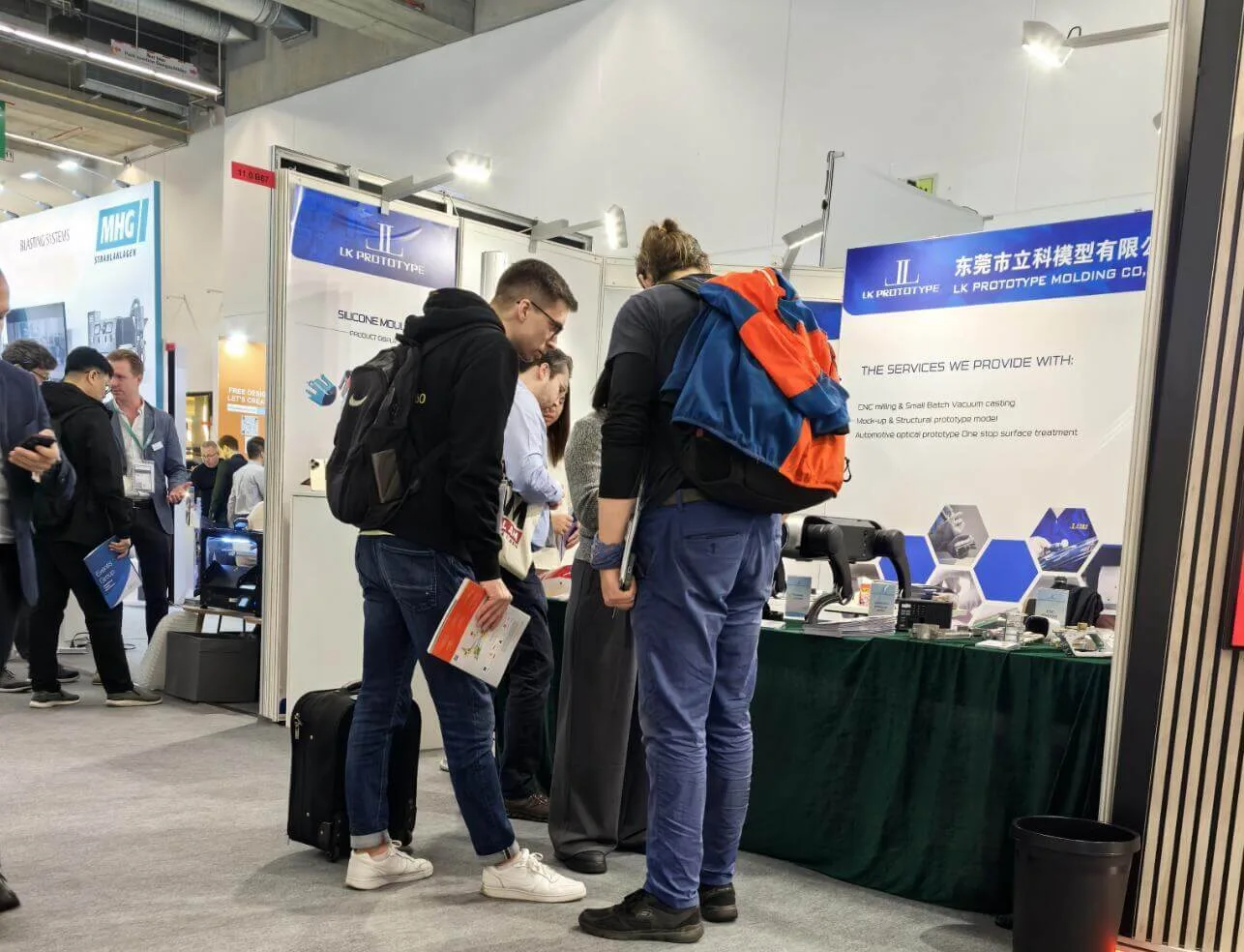
Start your project with LKprototype
LKprototype company simplifies procurement for custom manufacturing, Suitable for making your products or prototypes with a variety of materials, such as metal or plastic, silicone rubber, from 3D Printing to CNC Machined Parts and Vacuum Casting , with a focus on speed and efficiency. Our platform provides instant quotes. With LKprototype, You can connect with the team to communicate your project to ensure quality and on-time delivery.
Start with an instant quote and experience how our technology and expertise can make custom part procurement faster and easier.