Wondering whether MIG and stick welding is right for your needs? This article breaks down the key differences, pros, and cons of each welding method.
Key Takeaways
MIG welding offers faster and cleaner welds with a continuous wire feed but is less effective outdoors and for thick metals.
Stick welding is versatile and strong on dirty surfaces, excelling in thicker materials, but operates slower and requires more skill.
Choosing between MIG and stick welding involves considering project requirements, material types, and environmental factors.
Understanding MIG Welding
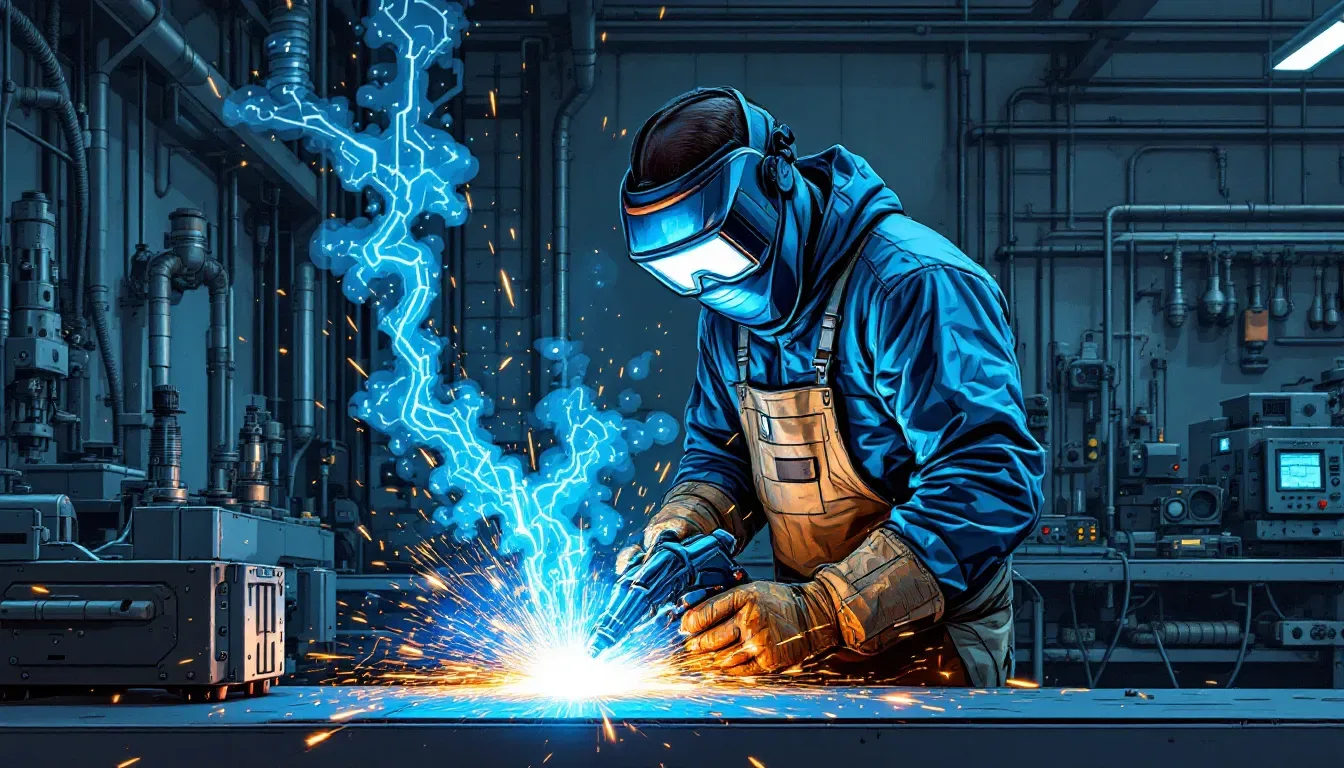
MIG welding, commonly referred to as Metal Inert Gas welding, involves the use of a MIG machine or machines for fusing metals together. The technique employs an electrode wire that is fed continuously while being accompanied by shielding gas through the process of gas metal arc welding. This approach is versatile enough for small-scale DIY endeavors as well as substantial industrial operations, which makes it highly suitable for both amateur and professional MIG welders alike. To attain superior quality in their welds, it’s crucial for these welders to have access to top-notch MIG welding machines and appropriate MIG wire.
In the practice of MIG welding, consumable electrodes serve a dual role. They provide both the necessary heat and act as filler material. This dualality significantly contributes to its adaptability and effectiveness in various welding scenarios.
Advantages of MIG Welding
MIG welding stands out for its proficiency in creating superior welds that exhibit minimal splatter, thanks to the continuous feeding of wire. This feature facilitates quicker production speeds relative to other methods of welding, enhancing its efficiency. MIG often yields cleaner welds than stick welding does, rendering it particularly suitable for handling thin metals where precision and neatness are paramount.
Disadvantages of MIG Welding
Before:
MIG welding, while offering certain benefits, is accompanied by significant drawbacks. These include elevated expenses when compared to other techniques of welding. The susceptibility of the process to wind can adversely affect welding performed outdoors. MIG welding tends not to be the most practical method for joining exceptionally thick materials such as cast iron, thereby constraining its versatility in various contexts.
After:
Notwithstanding its advantages, MIG welding presents several notable shortcomings. These encompass:
Increased costs relative to alternative approaches in welding
Sensitivity towards wind conditions that may compromise outdoor welding work quality
Suboptimal suitability for fusing particularly heavy-duty metals like cast iron, which curtails its utility across a range of situations
Exploring Stick Welding
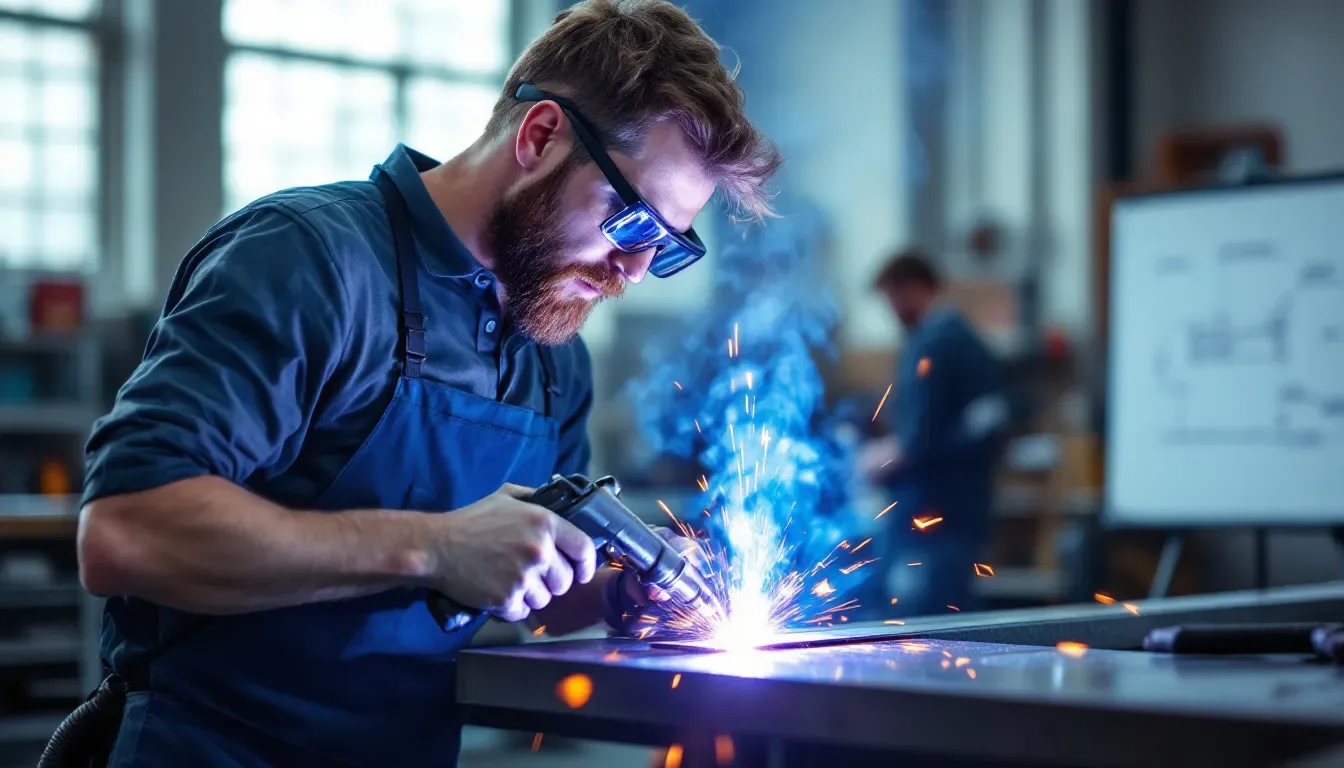
Stick welding, which is alternatively termed shielded metal arc welding (SMAW), employs a metallic stick or rod to serve as the filler material. This technique stands out among other arc welding processes for its adaptability and proficiency in joining various metals.
Renowned for its durability, stick welding excels even when applied to surfaces that are unclean or coated with rust. The bond created by a stick weld is notably durable, making this method highly effective under such challenging conditions.
Pros of Stick Welding
Stick welding boasts considerable adaptability, enabling its successful application across diverse metals, including nickel and aluminum. This form of welding tolerates less-than-pristine surfaces well, rendering it particularly useful for joining rusted or coated materials.
When dealing with thicker substances, stick welding offers deeper penetration compared to MIG (Metal Inert Gas) welding. Consequently, the welds produced through this method are typically more robust than those achieved with MIG techniques.
Cons of Stick Welding
Despite its benefits, stick welding comes with certain limitations. It progresses at a slower pace than MIG welding, which can extend the duration needed to complete projects. It demands greater expertise for successful execution, potentially discouraging those who are new to welding.
The necessity to regularly change the welding rod also contributes to more frequent interruptions in work, rendering stick welding less suitable for tasks that require uninterrupted welding processes.
Key Differences Between MIG and Stick Welding
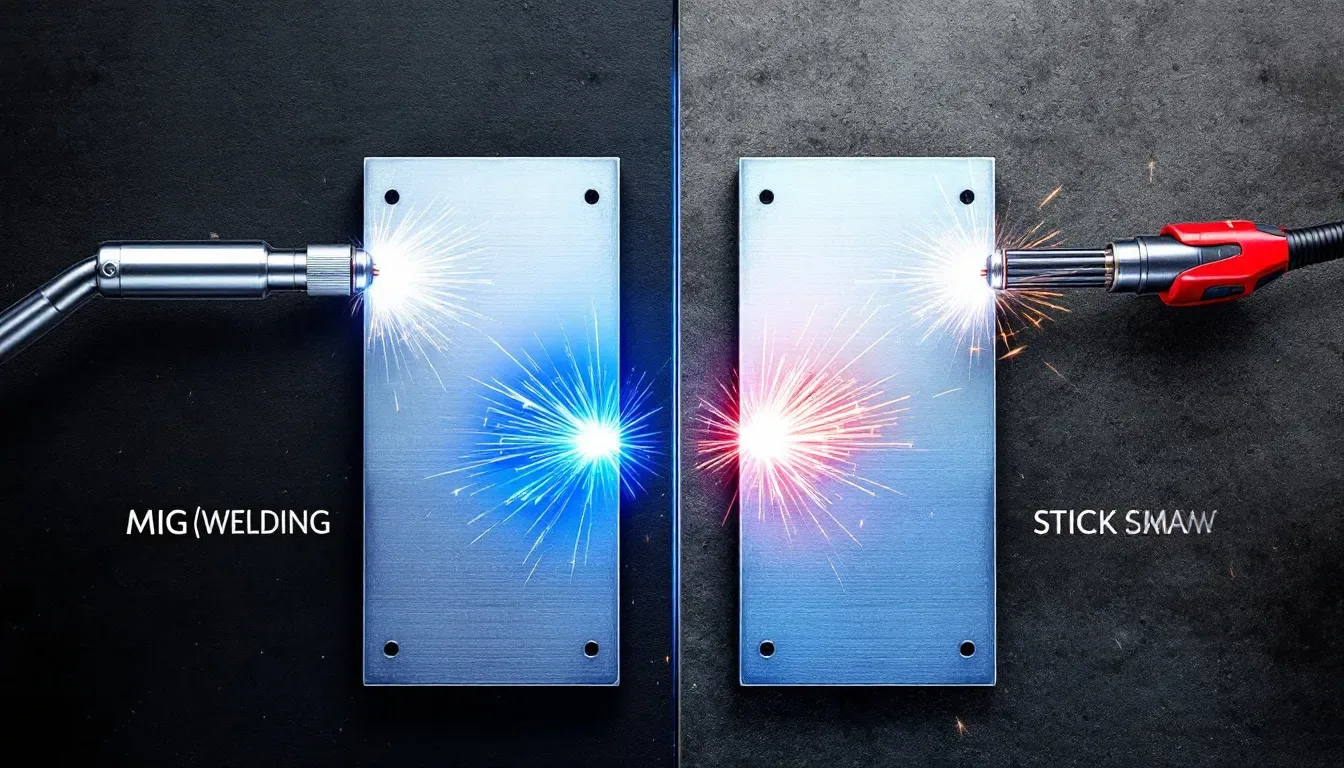
Understanding the primary distinctions between MIG and stick welding is crucial when deciding which technique to employ for a particular task. MIG welding leads to quicker production times and provides more refined welding due to its use of an electrode wire that is constantly supplied, in conjunction with a shielding gas. On the other hand, stick welding employs a flux-coated consumable electrode.
Considered less challenging for newcomers, MIG welding may be the better option for those just starting out. It necessitates sophisticated gear that might prove costlier than what’s needed for stick welding.
Weld Quality Comparison
Typically, MIG welding provides a superior visual quality over stick welding. The welds created by MIG are neater and require less cleaning after the weld is complete, which improves their overall look.
When deciding between MIG and stick welding, factors such as the preferred appearance of the weld, its strength requirements, and the materials being welded often play a critical role.
Indoor vs Outdoor Use
MIG welding is not as appropriate for outdoor applications because the shielding gas can be disrupted by wind. On the other hand, stick welding is highly effective when working outdoors or performing repairs on surfaces that are unclean or have rusted.
Both MIG and stick welding techniques can experience a substantial impact on weld quality and safety due to variations in wind conditions and temperature.
Metal Types and Thicknesses
MIG welding can join thin and thick metals such as aluminum, copper, stainless steel, carbon steel, nickel, and magnesium. Stick welding is capable of welding various metals such as nickel, aluminum, copper, iron, and steel.
MIG welding is preferred for thin materials, whereas stick welding excels in materials thicker than 3/8 inch.
MIG Welding Techniques
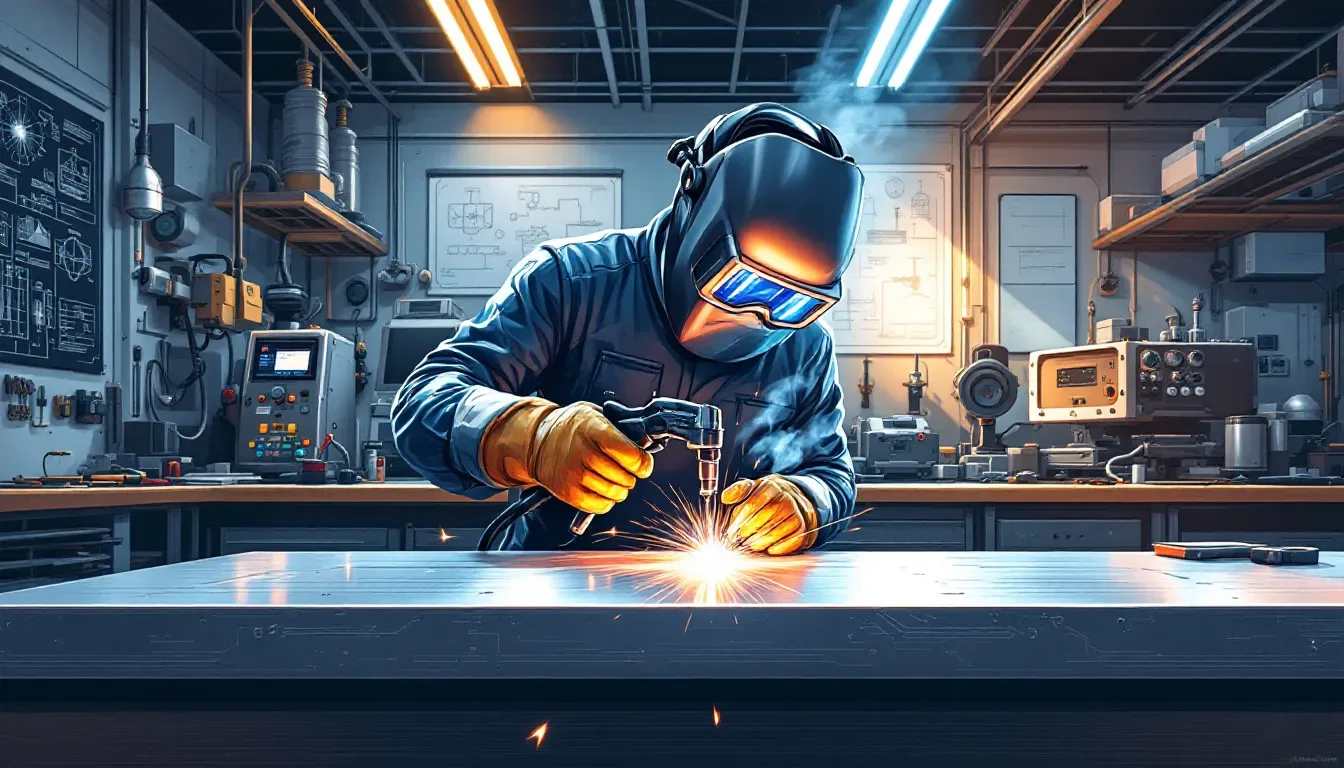
Effective MIG welding hinges on maintaining control and stability, which can be enhanced by using a two-handed grip on the MIG gun. The process of MIG welding is versatile enough to allow for both automatic and semi-automatic operation, dictated by how the equipment is set up.
Achieving superior results in MIG welding requires a steady application of technique as well as adjustments to settings that correspond with the material being welded and the intended result.
Setting Up MIG Welding Equipment
Several critical steps are involved in setting up MIG welding equipment. A clean, rust-free surface is crucial for better weld quality. The setup can be complex due to variables such as wire size, gas type, contact tips, and nozzle type.
Adjusting wire feed speed and voltage is crucial for proper weld formation, while the right shielding gas prevents contamination and maintains quality.
Common MIG Welding Mistakes
Common MIG welding mistakes can greatly affect weld quality. Improper stickout distance can compromise gas coverage and weld quality. Excessive wire speed can result in poor weld quality and spatter.
A consistent travel speed is essential for uniform welds and defect prevention.
Stick Welding Techniques
Attaining proficiency in stick welding necessitates more advanced skills compared to MIG welding. It demands the ability to initiate and sustain a steady arc, which might pose difficulties for novices. Diligent preparation and consistent practice are essential for producing superior-quality welds using the stick method.
Preparing for Stick Welding
Proper preparation is crucial for effective stick welding, as it entails cleansing the metal surface to eliminate any impurities that might negatively affect the quality of the weld. Failing to sufficiently clean can lead to suboptimal adhesion and inferior quality in the resulting weld.
Ensuring that metal surfaces are thoroughly cleaned before proceeding with welding contributes significantly towards achieving robust and reliable welds.
Overcoming Stick Welding Challenges
In stick welding, one of the main difficulties is ensuring a steady arc without causing the electrode to adhere to the material. Novices frequently find it hard to initiate and sustain an even arc. To avoid sticking electrodes, it’s crucial to preserve the appropriate angle along with a consistent length of the arc.
Eliminating slag effectively after each pass in welding is vital for averting slag inclusion within the weld.
Cost Considerations
When selecting between MIG and stick welding, financial considerations play a crucial role. MIG welding involves greater total costs because of the equipment and consumables required, whereas stick welding is less expensive in these areas.
Understanding these financial implications helps to make educated choices that align with both budget constraints and specific project requirements.
Initial Equipment Costs
The cost of initial setup for MIG welding is greater because it requires a shielding gas system. In contrast, stick welding equipment often comes with a lower price tag at the outset owing to its reduced need for consumables. As such, stick welding presents a more economical choice for individuals new to the field of welding.
Operational Costs
MIG welding operational costs can be higher due to consumables, power consumption, and maintenance. Continuous wire feeding in MIG welding can offset costs by enabling longer, uninterrupted welds.
Knowing the ongoing expenses is crucial for budgeting and planning long-term projects.
Safety Practices for MIG and Stick Welding
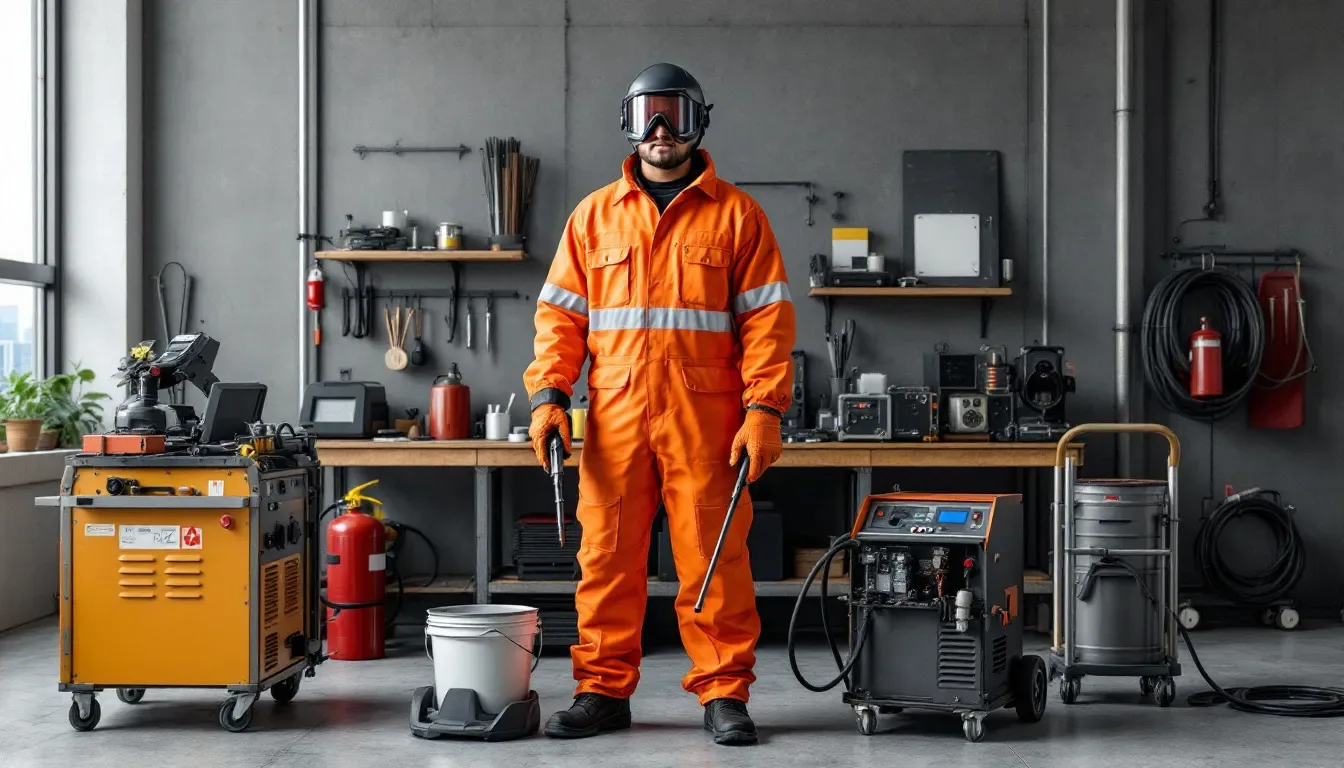
Adhering to safety protocols is critical in every welding process to avoid accidents and injuries. Maintaining a safe work environment for MIG and stick welders requires strict compliance with safety measures during both MIG and stick welding.
Essential Safety Gear
Appropriate safety gear is paramount for upholding health and safety protocols in welding. Helmets equipped with suitable filter shades are vital to safeguard against the intense light and radiation encountered during these tasks.
It’s important to use high-quality gloves that not only protect from burns but also enhance grip, which are necessary precautions when engaging in welding activities.
Safe Welding Practices
To ensure safety during stick welding, it is crucial to wear clothing that resists flames in order to shield oneself from burns caused by sparks and heated metal. Conducting routine checks on equipment can reveal potential problems before they lead to mishaps. Securing a proper ground for the welding machines mitigates the risk of electric shocks, and maintaining adequate ventilation is essential due to the fumes and smoke generated, particularly when engaging in outdoor stick welding.
Choosing the Right Welding Method for Your Project
Selecting the right welding processes method depends on project requirements, including materials and techniques.
Assess the required expertise level and specific project needs when choosing between MIG and stick welding.
Project Type Considerations
The selection of a welding method is greatly impacted by the nature of the project at hand. For projects where precision and clean finishes are crucial, especially in environments that can be controlled, MIG (Metal Inert Gas) welding is often favored.
Conversely, stick welding comes to the forefront for maintenance work or situations involving challenging access due to its inherent portability. Stick welders offer versatility and convenience as they function effectively without being limited by cable lengths, making them appropriate for a diverse range of applications.
Environmental Factors
Wind and temperature significantly influence the choice of welding method. MIG welding is less effective in windy conditions due to shielding gas disruption, while stick welding performs well outdoors.
Keeping the workspace free of flammable materials is vital to reduce fire hazards.
Summary
In summary, both MIG and Stick welding have unique advantages and challenges. MIG welding offers cleaner welds, faster production rates, and is easier to learn, making it ideal for beginners and precision work. On the other hand, Stick welding provides superior penetration for thicker materials, is versatile, and performs well in outdoor conditions.
Choosing the right welding method depends on the project’s specific requirements, environmental factors, and budget considerations. By understanding the key differences and best practices for both methods, you can make an informed decision that ensures high-quality welds and successful project outcomes. Embrace the art of welding with the right knowledge and tools to achieve your goals.
Frequently Asked Questions
What is the primary difference between MIG and Stick welding?
MIG welding uses a wire that is constantly fed as an electrode together with a shielding gas to protect the welding area, in contrast to Stick welding which makes use of a flux-coated consumable electrode.
This key difference influences their suitability and user-friendliness for different types of welding jobs.
Which welding method is better for beginners?
MIG welding is the better choice for beginners as it is easier to learn and has a straightforward operation.
Can I use MIG welding for outdoor projects?
MIG welding is not ideal for outdoor projects because wind can compromise the shielding gas and negatively impact weld quality.
It’s advisable to use a different welding method in outdoor conditions.
What metals can be welded using Stick welding?
Stick welding can effectively weld metals such as nickel, aluminum, copper, iron, and steel. This versatility makes it a valuable process for various applications in metal fabrication.
What are the cost considerations for MIG welding?
Cost considerations for MIG welding include higher expenses for equipment and consumables, but the efficiency of continuous wire feeding can mitigate some of these costs.
Therefore, it’s essential to weigh initial investments against long-term savings.
LKprototype has many years of experience manufacturing prototype parts for clients in the aerospace, automotive and consumer electronics industries, among others. Please contact us for a quick quote on any project.
Still, need help? Contact Us: lk@lkprototype.com Need a PROTOTYPE or PARTS machining quote? Quote now