Looking to speed up product development? Rapid prototyping services offer fast, precise prototypes for metals and plastics. This article explores key techniques and their benefits.
Key Takeaways
Rapid prototyping accelerates product development by allowing quick iterations and physical model creation from CAD data, utilizing techniques such as CNC machining, 3D printing, and vacuum casting.
Key benefits of rapid prototyping include reduced development costs, faster feedback on designs, and early identification of design flaws, thus enhancing the overall efficiency of the product development lifecycle.
Choosing the right rapid prototyping method depends on factors like budget, complexity, and production volume, with options ranging from high-precision CNC machining to versatile 3D printing and cost-effective vacuum casting.
Understanding Rapid Prototyping
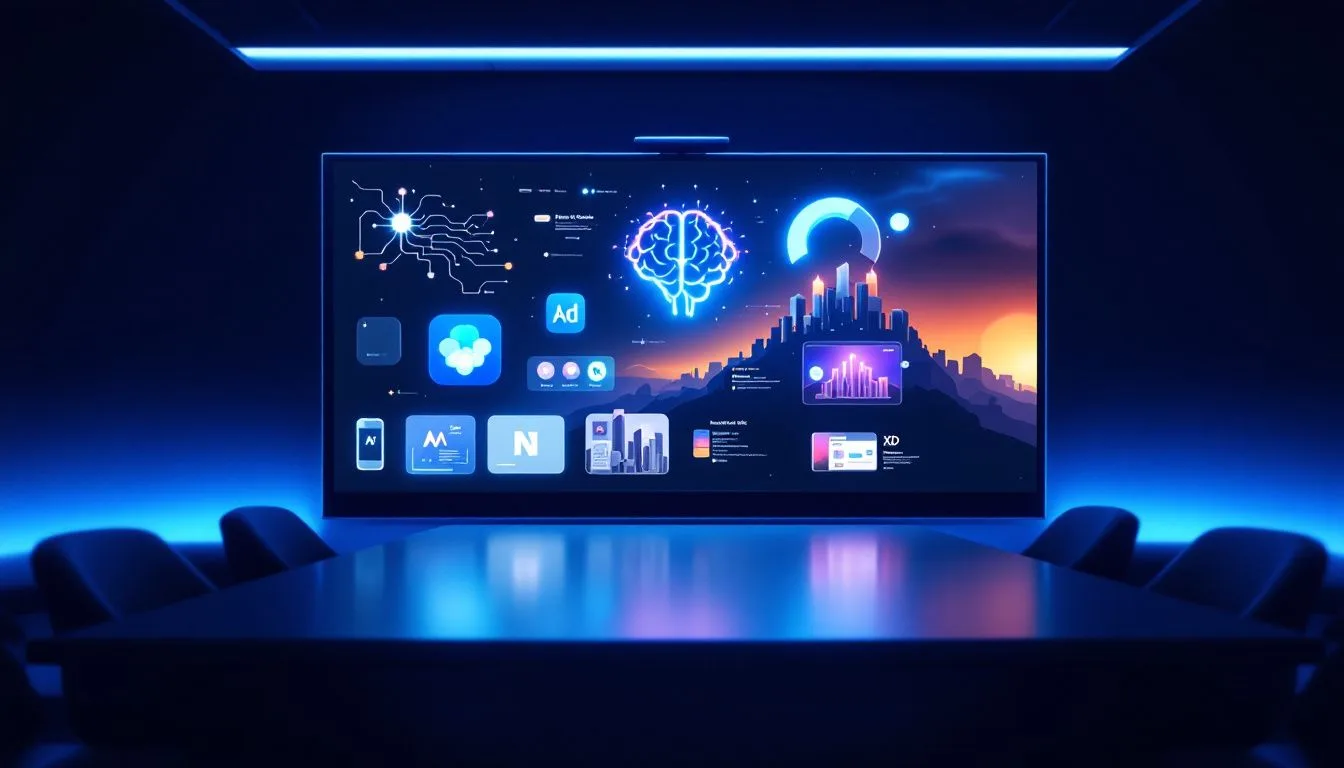
Rapid prototyping is an accelerated process that uses CAD data to quickly generate physical prototypes, greatly expediting the product development timeline. Its main goal is to produce a concrete representation of a new design concept for products, providing stakeholders with something they can see and feel in order to better evaluate and refine the idea. Such an approach promotes faster cycles of iteration and greater innovation by enabling designers to test adjustments on-the-fly. It also supports working with diverse materials including but not limited to plastics, metals, and composites tailored specifically for each individual project’s needs.
As rapid prototyping technology has advanced over time, it now makes possible highly intricate models that were once beyond reach. Additive manufacturing — one aspect of rapid prototyping — stands out by facilitating complex designs and personalized prototype production not feasible with conventional methodologies.
A suite of services within rapid prototyping encompasses techniques such as CNC machining (CNC prototyping), 3D printing, vacuum casting, and quick-turn tooling (rapid tooling). Each method brings distinct benefits depending on what the particular project calls for.
Key Benefits of Rapid Prototyping Services
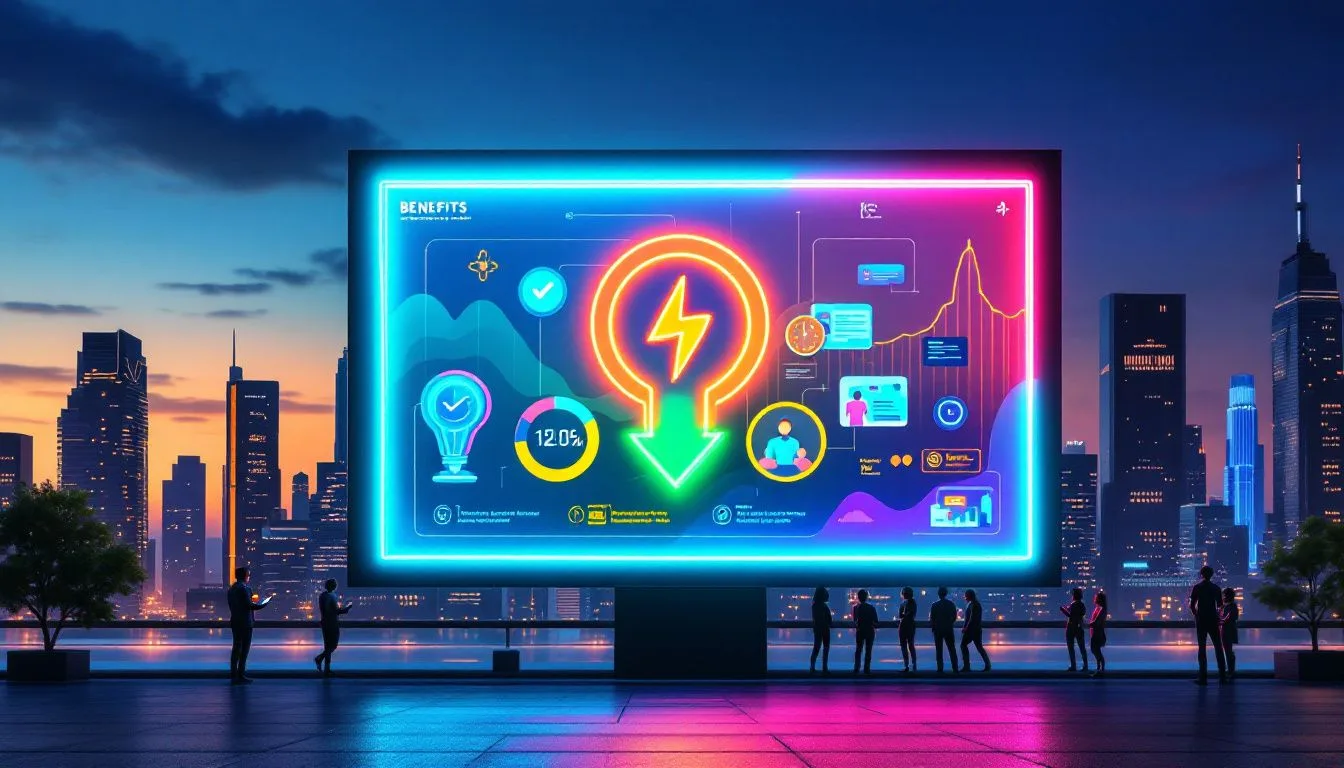
Rapid prototyping offers a substantial reduction in the costs associated with product development by streamlining the testing phase. This approach enables manufacturers to swiftly and economically create prototypes, significantly decreasing financial risks associated with moving forward too quickly with a project. By obtaining early feedback on prototype designs, engineers can pinpoint and correct design flaws more efficiently, cutting down both cost and time spent on subsequent revisions. With rapid manufacturing capabilities at their disposal, parts can be produced in as little as one day—significantly speeding up the overall development process.
This methodology provides an opportunity for early evaluation of safety standards and compliance matters that could pose future design challenges if unaddressed. Advanced 3D printing methods such as SLS (Selective Laser Sintering), SLA (Stereolithography), and FDM (Fused Deposition Modeling) are particularly beneficial due to their quick turnaround times coupled with high detail resolution capability. These technologies excel at constructing intricate shapes that would typically present difficulties for conventional fabrication techniques.
By utilizing rapid tooling processes during development stages, companies are able to thoroughly test design concepts along with material selection before entering large-scale production phases. This practice aids in smoothing out potential hiccups when shifting from prototyping into full-blown manufacturing workflows.
Types of Rapid Prototyping Techniques
Various techniques in rapid prototyping create scale models of physical parts or assemblies from three-dimensional CAD data. Common processes like CNC machining, 3D printing, sheet metal fabrication, and rapid injection molding each offer unique benefits depending on project requirements. Metals and plastics are popular materials in these processes, offering flexibility and precision for various prototype needs. Advanced technologies produce high-fidelity prototypes, ensuring accurate and functional models.
Let’s delve into three key techniques: CNC machining, 3D printing, and vacuum casting.
CNC Machining
Rapid prototyping heavily relies on CNC machining to deliver custom-designed prototypes and production parts that adhere to exacting standards. This process is adept at working with a range of materials, encompassing metals such as aluminum and stainless steel, alongside various plastics including ABS and nylon. The stringent precision offered by CNC machines—which can achieve tolerances close to +/- 0.0025 mm for metals and +/- 0.05 mm for plastics—facilitates the creation of superior quality parts that conform to rigorous industry benchmarks, making them indispensable in sectors like automotive, aerospace, medical devices, and consumer electronics.
Adaptable to a multitude of design requirements, both CNC milling and turning are key techniques used not only for rapid prototyping but also for small-scale production runs aimed at validating designs swiftly. Companies specializing in this field such as LKprototype offer an array of material choices along with numerous surface treatment options designed to satisfy both functional necessities and visual preferences of their prototypes or end-use products.
3D Printing
The advent of 3D printing has been a game-changer in the realm of rapid prototyping, offering the means to swiftly and cost-effectively manufacture intricate designs. The most commonly employed technologies in this field are Selective Laser Sintering (SLS), Stereolithography (SLA), and Fused Deposition Modeling (FDM). These techniques have found widespread use across diverse industries due to their distinctive advantages: SLS is celebrated for its swift production times, functional mechanical characteristics, and fine detail at an economical price point, SLA boasts a superior surface quality, whereas FDM excels in material diversity, including options like ABS, PC, and ULTEM.
One remarkable benefit of 3D printing is its capability for quick delivery—certain components can be constructed and dispatched all within the same day. This brisk efficiency coupled with cost-effective prototyping services positions 3D printing as an invaluable resource for producing prototypes rapidly.
Star Rapids particularly champions SLA-based 3D printing when crafting high-quality prototypes—a strategy exemplified during their contribution to Myant’s CES project in 2018.
Vacuum Casting
LKprototype Vacuum casting stands out as a superior option for low to medium volume production, renowned for its capacity to craft high-quality, intricately detailed prototypes. This technique makes use of silicone molds derived from master patterns commonly crafted through CNC machining or 3D printing techniques. By injecting liquid resin into these molds under vacuum pressure, parts are cast with exceptional precision and smooth finishes. Vacuum casting is highly versatile, suitable for creating parts that are rigid, flexible or even rubber-like in nature across various applications.
Despite the cost-efficiency of vacuum casting for small-scale manufacturing endeavors, the longevity of silicone molds presents a limitation. They yield about 20 to 25 pieces before showing signs of wear. Nevertheless, this method is advantageous due to its minimal waste generation, it uses materials sparingly and often allows recycling of unused resins.
The time frame required to complete a vacuum casting project typically spans from three days up to ten days contingent upon the complexity involved and quantity of items being produced.Still, need help? Contact Us: lk@lkprototype.com . Need a PROTOTYPE or PARTS machining quote? Quote now
Choosing the Right Rapid Prototyping Method
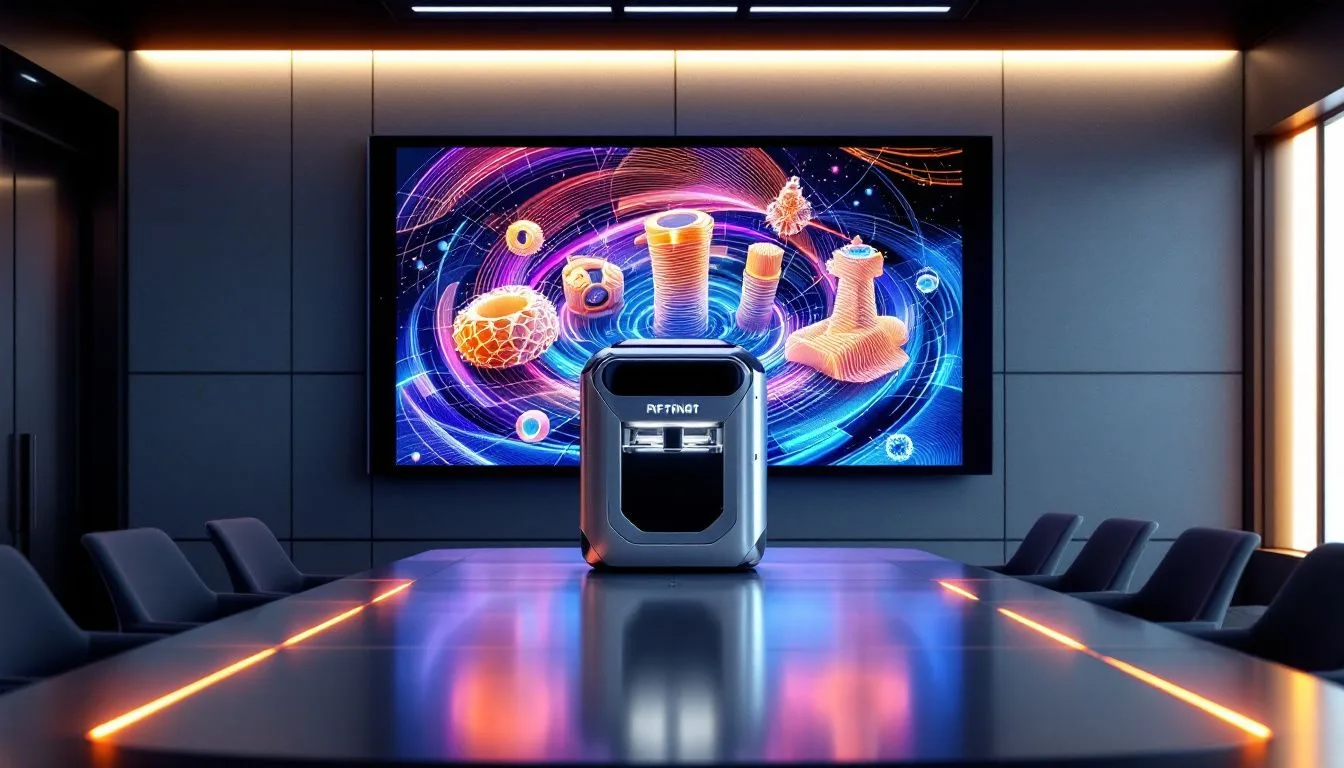
Choosing the right method for rapid prototyping depends on various aspects such as cost considerations, design intricacy, intended functionality, and the timeframe allocated for development. The end-use of the prototype is also a deciding factor in selecting the most fitting technology.
For example, when precision is paramount and only a small quantity of items are needed, CNC machining stands out as an optimal choice. Conversely, 3D printing offers a quick and cost-effective solution for creating intricate prototypes efficiently. For producing high-detail parts in low to medium quantities, vacuum casting emerges as an excellent option.
The overarching objective in this process is to facilitate a seamless progression from digital designs to tangible versions swiftly. This enables designers and engineers to make necessary modifications with ease, enhancing overall efficiency in product development.
Rapid Tooling for Prototypes
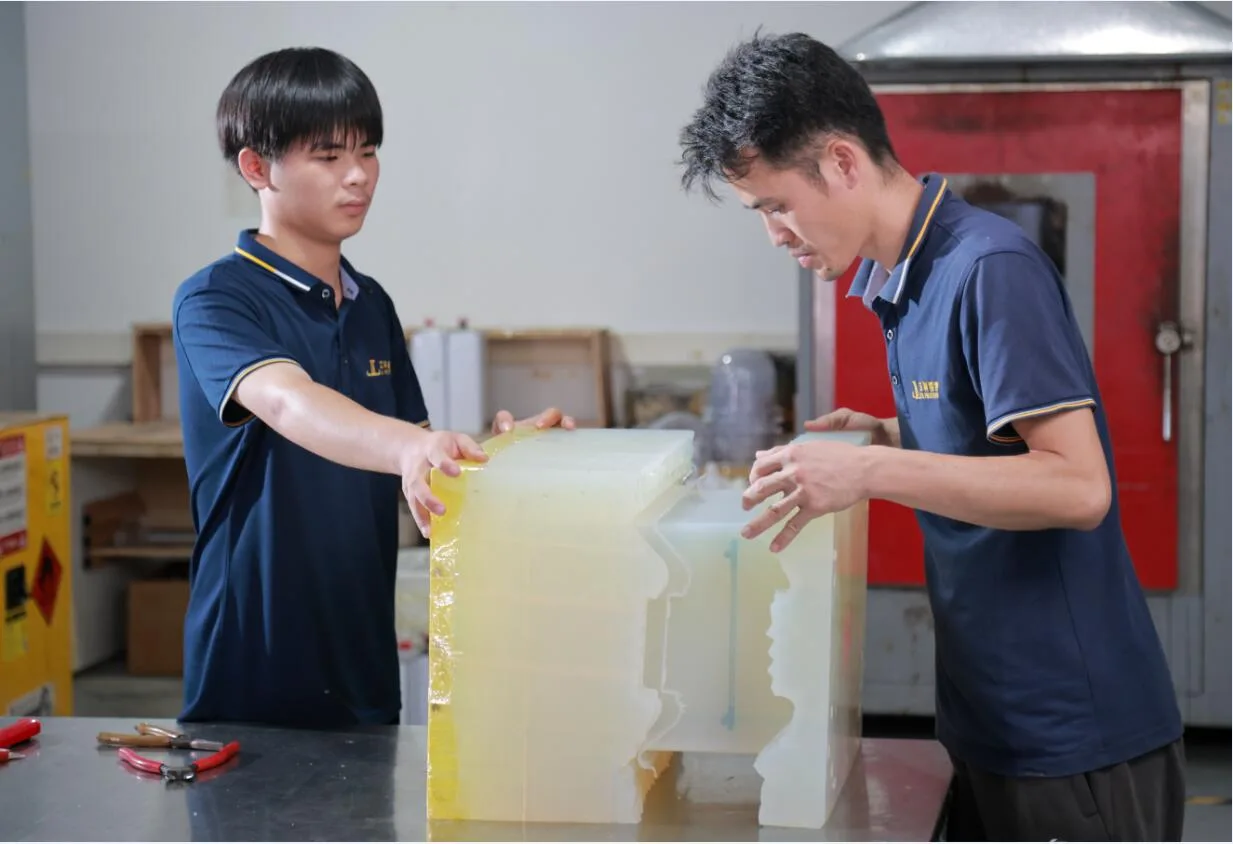
Rapid tooling serves as a critical intermediary between the stages of prototyping and mass production, offering economical means for swiftly generating molds and equipment. This technique encompasses methods such as soft tooling with silicone for limited quantity manufacturing, along with hard tooling employing metals when larger quantities are needed.
Embracing 3D printed molds in the realm of plastic injection molding is an advanced method that facilitates the manufacture of functional prototypes and modest batch sizes while minimizing both expenses and timeframes. To illustrate, fabricating aluminum molds through machining is quintuple to 10 times faster than producing steel ones, thus slashing costs and shortening lead times significantly.
Rapid injection molding delivers cost-effective molded components of superior quality at an accelerated pace. By taking advantage of rapid tooling strategies, companies can compress their production schedules from several weeks down to mere days—enabling faster product launches into the market with heightened efficiency.
Surface Treatment Finishing Options
Enhancing the visual appeal and functionality of components is achieved through various surface treatment processes. Techniques such as anodizing, which forms a protective oxide layer on aluminum to boost its corrosion resistance. Electroplating, involving the application of metal coating via electrical current for enhanced durability and look. And electropolishing that provides metals with a reflective high gloss finish are widely used.
Alternate methods include sandblasting—propelling abrasive materials at surfaces for cleaning—and powder coating—a process in which dry paint powder is applied then heat-cured to create a resilient coat.
At LKprototype, we provide extensive surface treatment options catering to different materials including metals, composites, and plastics. Our services ensure that every final product fulfills both practical performance requirements and aesthetic expectations.
Case Studies: Successful Rapid Prototyping Projects
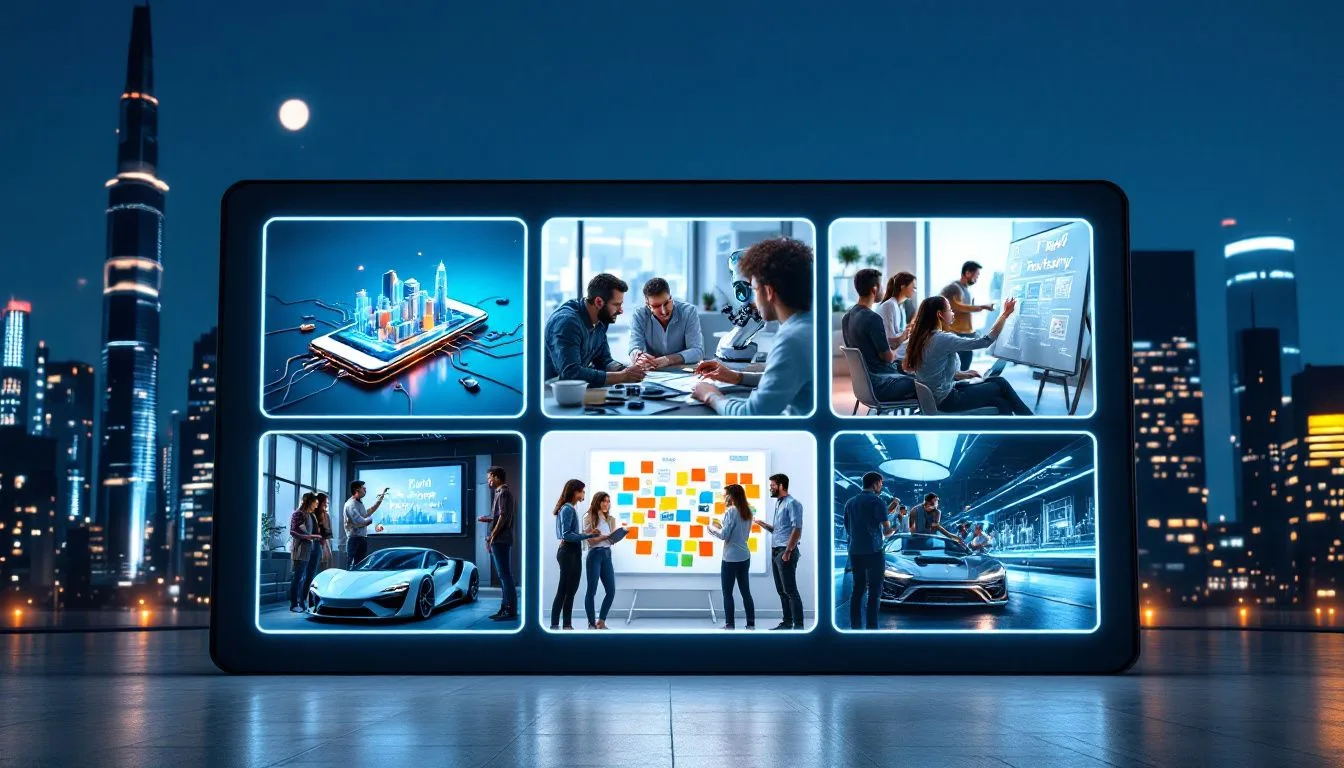
Many successful projects have demonstrated that physical prototypes can stimulate innovative ideas and inventive solutions by offering tangible, hands-on experiences. An exemplary case occurred during the COVID-19 pandemic when engineers joined forces with medical professionals to swiftly create a vital medical device prototype in less than three weeks, demonstrating rapid prototyping’s remarkable speed and efficacy. This phase of involving users and stakeholders allowed for collaborative input and valuable critique, which significantly improved the quality of the end product.
Similarly impressive were the quick-turnaround prototypes crafted for Myant prior to their significant presentation at CES 2018. By exposing design issues at an early stage, these rapid prototypes reduced chances of encountering market-launch failures. The profound influence that rapid prototyping exerts on streamlining the journey from initial idea to triumphant market debut is underlined by such examples, underscoring its essential role in refining both process and concept within product development.
Partnering with a Reliable Manufacturing Service
Having a trustworthy manufacturing services provider is essential for maintaining the high quality and uniformity of both prototypes and final production components. Look for critical certifications like ISO 9001:2015 Click here to view LKprototype ISO 9001:2015, ISO 13485, and IATF 16949:2016 when selecting a partner as they demonstrate compliance with rigorous quality management systems. A reliable manufacturing ally ought to offer thorough quality assurance measures such as dimensional checks and visual examinations to ensure every order meets standards of consistency and accuracy.
The ability to obtain quick quotations is fundamental in keeping projects on schedule. Aim for partners capable of delivering quotes within a day or even mere hours provided that clear RFQ information is available.
Engaging with an esteemed manufacturing service paves the way for seamless progression from prototyping through to full-scale production while upholding top-notch levels of quality and efficiency throughout your project’s lifecycle.
From Prototyping to Final Production
By engaging with service providers like LKprototype and Star Rapids, the progression from prototyping to final production becomes more efficient. These organizations offer flexible, scalable solutions without demanding a minimum number of orders, ensuring a seamless evolution from prototype models to parts ready for end use. Specifically, LKprototype expedites product development by swiftly creating prototypes and manufacturing parts in just days following order placement.
The implementation of advanced 3D printing materials that replicate the properties found in traditionally manufactured components serves to improve the accuracy of prototypes while also diminishing turnaround times within digital manufacturing landscapes. Clients can receive insights from Design For Manufacture analysis in as little as 12 hours, which promotes quicker design modifications and enhancements.
Ultimately, this process guarantees that the finished products adhere strictly to intended specifications and maintain high-quality standards before they are sent into mass production or introduced into market circulation.
Summary
Rapid prototyping has significantly transformed product development by providing a variety of methods and services tailored to diverse requirements and financial considerations. Techniques like CNC machining, 3D printing, vacuum casting, and rapid tooling each offer distinct advantages that contribute to the efficiency, precision, and affordability in producing functional prototypes. Grasping these methodologies and collaborating with dependable manufacturing services facilitates seamless progression from prototype creation to final production phases while guaranteeing superior quality products poised for successful market introduction.
Frequently Asked Questions
What is the typical lead time for urethane casting prototypes?
The production of urethane casting prototypes takes about 5 to 10 days. This period is subject to change based on the project’s intricacy and quantity requirements but ensures an effective manufacturing process that can adapt to diverse specifications.
What are the advantages of vacuum casting over other prototyping methods?
Vacuum casting provides high precision and excellent surface quality, making it a cost-effective choice for low-volume production with faster production times compared to CNC machining and 3D printing.
This makes it an ideal method for creating detailed prototypes efficiently.
How does CNC prototyping help cut down production costs?
CNC prototyping effectively reduces production costs by identifying design flaws early, enabling efficient iterations, optimizing materials and processes, and mitigating associated risks.
This proactive approach leads to significant savings in the overall manufacturing process.
What certifications should I look for in a reliable manufacturing partner?
For a reliable manufacturing partner, it’s important to look for certifications like ISO 9001:2015, ISO 13485, and IATF 16949:2016. These signify that the partner conforms to established quality benchmarks in their manufacturing processes.
What industries are CNC prototypes suitable for?
CNC prototypes are suitable for various industries, including automotive, aerospace, medical devices, consumer electronics, and industrial equipment. Their versatility makes them ideal for applications requiring precision and efficiency.
Still, need help? Contact Us: lk@lkprototype.com
Need a PROTOTYPE or PARTS machining quote? Quote now