Medical device prototyping involves creating early models of medical devices to test, refine, and perfect designs before mass production. By quickly identifying and resolving design flaws, prototyping ensures that the final product is safe, effective, and meets regulatory standards. In this article, we will explore the key stages and advanced techniques of medical device prototyping, offering insights for anyone involved in the development of innovative medical technologies.
Key Takeaways
Medical device prototyping is essential for transforming concepts into functional products, allowing for early design validation and risk reduction.
The prototyping process involves key stages such as conceptualization, material selection, and iterative testing, enhancing device functionality and ensuring compliance with healthcare standards.
Advanced techniques like rapid prototyping and 3D printing significantly improve efficiency in developing medical devices, leading to quicker market entry and better patient outcomes.
Understanding Medical Device Prototyping
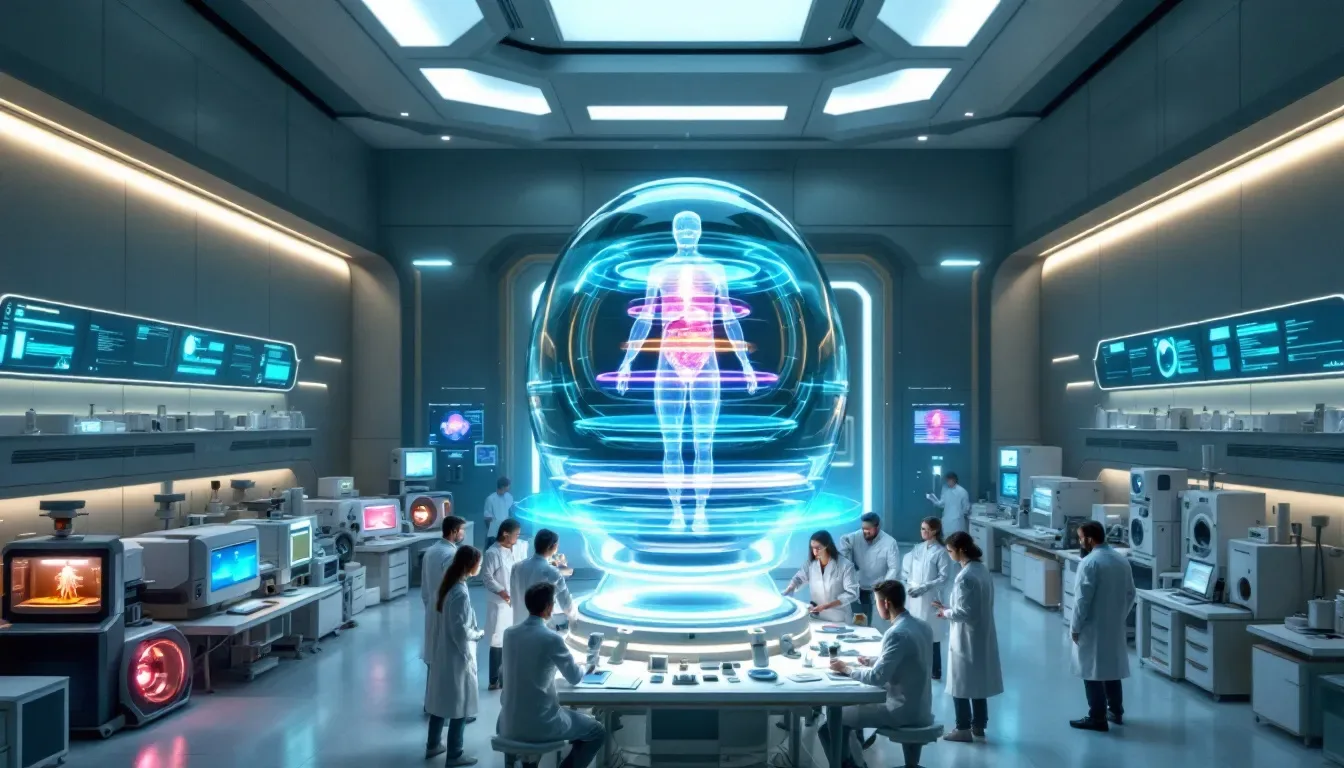
The creation of preliminary versions of medical devices, known as medical device prototyping, combines practical aspects and innovative elements to examine and refine design concepts. This step in the development process is crucial for designers and engineers to bring their ideas into reality while addressing any imperfections early on, consequently improving how these devices function. More than just producing tangible models, this stage involves continuous evolution of designs aiming to satisfy the stringent demands prevalent in healthcare.
Serving as a pivotal element within the progression from concept to usable product, prototyping bridges theoretical planning with real-world application. It facilitates detection of potential shortcomings while honing solutions, assuring that upon completion, medical devices are efficient and secure for patients. Prototyping’s absence would lead to a longer timeline fraught with mistakes during device development. Such outcomes could compromise patient well-being and escalate costs associated with healthcare provision.
As we delve deeper into this subject matter later on, we will unpack what encompasses medical device prototyping—the phases it includes along with cutting-edge methods employed—and its importance throughout the development lifecycle. Grasping these facets offers individuals involved—be they designers or health professionals—a greater understanding of the innovation propelling contemporary advancements in medical equipment technology.
What is Medical Device Prototyping?
The creation of early versions or models of medical devices, known as medical device prototyping, is integral to testing design concepts and determining their practicality. This stage is vital for transforming the initial concept into a product that is both operational and safe. The process commences with validating the core idea through a proof-of-concept phase, where it’s converted into a functional model. Establishing the feasibility of this fundamental notion at an early stage lays down a solid foundation for subsequent detailed development phases.
Medical device prototyping employs various forms of prototypes such as physical, analytical, focused, and complete models. Each tailored to fulfill distinct objectives ranging from component testing to overall functionality assessment. Utilizing these models allows designers to identify potential issues promptly and apply necessary modifications accordingly. Such thorough vetting during prototype stages guarantees that the final product adheres strictly to all requisite standards while operating effectively.
The Role of Prototyping in Medical Device Development
The prototyping stage is critical in the evolution of medical devices, acting as a crucial step from conceptual design to tangible implementation. During this phase, designers have the ability to bring their ideas into physical form, enabling them to pinpoint potential defects and improve both function and user experience of medical devices. This aspect not only bolsters the overall device design but also certifies compliance with stringent healthcare industry standards.
Nevertheless, navigating through the prototyping process can present various obstacles. Setbacks such as delayed delivery of components, unexpected modifications that arise during development, and required collaboration across diverse technical fields can disrupt timelines and inflate costs. It’s imperative that efficient project management and inter-disciplinary cooperation are prioritized in order to overcome these barriers on the path toward prototype completion.
By confronting such difficulties early within the development cycle, teams increase their chances of delivering a final product that is proficient for clinical application while ensuring patient safety remains paramount.
Key Stages in the Medical Device Prototyping Process
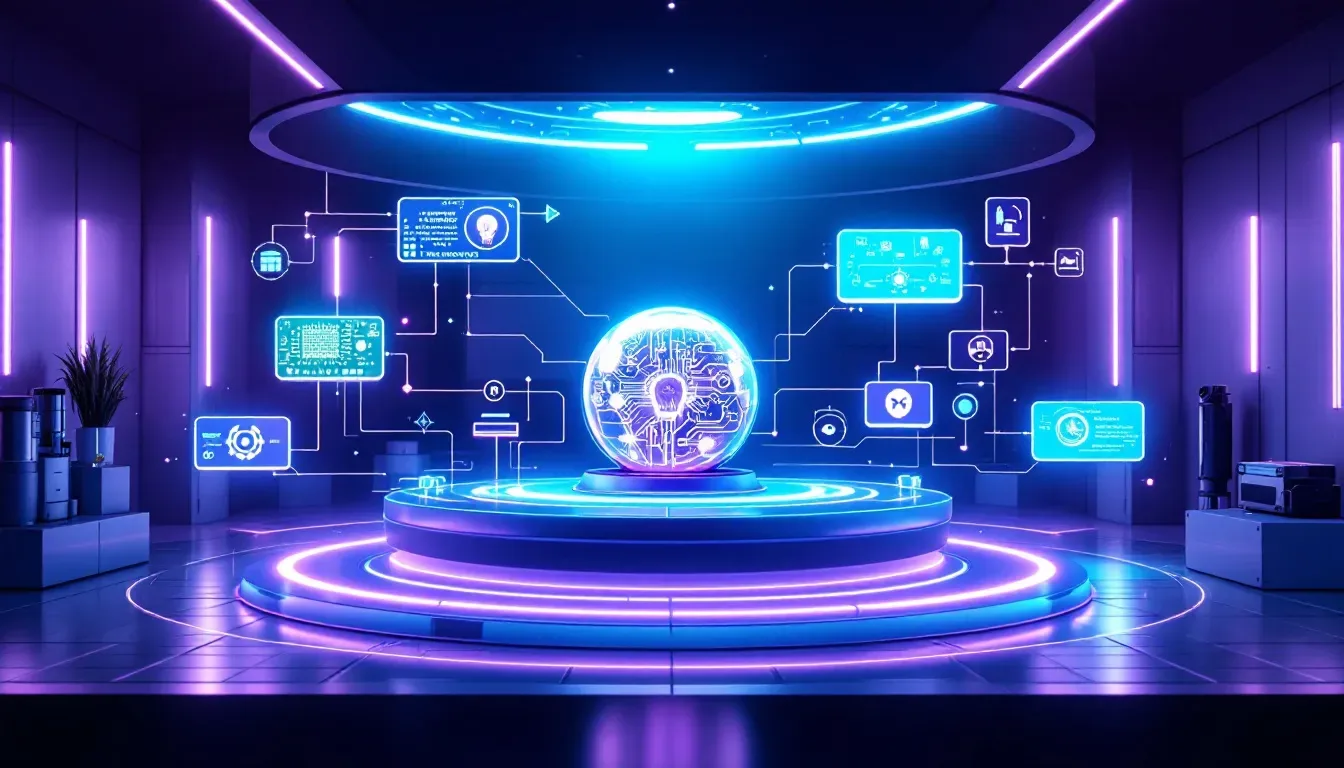
The process of prototyping medical devices comprises numerous critical stages, each instrumental in the advancement of cutting-edge medical technology. Starting with an initial proof of concept and progressing to a pilot prototype’s production, every step is key to honing both design and functionality for the device. Adherence to this sequence enables developers to minimize development duration, ensure compliance with necessary specifications, and boost prospects for market acceptance.
Thanks to contemporary advances in prototyping methods, there has been a surge in efficiency and success rates within medical device creation efforts. Developers harness these avant-garde techniques not only to elevate manufacturing quality but also curtail unnecessary expenditure – paving the way toward fabricating devices that foster improved patient care while simultaneously driving down healthcare expenses.
In subsequent sections below, we will explore the indispensable phases within the medical device prototyping procedure. From conceptual groundwork through rigorous testing cycles plus iterations required for refinement.
Conceptualization and Preliminary Design
The prototyping process for medical devices originates from an innovative idea with the capacity to revolutionize healthcare services. In the early stages, known as conceptualization, both designers and engineers collaborate to devise an initial design that accurately reflects the device’s anticipated function. This stage includes establishing test goals anchored in both regulatory standards and functional requirements to confirm that the design complies with all mandated regulations.
Laying down a solid foundation for a medical device hinges on a meticulous planning and design phase, where focus is placed on its intended use along with adherence to regulatory mandates. Designers are tasked with formulating a comprehensive plan which steers the development of the device through subsequent stages. It is imperative during this preliminary phase to ensure compliance with relevant criteria so that upon completion, the device operates exactly as it was designed to do so.
Material Selection and Prototype Fabrication
Selecting the appropriate materials is an essential aspect of the medical device prototyping process, as it influences both the function and safety of the end product. Materials that are biocompatible, such as titanium and silicone, are often chosen to guarantee patient well-being. Typical substances used in manufacturing medical devices include high-temperature plastics, medical-grade silicone rubber, and a variety of metals like stainless steel. These substances should be thoughtfully picked out to align with all necessary regulatory standards and functional demands.
The construction phase employs multiple techniques which include CNC machining for precision parts along with molding, casting, and 3D printing for various components within the manufacturing framework. Injection molding stands out among these methods due to its cost-effectiveness when producing large quantities while also enabling swift iteration during testing phases.
In contrast to injection molding’s traditional approach, 3D printing is a more flexible solution allowing for complex prototype production not possible through conventional means. Additive manufacturing encompasses this technology by empowering developers with rapid fabrication capabilities tailored towards intricate designs specific to customized prototypes.
Ensuring proper selection of materials coupled with effective fabrication strategies aids in crafting fully operational prototypes that adhere strictly to designated regulations while performing exactly as envisioned—pivotal for confirming both efficacy and patient protection upon completion of said device.
Testing and Iteration
The meticulous testing of medical devices is critical for confirming that they function as designed and comply with all regulatory requirements. Testing early in the prototyping stage can pinpoint design issues, thereby reducing future costs linked to making adjustments at advanced stages. Ensuring the device’s safety and efficiency through initial tests is crucial.
Creating successive versions of prototypes constitutes an iterative process, with each iteration refining upon its predecessor informed by feedback and test outcomes. Early-stage development employs proof-of-concept prototypes to ascertain whether the concept holds using materials that may not be durable.
Alpha prototypes primarily assess physical dimensions and visual appeal, often utilizing 3D printing techniques. In contrast, beta prototypes delve into assessing how well the device functions and its manufacturability—shedding light on particular characteristics of interest. Regular reviews and updates throughout this phase are instrumental in uncovering and rectifying any imperfections promptly, thus averting expensive mistakes as development progresses.
Through continual enhancements achieved during prototyping iterations—and extensive verification—the end result is a medical device rigorously tailored to fulfill necessary standards while delivering assured performance for patients’ benefit.
Advanced Techniques in Medical Device Prototyping
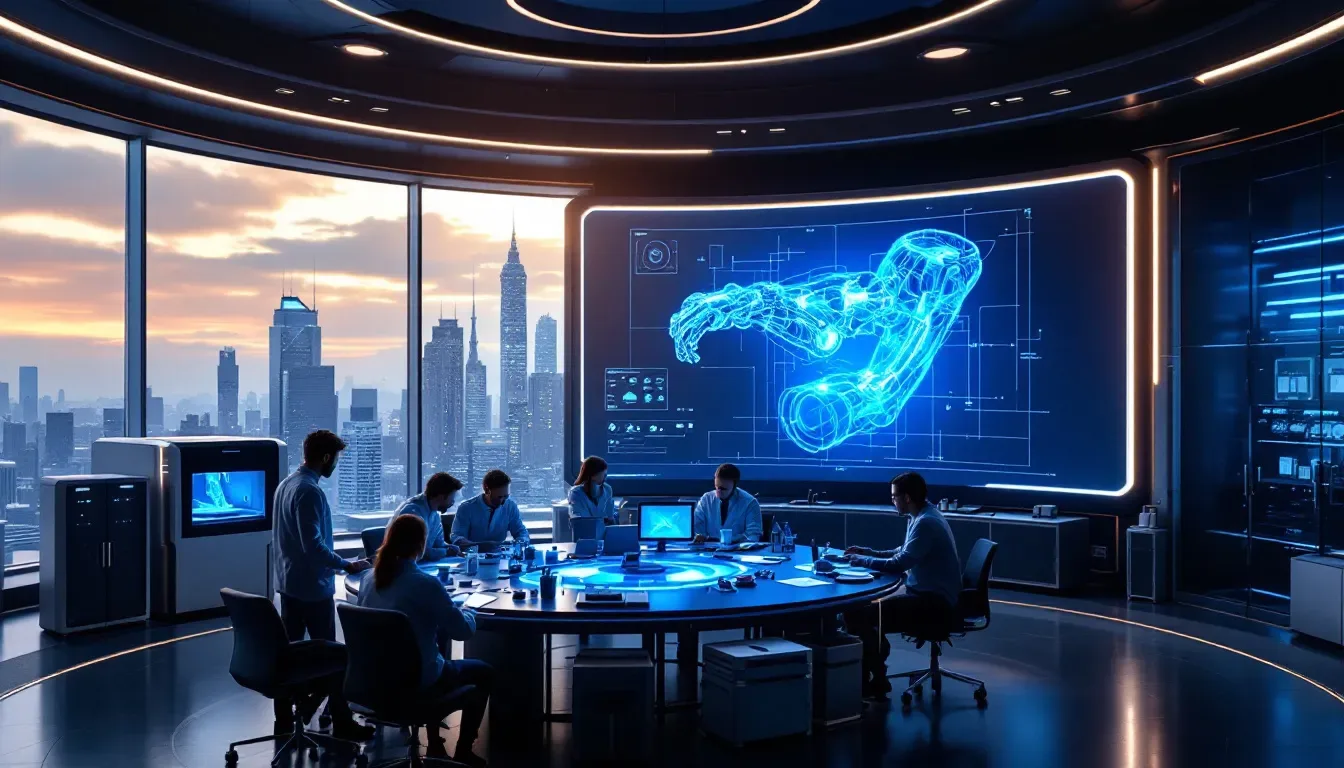
Technological advancements have transformed the prototyping process for medical devices, leading to faster and more precise development. Methods like CNC machining, 3D printing, and rapid prototyping have improved the capability of generating functional prototypes with intricate details. This enhanced prototyping enables developers to replicate user interfaces and functionalities effectively, ensuring that the final device complies with all required standards and functions as planned.
The implementation of these sophisticated methods allows for the creation of more refined and accurate prototypes which contribute to a higher quality end product. We will delve into each advanced technique in subsequent subsections and examine their influence on shaping the medical device prototyping landscape.
Rapid Prototyping for Medical Devices
The development process of medical devices is greatly enhanced by the utilization of rapid prototyping, which serves as a crucial element in streamlining and improving design methodologies. By substantially reducing the time it takes to progress from an initial concept to entry into the market, rapid prototyping facilitates more frequent updates and adjustments based on user input. The result is an expedited journey towards commercial availability, offering advantages for both manufacturers and those who require medical care.
Employing rapid prototyping allows developers to swiftly generate functional prototypes that can undergo extensive testing and improvement. This step in development is imperative for assuring that the end product adheres to all required standards and functions according to its purpose. Through rapid prototyping, innovative medical devices are brought forth, positively affecting patient care while simultaneously aiming at lowering healthcare expenditures.
CNC Machining and Injection Molding
CNC machining employs computer-guided tools to meticulously shape materials, and is crucial for crafting intricate prototypes of medical devices. It’s widely utilized with metals and durable plastics due to its precision in adhering to particular design stipulations. Techniques such as CNC milling and turning are instrumental in achieving the exact customizations and elaborate designs necessary for these devices.
In contrast, injection molding is a favored process for high-volume manufacturing of medical device parts. Its cost-effectiveness comes into play when producing parts at scale while also allowing swift prototype testing. The method supports the rapid production of detailed prototypes that not only meet all required standards but also ensure that the finished product functions correctly.
Additive Manufacturing and 3D Printing
Additive manufacturing, encompassing 3D printing processes, provides remarkable adaptability in terms of shape and form for tailored device prototypes. By building up layers of materials based on digital models, this method achieves intricate components that may be beyond the reach of conventional production techniques. It empowers creators to swiftly generate precise prototypes compliant with all requisite standards while ensuring they operate as designed through advanced digital manufacturing technologies.
The adoption of 3D printing has surged within the realm of medical device prototyping due to its capability for quick alteration and refinement. Developers can rapidly tweak their designs by incorporating user feedback and insights from testing sessions. This approach streamlines the advancement of groundbreaking medical devices aimed at enhancing patient care quality while simultaneously striving to diminish healthcare expenditures.
Ensuring Safety and Compliance in Medical Prototyping
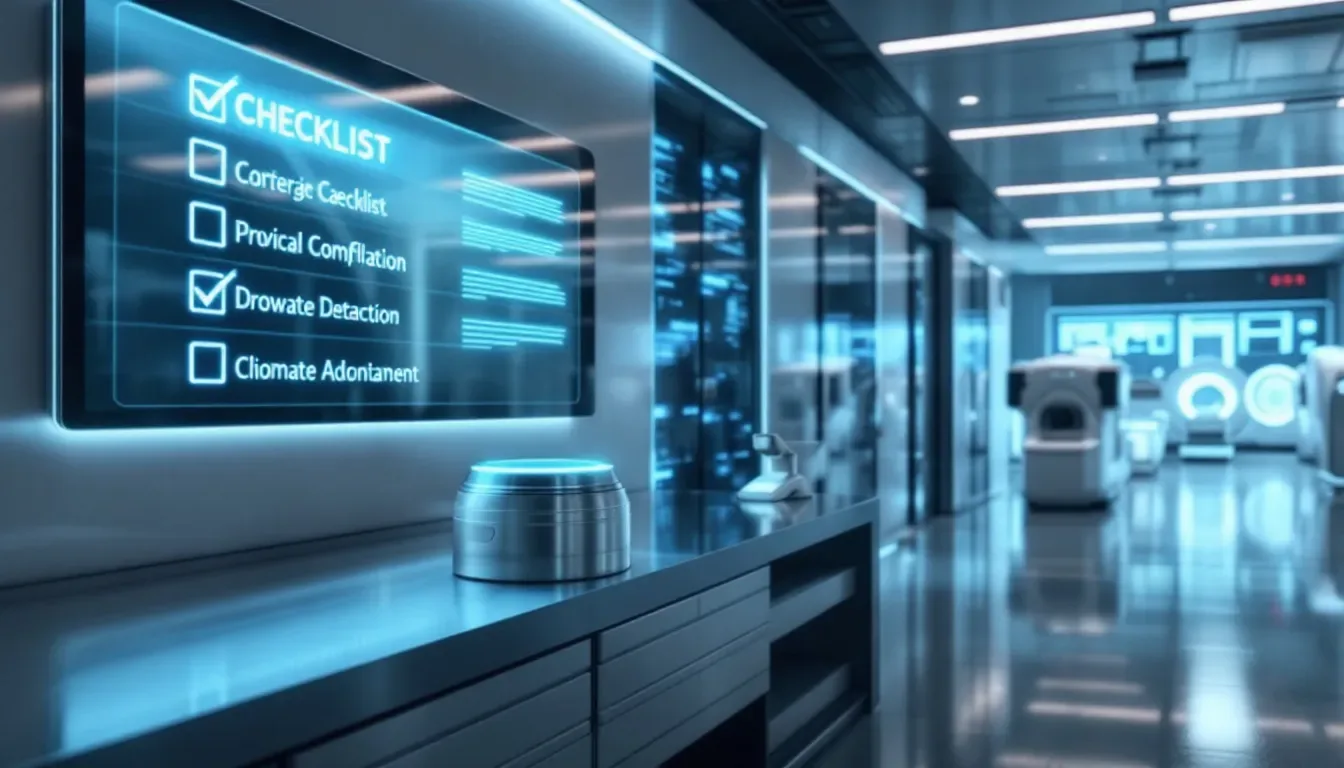
In the development of medical devices, adhering to regulatory compliance stands as a crucial hurdle. The depth of a manufacturer’s knowledge concerning regulations can greatly influence the success of their product. During device prototyping, its role is critical in ensuring that new medical devices adhere to stringent regulations regarding efficacy and safety, thus bolstering both aspects of the finished product through successive testing and improvements.
Conducting safety evaluations is imperative for confirming that no hazards are posed by medical devices to end-users. For comprehensive user trials and regulatory assessments, having a functional prototype at hand is indispensable. It confirms compliance with all necessary benchmarks. By integrating feedback from users into rigorous test regimes, manufacturers are empowered to forge safe and efficacious solutions for patients’ needs.
Contemporary techniques within the realm of device prototyping have markedly advanced validation procedures along with testing protocols — this evolution tackles regulatory challenges head-on effectively. Employing these progressive approaches enables developers not only to satisfy essential standards, but also ensures that their innovative medical products function according to design intentions—thereby enhancing patient care quality while concurrently minimizing healthcare expenditures.
Usability Testing and Human Factors
The process of usability testing stands as a pivotal element in the development of medical devices, serving to confirm that these devices are user-friendly, secure, and effective. Engaging with device prototypes allows designers to evaluate their ergonomic design and intuitive nature during use. By integrating feedback from this interactive phase into the prototyping process, designers can make essential modifications while simultaneously meeting regulatory demands for verification and validation. This ensures that the final product is crafted with consideration for the end-user’s requirements.
By subjecting prototypes to stringent evaluation early in their creation, developers have an opportunity to discover any potential issues that could arise and modify designs accordingly so as to bolster both functionality and safety measures. Usability testing transcends merely improving design aesthetics. It plays a critical role in certifying ease of use compliance alongside adherence to established standards.
Concentrating on human factors empowers developers in shaping medical devices aimed at amplifying patient outcomes by significantly enhancing user interaction with these products.
Regulatory Standards and Validation
Ensuring adherence to regulatory benchmarks is a vital element of prototyping medical devices. It’s imperative to meticulously record design choices and results from tests in order to showcase conformity with the standards set by regulatory authorities. For FDA approval in the manufacturing of medical devices, it’s important that there is a thoroughly documented quality control strategy confirming that the end product conforms to all mandated criteria.
Securing compliance with global norms is fundamental for obtaining permission to enter the market. When selecting a manufacturer for device production, their experience with regulations becomes particularly significant, especially concerning Class 2 and Class 3 medical devices. Fulfilling every regulatory mandate guarantees the development of safe and efficient medical tools which can enhance patient care while also diminishing healthcare expenses.
Case Studies: Successful Medical Device Prototypes
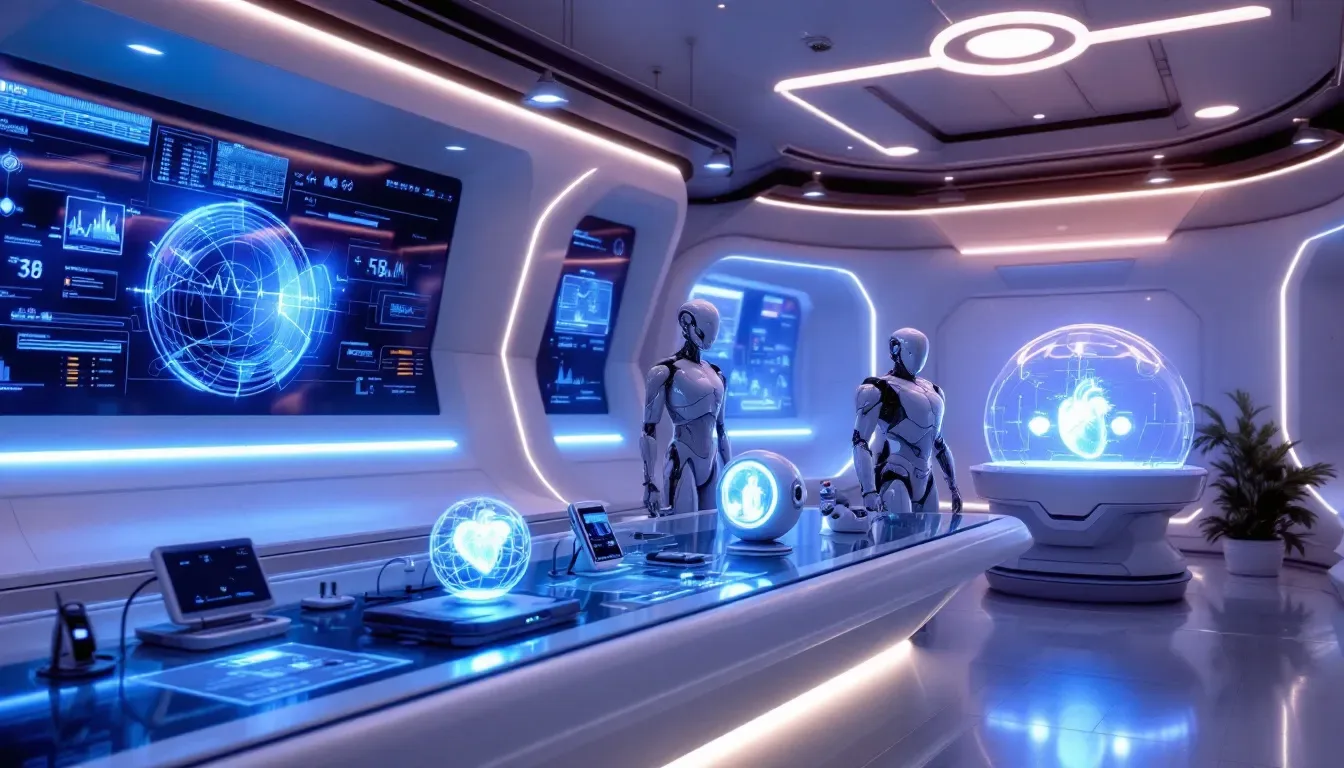
Exploring case studies of successful medical device prototypes offers practical understanding into pioneering solutions and the intricacies of their creation. Such instances underscore how critical the role of prototyping is in enhancing patient care, emphasizing that comprehensive testing and repeated refinement are essential.
Reviewing these real-world examples equips developers with crucial insights and encourages them as they embark on their own medical device development endeavors.
Wearable Health Monitoring Devices
A case study highlights the creation process of a wearable device designed to monitor cardiac health. This device offers constant tracking of heart-related metrics, delivering immediate health information that improves care for patients.
Developers utilized rapid prototyping techniques and extensive testing to construct a prototype that was both functional and compliant with all required standards. This advancement in medical technology has markedly elevated patient care by facilitating ongoing monitoring of their health status.
Innovative Surgical Instruments
In a case study of the development process for a minimally invasive surgical tool, the prototype underwent numerous modifications and enhancements. The result was an instrument that transformed surgical methods by elevating both function and ergonomic design. Concentrating on precision and user-friendliness enabled creators to produce a medical device that not only improved patient results but also shortened recovery periods.
The case study underscores the critical role that extensive testing and repeated iterations play in crafting groundbreaking medical devices. It highlights how these steps are pivotal in ensuring innovative solutions meet high standards of efficacy in the medical field.
Implantable Medical Devices
Advancements in neurological treatments have been underscored by the creation and evaluation of a neural implant prototype, which showcases innovation through its design and extensive testing. Prototyping for such implantable devices is particularly challenging because they must meet rigorous safety standards. Using sophisticated prototyping methods coupled with comprehensive testing has enabled developers to produce a device dedicated to enhanced neural monitoring that facilitates prompt patient interventions.
As a result of this pioneering effort, there has been an improvement in the health results for patients along with an elevation in the standard of care provided.
Choosing the Right Medical Device Prototype Manufacturer
Choosing a manufacturer that specializes in producing top-tier medical device prototypes is vital for the triumph of your project. It’s imperative to engage manufacturing services proficient in crafting both bespoke medical prototypes and production components, which are central to developing innovative and effective medical devices.
Collaborating with a reliable manufacturer guarantees that the prototypes adhere to all required standards and perform according to their intended purpose.
Key Factors to Consider
When selecting a manufacturer for your medical device prototype, prioritize those with the following offerings:
The capacity to carry out rapid prototyping
Proficiency in 3D printing technology
Expertise in CNC machining processes
Immediate solutions for manufacturing needs
The ability to produce on demand is essential for maintaining flexibility within the supply chain. This feature facilitates the production of components swiftly and diminishes waiting periods.
It’s critical that your chosen partner has versatile production capabilities, ranging from individual units to mass manufacturing. Such adaptability is necessary to accommodate potential growth and expansion of your project.
Choosing suitable materials is key to ensuring that prototypes adhere to safety and functional standards. Opting for manufacturers equipped with comprehensive facilities and robust networks can offer developers swift turnaround times coupled with superior quality output, which guarantees both patient safety as well as product effectiveness once it reaches its final form.
Benefits of Partnering with LKprototype
LKprototype holds an ISO 9001:2015 certification, underscoring their dedication to quality management systems specifically tailored for the prototyping of medical devices. They provide swift manufacturing solutions using automated machines within their facility, which significantly reduces industry standard lead times by over half. Possessing more than ten years in the field, LKprototype is well-versed in refining designs and offers comprehensive support from the initial device prototyping phase through to full-scale production.
The process of engineering validation and testing at LKprototype allows for quick adjustments and ensures that designs are ready for mass production while maintaining a high standard of quality for prototypes. Collaborating with LKprototype grants developers access to extensive experience as well as a strong commitment to quality assurance, helping guarantee that their medical devices adhere to all required standards and function according to plan.
Overcoming Challenges in Medical Device Prototyping
Device prototyping enhances teamwork and dialogue among key players, such as medical experts and developers, leading to better design results. The intricate task of merging electronic, mechanical, and software components in a medical device necessitates efficient coordination amongst engineers. Establishing a methodical process for tracking adjustments ensures that prototypes progress consistently while adhering to relevant regulations.
Controlling timeframes and budgets is pivotal for the triumph of projects involving the prototyping of medical devices. Emphasizing small-scale production while minimizing economic risks promotes rapid entry into the market without requiring a minimum number of orders. Proficient handling of time frames and financial resources is vital for project success, guaranteeing that the finished product fulfills all mandatory standards and functions according to its purpose.
Managing Cross-Disciplinary Collaboration
Prototyping for medical devices encompasses various fields such as electronic, mechanical, and software engineering. It’s essential that these disciplines work together to integrate their respective contributions and articulate specific requirements. This collaboration is key to guaranteeing the unified operation of every component within the device. To effectively oversee alterations and maintain smooth progress in prototype development, implementing a well-defined procedure for recording changes is imperative.
To keep teams synchronized throughout the evolution of prototypes, a methodical strategy for modification management is necessary. Employing a tracking system that records adjustments made by different sectors of engineering helps ensure that prototypes adhere to all required standards and operate correctly.
Handling Modifications and Iterations
The significance of cross-disciplinary dialogue and teamwork is underscored by the fact that alterations made in one area can have implications for others, especially during the prototyping phase. It’s essential to adeptly handle these changes to ensure cohesive operation among all aspects of the medical device. Embracing a cycle of repeated prototyping and consistent updates enables developers to spot and rectify design issues promptly, significantly reducing potential high-cost mistakes as development progresses.
Engaging in repetitive cycles of prototyping plays a pivotal role in uncovering design imperfections at an early stage while also facilitating ongoing enhancement of the medical device. Rigorous examination and refinement across several iterations lead to producing medical devices that comply with all regulations and perform according to their intended use.
Time and Budget Management
Managing time and budget effectively is essential for the successful prototyping of medical devices. By engaging in low-volume production, financial risks are minimized, facilitating a swift entry to the market without being constrained by minimum order requirements. Concentrating on efficient management of projects and focusing on critical milestones helps developers keep their projects aligned with timelines and financial plans.
To mitigate financial risks and guarantee timely completion of projects, it’s advantageous to utilize on-demand production coupled with rapid prototyping techniques. These methods enable developers to swiftly produce functional prototypes that meet rigorous standards efficiently while ensuring that the end device functions as envisioned for its medical applications.
Summary
In conclusion, medical device prototyping is a critical process that drives innovation and improves patient outcomes in the healthcare industry. By understanding the key stages of the prototyping process, leveraging advanced techniques, and ensuring safety and compliance, developers can create innovative medical devices that meet all necessary standards and perform as intended. The importance of collaboration, effective management of modifications, and time and budget management cannot be overstated in ensuring the success of medical device prototyping projects.
By following the guidelines and best practices outlined in this blog post, developers can navigate the complexities of medical device prototyping and bring their innovative ideas to life. The journey from concept to market is a challenging one, but with the right approach and tools, it is possible to create life-saving medical devices that improve patient care and reduce healthcare costs.
Frequently Asked Questions
What is the purpose of medical device prototyping?
The purpose of medical device prototyping is to develop initial concepts into functional and safe products by undergoing iterative testing and refinement.
This process ensures that the final device meets necessary standards and effectively serves its intended purpose.
How does rapid prototyping benefit medical device development?
Rapid prototyping significantly accelerates the medical device development process by enabling quick iterations and modifications based on user feedback, which leads to faster market entry.
This approach enhances innovation and responsiveness to user needs.
What are the key stages in the medical device prototyping process?
The key stages in the medical device prototyping process are conceptualization, material selection, prototype fabrication, testing, and iteration. Each stage is crucial for enhancing the device’s design and functionality.
How does usability testing improve medical device prototypes?
Incorporating user feedback into the design and usability refinement of medical device prototypes, usability testing considerably improves these devices by making certain they are both intuitive to operate and safe for use.
This method leads to the development of devices that are not only more efficient but also easier for users to handle.
Why is regulatory compliance important in medical device prototyping?
Regulatory compliance is crucial in medical device prototyping as it guarantees that devices adhere to safety and efficacy standards, leading to market approval and ensuring patient safety.
Meeting these regulations ultimately protects both the manufacturer and the end users.