Before electronic devices enter mass production, innovators develop prototypes as initial models to examine and improve their concepts. This crucial stage allows for the testing and perfecting of design details. It helps to confirm functionality, reduce potential risks, and certify that product standards are met. By having the devices prototyped, it becomes possible to determine cost-efficiency and identify potential defects early. Consequently, this helps prevent higher expenses during manufacturing. We will delve into the fundamental phases of electronic prototyping in this article and provide valuable advice for efficiently advancing your projects.
Key Takeaways
Electronic prototyping validates design and functionality, minimizing risks before mass production.
Key stages include concept development, circuit design, schematic design, PCB layout, component selection, and testing.
Partnering with experienced prototyping companies can enhance project efficiency and ensure quality standards.
Understanding Electronic Prototyping
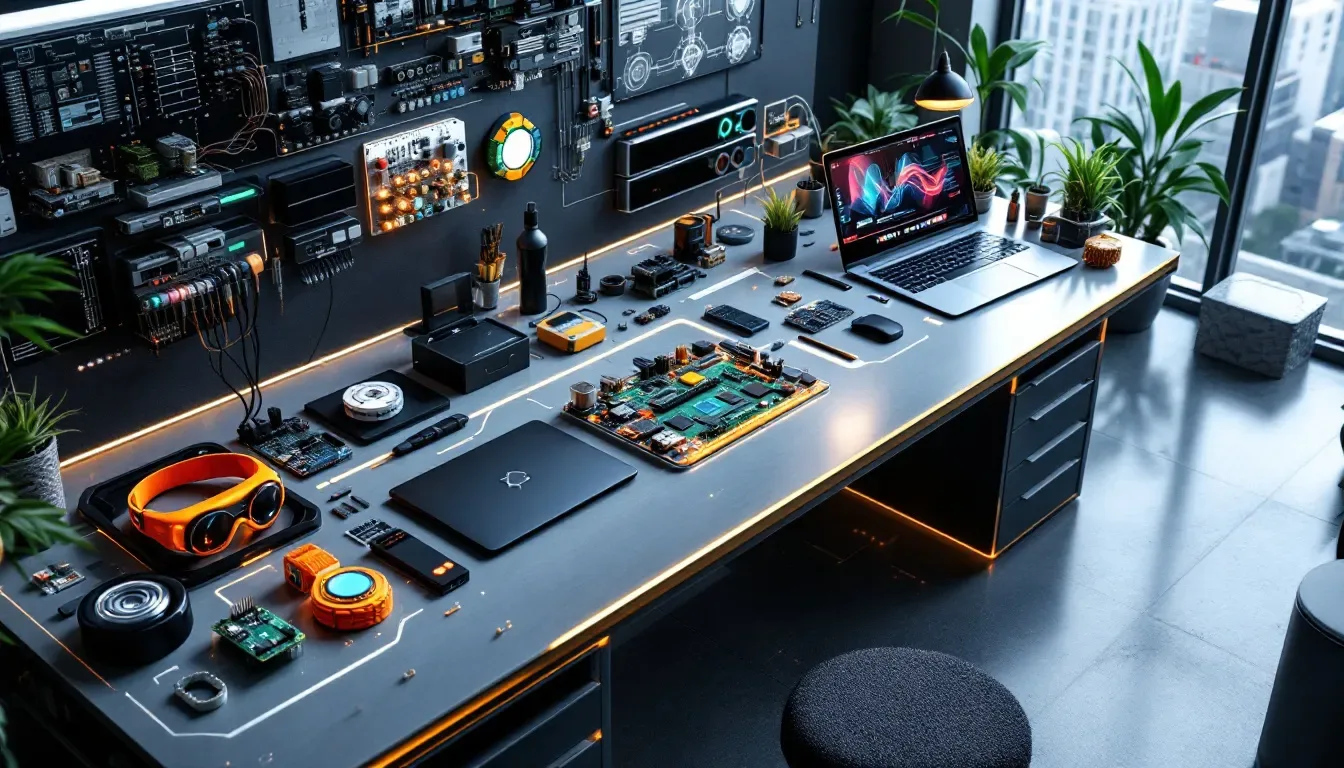
The practice of electronic prototyping involves crafting initial models of electronic devices, enabling creators to examine and polish their concepts before embarking on large-scale manufacturing. This stage is vital as it confirms both the function and design of an electronic device are up to standard and operate correctly. The development starts with idea formation and evolves through various phases such as designing the electronics, outlining schematics, and choosing components.
At its core, the art of prototyping in electronics revolves around affirming circuit operation, trialing solutions, and assessing comprehensive functionality. By utilizing functional prototypes early on, developers can identify potential problems that could lead to costly errors once production scales up. Instruments like prototype boards for electronics along with breadboards are integral in this phase for assembling and appraising circuits.
There is a broad market focused on producing these prototypes within the field of electronics. This includes numerous businesses offering related services dedicated to creating effective prototypes. This demand is fueled by consumers’ appetite for cutting-edge electronic devices paired with trustworthy testing methods. Each aspect from conception through every subsequent step involved in generating a successful electronic prototype holds significant importance within this process. Thorough evaluations at each stage help reduce risk through systematic reviews of specifications. Also, validating components ensures reliable prototypes that mitigate potential issues in software and hardware development.
Key Stages in the Electronic Prototyping Process
The prototyping process for electronics encompasses several key stages, which are essential for iterative refinement and testing of concepts. By concentrating on primary functionalities during the design phase, both efficiency is improved, and unwarranted costs can be minimized.
Every stage in this process plays a distinct role in enhancing the overall approach to creating prototypes. Each contributes to the cyclical nature of refining and rigorously examining ideas.
Concept Development
Before:
The first step in the prototyping process is defining the project requirements and objectives. This lays the foundation for successful development. Understanding the specific functional, electrical, mechanical, and environmental requirements is crucial before selecting components. This stage involves creating a conceptual design that aligns the team’s vision. It provides a clear depiction of the system’s functions through functional block diagrams.
After:
Define the project requirements and objectives to lay the foundation for successful development.
Understand the specific functional, electrical, mechanical, and environmental requirements before selecting components.
Create a conceptual design that aligns the team’s vision. It provides a clear depiction of the system’s functions through functional block diagrams.
Concept development requires aligning all team members with the project’s goals and objectives. This alignment helps in selecting the right design tools and planning the subsequent stages of the development process. A solid foundation at this stage helps teams work closely, streamlining the prototyping process. This helps in reducing the risk of errors and miscommunications.
Schematic Design
The schematic design stage plays a crucial role in transforming the initial concept into intricate circuit schematics. This is achieved through the use of electronic design software. Programs such as Altium are essential during this process, enabling designers to craft precise and effective circuit layouts. This layout phase encompasses selecting components and planning their interconnections within the circuit to align with the project’s operational criteria.
Identifying possible complications early on and making requisite modifications is fundamental at this juncture before proceeding to assemble a tangible prototype. Employing state-of-the-art tools alongside best practices for designing circuits leads to crafting a durable and trustworthy functional prototype that acts as an archetype for the eventual product.
PCB Design and Layout
During the design and layout stage of a PCB, electronic components are strategically affixed to the circuit board. It is critical to take into account factors like the size of the board, fitting all components properly, maintaining high electrical performance, and ensuring adequate heat dissipation for an efficient printed circuit board design. Employing methods such as Through-hole Technology and Surface Mount Technology along with tools like Pick-and-Place machines helps achieve accuracy and dependability in this process.
Creating a carefully engineered PCB layout not only boosts the dependability of an electronic prototype but also significantly influences its ultimate success. By prioritizing these design aspects during development, it’s possible to guarantee that the prototype aligns with project requirements and exhibits superior performance across diverse scenarios.
Selecting the Right Components
Choosing appropriate electronic components is a crucial phase in the process of prototyping. This step requires careful assessment of critical specifications such as current and voltage requirements, operational temperature range, capacitance levels, inductance values, and resistance characteristics. This guarantees the best possible performance. Opting for parts from trusted manufacturers can enhance quality and dependability, thereby lessening the likelihood of malfunctions.
It’s also essential to assess the reliability of suppliers. Taking into account their customer support services and policies regarding product discontinuation ensures ongoing component availability and assistance over time. Employing parametric selection tools facilitates a more effective narrowing down within an extensive array of options available on the market. This helps streamline the prototyping procedure while mitigating risks.
Staying abreast with evolving industry trends and technological advancements plays a significant role in making well-informed decisions when it comes to component selection. By choosing wisely, you not only mitigate potential hazards, but also boost both overall functionality and steadfastness throughout your electronic prototype development journey.
Assembling the Prototype
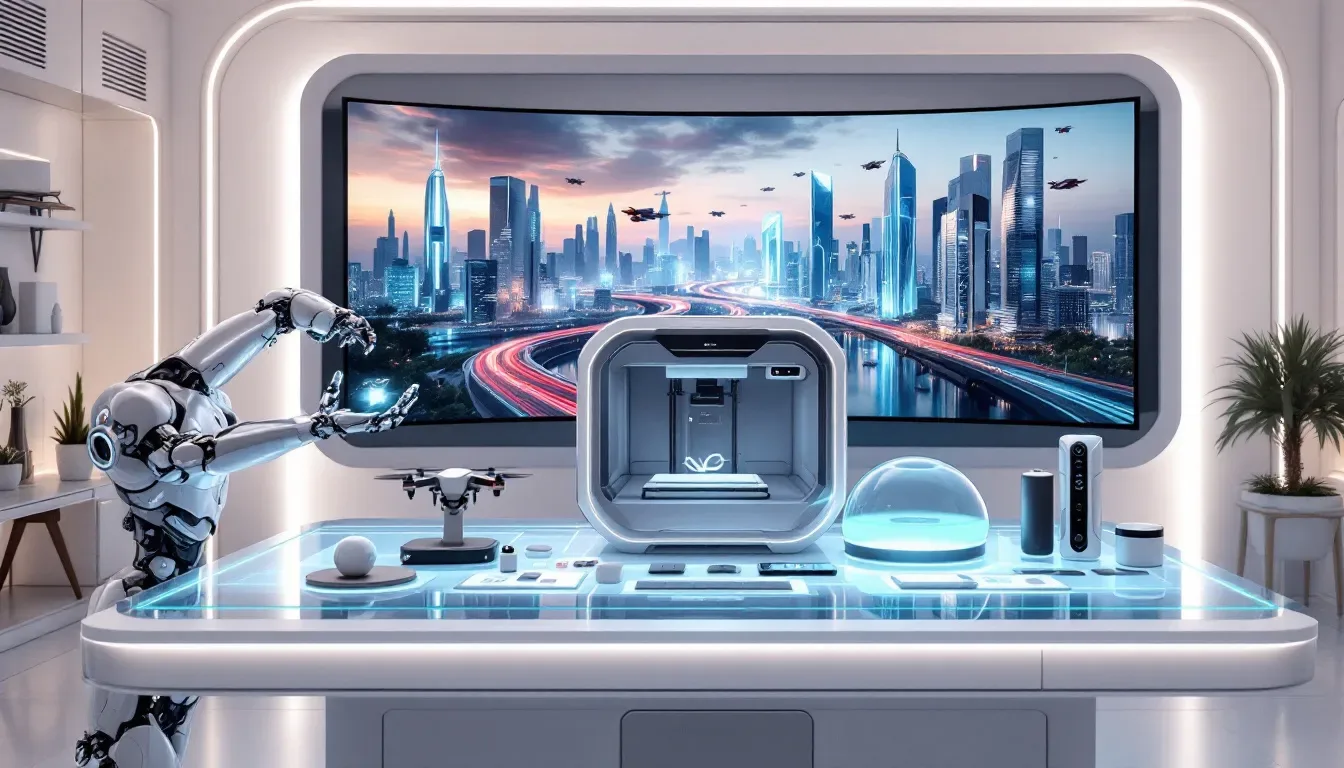
The prototyping process requires the careful placement of selected components onto the circuit board through different methods. For limited production runs, manual assembly is advantageous due to its precision in component placement. Conversely, automated assembly lines significantly speed up the process and are increasingly adopted within the industry.
Employing a combination of manual and automatic assembly enhances both efficiency and precision during prototyping. By utilizing this integrated approach, it guarantees that the prototype is constructed properly and operates as expected. This sets a solid foundation for subsequent mass production.
Testing and Validation
Testing and validation identify potential problems and ensure the prototype meets durability and regulatory standards before mass production. Successful testing indicates the prototype is sound and ready for further development.
Testing components in actual circuits is essential to identify compatibility and performance issues, alongside testing for environmental conditions like temperature and humidity. Durability testing simulates long-term usage to predict how the prototype will hold up over time, while performance testing evaluates functionality under stress.
Laboratory tests, near real-world testing, and simulations should be included in the testing phase to ensure thorough evaluation. Once testing is complete, analyzing the results and correcting errors is crucial to refine the prototype. This ensures it meets all required standards. After the prototype is tested, results should be meticulously analyzed. This helps identify errors, which then need to be corrected and retested to ensure the system operates reliably.
Importance of Design Verification
The process of design verification plays a crucial role in affirming the dependability of electronic devices by pinpointing possible issues at an early stage. It facilitates the discovery and resolution of design defects swiftly, preventing these concerns from becoming more significant and expensive during subsequent stages of production.
By integrating verification into the initial design phase, potential obstacles that could disrupt manufacturing workflows are addressed proactively. This attention to detail guarantees that products comply with quality benchmarks and regulatory requirements, mitigating the risk of expensive product recalls and enhancing confidence among stakeholders.
Rapid Prototyping Techniques
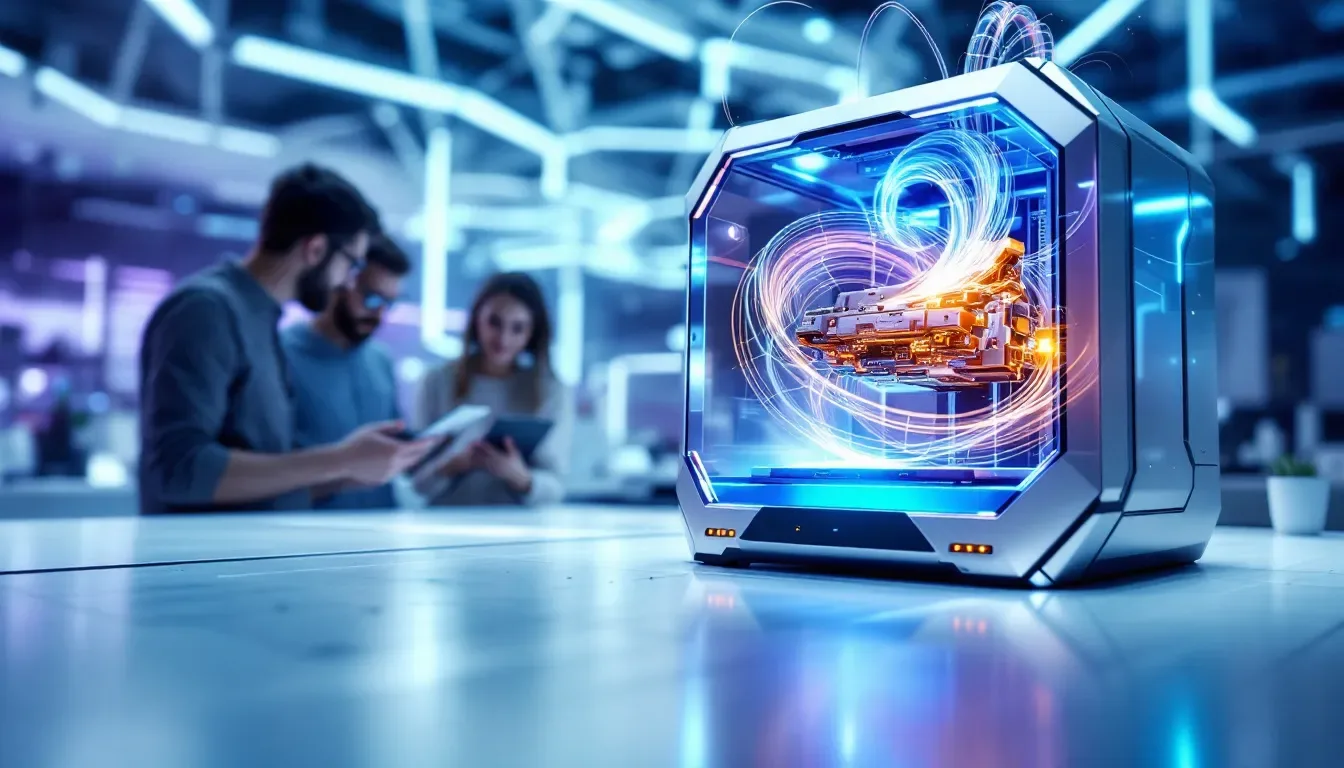
Methods such as 3D printing and CNC machining play an essential role in the creation of electronic prototypes. The use of 3D printing enables rapid iteration, expediting the completion of projects while minimizing material waste by utilizing only what is required. It is a cost-efficient approach because it eliminates the need for costly molds or manufacturing tools.
With its capability to fabricate intricate shapes that are challenging to achieve using conventional techniques, 3D printing facilitates easy customization of prototypes. Conversely, CNC machining brings forth superior precision and stringent tolerances which are ideal for generating prototypes with high-quality surface finishes.
Choosing appropriate prototyping strategies can lead to significant time and financial savings. The benefits differ according to project complexity. These methodologies guarantee the generation of functional prototypes. They are tailored to adhere to specific project requirements and are designed for optimal performance.
Cost-Efficiency in Prototyping
Prototyping may require upfront investment, but it is a cost-effective measure as it helps avoid expensive mistakes in the mass production phase. Introducing a product to the market without prototyping can result in increased expenses due to defects that emerge during large-scale manufacturing.
Leveraging online tools and open-source materials can considerably reduce costs associated with the prototyping stage of development. Keeping meticulous records of decisions related to component selection aids in simplifying future project management and problem-solving efforts, which enhances overall cost savings.
Real-World Applications of Electronic Prototypes
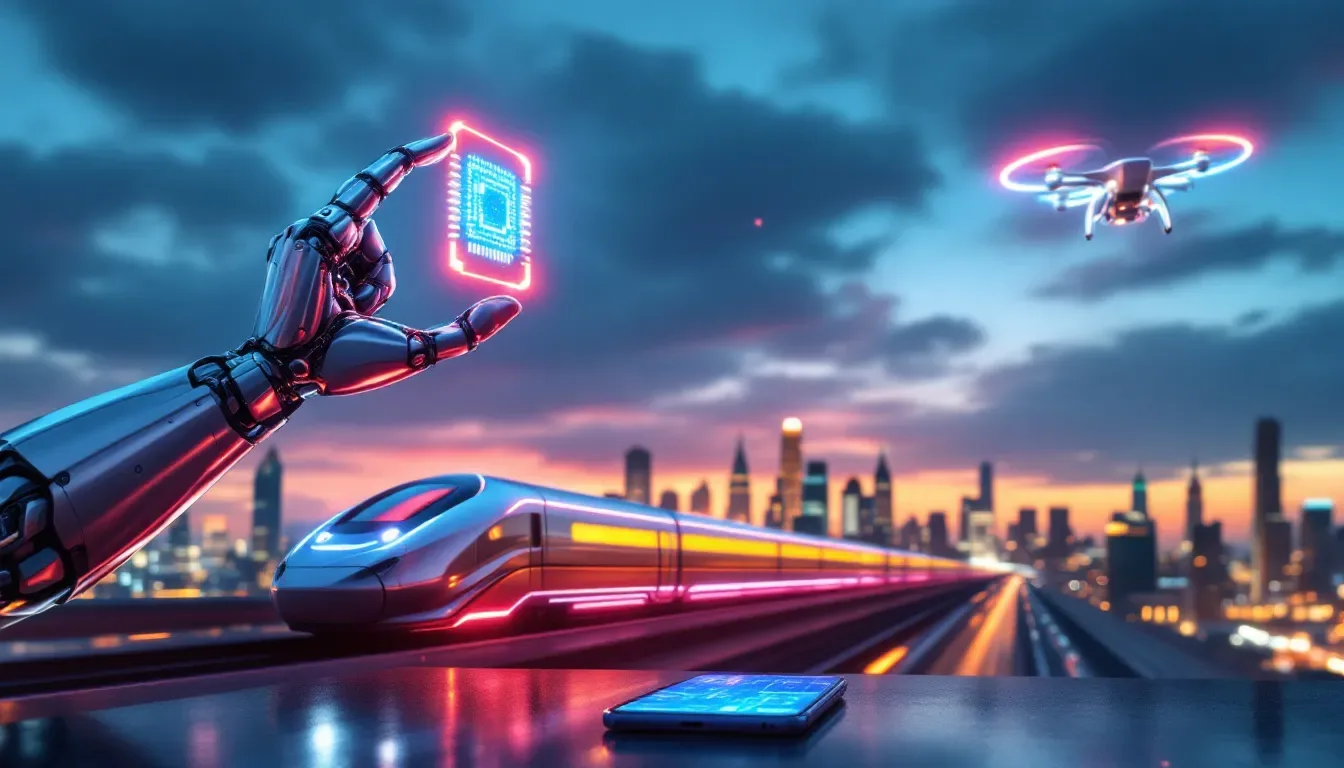
During the development process, prototypes play a crucial role in understanding market demands and user preferences. They serve to evaluate interest levels within the market and collect feedback from users that is then used to perfect the features of the product. For electronic devices, several prototyping techniques exist, such as 3D printing, developing prototype circuit boards, and crafting functional prototypes—each offering distinct benefits.
The selected method for creating a prototype is determined by its intended purpose along with how complex the project is. Utilizing these various methods enables developers to forge prototypes that closely resemble what will become their final product. This approach greatly facilitates an improved comprehension of both market requirements and user anticipations.
Partnering with an Electronic Prototyping Company
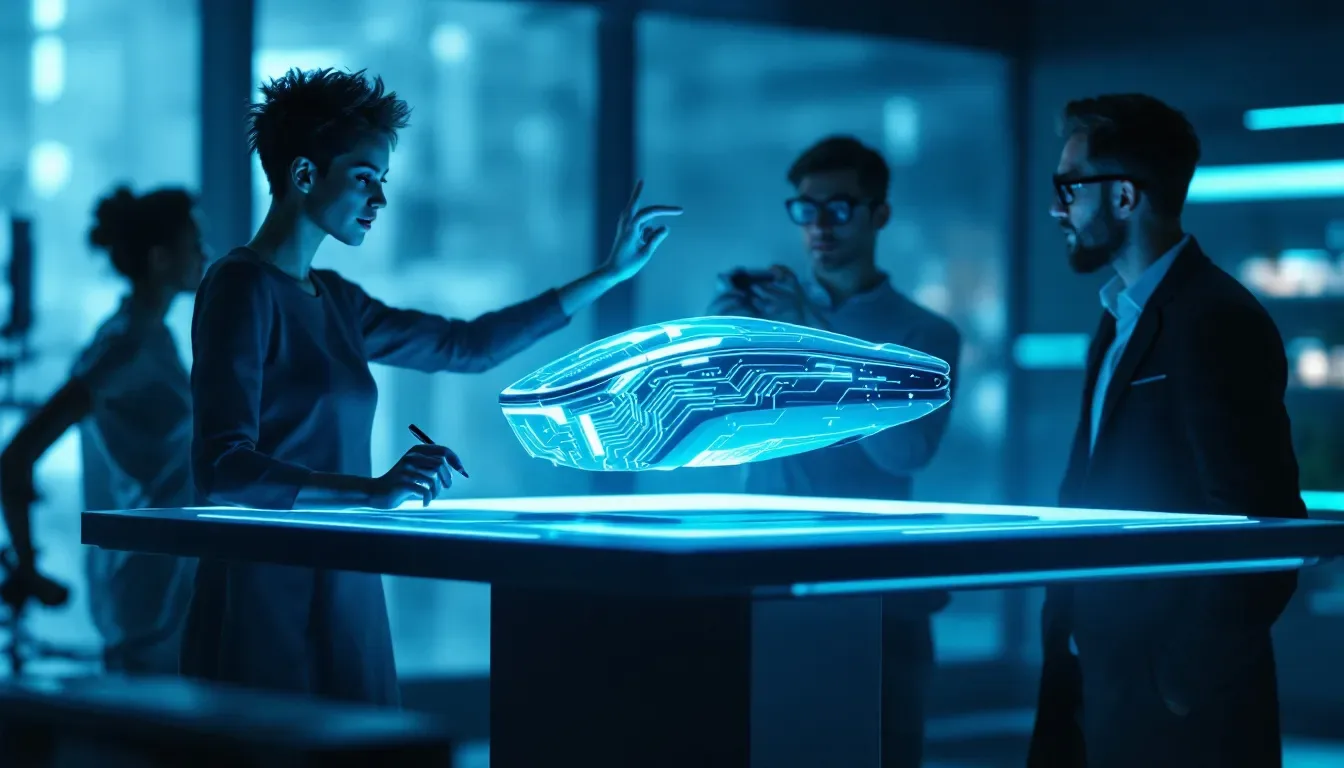
Working with a trustworthy electronic prototyping company can greatly improve the efficiency and likelihood of success for your project. Firms such as LKprototype have accumulated 15 years of specialized experience in prototyping, having produced more than 8 million prototypes and parts, bringing considerable knowledge and capabilities to the table.
Selecting a dependable company for electronic prototyping guarantees that your project will align with industry benchmarks while being carried out effectively. Such companies dedicate their efforts to crafting electronic prototypes suitable for diverse purposes, delivering superior quality prototypes tailored to match the specific requirements of your project.
Summary
Grasping the intricacies of electronic prototyping is about comprehending its crucial phases. This includes opting for suitable components and applying proper testing and validation techniques. Adhering to these vital recommendations will allow you to develop functional prototypes. These prototypes will adhere to industry norms and surpass user anticipations.
Embarking on the path from initial concept to finished creation brings a mix of hurdles and thrills. Equipped with appropriate expertise and instruments, this journey can be undertaken triumphantly. Delve into the craft of electronic prototyping and bring your concepts into reality as cutting-edge, reliable electronic devices.
Frequently Asked Questions
What is electronic prototyping?
Electronic prototyping is the creation of preliminary versions of electronic devices to evaluate and improve concepts prior to mass production. This approach enables innovation while minimizing costs and risks.
Why is design verification important in electronic prototyping?
In electronic prototyping, design verification plays a vital role. It detects early possible problems, which guarantees dependability. This minimizes time and expenses during subsequent production stages.
What are the benefits of rapid prototyping techniques like 3D printing?
Techniques for rapid prototyping, including 3D printing, significantly increase efficiency by allowing for speedy iterations. They also reduce expenses and support the generation of intricate and tailored designs.
Consequently, these benefits contribute to faster completion of projects and enhanced results in product development.
How can prototyping save costs in the long run?
By identifying and resolving issues early on through prototyping, businesses can prevent expensive mistakes from occurring during mass production, ultimately saving costs in the long run.
Utilizing online platforms and tapping into open-source materials can also help to keep costs low throughout this stage of the process.
What should you consider when selecting electronic components for a prototype?
When choosing electronic components for a prototype, it is essential to consider the ratings for current and voltage, as well as operating temperature ranges. Pay close attention to specifications such as capacitance and resistance.
Selecting components from well-known manufacturers is advisable in order to ensure their quality and dependability.
Still, need help? Contact Us: lk@lkprototype.com
Need a PROTOTYPE or PARTS machining quote? Quote now