Wondering whether brass vs stainless steel fittings are best for your project? This article breaks down durability, corrosion resistance, cost, and application suitability to help you decide.
Key Takeaways
Brass fittings are cost-effective and provide decent corrosion resistance, but they can suffer from dezincification in aggressive environments.
Stainless steel fittings offer superior corrosion resistance and durability, making them suitable for high-pressure and extreme temperature applications, despite their higher initial cost.
The choice between brass and stainless steel fittings should be based on factors such as budget, application environment, temperature tolerance, and pressure requirements.
Understanding Brass Fittings
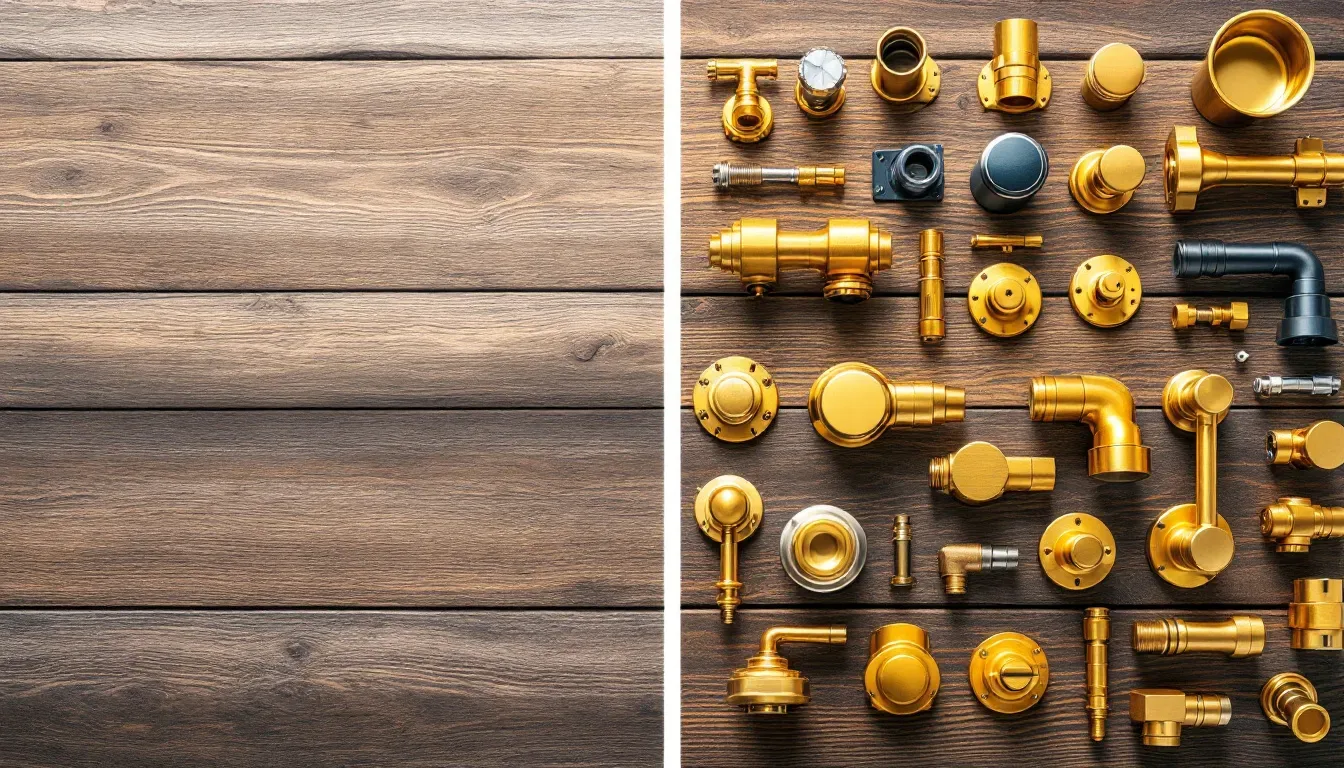
Many homeowners favor brass fittings for their residential plumbing needs because of the impressive balance between strength and user-friendliness they provide. This metal alloy, predominantly made up of copper and zinc, is especially suited to various applications owing to its robustness yet pliability. In the realm of plumbing fixtures, brass stands out for offering decent corrosion resistance while also maintaining long-term durability.
There are some limitations associated with brass. Despite its excellent ease of machining, it’s vulnerable to dezincification—a condition in which zinc is extracted from the alloy—resulting in structural weakness that could lead over time to malfunctions or breakdowns. In environments that aggressively induce such deterioration, using brass might not be advisable due to heightened risk factors.
Notwithstanding these considerations about potential complications with usage under certain conditions, many continue opting for brass fittings because they strike a balance between cost-effectiveness and straightforward installation processes. With capabilities like forming secure seals within plumbing systems as well as adding visual charm through polished finishes on both fixtures and valves made of this material—brass maintains a reputable standing among practical choices available for numerous standard uses.
Characteristics of Stainless Steel Fittings
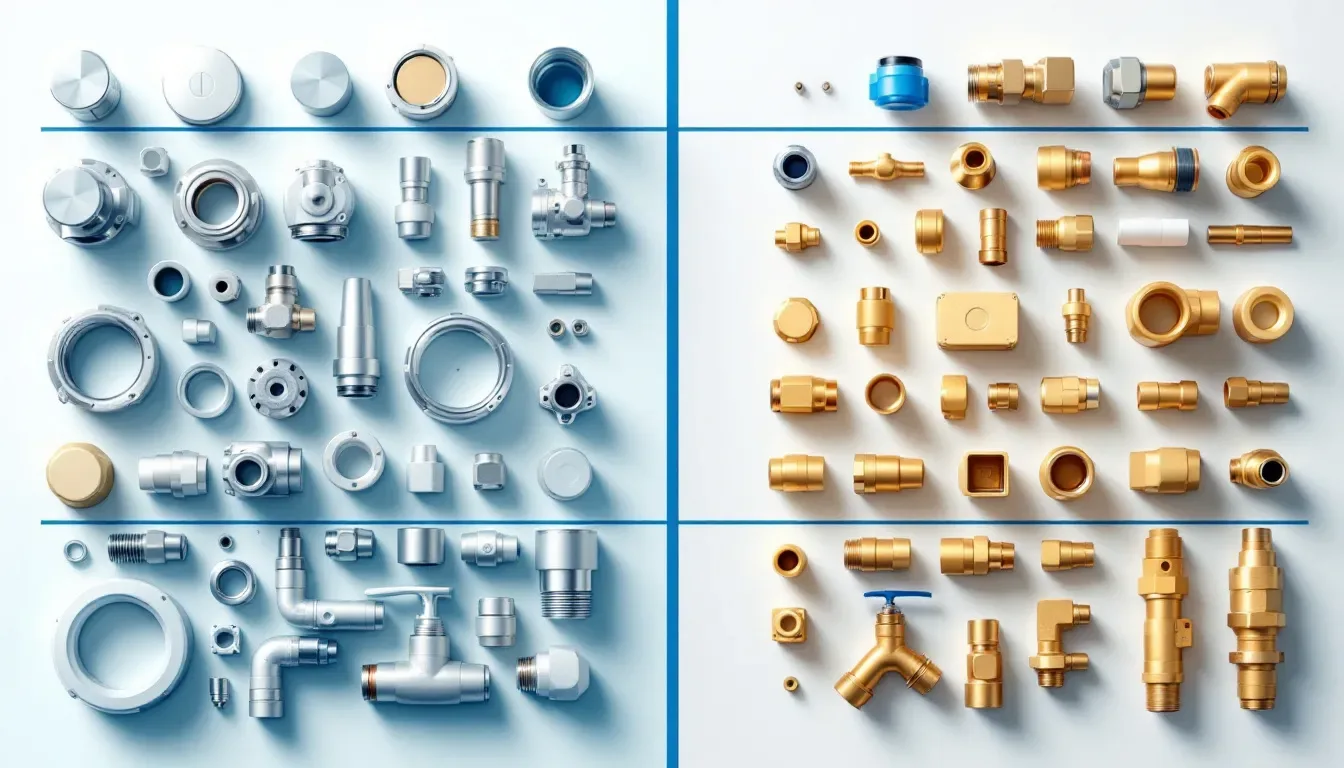
Conversely, stainless steel fittings are celebrated for their exceptional durability and superior corrosion resistance. This impressive resilience originates from the alloy’s unique composition. With at least 10.5% chromium present, it forms a passive oxide layer on its surface that shields the underlying metal against rust and deterioration. Consequently, such fittings prove especially useful in demanding conditions like those involving saltwater or acidic substances.
Not only do stainless steel fittings excel in resisting corrosion, but they also boast notable longevity, requiring little to no maintenance over time. The reduced necessity for constant repairs or replacements offers cost-saving advantages over extended periods of use. For this reason, sectors such as aerospace, maritime operations, and manufacturing heavily rely on these durable fixtures to maintain functionality even within extreme settings.
Despite being pricier upfront compared to other materials and having a vulnerability to pitting corrosion under specific circumstances, they are pricier upfront.
The prolonged lifespan paired with unparalleled protection against decay ensures that investing more initially in stainless steel can be economically favorable due to fewer costs incurred down the line because of its inherent sturdiness and protective qualities.
Comparing Corrosion Resistance
Regarding the resistance to corrosion, brass and stainless steel fittings display notable variances. Although brass fittings provide reasonable protection against corrosion, they are susceptible to tarnishing or developing a patina as time progresses, which may not be appropriate for all uses. More importantly, when exposed to harsh environments with elevated levels of chloride, brass is at risk of dezincification — a process that can weaken the material and impair its structural soundness.
Conversely, in settings where combating corrosion is crucial, stainless steel fittings demonstrate superior performance. The chrome within stainless steel creates an oxide layer on the fitting’s surface that shields it from rusting and other corrosive effects. This protective feature renders stainless steel fittings more suitable for highly aggressive conditions such as marine applications where saltwater exposure occurs routinely. Their capacity to thwart pitting and crevice corrosion serves to amplify their durability under these circumstances.
While in less challenging environments brass fixtures might prove adequate. Due their tendency towards dezincification and susceptibility to tarnish diminishes their effectiveness in harsher corrosive situations. Stainless steel stands out by providing unmatched resistance against deterioration making it an optimal choice for scenarios demanding extended lifespan and robustness of materials used.
Performance Under Pressure
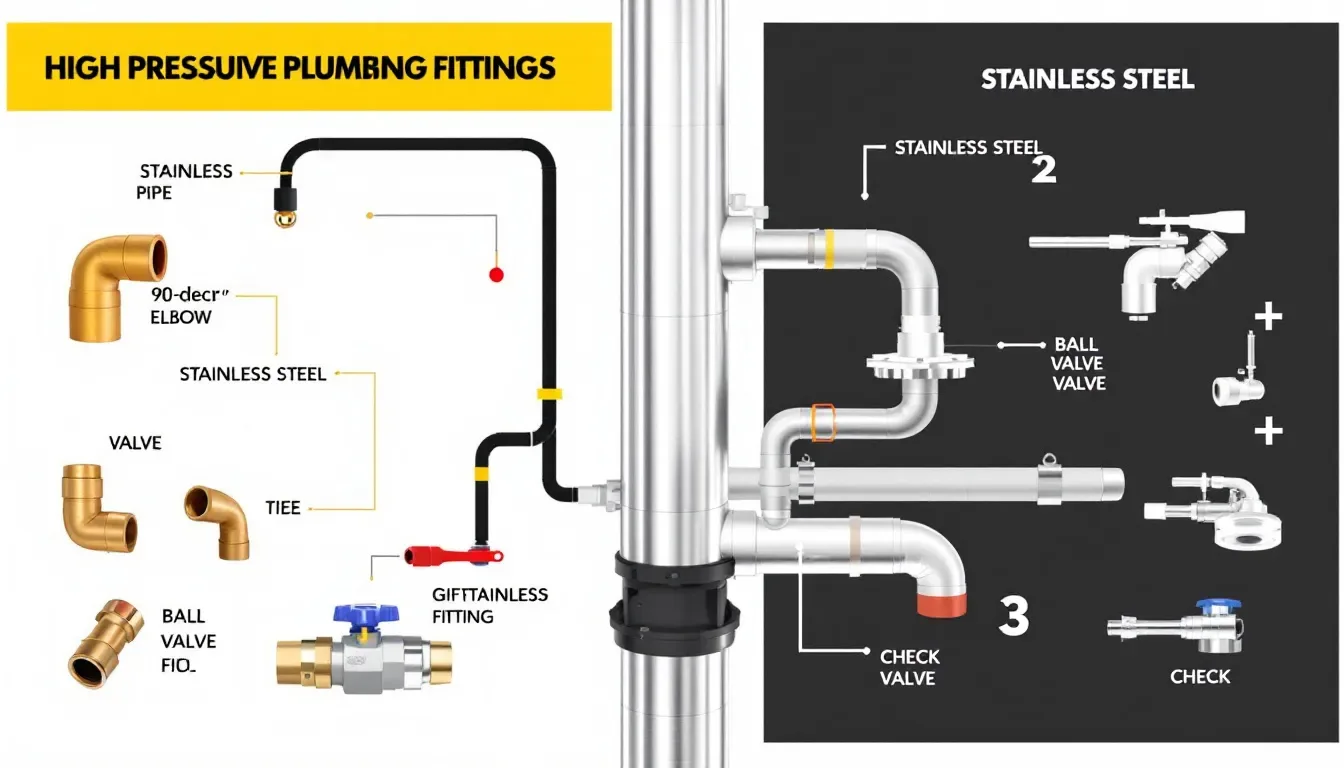
When assessing the suitability of fittings for pressurized environments, one must take into account their performance capabilities. Brass fittings are often favored in situations that call for low to moderate pressure because they provide an acceptable level of strength along with ease of manufacturing. These brass components are typically found in domestic and minor industrial contexts where the pressures involved do not reach extreme levels.
Conversely, stainless steel fittings emerge as the preferred option when dealing with high-pressure applications. Owing to their impressive tensile strength and robustness, these stainless steel variants can endure the rigorous conditions imposed by high-pressure systems without sacrificing security or operational efficiency. Their reliability is particularly valued in settings such as hydraulic systems among other scenarios involving intense pressures.
To choose materials aptly suited for your system’s needs is crucial. This requires a clear understanding of its specific demands. While brass might be adequate for less strenuous pressure requirements, it is under circumstances requiring heightened resistance and endurance where stainless steel truly becomes indispensable due to its unparalleled durability and resilience under substantial pressure loads.
Cost Considerations
Choosing between brass and stainless steel fittings often comes down to cost considerations. Typically, the initial outlay for projects involving brass fittings is lower than that of those requiring stainless steel, making them appealing for situations where immediate costs are a pivotal concern.
Nevertheless, over time, stainless steel can become more economically viable due to its exceptional robustness and minimal upkeep demands. The long-term endurance of stainless steel equates to less frequent need for replacement or repair work—especially in settings where high pressure or corrosive elements are at play—potentially leading to significant financial savings.
The higher residual value of brass adds another dimension to its economic appeal in the long term. Consequently, while upfront expenses may be lower with brass fittings, investing in the superior durability and maintenance advantages offered by stainless steel fittings could prove beneficial on numerous projects.
Temperature Tolerance
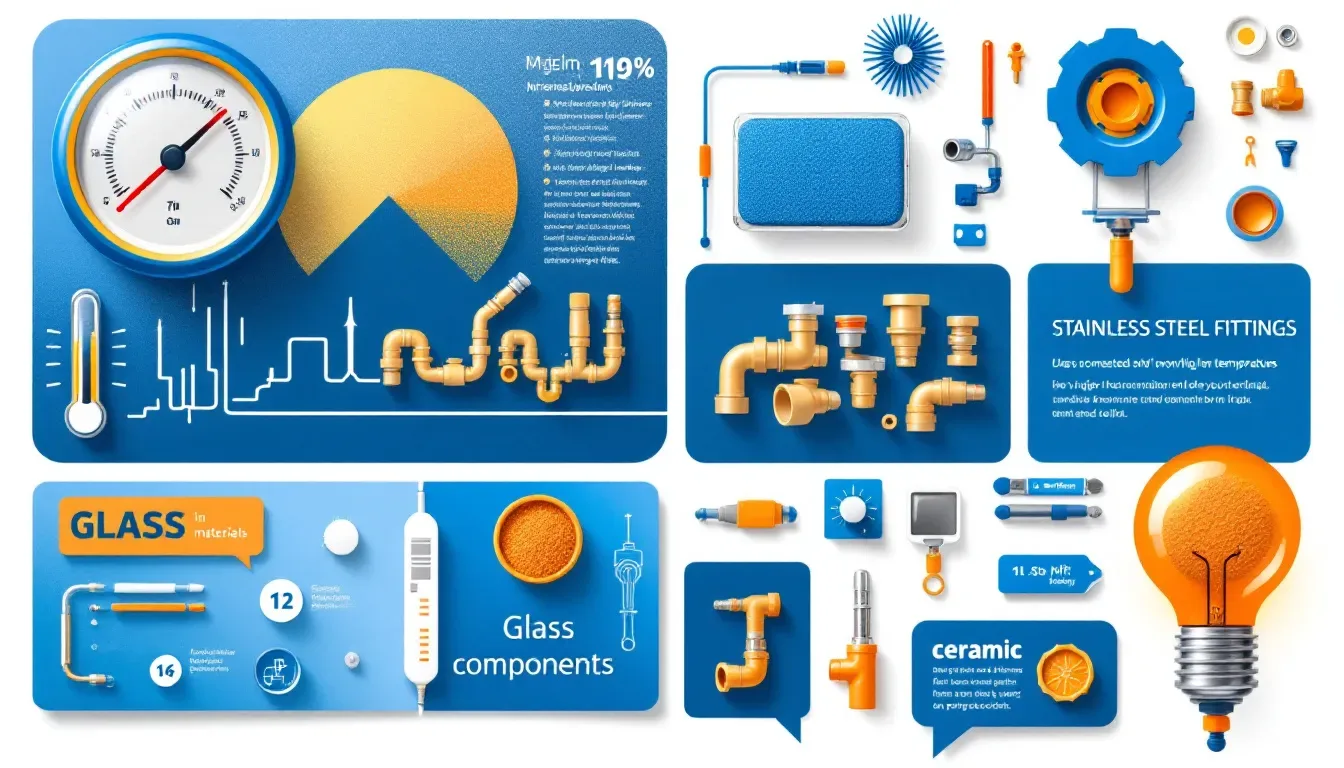
When evaluating fittings based on temperature endurance, it’s important to take into account their heat tolerance. Brass fittings are capable of withstanding elevated temperatures and are appropriate for use in hot water systems or settings where they will be exposed to moderate warmth. The efficacy of brass diminishes when faced with exceedingly high heat, which restricts its suitability for applications requiring resistance to intense temperatures.
On the other hand, stainless steel fittings preserve their mechanical integrity even at extreme temperatures. They can endure much higher levels of heat than brass—up to a remarkable 1200°F compared to brass’s upper limit of just 400°F. This exceptional capability renders stainless steel an optimal choice for scenarios that demand significant temperature resilience.
In essence, although brass fittings may perform well within a limited range of temperatures, stainless steel provides superior durability needed for challenging high-temperature environments. Its ability to resist such conditions ensures lasting functionality and consistent performance across diverse thermal landscapes.
Real-World Applications
The selection of brass or stainless steel fittings largely depends on their intended use. Stainless steel fittings are typically the go-to option for marine settings due to their exceptional ability to combat pitting and crevice corrosion caused by exposure to saltwater. Likewise, for hydraulic systems that face both high pressure and corrosive elements, stainless steel is often favored.
Conversely, brass fittings find common use in household water systems where conditions concerning pressure and environmental factors are relatively less intense. Given their conducive properties related to heat and electricity conduction, these types of fittings serve well in various applications such as gas transport systems, chemical processing units, and automotive manufacturing.
The broad adaptability inherent in both brass and stainless steel fittings ensures they remain integral components within numerous sectors. Each type thrives under certain conditions owing to its unique characteristics coupled with the specific demands posed by different environments.
Choosing the Right Fitting for Your Project
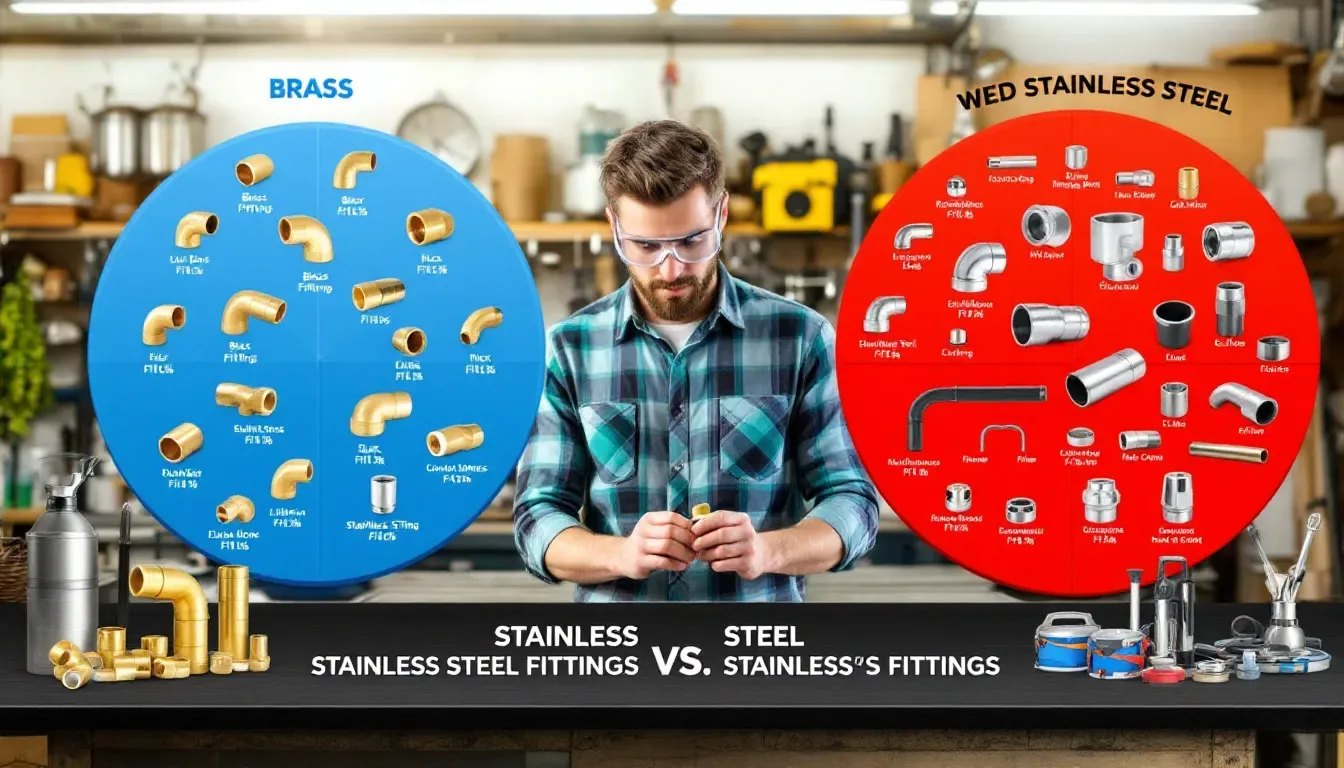
When choosing the appropriate fitting for your endeavor, it is important to evaluate a multitude of factors such as budgetary constraints, compatibility with the material in use, and the pressure ratings necessary. Brass fittings are more user-friendly when it comes to handling and installing because they are composed of a softer substance. This characteristic makes them preferable for applications that necessitate regular modifications or updates.
In contrast, stainless steel fittings present a higher degree of difficulty in terms of manipulation. Their malleability allows for precise custom fabrication. These characteristics render them apt for projects where exacting standards must be met. Seeking expert advice can prove extremely beneficial when making this decision to ensure that the chosen fittings align perfectly with your project’s unique requirements.
Carefully weighing these elements will assist you in determining which type of fitting best fulfills what your specific project requires.
Surface Treatments for Enhanced Performance
Applying surface treatments to brass and stainless steel fittings can substantially improve their functionality. Treatments such as sandblasting, anodizing, electroplating, and polishing each provide distinct advantages. Anodizing in particular enhances corrosion resistance and wear properties while also improving the visual appeal of these fittings.
For brass fittings specifically, electroplating is advantageous as it utilizes electrical current to deposit a metal coat that augments both surface durability and electrical conductivity. Sandblasting is another preparatory treatment that evens out texture on surfaces and eradicates contaminants, which is essential for proper coating adhesion.
By polishing the fittings, one achieves not just an aesthetically pleasing mirror finish, but also minimizes surface irregularities. This contributes significantly to enhancing both endurance and operational effectiveness of the metal components. The implementation of these treatments can prolong the service life of your fixtures by ensuring dependable performance within their designated roles.
Summary
To sum up, fittings made of both brass and stainless steel present distinct benefits and considerations that render them appropriate for varying uses. Fittings crafted from brass are cost-effective and simple to install, which makes them well-suited for environments with moderate pressure and temperature. In contrast, those constructed from stainless steel stand out due to their excellent corrosion resistance and robustness. They are favored in situations involving elevated pressures, extreme temperatures, or substantial corrosive conditions. By recognizing the contrasts between these materials along with the particular requirements of your undertaking, you can make an informed decision that guarantees sustained reliability and efficacy.
Frequently Asked Questions
What makes stainless steel fittings more suitable for high-pressure applications?
Stainless steel fittings are more suitable for high-pressure applications due to their high tensile strength and durability, allowing them to withstand demanding conditions effectively.
Are brass fittings more cost-effective than stainless steel?
Brass fittings may be cheaper upfront, but stainless steel can be more cost-effective in the long run due to its durability and reduced maintenance needs.
Can brass fittings tolerate high temperatures?
Brass fittings can tolerate moderate high temperatures up to 400°F; however, they are unsuitable for extreme heat applications exceeding this limit.
What are some common surface treatments for fittings?
Surface treatments like sandblasting, anodizing, electroplating, and polishing are frequently applied to fittings to improve their resistance to corrosion, increase their longevity, and upgrade their aesthetic appeal.
In what environments are stainless steel fittings preferred?
Stainless steel fittings are ideal for environments prone to corrosion, including marine and industrial settings, because of their excellent rust and corrosion resistance.
Still, need help? Contact Us: lk@lkprototype.com
Need a PROTOTYPE or PARTS machining quote? Quote now