When deciding between brass vs bronze for a project, understanding their key differences is essential. Despite both being copper-based alloys, brass and bronze have distinct compositions and properties that make them suitable for different applications. This article will break down the composition, physical properties, mechanical properties, corrosion resistance, and common uses of brass vs bronze to help you make an informed choice.
Key Takeaways
Brass and bronze are distinct copper-based alloys, with brass being primarily composed of copper and zinc, while bronze consists mainly of copper and tin, leading to differing physical and mechanical properties.
Brass is more malleable and is often used in decorative and plumbing applications, while bronze, known for its strength and corrosion resistance, is preferred for marine and industrial uses.
Identifying brass and bronze can be accomplished through visual inspection, weight comparison, and sound tests, each leveraging their unique physical characteristics.
Understanding Brass and Bronze
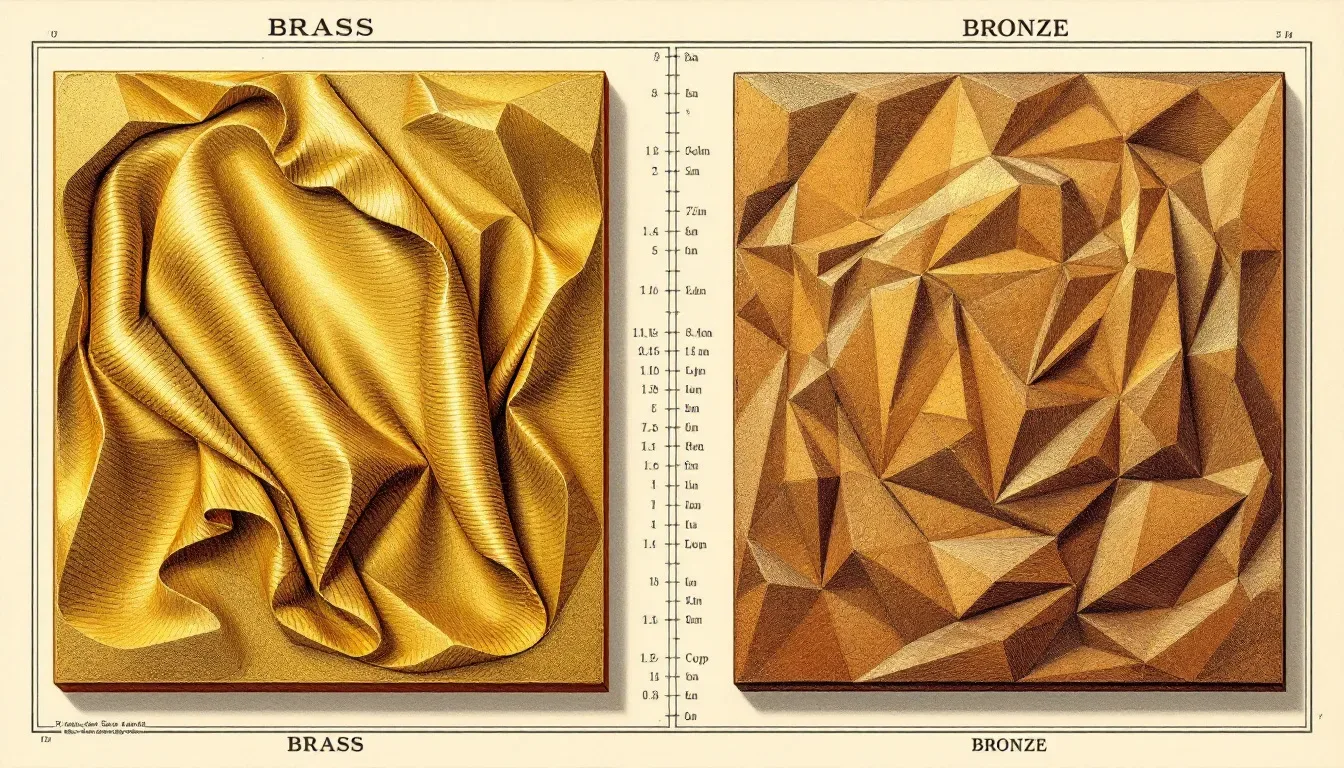
Both brass and bronze are alloys grounded in copper, possessing unique physical attributes that have lent themselves to diverse industrial applications for millennia. Despite superficial resemblances, the particular makeup and resulting qualities of these metals differentiate them, ensuring each is appropriate for specialized uses. The broader category of pure copper alloy includes both of these materials.
At their core, brass and bronze differ due to what they’re made from: brass is an alloy formed from copper and zinc primarily. On the other hand, bronze consists mainly of copper combined with tin. These compositional distinctions give rise to different physical properties as well as mechanical strengths and levels of resistance to corrosion amongst the two metals.
Brass Composition
Brass mainly consists of copper and zinc. The proportion of zinc in brass plays a crucial role, with increased amounts typically boosting the alloy’s strength and pliability, thus rendering it more malleable for easier manipulation.
Additional elements such as iron, aluminum, silicon, and manganese might also be incorporated into brass to modify its attributes. This adaptability allows brass to be used effectively across various applications including the creation of musical instruments and ornamental pieces.
Bronze Composition
Composed chiefly of copper and tin, bronze exhibits inherent strength and corrosion resistance due to this metallic blend. It is distinct from brass which incorporates zinc, bestowing upon bronze unique mechanical qualities for various uses.
Incorporating elements such as aluminum or phosphorus into the composition of bronze can enhance its attributes. Aluminum serves to amplify both its robustness and ability to withstand corrosive conditions, rendering it apt for use in marine settings and heavy industry sectors. Consequently, these enhanced characteristics render bronze a favored material when endurance and resilience against extreme conditions are paramount.
Physical Properties
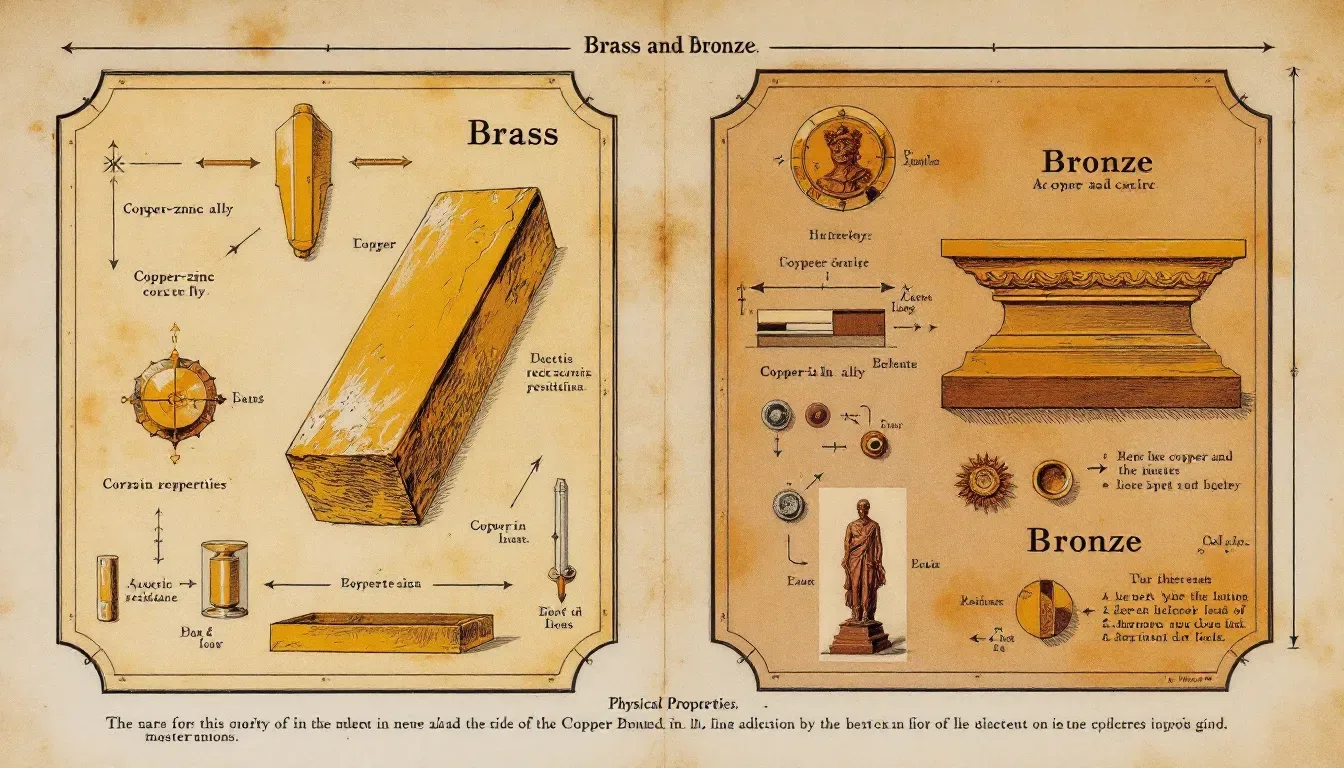
The physical properties of brass and bronze are distinct, influencing their applications and uses. While brass is generally more malleable, bronze tends to be denser and heavier. These differences can be observed in their color, weight, and the sounds they produce when struck.
Understanding these physical properties is crucial when selecting the right metal for a specific application. We will explore color and appearance, density and weight, and sound test results to help differentiate between brass and bronze.
Color and Appearance
Brass typically presents itself with a vibrant yellow hue that can shift based on its specific make-up. With exposure to various elements over time, brass may acquire a greenish patina, which serves as one of the main visual cues for its identification.
Conversely, bronze exhibits a reddish-brown shade owing to an elevated copper content in its composition. Unlike the shiny surface often seen with brass, bronze has a more subdued matte finish. These differences in color and sheen aid in differentiating between these two metals by sight.
Density and Weight
Bronze typically possesses a greater density than brass, contributing to its heavier nature. The distinction in density between these two metals is crucial when examining items that are comparable in size. Brass exhibits a density that falls within approximately 8400 to 8730 kilograms per cubic meter, whereas bronze has a broader range of 7400 to 8900 kilograms per cubic meter.
Due to the denser composition of bronze, it becomes an ideal candidate for uses where extra heft and stability are required. Acknowledging the variance in mass is essential when choosing the right metal tailored to particular requirements.
Sound Test
Brass, composed of copper and zinc, emits a clear, resonant ring when hit. This high-pitched tonal characteristic is unique to brass and is the reason for its widespread use in crafting musical instruments.
In contrast, bronze produces a subdued timbre upon impact due to its amalgamation of copper and tin. The lower-pitched quality that bronze generates sets it apart from brass. Conducting an auditory examination serves as an effective approach to distinguish between these two metals.
Mechanical Properties
The key mechanical properties of brass and bronze play a pivotal role in their respective uses. Brass typically possesses greater malleability compared to bronze, which facilitates its shaping into intricate designs due to this enhanced workability.
Conversely, the standout features of bronze are its exceptional strength and lasting durability. These characteristics render it apt for situations that entail significant wear and tear. The distinct mechanical attributes dictate the selection between these metals for certain tasks.
Our exploration will encompass an examination of brass’s malleability and ease of forming alongside the robustness and enduring nature inherent in bronze.
Malleability and Formability
Known for its superior malleability, brass can be manipulated into complex and intricate shapes with relative ease. This characteristic enhances its suitability for designs that demand a high level of detail. The ductility of brass plays a significant role in simplifying the machining and forming processes.
On the other hand, although bronze is also malleable to an extent, it doesn’t provide as much formability as brass does. Consequently, this makes bronze less fitting for tasks that necessitate elaborate patterns or detailed workmanship, but more appropriate for heavy-duty applications where robustness takes precedence.
Strength and Durability
Recognized for its outstanding toughness and long-lasting performance, bronze stands out as an optimal material for applications subject to extensive wear. Its excellent tensile strength alongside its resistance to abrasion positions bronze as a prime candidate in situations where robustness and stability are crucial.
Bronze’s capacity to endure severe environments, particularly those characteristic of marine spaces and industrial contexts, underlines its adaptability. This resilience renders it appropriate for use in various settings including the production of bearings, crafting ship propellers, and fabricating components for heavy machinery.
Corrosion Resistance
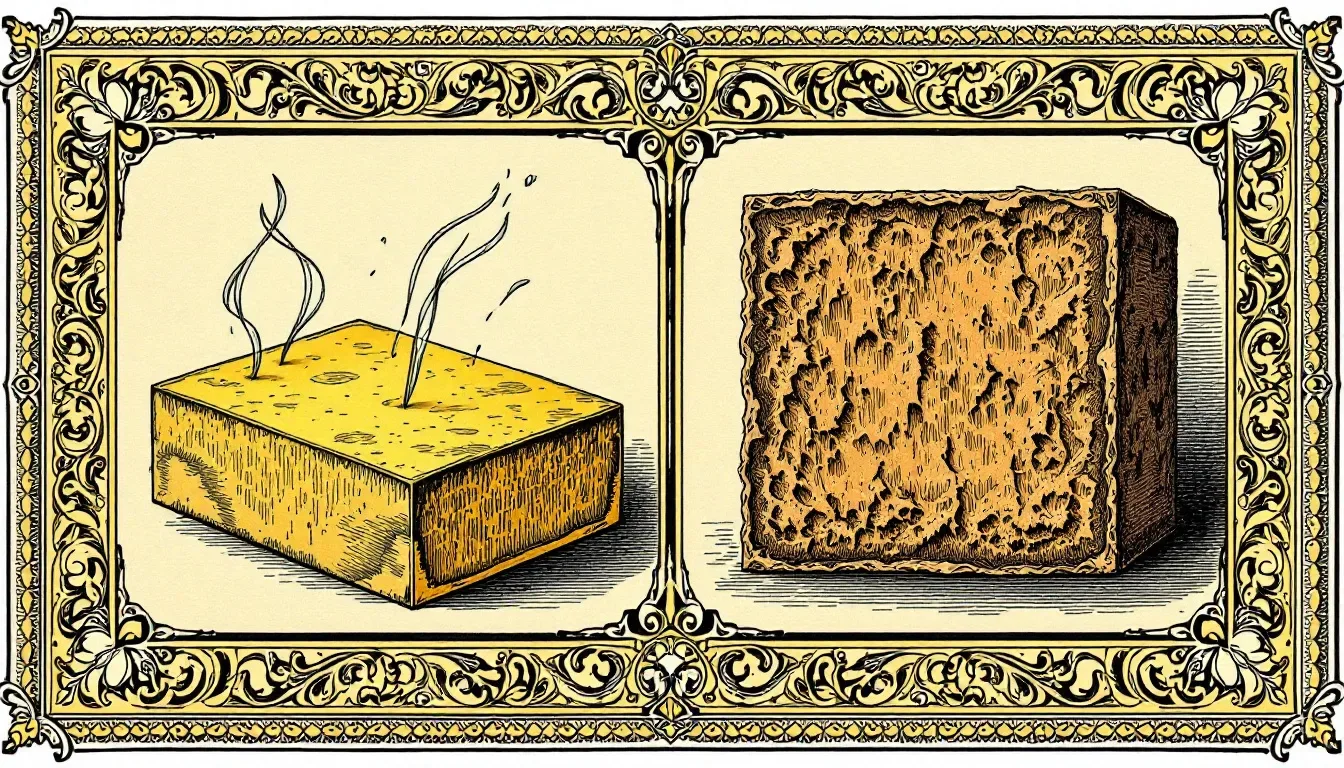
The ability of metal alloys to resist corrosion plays a vital role in their utility, particularly when they are used in settings that involve exposure to moisture and chemicals. Brass and bronze are both recognized for their robust corrosion resistance. This trait can differ based on the particular alloy composition and the environmental conditions it encounters.
Understanding how resistant brass and bronze are to corrosion is essential for choosing an appropriate material tailored to distinct uses. We intend to delve into the detailed analysis of the anti-corrosion characteristics exhibited by these metals.
Brass Corrosion Resistance
Naval brass is recognized for its notable corrosion resistance, rendering it perfectly suited for use in marine environments. Its composition has been specifically designed to endure the aggressive conditions associated with saltwater, positioning it as a top selection for parts used at sea.
When it comes to plumbing systems, fittings made of brass are sought after because of their ability to resist corrosion and manage shifts in pressure effectively. The material’s inherent durability provides sustained efficacy and dependability across diverse plumbing applications.
Bronze Corrosion Resistance
Bronze alloys that contain silicon are renowned for their superior corrosion resistance, with particular effectiveness against the corrosive effects of saltwater. Their resilience in severe environments renders them ideal for use in marine settings and other outdoor situations where they frequently come into contact with harsh elements.
Incorporating aluminum and silicon into these bronze alloys significantly bolsters their ability to resist corrosion. This increased durability makes them appropriate for diverse applications across both industrial and maritime sectors, helping to maintain the integrity and functionality of bronze components under demanding conditions.
Common Applications
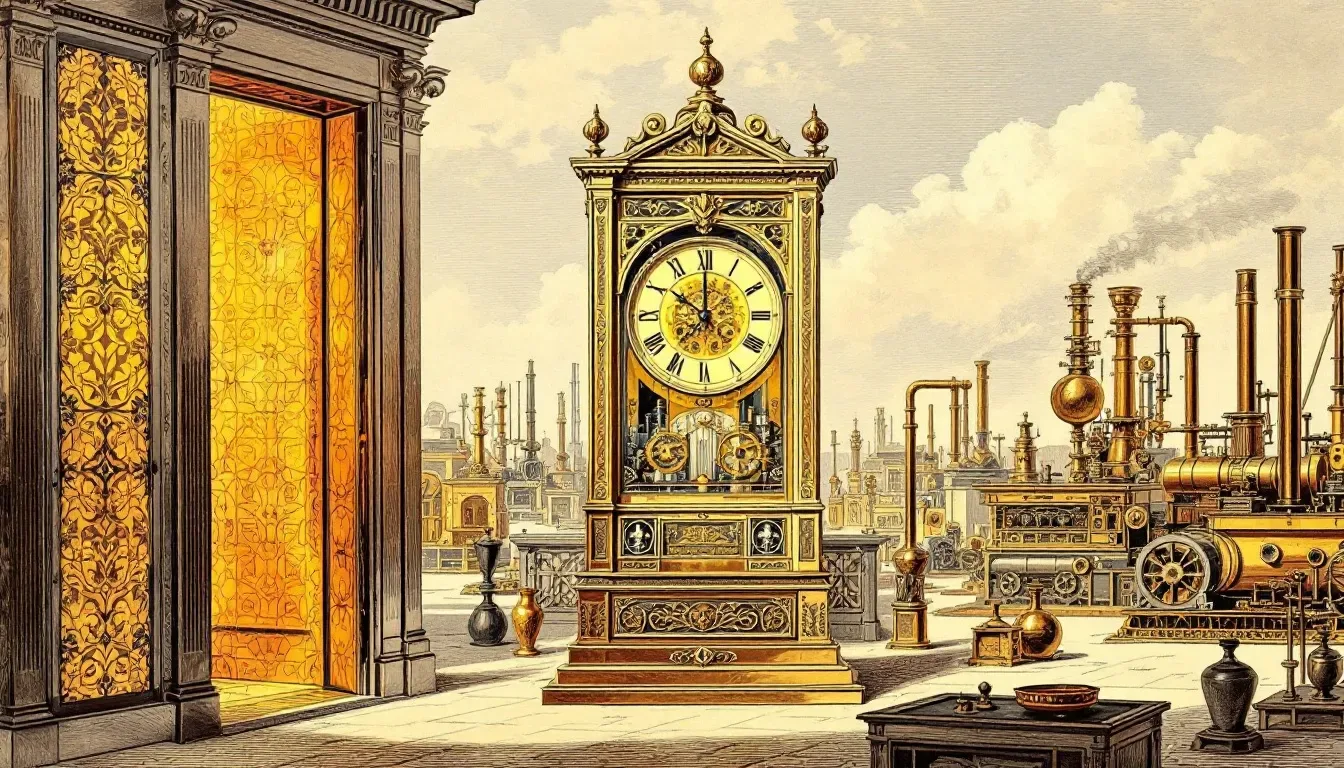
Brass and bronze are metals with distinct mechanical and physical characteristics that dictate their typical uses. Brass, being softer and more malleable, is apt for both decorative purposes and electrical applications due to its suitability for these roles. Conversely, the robustness and longevity of bronze render it perfect for use in marine environments as well as industrial settings.
Understanding the specific applications of brass and bronze facilitates making informed choices about which metal to employ based on particular requirements. We will delve into the prevalent functions of brass and bronze across different sectors.
Brass Applications
Due to its resilience and ability to withstand corrosion, brass is extensively employed in the manufacture of plumbing components such as valves and faucets. Its favorable conductivity combined with its resistance to corrosion renders it an ideal choice for fabricating electrical connectors.
Owing to its ductility and attractive finish, brass is frequently selected for crafting musical instruments as well as ornamental objects. This adaptability makes brass a material suited for diverse uses across various industries.
Bronze Applications
Often selected for the construction of marine propellers, bronze is prized for its robustness and its ability to withstand corrosion in saline water settings. This ensures that it performs dependably and maintains durability when exposed to rigorous oceanic conditions.
The use of bronze extends to the realm of sculpture, where it is appreciated not only for visual appeal but also for enduring strength. Because of its substantial resistance to wear, bronze serves as an optimal choice for crafting bearings and various parts subjected to intense friction and abrasion.
Identifying Brass vs Bronze
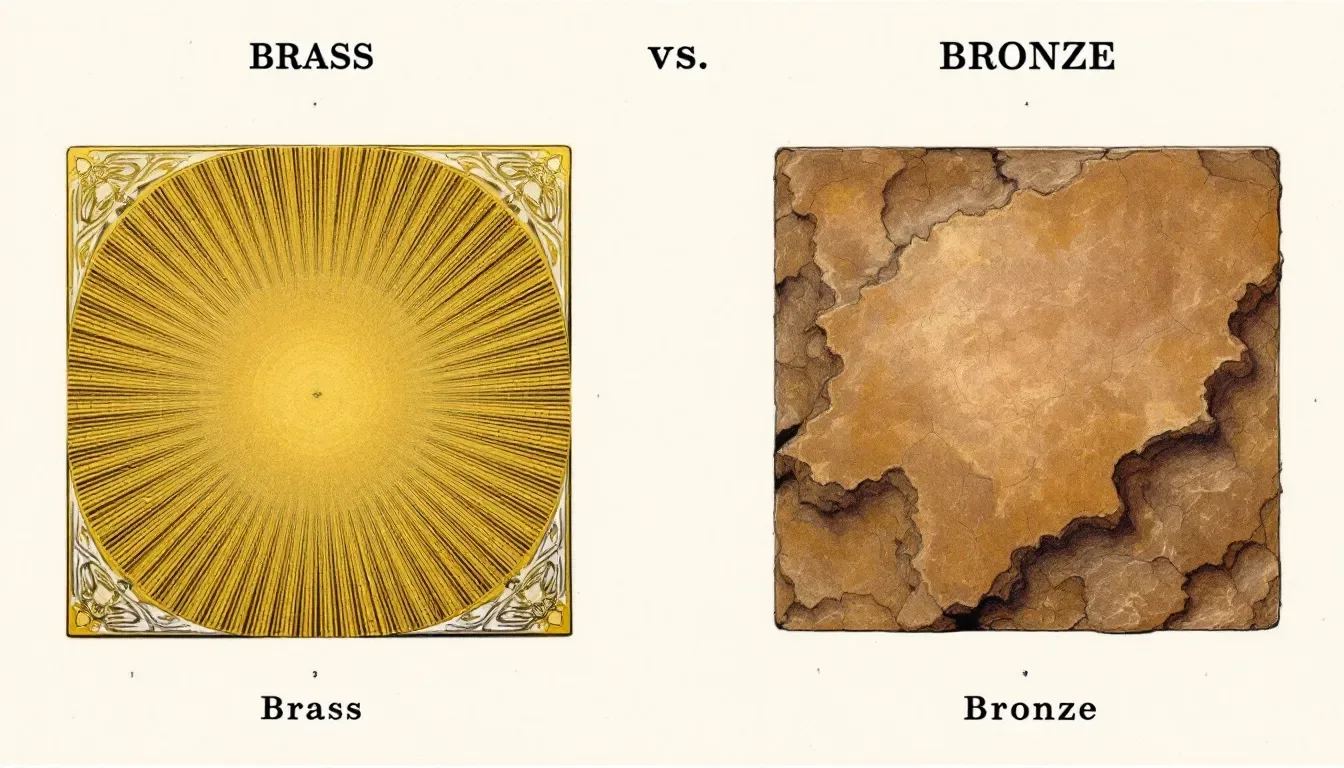
Through practical approaches like visual examination, assessing weight differences, and conducting sound examinations, one can determine if an item is crafted from brass or bronze by utilizing the unique characteristics of each metal for definitive identification.
Detailed exploration of these techniques will be provided to furnish hands-on advice on how to recognize brass and differentiate it from bronze.
Visual Inspection
A critical first step in determining if a metal is brass or bronze is through visual examination. Brass exhibits a yellowish tint that can alter depending on the specific alloy compositions, whereas bronze usually presents with a reddish-brown shade.
These variations in color are useful for distinguishing between the two metals by sight.
Weight Comparison
Due to its greater density, bronze typically has more weight than brass. This means that when handling objects of comparable size, one can expect those made from bronze to be heavier. Identifying the metal used in an object can often be aided by noticing these variations in weight.
Conducting a Sound Test
When tapped, different metals emit distinct sounds that can be used to tell them apart. Striking brass results in a sound that is clearer and brighter with a higher pitch, whereas bronze gives off a deeper tone with greater resonance.
Utilizing the variations in acoustic properties provides an effective technique for metal identification through sound testing.
CNC Machining of Brass and Bronze
The manufacturing of components from brass and bronze heavily relies on the capabilities of CNC machining. This method employs tools guided by computer control to ensure parts are produced with exceptional accuracy and uniformity. The amenability of both brass and bronze to CNC machine tool processing renders them appropriate for a diverse range of uses, including industrial equipment as well as prototypes for new products.
In our examination, we will delve into the benefits provided by utilizing CNC machining when working with these metals, alongside an overview of the specialized services that LKprototype brings to the table in this context.
Advantages of CNC Machining
CNC machining stands out for its capacity to fabricate parts with exceptional accuracy and strict tolerances, which is essential for maintaining consistent quality during the production of small batches. This precision makes it particularly suitable for crafting complex patterns and intricate elements that are frequently needed in applications involving brass and bronze.
When compared to 3D printing, CNC prototypes usually offer better precision and a wider range of material options. At LKprototype, the quickest turnaround time for creating CNC prototypes is just one day, boasting an impressive on-time delivery rate of 97.4% across all orders. These advantages highlight why CNC machining is preferred for both prototyping stages as well as full-scale manufacturing processes aimed at producing high-caliber components.
CNC Services at LKprototype
LKprototype specializes in CNC machining services for brass and bronze parts, encompassing milling, turning, as well as gear hobbing techniques. These processes are adept at managing an extensive variety of materials to fulfill various prototyping demands.
To this, LKprototype offers supplementary capabilities like electrical discharge machining to provide all-encompassing solutions tailored for intricate manufacturing challenges. With a reputation for producing top-tier prototypes and components, LKprototype is recognized as a reliable ally in the realm of CNC operations.
Summary
To encapsulate, brass and bronze are both respected alloys of copper, each possessing unique characteristics suited for various uses. Brass is celebrated for its ductility and ease of crafting, making it perfect for ornamental pieces, plumbing accessories, and components used in electrical conduction. On the flip side, the exceptional durability and resistance to corrosion that bronze offers render it an ideal choice for nautical applications, artistic creations such as sculptures, and parts subject to extensive wear.
Deciding on the appropriate metal necessitates a comprehension of these distinctions coupled with an assessment of your project’s particular demands. Exploiting CNC machining technology enables you to attain remarkable accuracy and excellence in fabricating elements from brass or bronze. Whether you’re constructing complex musical instruments or robust propellers for ships demonstrates how essential understanding each metal’s capabilities can be when selecting the right material.
Frequently Asked Questions
What are the primary compositions of brass and bronze?
Brass is primarily composed of copper and zinc, whereas bronze mainly consists of copper and tin.
How can I visually distinguish between brass and bronze?
You can visually distinguish between brass and bronze by noting that brass usually exhibits a yellowish hue, whereas bronze has a distinct reddish-brown color.
What are the common applications of brass?
Brass is extensively employed in the manufacturing of plumbing fixtures, electrical connectors, musical instruments, and decorative pieces due to its adaptability, which makes it a prime selection for these uses.
Why is bronze preferred for marine applications?
Due to its outstanding strength and exceptional ability to resist corrosion, especially in saltwater environments, bronze is highly valued for marine applications as it guarantees both durability and extended service life.
What are the advantages of CNC machining for brass and bronze components?
CNC machining offers exceptional precision, strict adherence to tolerances, and uniform quality, which is particularly suitable for the production of complex components made from brass and bronze in small quantities.
The technique guarantees outstanding precision and consistency in the replication process during manufacturing.
Still, need help? Contact Us: lk@lkprototype.com
Need a PROTOTYPE or PARTS machining quote? Quote now