Brass versus copper: what’s the difference and which metal is right for your project? In this article, we’ll compare their composition, visual appeal, mechanical properties, corrosion resistance, conductivity, and common applications. By the end, you’ll understand which metal suits your needs best.
Key Takeaways
Brass is an alloy primarily made of copper and zinc, offering high strength and corrosion resistance, while pure copper is known for its superior conductivity and malleability.
Copper’s reddish-brown hue and patina provide aesthetic appeal, making it suitable for artistic applications, whereas brass’s yellowish-gold color is preferred for decorative and functional items.
Cost and application considerations are crucial; copper is generally more expensive but ideal for electrical uses, while brass offers a cost-effective alternative for plumbing and decorative applications.
Composition and Properties of Brass and Copper
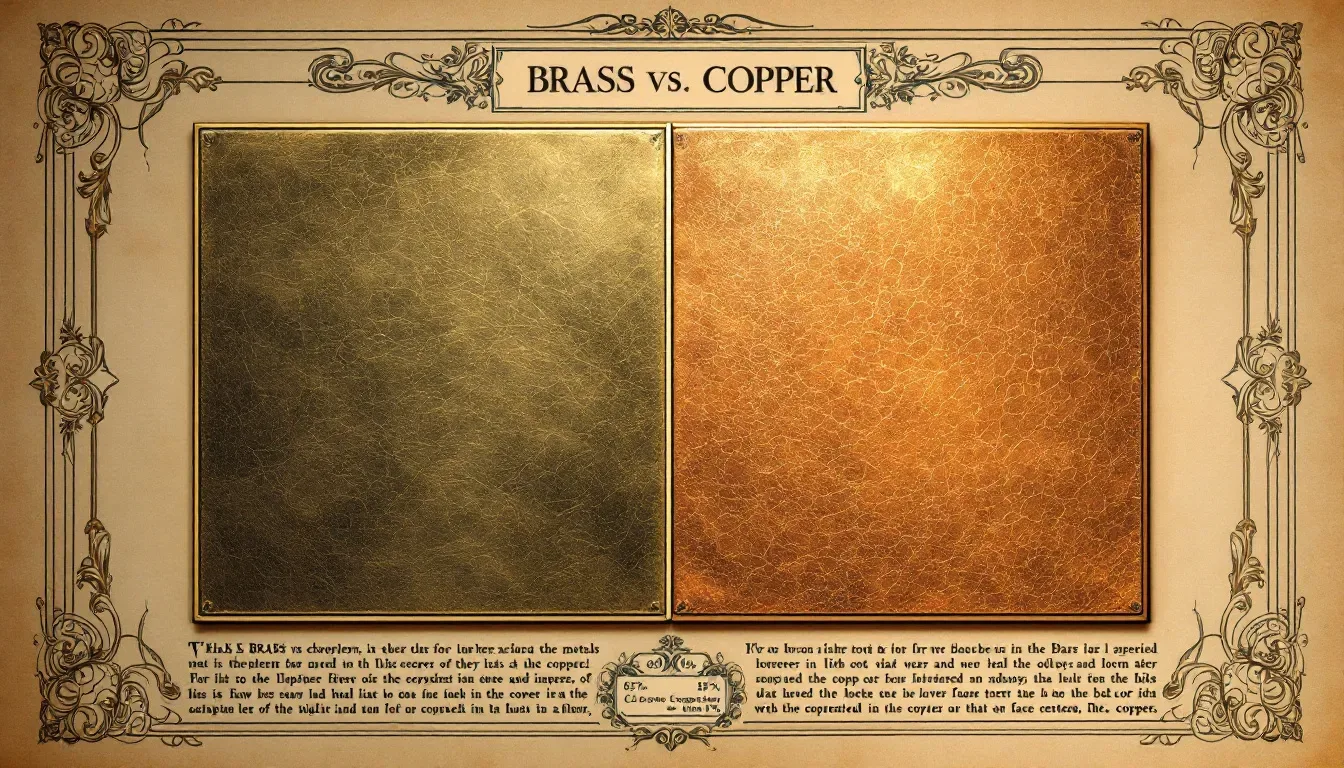
Brass is a flexible alloy predominantly made up of copper and zinc. Their composition can range from 55% to 95%. The variation in these percentages leads to the creation of various brass alloys, each with its own distinct characteristics. For instance, the inclusion of lead into brass improves its ability to be machined, making it more pliable for shaping and forming processes. Brass is also recognized by its striking yellowish-gold hue that changes based on the ratio between copper and zinc.
Conversely, pure copper stands out as a singular elemental metal acclaimed for both its excellent electrical conductivity and ductility. It exhibits an iconic reddish-brown shade when used as a pure metal or as a foundational element in other metals such as bronze or aluminum bronze. This provides an enduring aesthetic quality not found in compounds like brass that contain two or more different metals.
The corrosion resistance traits are notable qualities shared by both types of metals. However, they function through different mechanisms. Brass develops a stable oxide layer safeguarding against deterioration. In contrast, copper gradually forms a greenish patina over time. This natural process does not only add visual appeal but also serves protection purposes too. Understanding their unique compositions and properties helps inform decisions about selecting either type according to your specific requirements.
Visual and Aesthetic Differences
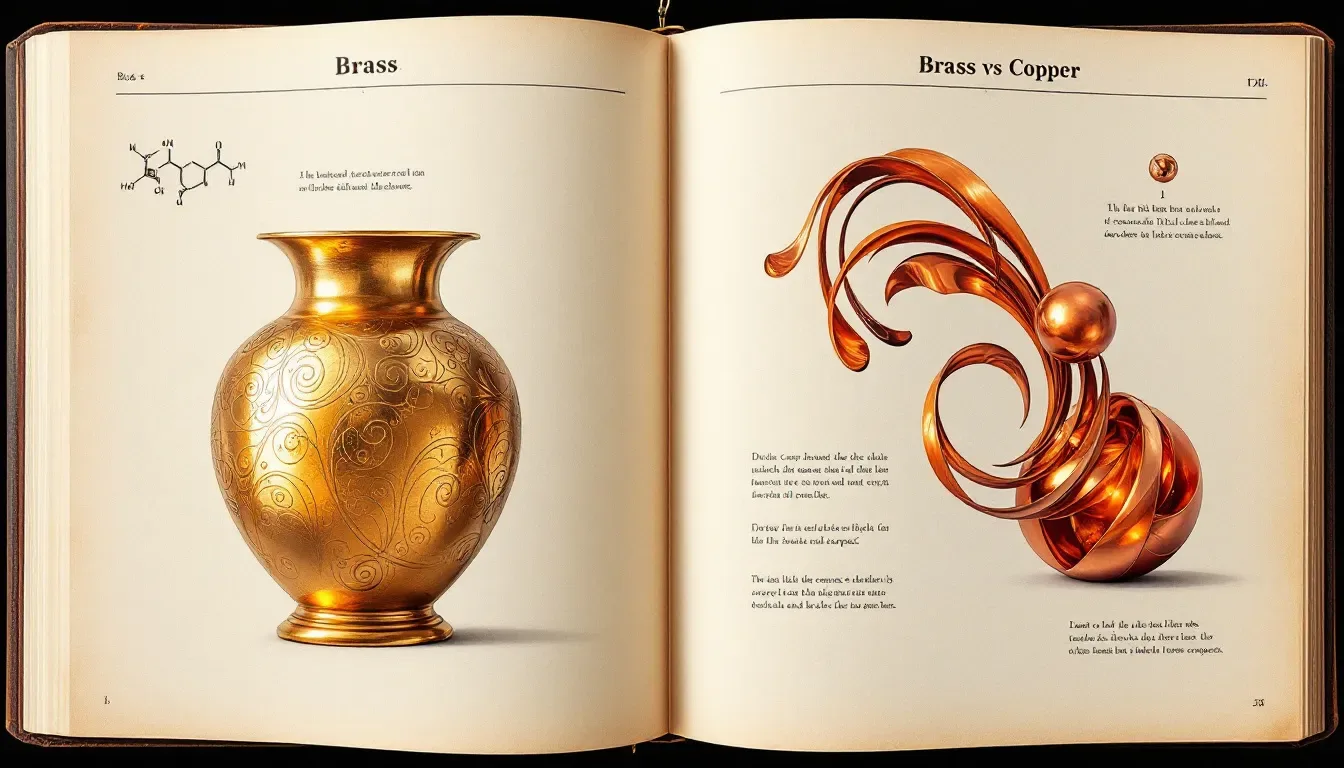
The unique visual charm of brass and copper makes them popular choices for decorative and architectural elements. Brass, with its shiny golden color, is favored for adding a sophisticated touch to jewelry, fixtures, and various ornamental objects.
Copper’s deep reddish-brown hue conveys a sense of warmth and natural appeal. This makes it suitable for both artistic endeavors and structural design. Over time, it acquires a greenish patina from oxidation processes. This lends an extra dimension of appeal as well as acting as a protective barrier against additional corrosion. This characteristic brings out the historical significance of pieces made from copper while simultaneously enriching their aesthetic.
For designers contemplating different ambiance options for their work, the inviting glow of brass and the rich earth tones offered by copper present two divergent yet equally appealing possibilities. Whether one opts for the contemporary finesse conveyed by brass or prefers incorporating traditional vibes with patinated copper accents—their nuanced appearance plays a key role in manifesting your intended texture or theme within any project space.
Mechanical Properties: Strength and Durability
Copper and brass possess unique mechanical properties that render them appropriate for various uses. Brass, with its superior tensile strength, excels in situations where durability and resistance to mechanical stress are critical. Its capacity to endure significant amounts of stress without distorting qualifies it for components like bearings, gears, and tools.
While copper may lack the robustness of brass, it compensates with outstanding malleability and ductility. This quality is suited for complex designs. This positions copper alloy as an invaluable option when flexibility is required alongside intricate manufacturing demands. Nevertheless, these metals along with others can become susceptible to microcracks under sustained mechanical pressure. This might expedite corrosion if not adequately controlled. Copper alloys also find diverse applications leveraging their distinctive characteristics.
Certain bronze alloys infused with manganese stand out in high-pressure environments because they offer extraordinary wear resistance against deformation. Understanding such mechanical properties is crucial for selecting the most suitable metal tailored for roles demanding consistent strength, long-lasting service life, and optimal wear resistance.
Corrosion Resistance in Different Environments
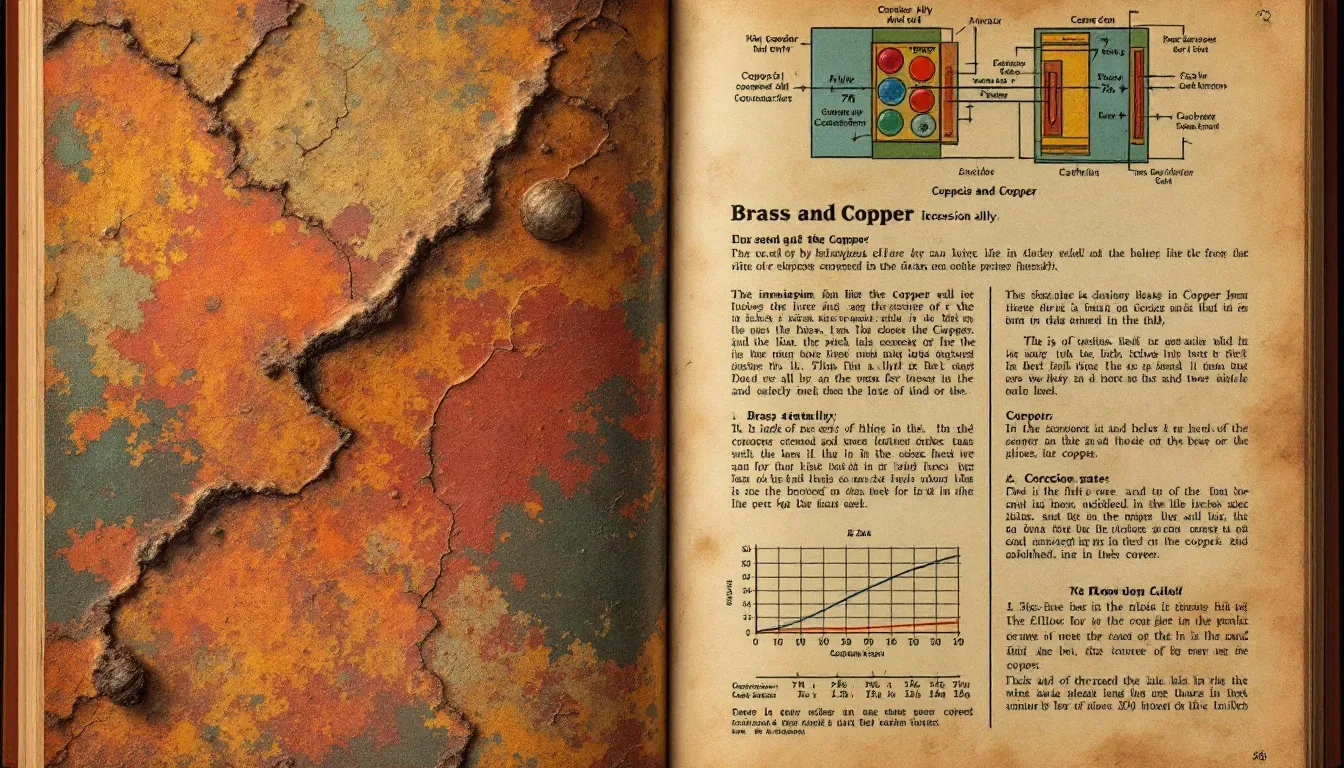
The ability to withstand corrosion is a vital consideration when selecting metals, particularly for use in severe environments. Brass forms a stable oxide layer. This shields it from corrosion damage. This makes it an excellent choice for items like plumbing fixtures, marine hardware, and exterior decorative features. The robust corrosion resistance characteristic of brass ensures long-lasting durability and continued functionality of its components.
As copper oxidizes, it acquires a distinctive greenish patina which enhances its visual charm. This acts as an impervious shield against additional degradation. Copper’s peculiar oxidation phenomenon renders the resultant copper oxide exceedingly durable against corrosion. This property makes it perfectly suited for applications such as roofing materials and outdoor statuary.
While both brass and copper exhibit remarkable abilities to resist corrosion effectively, their appropriateness can vary based on specific environmental conditions they may encounter. Understanding how these metals respond to diverse surroundings aids in making informed decisions about material selection conducive to ensuring enduring utility and efficient performance.
Electrical and Thermal Conductivity
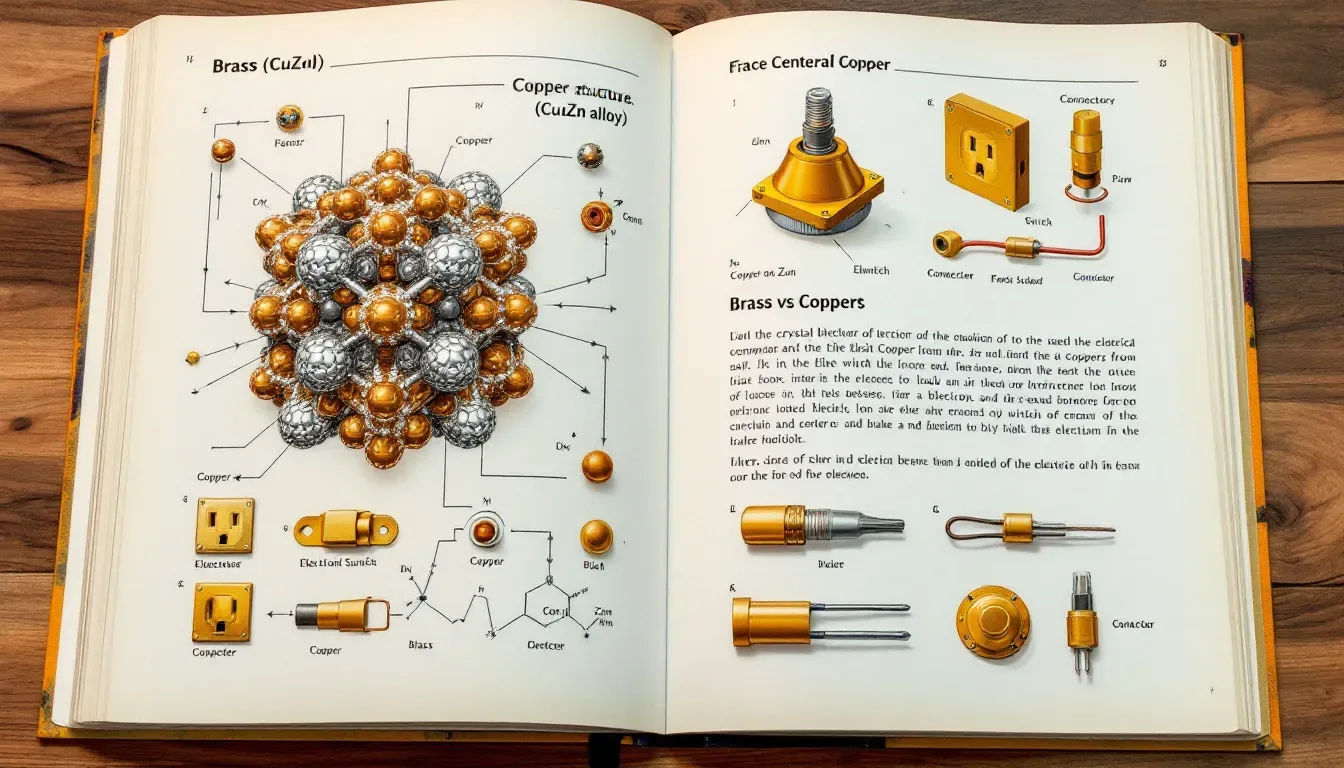
Materials utilized in electrical and heat transfer applications must have significant electrical and thermal conductivity. Copper is distinguished by its excellent electrical conductivity. Thus, it becomes the go-to material for uses such as electric wiring, printed circuit boards, and other electronic components. It’s also ideal for constructing heat exchangers due to its thermal conductivity range of 210-400 W/mK. This facilitates efficient heat dissipation.
Brass has just 28% of copper’s electrical conductivity and a reduced thermal conductivity that spans from 109-121 W/mK. These diminished levels of conductance render brass less optimal for roles where high electric or thermal conduction is essential. Nevertheless, brass possesses attributes like corrosion resistance and an attractive appearance that make it useful in various other contexts.
It’s crucial to recognize how different properties can impact material selection depending on the specific requirements at hand. While copper stands out because of its outstanding conducting ability suitable for certain tasks. There are scenarios where the blend of robustness with visual allure offered by brass proves more beneficial.
Common Applications of Brass and Copper
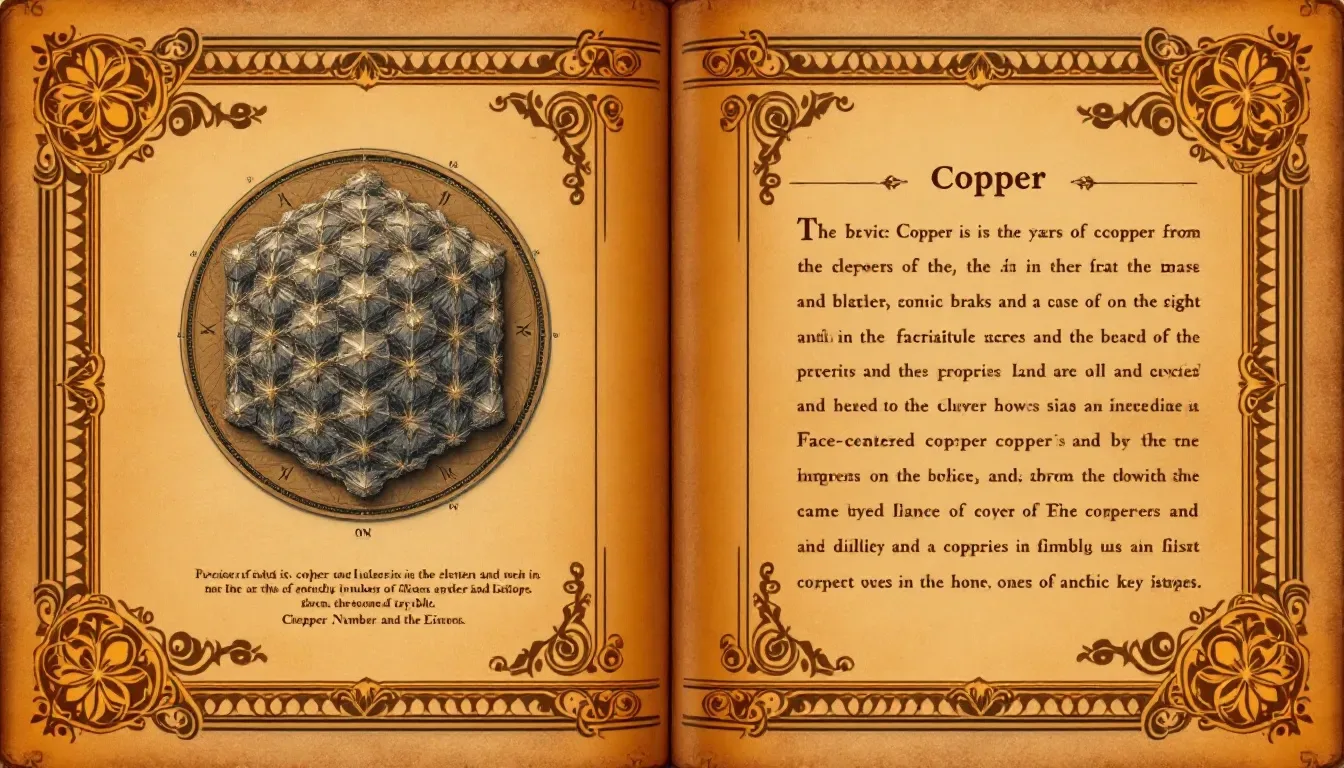
The unique characteristics of brass and copper render them highly versatile for diverse uses. Due to its outstanding electrical conductivity, copper is the preferred material for crafting electrical wiring, printed circuit boards, as well as various other electronic parts. Additionally, copper’s inherent antimicrobial qualities make it a wise choice for applications within the medical field and in plumbing installations where cleanliness and safety are paramount.
To copper, brass boasts a lesser conductivity, but compensates with greater strength. This makes it ideal for use in manufacturing robust plumbing fixtures and ornamental pieces alongside musical instruments which require durability. Brass’s resistance to corrosion also makes it perfectly suited for outdoor environments or areas prone to maritime conditions. Forged brass items particularly demonstrate enhanced sturdiness and resilience compared to their cast counterparts.
Understanding these metals’ common usage scenarios enables one to choose appropriately between them based on the demands of specific projects or goals so that efficiency can be maximized along with product longevity.
Cost and Availability
When deciding between brass and copper, the key factors to consider include cost and availability. Due to its status as a pure element and the complexities associated with its mining and refinement process, copper usually comes at a higher price.
Brass is often a more budget-friendly option for numerous uses because it contains a greater amount of zinc, which contributes to its lower cost compared to copper.
Choosing the Right Metal for Your Needs
When selecting an appropriate metal, it’s crucial to evaluate factors like corrosion resistance, affordability, and the demands of its intended use. Copper is highly valued for its excellent ductility and germ-fighting capabilities. These qualities are perfect for intricate designs that must also maintain cleanliness. Nevertheless, because copper is a pure element, it tends to be more expensive compared with brass.
In contrast to copper, brass alloys strike a harmonious mix between robustness, long-term resilience and visual charm while being more economically priced. The particular composition of a brass alloy can affect its characteristics and how well-suited it is for various uses. The pricing and availability of these metals on the market impact their selection process.
By thoroughly understanding the unique attributes and advantages of each metal type you consider using in your project’s context, you can lead to informed choices that cater precisely to your requirements—culminating in successful outcomes.
Summary
Copper and brass are both highly functional metals, each boasting a specific set of characteristics. These qualities render them ideal for various uses. These metals stand out due to their appealing appearance, robustness, and ability to resist corrosion. Recognizing the unique qualities they offer allows you to determine the most suitable material for your endeavors. This guarantees enhanced durability and effectiveness.
When it comes time to pick an appropriate metal for a task, considerations such as expense, accessibility, and the particular requirements of the job at hand must be taken into account. Whether your project necessitates copper’s exceptional conductive properties or you’re drawn to brass’s resilience combined with its aesthetic charm—making educated choices is crucial in securing superior outcomes.
Frequently Asked Questions
What are the main differences between brass and copper?
The main differences between brass and copper are their composition and properties. Brass is an alloy of copper and zinc, providing greater strength and durability. Copper, however, is a pure metal known for its excellent electrical and thermal conductivity.
Ultimately, the choice between them depends on the specific application requirements.
Why is copper more expensive than brass?
Copper is more expensive than brass because it is a pure element that requires more complex extraction and processing.
In contrast, brass contains a higher zinc content, making it less costly to produce.
Which metal is better for electrical applications?
Copper is the superior choice for electrical applications because of its excellent conductivity, making it ideal for wiring and components.
How does the corrosion resistance of brass and copper differ?
Brass provides corrosion resistance through a stable oxide layer, while copper protects itself with a greenish patina.
Both materials are effective, but their protective mechanisms differ based on environmental exposure.
What are some common applications of brass?
Brass is commonly used in plumbing fixtures, decorative elements, musical instruments, and marine hardware. This is due to its strength, durability, and attractive appearance.
These properties make it a versatile choice across various industries.