Facing a choice between alloy steel vs stainless steel? Understanding their differences in strength, corrosion resistance, cost, and applications will help you decide the best material for your project.
Key Takeaways
Alloy steel is versatile and primarily used for high strength and toughness applications, while stainless steel is known for its superior corrosion resistance and aesthetic appeal.
The choice between alloy steel and stainless steel depends on factors like mechanical properties required, environmental conditions, and long-term cost considerations, with alloy steel being generally less expensive upfront but potentially requiring more maintenance.
Understanding the specific applications of each type of steel—such as alloy steel in construction and automotive sectors versus stainless steel in food, medical, and marine applications—is essential for making an informed material selection.
Understanding Alloy Steel
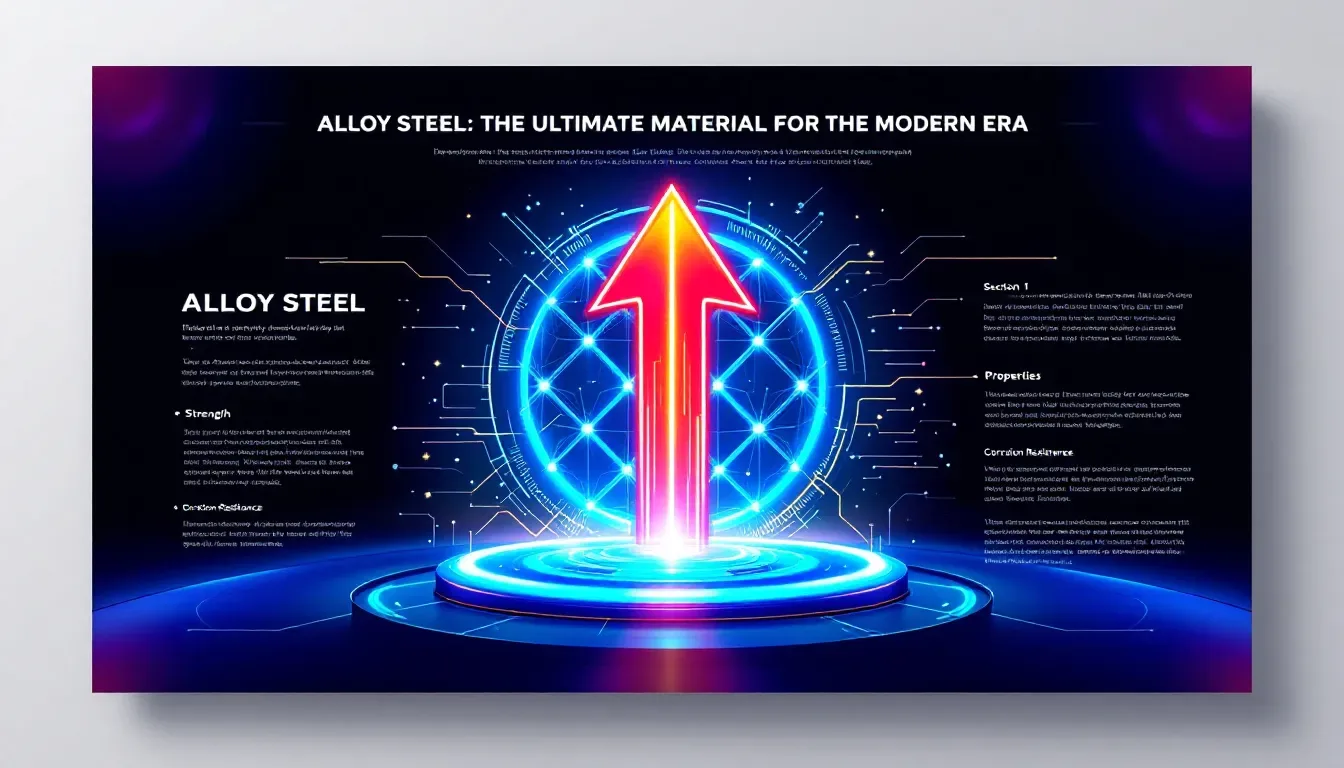
Alloy steel stands as a testament to the advances of contemporary engineering, characterized by its formulation which incorporates numerous alloying constituents beyond just iron and carbon steel. These components blend with the foundational metal’s matrix, transforming its attributes to become exceptionally adaptable. The fundamental makeup of alloy steel encompasses iron, carbon, along with one or several additional alloying elements such as chromium, nickel, molybdenum, and vanadium. Its capacity for precise customization for diverse uses comes from the judicious integration of these elements.
The introduction of alloying substances significantly augments the characteristics of alloy steel by amplifying its strength, durability, ease of hardening processes and improving resistance against wear. Consequently, making it suitable for use in industries like construction.
Automotive aerospace manufacturing industries where high-performance materials are crucial. Heavy equipment also benefits from this material due to superior strength-to-weight ratio qualities that deem it fitting for demanding projects necessitating stalwart yet light constructs.
Types of Alloy Steel
Steel alloys are divided into two main groups: low alloy steels and high alloy steels. Low alloy steels have an alloying element content below 8%, incorporating modest quantities of elements such as chromium, molybdenum, or nickel. The addition of these elements moderately enhances the mechanical properties while maintaining a reasonable cost, making them economically efficient for numerous uses. Enhanced strength, toughness, and hardenability are among the notable qualities of low alloy steels.
In contrast to their lower-content counterparts, high-alloy steel varieties possess over 8% of various alloying constituents with concentrations frequently exceeding 5% for components like chromium, molybdenum or nickel. Recognized for their improved hardness and toughness along with superior corrosion resistance qualities make them suitable choices where demanding performance is required in harsh conditions. High-alloy variants often incorporate substantial levels of manganese, vanadium and tungsten that play pivotal roles in boosting their overall capability to withstand challenging operating environments.
Common Alloying Elements
The distinctiveness of alloy steel is attributed to the unique properties imparted by its alloying elements. Commonly used additions such as vanadium, nickel, manganese, molybdenum, titanium, and tungsten tailor various alloys for specific enhancements. For example, chromium significantly increases toughness, hardness, and wear resistance, which translates into improved durability under severe conditions. Meanwhile manganese contributes to an increase in ductility and hardenability along with augmenting wear resistance. This allows the metal structure to endure greater levels of stress without permanent deformation.
In terms of enhancing performance characteristics like strength and wear resistance in steel matrices, molybdenum plays a pivotal role. It functions by obstructing dislocation movements within the matrix, leading to stronger mechanical attributes. The deliberate selection and combination of these different elements ultimately determine how alloy steel performs, making it highly adaptable for challenging industrial applications that demand robust material solutions.
Exploring Stainless Steel
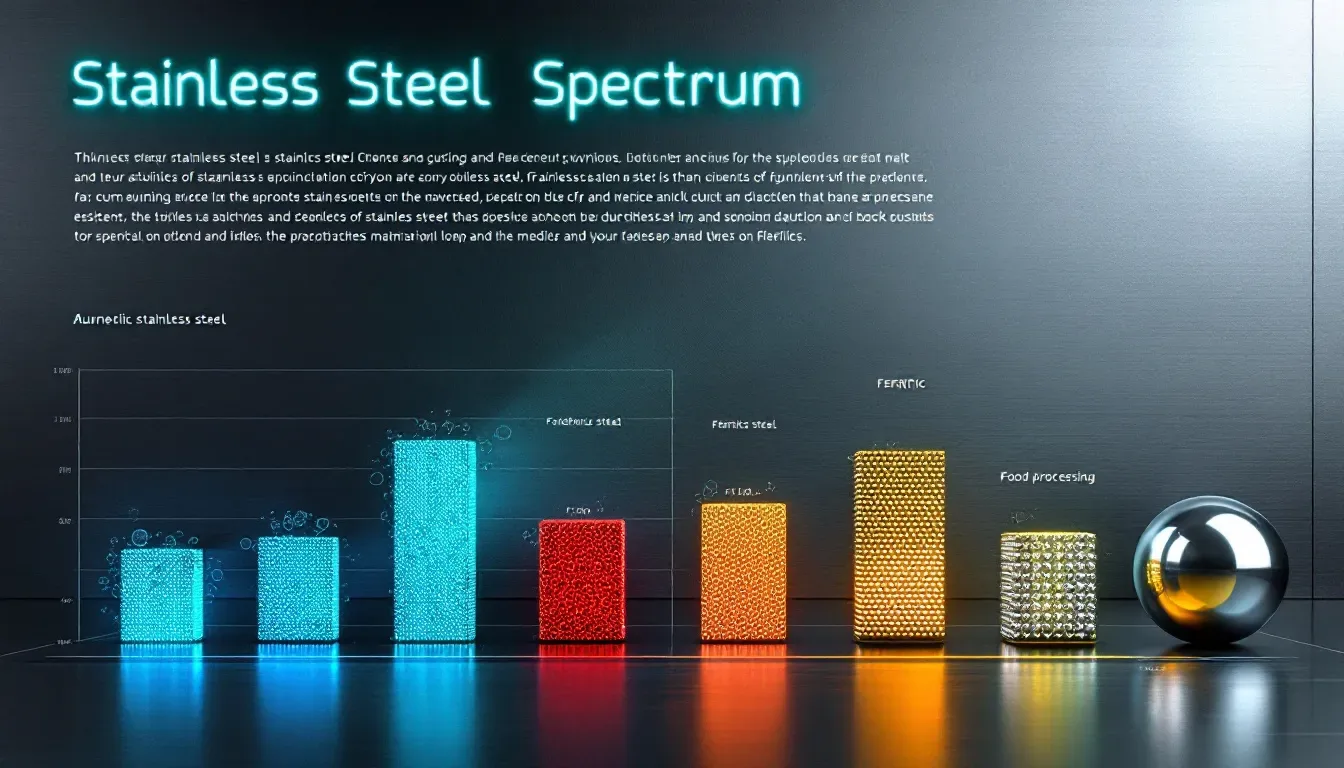
Stainless steel is renowned in the field of metallurgy for its exceptional corrosion resistance and visual attractiveness. It’s characterized by a composition that includes at least 10.5% chromium, along with iron and carbon as primary constituents. This specific blend enables stainless steel to develop a protective passive oxide layer on its exterior, safeguarding it against both corrosion and discoloration. This material can endure higher temperatures without losing structural integrity or strength, making it an adaptable option for many different uses.
The sleek and contemporary appearance of stainless steel contributes to its popularity in sectors where style is crucial, such as architecture and kitchenware manufacturing. The ease with which it can be cleaned adds to its desirable factor. Beyond aesthetics, features like durability and non-magnetic characteristics increase the suitability of stainless steel across various industrial fields as well as consumer products applications.
Types of Stainless Steel
There are multiple varieties of stainless steel, each distinguished by its distinct properties and specific uses. The main categories of stainless steel encompass austenitic, ferritic, martensitic, duplex, and precipitation-hardened steels.
Austenitic stainless steels like the 304 and 316 grades boast excellent corrosion resistance and malleability which render them versatile for a multitude of purposes. On the other hand, ferritic stainless steels such as grade 430 demonstrate good corrosion resistance that lends well to their employment in automotive parts and industrial settings.
Martensitic variants including grades 431 and 420C distinguish themselves with superior hardness along with wear resistance that is advantageous for manufacturing cutting implements as well as medical devices. Meanwhile, duplex stainless steels meld the characteristics inherent in both austenitic and ferritic types offering an exceptional defense against pitting erosion alongside stress-induced cracking susceptibility.
These diverse classifications among different grades of stainless steel serve to fulfill varied requirements ensuring there is an appropriate option available for any application at hand.
Corrosion Resistance Properties
Stainless steel is widely acclaimed for its ability to resist corrosion, a trait largely attributed to the incorporation of chromium. Chromium’s role involves creating a self-repairing passive oxide layer on the steel’s exterior that consistently preserves the metal’s durability.
Stainless steel benefits from additional elements such as nickel and molybdenum which bolster its defense against diverse types of corrosion like pitting and crevice corrosion. This fortification renders stainless steel an ideal material for demanding settings, particularly in marine and industrial contexts where it may be subject to corrosive agents.
Mechanical Properties Comparison
In the process of comparing alloy steel with stainless steel, it is essential to consider their respective mechanical attributes like strength, endurance, and flexibility. Alloy steel is frequently chosen for roles that demand heightened strength and resilience due to additional elements which amplify these characteristics. Conversely, stainless steel is celebrated for its exceptional ability to resist corrosion—this quality renders it particularly valuable in situations prone to contact with corrosive materials.
The contrasting mechanical qualities between alloy steel and stainless steer decisively into their appropriateness for different tasks. Where intense stress or impact resistance is necessary, alloy steels take precedence. When facing scenarios demanding long-term durability against deterioration by corrosive agents, the superior corrosion resistance offered by stainless steels makes them a preferable option.
Tensile Strength
The capacity of a material to resist forces that attempt to stretch it is referred to as tensile strength. When compared with stainless steel, alloy steel demonstrates notably higher tensile strength, with measurements between 758 and 1882 MPa. Conversely, the typical range for the tensile strength of stainless steel falls between 515 and 827 MPa.
Due to its greater durability and ability to support heavier loads, high alloy steel is considered more appropriate for structural uses where increased robustness is necessary.
Fatigue Strength
The capacity of a material to endure repeated stress without failure is known as fatigue strength. Alloy steel typically demonstrates greater fatigue strength than stainless steel, rendering it more appropriate for uses that experience cyclical loading.
Specifically, duplex stainless steel possesses robust fatigue strength, making it beneficial in settings such as bridge construction and offshore platforms where cyclic stresses are frequently encountered.
Impact Resistance
For applications where materials must endure abrupt and strong impacts, the ability to resist such forces is essential. The increased hardness of alloy steel improves its capacity to withstand impacts when compared to stainless steel. On the other hand, stainless steel has a higher tendency to break under conditions involving impact, rendering it less suitable for applications where safety is a key concern.
Due to this distinction in impact resistance properties, alloy steel emerges as the preferred option for sectors like automotive and aerospace that prioritize this characteristic.
Corrosion Resistance and Environmental Suitability
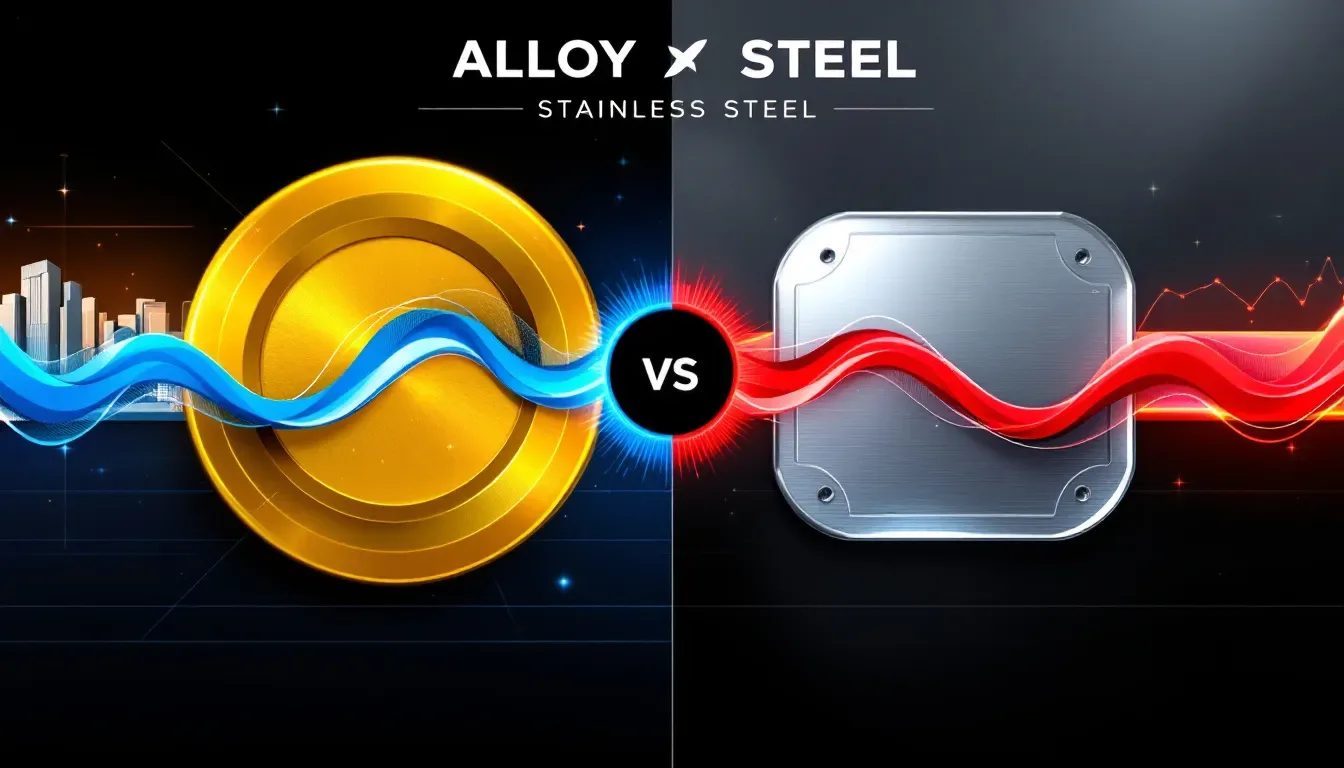
When selecting materials for areas that are at risk of coming into contact with corrosive agents, the ability to resist corrosion is a crucial consideration. Stainless steel, due to its increased chromium content, typically demonstrates more effective corrosion resistance than alloy steel and is often recognized as being corrosion resistant. As such, stainless steel becomes the material of choice in severe and corrosive conditions found within marine and chemical industries.
The compatibility of both alloy steel and stainless steel with their intended environments depends on their respective compositions as well as the specific environmental challenges they will encounter. Alloy steels might necessitate additional protective coatings or consistent maintenance to combat corrosion effectively. In contrast, stainless steels inherent capacity for resisting corrosion means there’s less reliance on these preventive strategies. Although initially costlier, stainless steel may be more cost-effective over time for certain uses due to this diminished need for upkeep measures.
General Corrosion Resistance
Stainless steel boasts a markedly superior general corrosion resistance compared to alloy steel, largely attributable to the chromium it contains. This element enables stainless steel to form a passive oxide layer that has self-repairing properties when damaged, which in turn prolongs its service life in corrosive environments. The enhanced corrosion resistance of stainless steels is a key factor behind their extensive utilization across diverse applications.
The discrepancy in corrosion resistance between these materials affects their appropriateness for certain industrial uses. Stainless steel emerges as the material of choice for scenarios where there’s regular exposure to corrosive substances.
Special Corrosion Conditions
Exposure to chloride ions can severely affect the behavior of stainless steel, leading to specific types of corrosion such as pitting and crevice corrosion. These are prevalent in settings with elevated levels of chlorides. The chromium content within stainless steel acts as a defense against this localized type of corrosion, which is why it’s often used in marine and chemical settings.
On the other hand, alloy steel may not perform well under similar circumstances unless extra precautions are taken for its protection.
Heat Resistance and Treatment
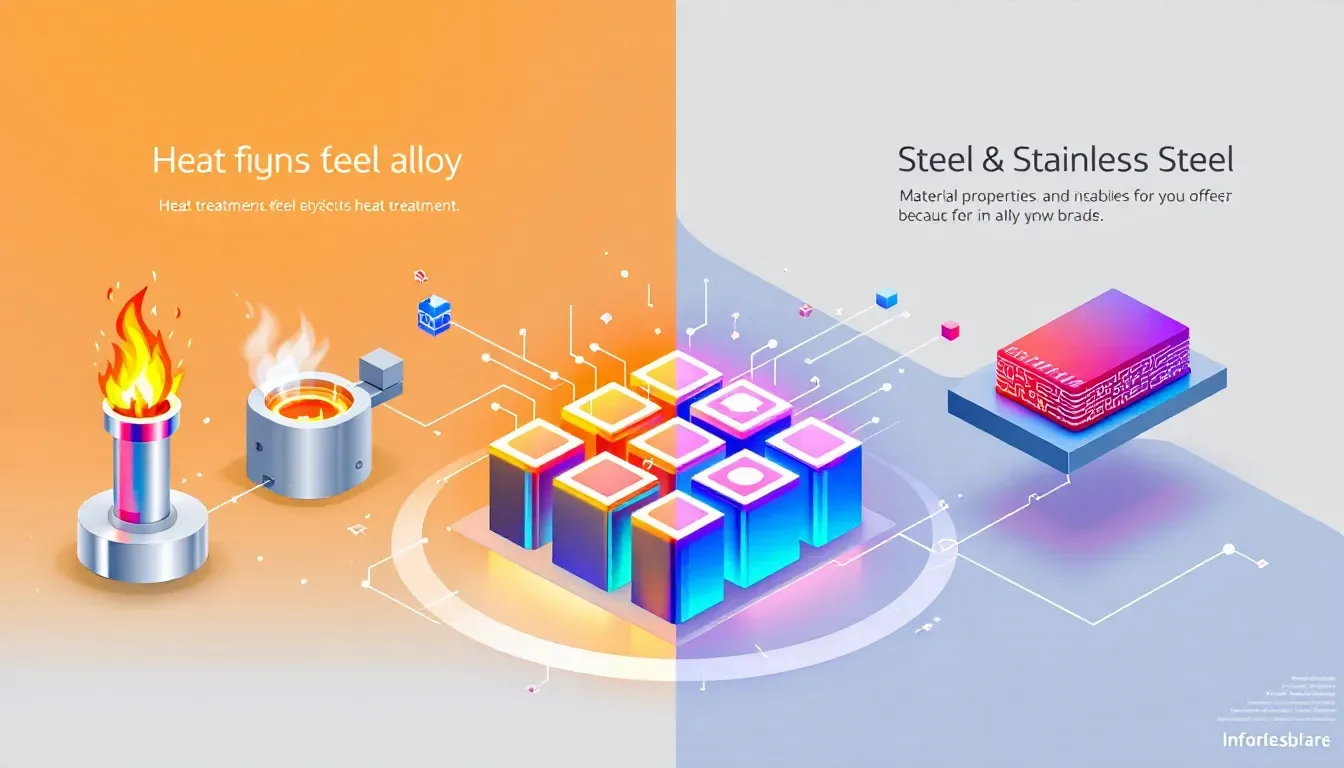
Enhancing the characteristics of both alloy steel and stainless steel heavily relies on heat resistance and treatment techniques. Common practices such as quenching, tempering, annealing, and normalizing are implemented to augment the mechanical properties of alloy steels. These methods modify attributes like hardness, ductility, and brittleness to suit diverse applications.
Conversely, for stainless steel varieties, thermal treatments including annealing, stress relieving, and hardening are applied to boost their functional performance. Such processes ensure that stainless steel retains its stability and structural integrity even under extreme temperatures conditions, which is essential for uses demanding outstanding heat resistance.
An understanding of these various heat treatment procedures is key when selecting an appropriate type of steel for use in environments subject to high temperatures.
Heat Treatment Processes
Enhancing the characteristics of both alloy steel and stainless steel is crucial, which can be achieved through various heat treatment processes. Low alloy steel benefits from reduced annealing temperatures that bolster its strength and resilience. The typical procedures for treating alloy steel include quenching, tempering, annealing, and normalizing. While stainless steels are commonly subjected to annealing, stress relieving, and hardening.
These treatments are designed to augment particular mechanical properties tailored to the needs of their respective applications. Recognizing these heat treatment techniques is essential when selecting suitable steels for specific purposes such as manufacturing automotive parts or producing food processing machinery.
High Temperature Performance
Austenitic stainless steels are renowned for their robust stability and integrity when exposed to high temperatures. Their ability to retain properties at elevated temperatures renders them perfect for use in applications such as boilers and heat exchangers.
On the other hand, although alloy steel can withstand high temperatures effectively, it might necessitate extra treatments to preserve its structural integrity. Consequently, austenitic stainless steel is often the preferred material for environments where it’s essential to maintain the material’s integrity under high-temperature conditions.
Applications and Industry Use
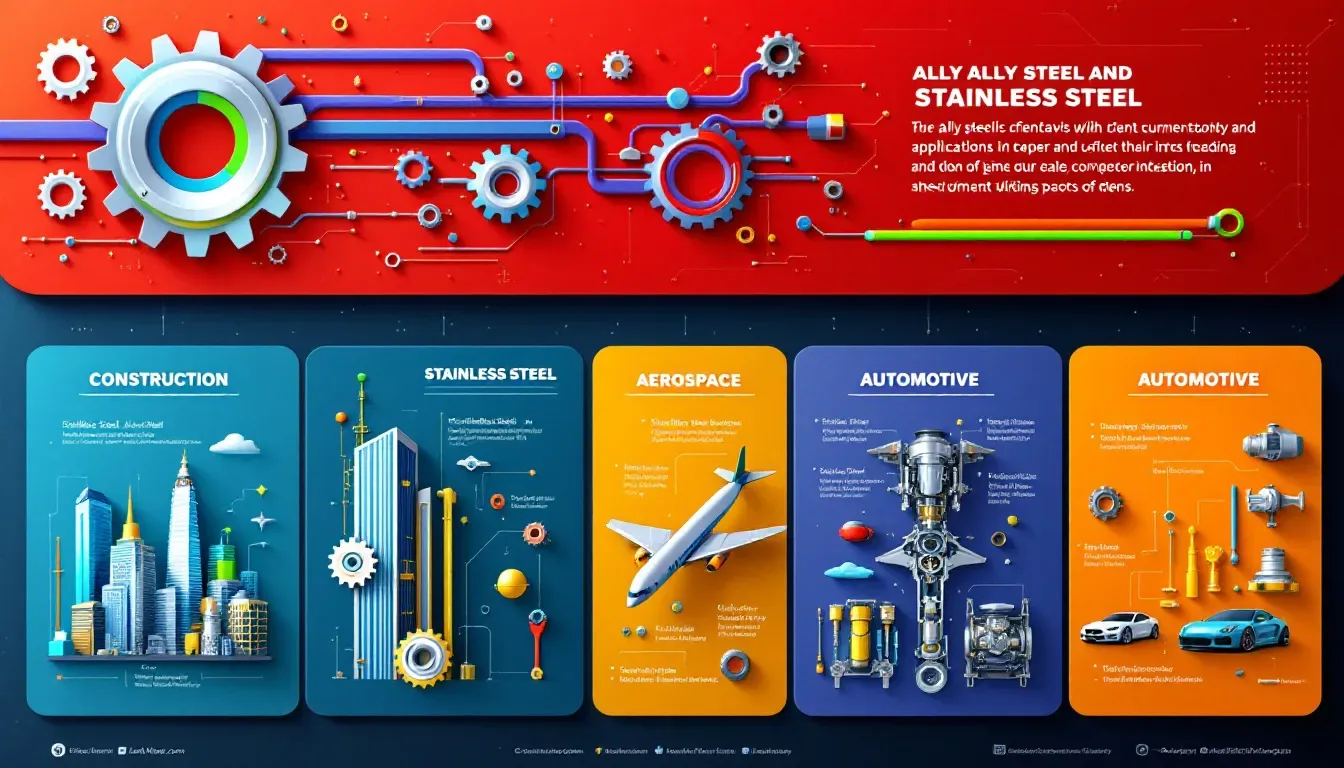
The applications of alloy steel and stainless steel are as diverse as the industries that rely on them. Alloy steel, with its high strength-to-weight ratio, is commonly used in construction, automotive, aerospace, and heavy machinery industries. Its ability to withstand high stress and impact makes it ideal for structural components like beams, engine parts, and heavy-duty machinery.
Stainless steel, on the other hand, is designed to withstand high temperatures and corrosive environments, making it suitable for applications like heat exchangers, boilers, and medical devices. Its excellent corrosion resistance and aesthetic appeal also make it a popular choice in the food and beverage industry, as well as in architectural applications.
Alloy Steel Applications
Various industries find alloy steel crucial because of its superior mechanical properties. Within the automotive sector, it serves to enhance both the efficiency and safety features of engine parts. For construction applications, key structural components such as beams and columns depend on alloy steels for their essential strength.
In aerospace applications, alloy steel is valued for creating components that demand both high strength and low weight characteristics. Heavy machinery takes advantage of the wear resistance and durability offered by alloy steel to ensure longevity under strenuous conditions.
Stainless Steel Applications
The multifaceted nature of stainless steel renders it an essential material across numerous sectors. Its exceptional corrosion resistance and easy-to-clean surface make it particularly valuable in the food and beverage industry, where its resilience to food acids is critical. For medical devices, stainless steel’s compatibility with biological systems along with its capacity to endure sterilization methods stands out.
In fields such as the chemical and petrochemical industries, stainless steel is sought after for its outstanding ability to resist deterioration from corrosive substances. Duplex stainless steel exhibits enhanced fatigue strength that proves beneficial for cyclic load applications like bridges and marine structures typically found offshore.
Owing to its robustness against corrosion, stainless steel emerges as a preferred choice within marine environments as well.
Cost Considerations
Alloy steel tends to be more economical compared to stainless steel, mainly due to the lower costs associated with its alloying components. In contrast, the inclusion of expensive elements such as chromium and nickel in stainless steel contributes significantly to its higher cost. These financial factors are crucial when choosing materials as they can greatly impact the budget of a project.
In situations where corrosion resistance is paramount, investing in stainless steel might prove beneficial despite its greater upfront cost because it offers extended durability and requires less upkeep over time. Conversely, while initially cheaper, alloy steel may necessitate additional expenses for protective treatments or consistent maintenance to combat rust and deterioration.
Henceforth, considering both the purchase price and ongoing care requirements suggests that stainless steel could ultimately result in reduced cumulative expenses throughout its service life for certain uses due to its lasting nature and negligible maintenance needs.
Initial Costs
Alloy steel presents a more economical choice for numerous endeavors, as it is commonly less costly compared to stainless steel. The elevated price of stainless steel stems largely from the cost associated with incorporating alloying elements such as chromium and nickel into its composition. On average, prices for stainless steel can fluctuate quite broadly, usually falling between $800 and $2,500 per ton. In contrast, the price spectrum for alloy steel lies in a narrower band ranging from $600 to $800 per ton.
Consequently, when financial limitations are taken into account, alloy steel becomes the preferred alternative due to its relative affordability.
Maintenance and Lifecycle Costs
Alloy steel might be more affordable upfront, but to avoid rust it usually requires either regular upkeep or protective layers, adding to its total lifetime cost. Stainless steel is known for its durability and the lesser need for maintenance, which may result in reduced overall lifecycle costs, particularly in settings where corrosion poses a major issue.
Consequently, despite bearing a greater initial price tag, stainless steel could prove to be a more cost-effective option over time for specific uses due to these factors.
Selecting the Right Material for Your Needs
When selecting the appropriate material for your project, it’s essential to weigh several considerations such as functional needs, visual desires, and financial limits. It is vital to match the characteristics of both alloy steel and stainless steel with what you require. For instance, when prioritizing strength and resilience, alloy steel might be more advantageous. On the other hand, in situations where resisting corrosion and extending service life are essential criteria, opting for stainless steel could prove beneficial.
In making a choice between alloy and stainless steel, cost plays an integral part in influencing that decision. The influence of environmental conditions must also be taken into account. Although low alloy steel may appear more economically favorable initially due to its lower price point compared to its counterpart. Often times the remarkable corrosion resistance along with diminished upkeep demands associated with stainless steel can validate a higher upfront expenditure within certain scopes of use. Weighing these elements carefully will assist you in arriving at a well-informed choice that satisfies both your practical specifications as well as your budgetary limitations.
Functional Requirements
Selecting the correct steel type for a particular application hinges on the functional demands of that use. In scenarios where durability and robustness are paramount, alloy steel is typically the optimal selection due to its characteristics. On the other hand, when it is essential to have materials that can withstand corrosion, stainless steel stands out as an ideal choice thanks to its inherent properties.
Acknowledging these needs is crucial in making an informed decision about which material will fulfill the unique requirements of any given project.
Aesthetic Preferences
The selection of materials can be influenced by aesthetic tastes. Owing to its contemporary and polished look, stainless steel is often the preferred choice in the fields of design and architecture. Its adaptability for various design purposes enables it to cater to an extensive array of visual uses, including anything from domestic kitchen devices to structural elements.
Consequently, stainless steel frequently becomes the material of preference for endeavors where the significance lies heavily on aesthetics.
Budget Constraints
Material selection is heavily influenced by budget limitations. Alloy steel typically comes at a lower price point compared to stainless steel, making it an attractive option when initial costs are a significant concern. It’s crucial to factor in the potential long-term expenses that stem from upkeep and the need for corrosion resistance before finalizing this decision.
On the other hand, if combating corrosion is of paramount importance within a given environment, opting for stainless steel might make economic sense despite its higher upfront cost. The investment can pay off through diminished maintenance needs and an extended service life of the material.
Summary
To sum up, when deciding between alloy steel and stainless steel, one must weigh various elements such as mechanical strength, resistance to corrosion and heat, along with economic factors. Alloy steels are recognized for their superior strength and durability, which renders them suitable for applications that encounter high levels of stress. Conversely, stainless steel stands out due to its exceptional ability to withstand corrosion and maintain aesthetic quality—making it the material of choice in corrosive environments or where visual design is a priority.
Choosing the most appropriate metal requires meticulous assessment of your project’s unique needs. Grasping both the characteristics and uses of alloy steels compared to stainless steels enables you to make a well-informed selection that aligns with your project’s requirements while adhering to budgetary limitations. Whether the primary concern lies with robustness, resistance against decay from chemicals or monetary considerations—you’ll find essential guidance here for picking out the optimal substance suited for your task at hand.
Frequently Asked Questions
Is alloy steel rust proof?
Due to the presence of iron, alloy steel is vulnerable to rust when it comes into contact with moisture and other atmospheric conditions.
As a result, it is necessary to implement suitable protection strategies in order to combat corrosion.
What is the main difference between alloy steel and stainless steel?
Alloy steel is differentiated from stainless steel primarily based on their compositions. It includes a variety of alloying elements that enhance its properties, while stainless steel is defined by having at least 10.5% chromium content, which is essential for its ability to resist corrosion.
Which type of steel is more cost-effective?
Alloy steel is typically more cost-effective initially compared to stainless steel. However, when considering long-term maintenance, stainless steel may offer lower total lifecycle costs in specific applications.
What applications are best suited for stainless steel?
Stainless steel is best suited for applications that demand high corrosion resistance, including the food and beverage industry, medical devices, and marine environments.
Its durability and hygienic properties make it the material of choice for these sectors.
Why is alloy steel preferred in the automotive and aerospace industries?
The automotive and aerospace industries prefer alloy steel due to its exceptional combination of high strength relative to weight, durability, and ability to resist wear. This makes it highly suitable for essential parts such as engine components and structural features.
Such a mix of attributes guarantees that performance is maintained and dependability assured in applications where the demands are great.
Still, need help? Contact Us: lk@lkprototype.com
Need a PROTOTYPE or PARTS machining quote? Quote now