Are you looking to achieve low cost CNC machining without sacrificing quality? This guide offers valuable insights into reducing CNC machining expenses. You’ll learn about factors that impact costs, tips for cutting down expenses, and affordable CNC machine options for small businesses. Dive in to discover strategies that can optimize your CNC machining processes efficiently.
Key Takeaways
CNC machining costs are influenced by material selection, design complexity, machine setup time, and production volume.
Key strategies to reduce CNC machining costs include optimizing material usage, simplifying designs, bulk ordering, and minimizing finishing operations.
Low-cost CNC machining provides significant advantages like cost savings, enhanced efficiency, and scalability, benefiting various industries including automotive, medical, and consumer electronics.
Key Factors Affecting CNC Machining Costs
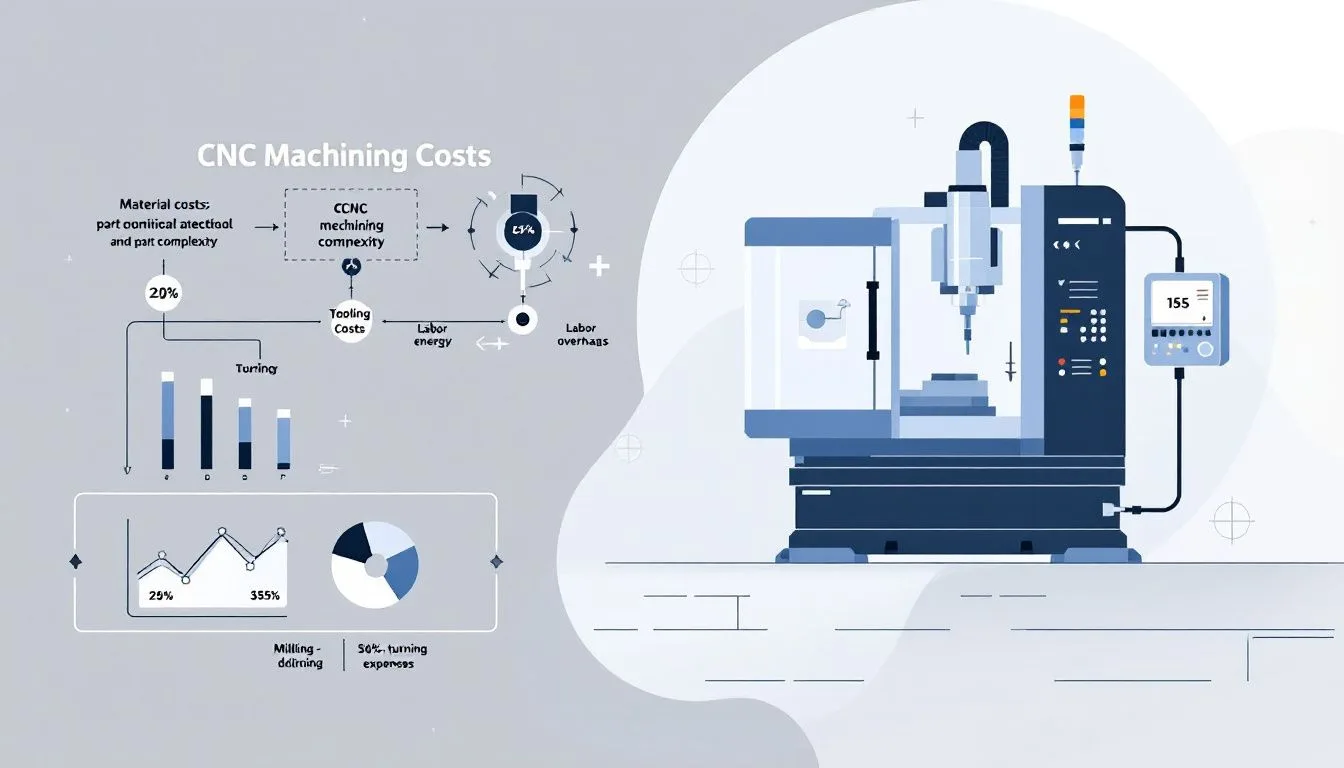
Comprehending the expenses associated with CNC machining is crucial for enterprises looking to refine their manufacturing processes. The costs involved in CNC machining can be influenced by several elements, including but not limited to the material selected, design intricacy, time necessary for machine preparation, and quantity of units produced.
The combined effect of these variables plays a pivotal role in establishing the total cost incurred during a CNC machining endeavor.
Material Selection
Selecting an appropriate material is crucial for the CNC machining process, as it affects both the cost and success of machining. Materials range from aluminum and stainless steel to brass and assorted plastics, each with its own machinability level and availability that influence their cost. Aluminum typically presents a more affordable option given its ease in the machining process, whereas materials such as stainless steel might come at a higher price but provide enhanced mechanical properties.
The selection of material within the CNC machining realm demands a careful assessment of various factors – including expenses, how well-suited they are to be machined (machinability), along with what characteristics you require in your final component.
Design Complexity
CNC machining expenses are directly impacted by the intricacy of a design. Costs tend to rise substantially when designs demand the utilization of sophisticated CNC machines and extend the duration of machining time, particularly for components that require intricate details or tight tolerances—both factors necessitate heightened precision and additional time, which escalates total costs.
On the other hand, streamlining designs can effectively cut down on CNC machining outlays without compromising their functional capabilities.
Machine Setup Time
Setup time also significantly affects CNC machining costs. The time required to set up the machine for a specific job can be substantial, especially for complex projects. Optimizing setup times through efficient planning and preparation can lead to significant cost reductions and increased efficiency.
Maximizing productivity and minimizing downtime is crucial for businesses.
Production Volume
The quantity produced significantly affects the cost of each CNC machined part, with larger quantities resulting in a decreased cost per unit due to scale economies. The setup expenses for CNC machined parts are distributed across more units during high-volume orders, which notably diminishes the total cost attributed to each individual component.
Opting for mass production not only lowers costs, but also maintains the quality of CNC machined parts, presenting it as a desirable strategy.
Tips to Reduce CNC Machining Costs
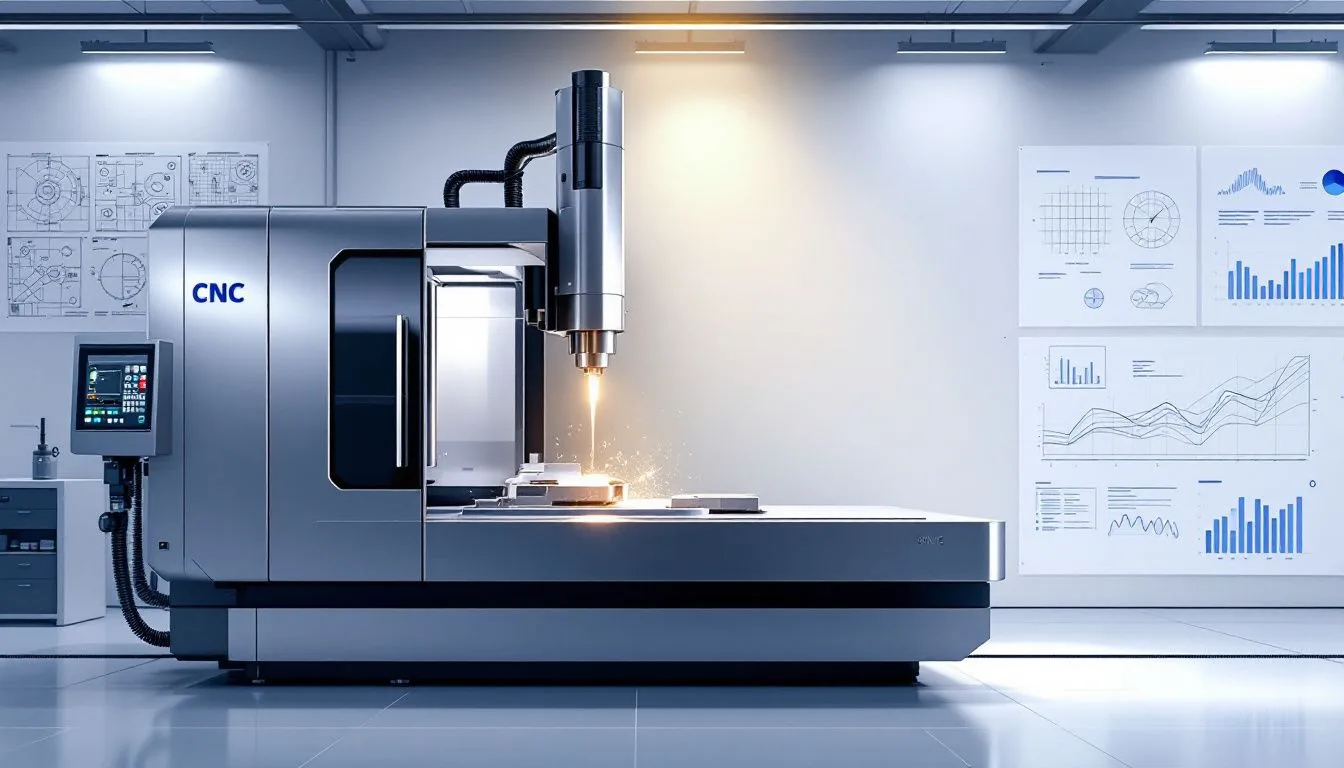
Numerous companies endeavor to strategically lower expenses associated with CNC machining. By adopting crucial tactics, it’s possible to control costs effectively without compromising the quality of the output.
Such strategies encompass utilizing materials more efficiently, streamlining part designs, consolidating purchases into larger batches, and reducing the extent of finishing processes required. All these methods provide viable options for cutting down on expenditures while ensuring that the end product retains its desired standards.
Optimize Material Usage
Minimizing waste in material consumption is crucial to cutting down on CNC machining expenses. By choosing materials that are economical, such as aluminum or ABS plastic, and efficiently reducing material excess, companies can achieve substantial cost reductions.
Employing layout optimization software for materials aids in decreasing the amount of scrap generated during the CNC machining process. This not only furthers cost-efficiency, but also enhances environmental sustainability.
Simplify Designs
By opting for simpler designs in parts, significant savings can be achieved in CNC machining costs. Designating broader tolerances and eliminating intricate details can diminish both the time required for machining and its associated expenses. For instance, incorporating rounded internal corners facilitates uninterrupted operation of the machine, thereby curtailing the time needed for CNC machining.
Not only do these simplified designs reduce expenditures, but they also improve efficiency during production.
Bulk Ordering
Purchasing larger quantities can substantially lower the cost per unit in CNC machining due to the advantages of scale. By distributing the initial setup expenses across a greater number of parts, companies can achieve considerable reductions in costs. Increased order volumes frequently strengthen bargaining leverage with vendors, potentially securing more favorable pricing agreements.
This approach proves especially advantageous for enterprises aiming to maximize efficiency within their budgetary constraints related to the manufacturing process involving CNC machinery.
Minimize Finishing Operations
Minimizing the number of finishing operations can greatly decrease the expenses associated with CNC machining. Operations like polishing or adding a coat contribute additional costs, but by opting for standard surface finishes and maintaining consistent specifications, companies are able to cut down on post-processing needs and realize savings through more streamlined CNC machining processes.
Employing this strategy allows companies to ensure that the final product adheres to required quality benchmarks while eliminating superfluous extra expenditures.
Affordable CNC Machines for Small Businesses
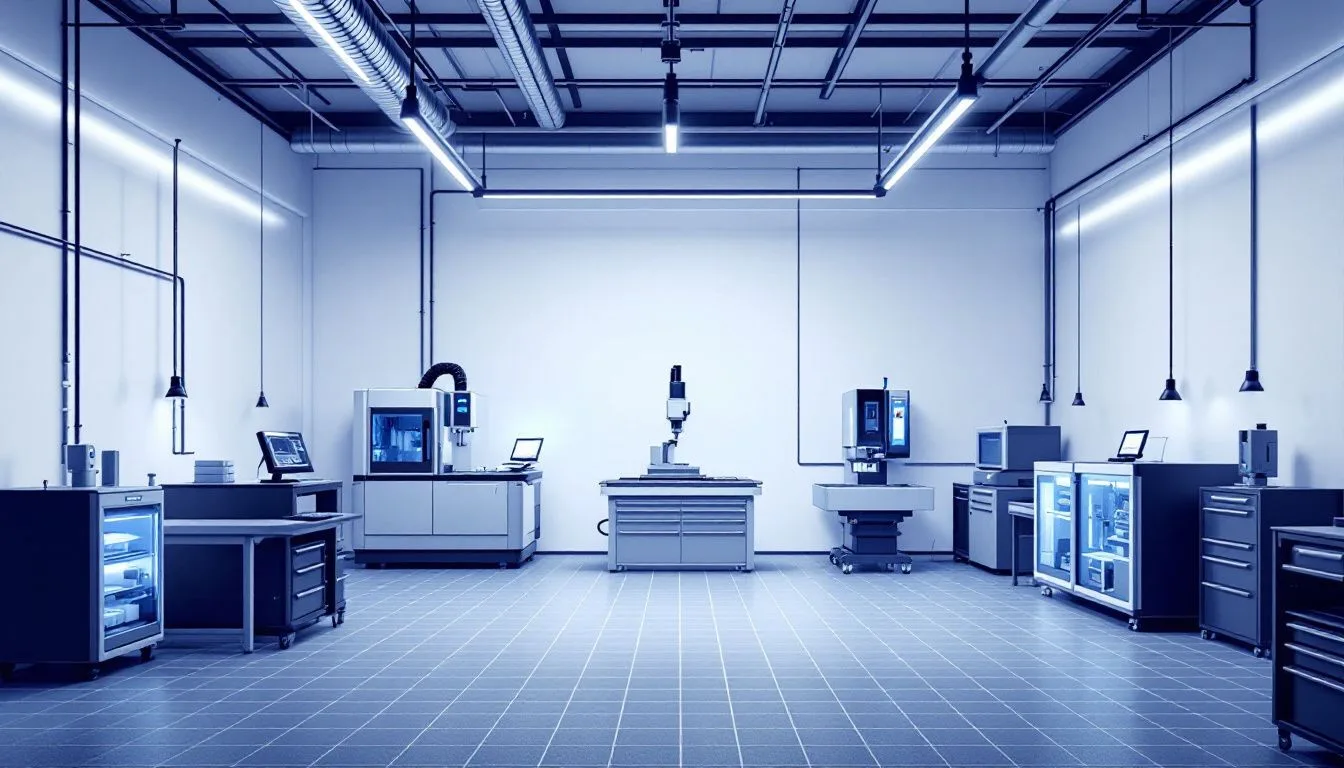
CNC machines that are budget-friendly can revolutionize the way small businesses and enthusiasts approach production. With these cost-effective machines, such as the SYIL X7, Tormach 1100MX, and Pocket NC, users can achieve professional-level precision and functionality without having to invest in expensive industrial-grade equipment.
The array of choices available serves a wide range of requirements and financial plans, making them perfect for operations with limited scale.
SYIL X7
For small enterprises in search of a cost-effective CNC machine that does not compromise on performance, the SYIL X7 is an excellent option. Renowned for its sturdy build, cutting-edge capabilities, and space-saving size, it delivers both accuracy and dependability.
The machine’s appeal to hobbyists and minor production setups can largely be attributed to its straightforward operating system and reasonable pricing.
Tormach 1100MX
The Tormach 1100MX presents a highly economical CNC machining option suitable for small enterprises. It offers outstanding performance at an affordable price, boasting features such as a high-speed spindle, an automatic tool changer, and sturdy build quality.
For operations on a smaller scale, this machine is perfect due to its low running costs and ease of configuration, making it user-friendly for those looking to engage in CNC machining.
Pocket NC
The Pocket NC delivers exceptional value for small-scale production and prototype development as a compact, budget-friendly desktop CNC machine. Its sophisticated features and meticulous engineering guarantee consistent high precision.
This machine’s small footprint is ideal for those with limited space or less experience, providing flexibility across diverse applications due to its versatile nature.
Advantages of Low Cost CNC Machining
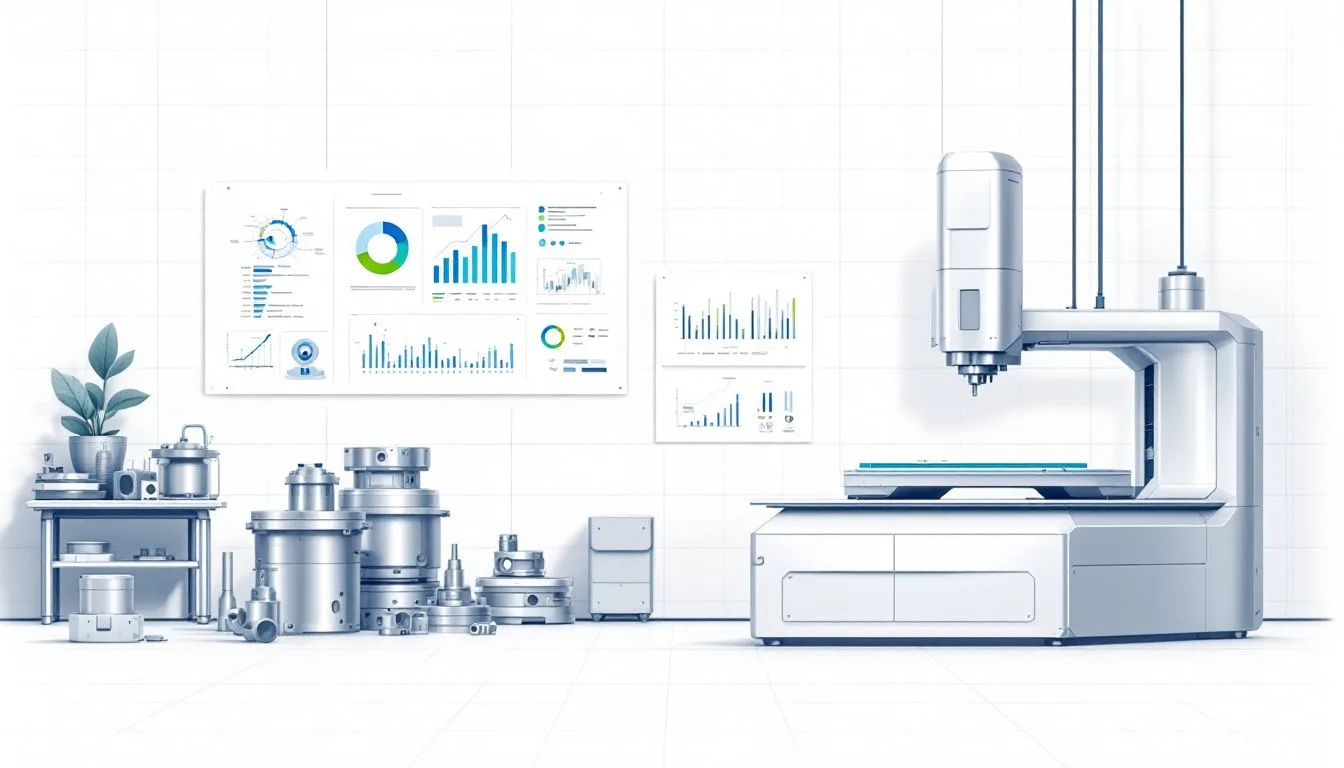
The substantial benefits offered by cost-effective CNC machining are immensely advantageous for companies. These advantages, which include significant reductions in expenses and advancements in operational efficiency, along with the ability to effortlessly expand production efforts, render CNC machining a highly appealing choice for businesses regardless of their scale.
By harnessing these impressive advantages of CNC machining, enterprises can bolster their manufacturing processes and attain exceptional outcomes.
Cost Savings
Significant cost savings are a strong benefit of utilizing low-cost CNC machining. The reduction in expenses for tooling and setup makes it an affordable option for the manufacture of parts with straightforward structures.
The capacity to swiftly create components, sometimes completing them within just one day, accelerates manufacturing schedules and cuts down on overall expenses even more.
Efficiency
CNC machining is renowned for its efficiency, delivering precise control during the machining process and achieving tight tolerances while reducing errors. Quality control protocols are rigorously applied to guarantee that each component conforms to stringent specifications, thereby boosting the efficiency of production.
The application of finishes such as PTFE impregnated hard anodize creates self-lubricating surfaces that improve the efficiency of CNC machining.
Scalability
CNC machining at an affordable price enables companies to increase their production capacity without a hefty initial expenditure. Such cost-efficiency ensures that firms can adapt swiftly to escalating demand and upscale their operations with ease.
Utilizing CNC technology allows businesses to fabricate superior-quality final products while broadening their range of merchandise effortlessly.
Choosing the Right CNC Machining Service
Choosing the right CNC machining service ensures quality and cost-effectiveness. Evaluate service providers based on experience, industry specialization, and capacity to meet specific needs. Certifications assure a provider’s commitment to quality.
A case study of LKprototype illustrates these points and shows the benefits of working with a reliable CNC machining service.
Evaluating Service Providers
When assessing providers of CNC machining services, prioritize those with a wide array of capabilities, including milling and turning as well as ancillary processes. This versatility facilitates swift adjustments to unforeseen problems and the capacity to adapt to evolving demands within projects.
The level of industry experience possessed by a provider is indicative of their competence in fulfilling particular specifications.
Importance of Certifications
Certifications are a testament to the dedication of a CNC machining service towards delivering dependable and superior quality. The attainment of an ISO 9001:2015 certification confirms that the provider meets rigorous standards for quality management, ensuring they consistently yield premium results, which in turn enhances confidence in their services.
Case Study: LKprototype
LKprototype stands as a dependable provider of CNC machining services, ensuring the production of precise components quickly and affordably while maintaining an unwavering commitment to high-quality results.
With the capability to manufacture CNC prototypes in just one day, LKprototype maintains an impressive 97.4% on-time and complete delivery rate for orders, showcasing their dedication to fulfilling customer expectations with efficiency.
Common Applications of Low Cost CNC Machining
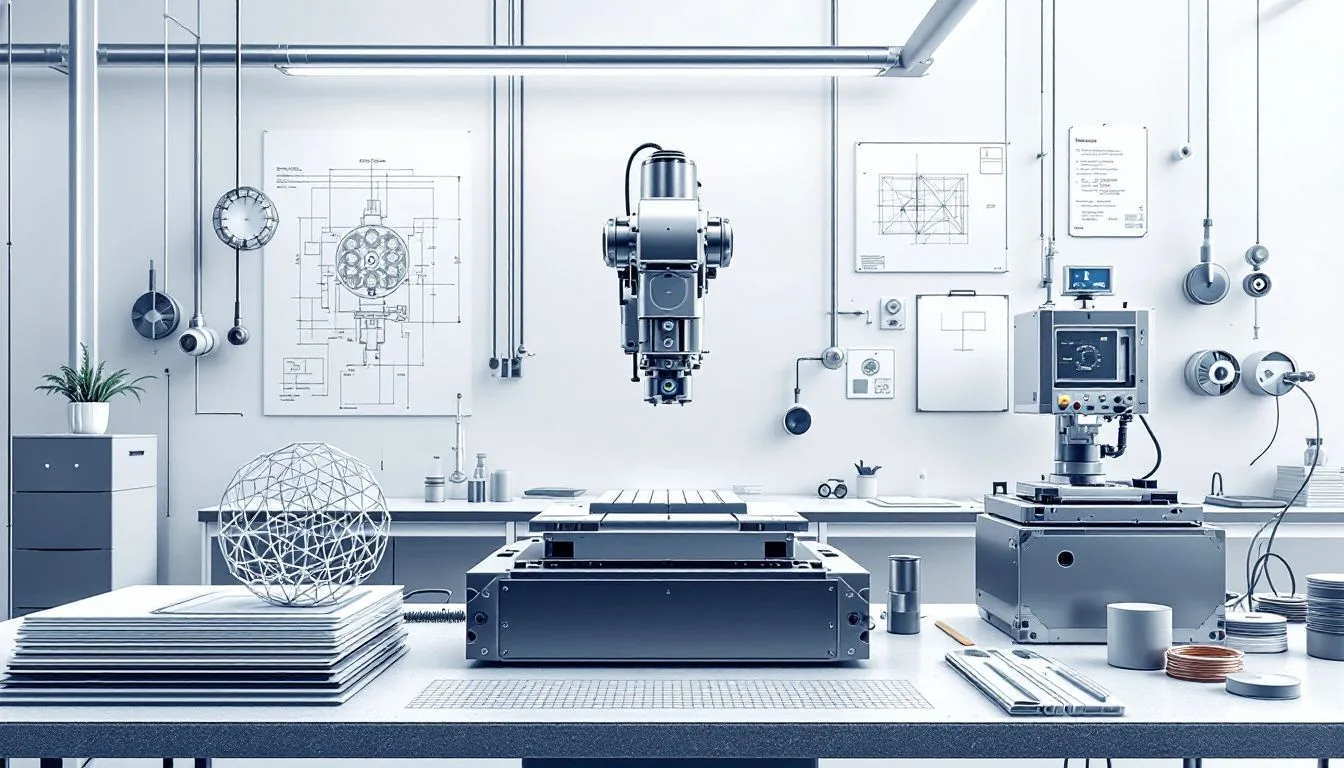
CNC machining is employed by multiple sectors due to its precision and adaptability, all at a low cost. Industries ranging from automotive to medical devices, including the consumer electronics sector, rely on CNC machining for both prototype development and full-scale production.
Scalability and economic efficiency of CNC technology are key advantages that various industries benefit from.
Automotive Industry
CNC machining plays a crucial role in the automotive sector, ensuring high precision in the manufacturing of key components such as engine blocks, cylinder heads, and transmission elements. This technology is adept at handling both smaller parts like gears and larger items while maintaining superior quality and dependability.
Medical Devices
CNC machining plays a pivotal role in the production of medical devices, as it allows for the creation of detailed designs and sophisticated shapes that are essential for contemporary surgical tools. This process facilitates swift prototyping, which accelerates the cycle of testing and refining designs within the medical device industry.
Tailored medical devices benefit from CNC machining since it enables them to conform precisely to each patient’s specific anatomical needs.
Consumer Electronics
CNC machining plays a critical role in the production of intricate and exact parts for consumer electronics such as smartphones and tablets. The high-quality components produced through computer numerical control contribute significantly to improving both the performance and longevity of these devices.
The precision involved in CNC machining processes is crucial for fabricating complex enclosures and components that must adhere to strict tolerances and possess robust finishes, ensuring their reliability within consumer electronic products.
Summary
To sum up, cost-effective CNC machining services bring a multitude of advantages to companies big and small. By grasping the essential elements that impact pricing while applying methods to minimize outlays, businesses can manufacture parts of exceptional quality in an efficient and economical manner. Small-scale enterprises have access to cutting-edge CNC technology at an accessible price point through options like SYIL X7, Tormach 1100MX, and Pocket NC.
Selecting a suitable CNC machining service is vital for securing high-quality outcomes and dependability in your endeavors. Assessing potential providers by examining their expertise, accreditation, and performance history enables you to make well-grounded choices. Sectors such as automotive manufacturing, medical device production, and consumer electronics stand to gain from the exactitude and adaptability offered by CNC machining processes. Leverage low-cost solutions within this sphere of precision engineering to improve your manufacturing operations with top-notch results consistently.
Frequently Asked Questions
What is the fastest production time for CNC prototypes at LKprototype?
The fastest production time for CNC prototypes at LKprototype is just 1 day, with a remarkable 97.4% of orders delivered on-time and in full.
How many certified materials and surface treatment finishing processes does LKprototype offer?
LKprototype offers over 65 certified materials and more than 11 surface treatment finishing processes. This extensive range allows for versatile and high-quality production options.
What industries are suitable for CNC prototypes?
CNC prototypes are highly suitable for industries like automotive, aerospace, medical devices, consumer electronics, and industrial equipment.
These sectors benefit from the precision and efficiency that CNC machining offers.
What is the typical lead time for most CNC machining projects at LKprototype?
The typical lead time for most CNC machining projects at LKprototype is 5 business days, with the possibility of delivering simple parts in as little as 1 day.
What certifications does LKprototype hold?
LKprototype holds certifications in ISO 9001:2015, ISO 13485, ISO 14001:2015, and IATF 16949:2016, ensuring quality management and compliance in various sectors.